Contributing editor
- FMA
- The Fabricator
- FABTECH
- Canadian Metalworking
Categories
- Additive Manufacturing
- Aluminum Welding
- Arc Welding
- Assembly and Joining
- Automation and Robotics
- Bending and Forming
- Consumables
- Cutting and Weld Prep
- Electric Vehicles
- En Español
- Finishing
- Hydroforming
- Laser Cutting
- Laser Welding
- Machining
- Manufacturing Software
- Materials Handling
- Metals/Materials
- Oxyfuel Cutting
- Plasma Cutting
- Power Tools
- Punching and Other Holemaking
- Roll Forming
- Safety
- Sawing
- Shearing
- Shop Management
- Testing and Measuring
- Tube and Pipe Fabrication
- Tube and Pipe Production
- Waterjet Cutting
Industry Directory
Webcasts
Podcasts
FAB 40
Advertise
Subscribe
Account Login
Search
El chorro de agua avanza en velocidad de corte, calidad de corte y facilidad de uso
Los fabricantes dan su opinión sobre qué avances tecnológicos son más útiles
- By Kate Bachman
- Updated June 18, 2021
- July 12, 2021
- Article
- Waterjet Cutting
Para compensar la conicidad de la corriente, así como el retraso, los cabezales de chorro de agua dinámico Dynamic Waterjet de Flow utilizan modelos de corte avanzados y tecnología patentada para controlar una unión articulada que se inclina y ajusta automáticamente durante el proceso de corte. Imagen: Flow Waterjet
La tecnología de chorro de agua se ha utilizado en la industria durante décadas -según algunos informes ya en la década de 1930- con mejoras en las bombas, la presión, el granate y el control de movimiento a lo largo de los años. Los sistemas de chorro de agua abrasivos se han utilizado en la industria de la fabricación de metal de 30 a 40 años. Entonces, ¿cuáles han sido los principales avances de la tecnología?
Preguntamos a varios fabricantes de equipos originales de chorro de agua--Flow; OMAX, una subsidiaria de Hypertherm ; KMT; TechniWaterjet ; y American Machinery Group / Polaris Waterjet, para saber su opinión sobre cómo han avanzado la tecnología a lo largo de los años para mejorar la velocidad de corte, la calidad de corte y la facilidad de uso.
1. ¿Cuál es el avance más significativo en la tecnología de chorro de agua que ha aumentado la velocidad de corte?
Tom Sanders, director de ventas y marketing de KMT: Hace más de 10 años, KMT diseñó y lanzó la serie de bombas de chorro de agua de ultra alta presión Streamline PRO de 90,000 PSI, logrando un aumento significativo en las presiones de operación del estándar de la industria de 60,000 PSI a 90,000 PSI en Bombas de 60 HP y 125 HP.
Después de cientos de instalaciones de estas bombas de la serie PRO de 90,000 PSI, los usuarios finales informan un aumento de hasta un 50% en la velocidad de corte a 90,000 PSI en comparación con 60,000 PSI, así como un 50% de ahorro en el uso de medios abrasivos. Cortar un 50% más rápido ha aumentado la capacidad de fabricar más piezas a un menor costo por producto terminado.Cuanto más tiempo permanece el material que se está cortando en la máquina, más le cuesta al fabricante debido a los gastos generales, incluidos los costos de construcción, mano de obra y servicios. Cortar más rápido cuesta menos porque todo lo relacionado con la fabricación de la pieza se reduce.
Flow Intl. Brian Sherick, vicepresidente global de sistemas de ventas: La bomba está en el corazón del sistema de chorro de agua porque presuriza el agua que continuamente alimenta al cabezal de corte. La presión más alta de la bomba HyperJet de 94,000 PSI se traduce directamente en una velocidad de corte más rápida cuando el agua pasa a través del cabezal de corte en su orificio. Los aumentos del 30% al 50% en las velocidades de corte son el resultado directo de la aceleración del chorro de agua al nivel más rápido disponible, aumentando en consecuencia la presión de la bomba. Velocidades de corte más rápidas significan que se pueden cortar más piezas, lo que aumenta el rendimiento y el retorno de la inversión.
