Contributing Writer
- FMA
- The Fabricator
- FABTECH
- Canadian Metalworking
Categories
- Additive Manufacturing
- Aluminum Welding
- Arc Welding
- Assembly and Joining
- Automation and Robotics
- Bending and Forming
- Consumables
- Cutting and Weld Prep
- Electric Vehicles
- En Español
- Finishing
- Hydroforming
- Laser Cutting
- Laser Welding
- Machining
- Manufacturing Software
- Materials Handling
- Metals/Materials
- Oxyfuel Cutting
- Plasma Cutting
- Power Tools
- Punching and Other Holemaking
- Roll Forming
- Safety
- Sawing
- Shearing
- Shop Management
- Testing and Measuring
- Tube and Pipe Fabrication
- Tube and Pipe Production
- Waterjet Cutting
Industry Directory
Webcasts
Podcasts
FAB 40
Advertise
Subscribe
Account Login
Search
Selecting the right temporary coating: Choices abound for tube and pipe applications
- By David McKruit
- April 24, 2001
- Article
- Tube and Pipe Fabrication
Temporary coatings preserve the quality of tube or pipe after it is manufactured until it is received by the end user. The primary functions of this type of coating are to prevent the formation of red rust (iron oxide on steel pipe) or white rust (zinc oxide on galvanized pipe) during storage and transportation and to ease the application of finishing paint.
Most temporary coatings are destroyed when the pipes or tubes are put through a fabricating process, such as welding, bending, or finishing. Depending on the application, it may be necessary to paint the finished product for aesthetics and to prevent corrosion.
Four main types of temporary coatings are applicable for steel pipe and tube operations. These are conventional solventborne coatings, waterborne coatings, ultraviolet (UV) coatings, and chromate-based conversion treatments.
The main criteria for choosing a coating are conformance to federal, state, and local laws for volatile organic compound (VOC) emissions in the areas where the pipe will be coated; the capital equipment investment needed to set up the coating line; the cost of the coating per square foot of coverage; the quality of the coating; ease of application; and drying time. As environmental laws become stricter, the amount of VOCs becomes an increasingly significant factor.
Conventional Solventborne Coatings
Conventional solventborne coatings have been used for many years and once were considered the industry standard. Because of changing governmental regulations concerning VOCs, the use of these coatings is being phased out. These coatings contain an alkyd resin base and are reduced with solvents such as xylene, mineral spirits, and varnish makers' and painters' (VM&P) naphtha. They are available with various levels of solids content.
Some key advantages to solventborne coatings are:
- Moderately fast drying time.
- Excellent corrosion resistance.
- Clear, glossy finish.
- Mineral spirits and VM&P naphtha are hazardous air pollutant-(HAP-)free.
- Available in high-solids versions that contain lower levels of VOCs.
- Less expensive to purchase than other coatings.
- Better adherence than other coatings when applied over oils and mill scale.
Some disadvantages are:
- They come in low-solids versions that contain higher levels of VOCs.
- They are hazardous and potentially highly flammable.
Waterborne Coatings
Waterborne coating use is growing in popularity because of its low toxicity, lower VOCs, and ease of thinning. These coatings have fast drying times, excellent hard film and adhesion properties, and can be applied with a variety of methods—spray, flood and wipe, and dip.
Advantages to waterborne coatings are:
- Low amounts of VOCs. Also available in HAP-free solvent systems .
- Low risk of fire. Elevated flash points greater than 120 degrees F.
- Water-thinnable. Easy to clean up.
- Can be force-dried (heat-cured), providing a high-quality finish.
Disadvantages:
- Inconsistent drying times, which are dependent on humidity and temperature.
- Higher levels of VOCs.
- Higher cost of raw materials (resin and cosolvents).
- Water-thinnable, but contain some organic solvents.
- Unpleasant odor. Most smell like ammonia.
- Less forgiving. The surface of the pipe must be relatively free of grease and dirt or the coating will not adhere.
- Not compatible with other solvent-based coatings. All tanks, lines, and spray equipment must be cleaned thoroughly before converting to or from this type of coating.
- Very poor moisture resistance if not completely dry before exposure to moisture.
UV Coatings
This type of coating is photoreactive and polymerized instantaneously once exposed to UV radiation. The coating cure rate typically is stated in feet per minute and will vary with the power of the light source; the amount of oxygen present in the chamber (oxygen inhibits surface cure); and the length of time the coating is exposed to the light (lamp length). These coatings can be applied by conventional spray or flood and wipe equipment.
Advantages to this type are:
- Instant cure. Needs no dry time. This minimizes roll and handling marks. Product can be handled immediately and stored outside.
- 100 percent solids. Contain no solvents or VOCs.
- Reduced waste. Produces no runs or drips at 1 mil thickness.
- Improved corrosion resistance.
- Improved coating appearance.
- No solvents to add.
Disadvantages:
- More expensive than most coatings.
- Strong odor in some cases.