Una presión más alta también reduce la cantidad de granate que se consume durante el proceso de corte, lo que puede reducir significativamente el costo por pieza, generalmente entre el 25% y el 35%.
Joshua Swainston, líder de comunicaciones y marketing de OMAX: Aunque la presión del agua de la bomba y el recorrido lineal aumentan la velocidad general de corte, este no es el fin de la historia. El software Waterjet marca una gran diferencia.
El chorro de agua corta en un espacio tridimensional (incluso durante el corte en 2D debido al grosor del material) utilizando un chorro de agua que, naturalmente, no quiere permanecer en la forma que tiene cuando sale de la boquilla. Eso requiere un software especializado que realice miles de cálculos por pulgada.
Nuestro software integrado IntelliMAX se desarrolló junto con el hardware de chorro de agua abrasivo. Al hacer referencia a los modelos de corte sobre cómo se comportó la corriente de chorro en las configuraciones específicas de boquilla, abrasivo y material, el software se ajusta a lo que realmente está sucediendo en la mesa de corte. El software reconoce que el método agua / abrasivo es más un método de corte flexible que una herramienta dura.
A medida que los modelos de corte OMAX IntelliMAX han mejorado en los últimos 25 años, se han producido ganancias en velocidad y precisión. Los modelos de corte más avanzados, el “pase de esquinas” y la compensación cónica se traducen en piezas mejores y más rápidas desde la mesa de corte.
Las innovaciones como la compensación de conicidad, el paso de esquina y los datos refinados sobre cientos de materiales crearon una herramienta de corte que rivaliza con cualquier otra máquina. Imagen: OMAX
Jim Fields, vicepresidente de ventas y marketing de TechniWaterjet: La inteligencia de diagnóstico avanzada aumenta la velocidad de corte al reducir la cantidad de tiempo de inactividad general. Esto se debe a que maximiza la vida útil de los componentes y una cultura de mantenimiento predictivo contra el status quo del mantenimiento reactivo o preventivo. Esta característica también está en el corazón del corte sin operador que está diseñado en nuestras máquinas.
Las bombas de alta presión de 87,000 a 90,000 PSI ofrecen velocidades de corte más rápidas, aunque pueden tener un costo operativo más alto que las bombas que operan en el estándar industrial de 60,000 PSI. Hemos estado desarrollando, y lanzaremos a finales de este año, nuestra propia bomba de 87,000 PSI. Hemos tardado más en lanzar esta bomba de alta presión porque debe cumplir con nuestros objetivos de diseño: minimizar el aumento en los costos operativos y maximizar la vida útil esperada del sello. Cuando lanzamos una bomba de 66,000 PSI en nuestra tecnología servo, lo hicimos sin aumentar el costo ni sacrificar el tiempo de funcionamiento de la máquina. Eso está en línea con nuestra misión: "TechniWaterjet se enfoca en ofrecer sistemas de chorro de agua innovadores y de alta calidad que utilizan tecnología de vanguardia para brindar beneficios reales y útiles para el cliente".
Denis Lufkin, jefe de ingeniería de American Machinery Group / Polaris Waterjet: La introducción de la presión ultra alta aumentó las velocidades de corte, pero el aumento del tiempo de inactividad por mantenimiento combinado con el alto costo de los componentes de reemplazo da como resultado un escenario económico diferente. El año pasado, nuestra empresa introdujo un nuevo estilo de bomba de ultra alta presión que se construyó con la ingeniería probada y real de las bombas de 60,000 PSI. Tiene el mismo tiempo de mantenimiento para cambio de sellos y no tiene los costos de reemplazo de componentes que se conocen en el mercado.
2. ¿Cuál es la mejora tecnológica más significativa que ha mejorado la calidad de corte?Sherick, Flow: La compensación de conicidad del Dynamic Waterjet es fundamental para mejorar la calidad de corte. Al cortar a través de metal, todos los sistemas de chorro de agua exhiben cierta conicidad del chorro, que quizás, puede tener el impacto negativo más significativo en la calidad y precisión del corte. Para compensar la conicidad de la corriente, así como el retraso, los cabezales de chorro de agua dinámico Dynamic Waterjet de Flow utilizan modelos de corte avanzados y tecnología patentada para controlar una unión articulada que se inclina y ajusta automáticamente durante el proceso de corte. La capacidad de minimizar los errores inherentes causados por la conicidad y el retraso permite el corte de piezas de calidad más precisas que las que se cortan con un chorro de agua estándar. El Dynamic Waterjet ofrece una mayor precisión y mayor calidad, menos desperdicio, más productividad y por lo tanto, un mayor retorno de la inversión.
Fields, TechniWaterjet: Nuestro diseño de cabezal de corte TechHead, y su integración con otras características únicas que trabajan en conjunto han creado nuestra mejor calidad de corte hasta la fecha.
La mejor calidad de corte se logra mediante una separación constante y precisa. El mapeo del terreno permite una altura de separación constante, incluso cuando cambia la altura del material. A medida que varía la superficie plana del material y cambia la separación, también lo hace la geometría de la pieza. Un distanciamiento constante y preciso del material es fundamental durante el corte en ángulo; cuanto mayor es el ángulo, más crítico se vuelve.
Ofrecemos dos opciones para lograr esto: sensor láser y detección de sonda táctil.
Sensor láser. El láser se utiliza como puntero para encontrar los bordes, el centro de un agujero y el punto para establecer el origen de la placa. Esta opción se realiza mapeando cuatro esquinas y el centro de una hoja y líneas con biseles programados antes de cortar los puntos de perforación, la ruta o la hoja completa.
Detección de sonda táctil. La opción de detección de altura con sonda táctil realiza un mapeo del terreno confiable y preciso en la superficie del material, lo que permite que el cabezal de corte ajuste automáticamente su separación antes de perforar y durante el proceso de corte. La sonda toca la superficie de la losa, detectando discrepancias de espesor y realizando compensaciones en la altura Z. Esto es particularmente importante durante el corte en bisel para evitar resultados inesperados. Esta tecnología alternativa a un sensor láser es más eficaz en acero inoxidable pulido, aluminio y todos los materiales reflectantes.
Sanders , KMT: KMT ha mejorado la calidad del corte con el desarrollo de dos estilos diferentes de cabezales de corte. La boquilla de corte AUTOLINE permite la flexibilidad de cambiar y alinear la boquilla de gema, según los materiales que se cortan. Como alternativa, el conjunto de orificios de diamante del cabezal de corte IDE es un diamante insertado y una cámara de mezcla montados permanentemente. Esto elimina la desalineación y el torque excesivo para un rendimiento máximo. El cabezal de corte IDE ha demostrado más de 1,000 horas de corte en el campo para muchas aplicaciones.
La tecnología de chorro de agua se ha utilizado en la industria por décadas, con mejoras en las bombas, la presión, el granate y el control de movimiento a lo largo de los años. Imagen: OMAX
Además, cuando el chorro de agua corta a 90,000 PSI, el diámetro del orificio IDE se reduce de 0.014 a 0.011 pulgadas, lo que minimiza la corriente abrasiva. Aumentar la velocidad del flujo de erosión en un 50% genera un corte terminado más suave.
Swainston, OMAX: Las innovaciones como la compensación de conicidad, el paso de esquina y los datos refinados sobre cientos de materiales crearon una herramienta de corte que rivaliza con cualquier otra máquina.
En aplicaciones de corte de precisión, es deseable obtener condiciones de conicidad cercanas a cero. Con el desarrollo del modelo de corte en el software IntelliMAX, todo el cálculo y optimización de la velocidad de corte para obtener una conicidad cercana a cero se realiza dentro del software. Por lo tanto, los usuarios solo necesitan asignar la característica de calidad mínima de conicidad en la función CAM a cualquiera de las características geométricas del trabajo de corte, y el software asignará automáticamente la velocidad de corte óptima. Esta acción reduce significativamente la cantidad de tiempo necesario para programar el trabajo de corte, ya que no es necesario cortar y optimizar repetidamente la trayectoria de corte.