- Hazardous. Can cause exposure allergies and sunburn.
- Higher equipment maintenance costs (replacement of UV bulbs).
- Airless spray equipment is not recommended for use.
Chromate-based Conversion Treatments
Chromate-based conversion treatments are intended for use on galvanized steel to prevent the formation of white rust (zinc oxide). This technology relies on the use of chromic acid, or a chromic ion, to react with the zinc substrate to form zinc chromate. Best results occur when the chromate solution is applied immediately after the galvanization process, which eliminates the formation of white rust before the chromate treatment. This is by far the best-known technology for prevention of white rust on galvanized pipe.
Advantages to this type of coating are:
- Best adhesion to galvanized pipe by the formation of zinc chromate.
- Extensive corrosion protection.
- Low cost.
- Versatility in application. Can be spray-, flow-, or dip-applied.
- Treated steel can be handled immediately upon drying.
Disadvantages are:
- High toxicity (chromic acid and its chromate derivatives).
- Banned in some areas, such as Philadelphia.
- Production of hazardous waste when material is scrapped.
Other Coatings
Other coating application technologies such as hot melts and powder coatings have been evaluated. Powder coatings eliminate organic solvents; however, they do not seem to be suitable for clear, thin-film pipe coatings for the following reasons:
- High energy cost (coating must be baked on).
- Thin film application (less than 2 mils) not proven to provide adequate corrosion resistance.
- High cost of coating material (two to three times more than conventional coatings).
- Clean, scale-free surface required.
Hot-melt coatings generally are solid at room temperature. They contain no organic solvents, so they are safer to use and more environmentally compatible than solventborne coatings. Problems with application are:
- Product must be heated to liquefy for spraying (creating safety concerns and raising energy costs).
- Changes in ambient air temperature will drastically affect spray atomization and dry time.
- Difficult to apply thin film.
- High cost of application equipment.
- High operating costs.
Compatibility
Although there are many criteria for selecting a temporary coating, compatibility with the final application is among the most important. For instance, oil country tubular goods (OCTGs) should have a coating that is soluble in crude petroleum. If the coating is not soluble, it may flake off and plug pumps and filters.
Another type of coating (not discussed in this article) is made with polyurethane, which is manufactured using toluene diisocyanate (TDI). Although the TDI is reacted into the finished resin, it releases toxic cyanide gas when Burned. Tube or pipe treated with this type of coating must not be exposed to high temperatures--it must not be welded or installed as part of a sprinkler system.
In addition to compatibility, other factors must be weighed: compliance with environmental laws, coating costs, equipment and maintenance costs, and disposal costs. A coating supplier can provide assistance and more information on the various types of coatings on the market and how to choose the best temporary coating for a particular application.
About the Author
About the Publication
subscribe now
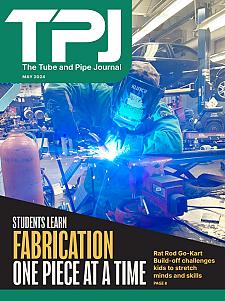
The Tube and Pipe Journal became the first magazine dedicated to serving the metal tube and pipe industry in 1990. Today, it remains the only North American publication devoted to this industry, and it has become the most trusted source of information for tube and pipe professionals.
start your free subscription- Stay connected from anywhere
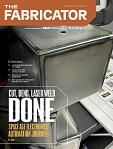
Easily access valuable industry resources now with full access to the digital edition of The Fabricator.
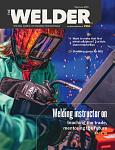
Easily access valuable industry resources now with full access to the digital edition of The Welder.
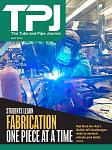
Easily access valuable industry resources now with full access to the digital edition of The Tube and Pipe Journal.
- Podcasting
- Podcast:
- The Fabricator Podcast
- Published:
- 05/14/2024
- Running Time:
- 62:12
Cameron Adams of Laser Precision, a contract metal fabricator in the Chicago area, joins the podcast to talk...
- Trending Articles
Making the move from hard automation to robotic welding
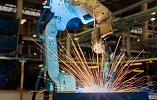
Zekelman Industries to invest $120 million in Arkansas expansion
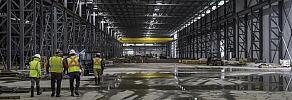
Students learn fabrication one piece at a time
HGG Profiling Equipment names area sales manager
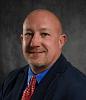
Brushless copper tubing cutter adjusts to ODs up to 2-1/8 in.
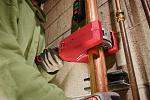
- Industry Events
Laser Welding Certificate Course
- May 7 - August 6, 2024
- Farmington Hills, IL
World-Class Roll Forming Workshop
- June 5 - 6, 2024
- Louisville, KY
Advanced Laser Application Workshop
- June 25 - 27, 2024
- Novi, MI
Precision Press Brake Certificate Course
- July 31 - August 1, 2024
- Elgin,