Para obtener una conicidad cercana a cero, el software creará automáticamente una trayectoria optimizada para el cabezal de corte A-Jet. El software no solo determina la velocidad de corte óptima en cada entidad, sino que también optimiza todos los perfiles de aceleración y desaceleración. Esto permite un corte más preciso y aumentos significativos en la velocidad de corte.
Lufkin, American Machinery: El software es lo que más ha mejorado la calidad de corte. La creación del modelo de chorro de agua permitió el desarrollo de ecuaciones y algoritmos que proporcionan acabados de corte repetibles.
El alimentador de abrasivo rotatorio digital proporciona una alimentación de abrasivo de flujo suave y medida con precisión y elimina el aumento repentino y las variaciones en el flujo de abrasivo.
El cabezal de corte de diamante integrado proporciona un chorro perfectamente centrado.
3. ¿Qué es lo que más ha mejorado su facilidad de uso?
Swainston, OMAX: Existe consenso en que hay una creciente escasez de maquinistas capaces, e incluso nuevos, en el mercado laboral, y esa tendencia no parece estar cambiando. La facilidad de uso de un sistema de chorro de agua se debe a un sencillo proceso CAD-to-CAM. Si un fabricante puede aprender CAD básico, puede ejecutar un chorro de agua. En su mayor parte, programar un chorro de agua es un proceso simple. De hecho, la mayoría de los clientes de OMAX informan que pueden cortar piezas en sus máquinas el primer día de instalación. Muchos de nuestros avances en software están integrados y se ejecutan en segundo plano para que los nuevos usuarios y los usuarios experimentados puedan beneficiarse por igual.
Sherick , Flow: El modelado con software inteligente ayuda a los operadores de nuestros sistemas a ser lo más eficientes posible. Equipamos nuestros chorros de agua con software CAD / CAM inteligente y flexible que permite importar rápidamente casi cualquier archivo externo para un diseño preciso y mapeo de cortes.
El software se complementa con un menú de entrada de parámetros de corte fácil de usar para ingresar la dirección básica, como el tipo de material, el espesor y el acabado del borde; luego el software hace el resto. También ofrecemos un módulo de anidamiento geométrico que permite colocar piezas pequeñas dentro de piezas más grandes para optimizar el material tanto como sea posible para eliminar el desperdicio. Esto es parte de un sistema de control integrado que conecta la bomba de ultra alta presión, el cabezal de corte y la mesa de corte XY.
La opción de detección de altura con sonda táctil de TechniWaterjet realiza un mapeo del terreno en la superficie del material al tocar esta. Detecta discrepancias en el grosor y realiza compensaciones en la altura Z, lo que permite que el cabezal de corte ajuste automáticamente su distancia antes de perforar y durante el proceso de corte. Imagen: TechniWaterJet
Fields, TechniWaterjet: en lugar de ser un módulo múltiple -uno para la creación de CAD, otro para la ruta de herramientas y otro para el anidamiento- nuestro software Softec es un módulo único para todos. Esto simplifica la creación, edición y corte, agilizando cada paso del proceso para ahorrar tiempo valioso.
Nuestro Tech-Sense es una combinación de un sensor de vacío en la línea de alimentación de granate y diagnósticos que ayudan a detectar si el cabezal de corte está funcionando de manera eficiente. Mide el vacío, o venturi, en el tubo de alimentación de granate. Si eso cambia, el software Softec calcula el significado del cambio, ya sea una falla en el orificio, un tubo de enfoque obstruido o roto, un bloqueo de granate, una manguera de alimentación doblada, un problema con el intensificador o una fuga en la manguera. Además, detecta el desgaste lento causado por el uso normal.
Si este sistema detecta algo fuera de un ancho de banda establecido de parámetros operativos, pone la máquina en retención de alimentación y alerta al operador, gerente o personal de mantenimiento a través de una notificación por SMS a través de un mensaje de prueba.
Este sistema de detección permite operaciones confiables de apagado.
Lufkin, American Machinery: La facilidad de uso tiene tres componentes: software para facilitar el proceso, un diseño de pórtico / máquina que minimiza el mantenimiento y una bomba / cabezal de corte de alta presión bien diseñado.
Sanders , KMT: Nuestro equipo de servicio brinda asistencia de mantenimiento preventivo en todas las bombas y productos KMT, incluida la bomba de la serie PRO de 90,000 PSI. Los fabricantes que optan por este servicio nos comentan que, al darnos la programación del mantenimiento preventivo, ellos pueden concentrarse en otros aspectos de su negocio. Nuestra tecnología patentada de sellos de metal a metal garantiza 500 horas de vida útil del sello con la compra de bombas PRO cuando nuestro equipo de servicio realiza el mantenimiento preventivo.
Muchos fabricantes de equipos originales integran nuestros componentes, incluidas las bombas de chorro de agua de ultra alta presión, los conjuntos de cabezales de corte y los recipientes de transferencia de abrasivos con sus mesas CNC.
Un aspecto amigable con el usuario de nuestra tecnología de 90,000 PSI es el ahorro de tiempo de mantenimiento y limpieza asociado con el consumo reducido de granate abrasivo. Debido a que cortar a esa alta presión usa la mitad del abrasivo en comparación con cortar a 60,000 PSI, esto reduce el tiempo de inactividad asociado con la limpieza de los abrasivos de las mesas, además del tiempo para transportar el abrasivo a un vertedero
El corte final
La velocidad de corte, la calidad de corte y la facilidad de uso son aspectos importantes de la utilidad del chorro de agua, pero deben evaluarse entre sí, así como con respecto al costo y la productividad general, advierten algunos fabricantes.
"La narrativa, si bien es importante, no siempre se trata acerca de reducir la velocidad de corte", dijo Fields de TechniWaterjet. “Si un aumento en la velocidad de corte se produce a expensas del tiempo de actividad, el costo de mantenimiento adicional y más tiempo para realizar el mantenimiento más difícil, es un lavado en el resultado final de una fábrica de producción. El juego final es más recortado dentro de un período de tiempo determinado a un costo razonable ".
La versatilidad de la tecnología de chorro de agua no debe pasarse por alto, según Sanders de KMT. Tener una máquina que puede cortar no solo metales, sino también vidrio, piedra, mármol, madera y otros materiales y el conocimiento para usarla abre oportunidades para ser un proveedor de componentes multimateriales.
About the Author
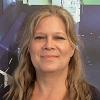
Kate Bachman
815-381-1302
Kate Bachman is a contributing editor for The FABRICATOR editor. Bachman has more than 20 years of experience as a writer and editor in the manufacturing and other industries.
About the Publication
Compañías Relacionadas
subscribe now
FMA Communications ha introducido al mercado la edición en Español de la revista The Fabricator. Esta versión consiste del mismo tipo de artículos técnicos y sección de lanzamientos de nuevos productos que actualmente presentan el personal de primera categoría de Fabricator en Inglés.
start your free subscription- Podcasting
- Podcast:
- The Fabricator Podcast
- Published:
- 04/30/2024
- Running Time:
- 53:00
Seth Feldman of Iowa-based Wertzbaugher Services joins The Fabricator Podcast to offer his take as a Gen Zer...
- Trending Articles
Prescripción para la reducción del desperdicio: arreglo esbelto de las instalaciones
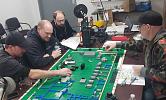
Anidado para la estabilidad del corte láser
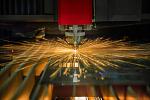
La máquina procesadora de placas crea biseles complejos en un solo corte
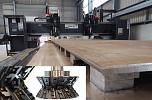
El software guía a los soldadores a través de instrucciones de trabajo
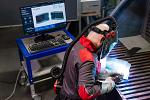
La rueda reduce las fuerzas de empuje/tracción hasta en un 50%

- Industry Events
Pipe and Tube Conference
- May 21 - 22, 2024
- Omaha, NE
World-Class Roll Forming Workshop
- June 5 - 6, 2024
- Louisville, KY
Advanced Laser Application Workshop
- June 25 - 27, 2024
- Novi, MI
Precision Press Brake Certificate Course
- July 31 - August 1, 2024
- Elgin,