Contributing editor
- FMA
- The Fabricator
- FABTECH
- Canadian Metalworking
Categories
- Additive Manufacturing
- Aluminum Welding
- Arc Welding
- Assembly and Joining
- Automation and Robotics
- Bending and Forming
- Consumables
- Cutting and Weld Prep
- Electric Vehicles
- En Español
- Finishing
- Hydroforming
- Laser Cutting
- Laser Welding
- Machining
- Manufacturing Software
- Materials Handling
- Metals/Materials
- Oxyfuel Cutting
- Plasma Cutting
- Power Tools
- Punching and Other Holemaking
- Roll Forming
- Safety
- Sawing
- Shearing
- Shop Management
- Testing and Measuring
- Tube and Pipe Fabrication
- Tube and Pipe Production
- Waterjet Cutting
Industry Directory
Webcasts
Podcasts
FAB 40
Advertise
Subscribe
Account Login
Search
Toyota WV president weighs in on materials, electrification
“We have to raise the level of our suppliers so we can build more in the U.S.”
- By Kate Bachman
- March 14, 2019
- Article
- Shop Management
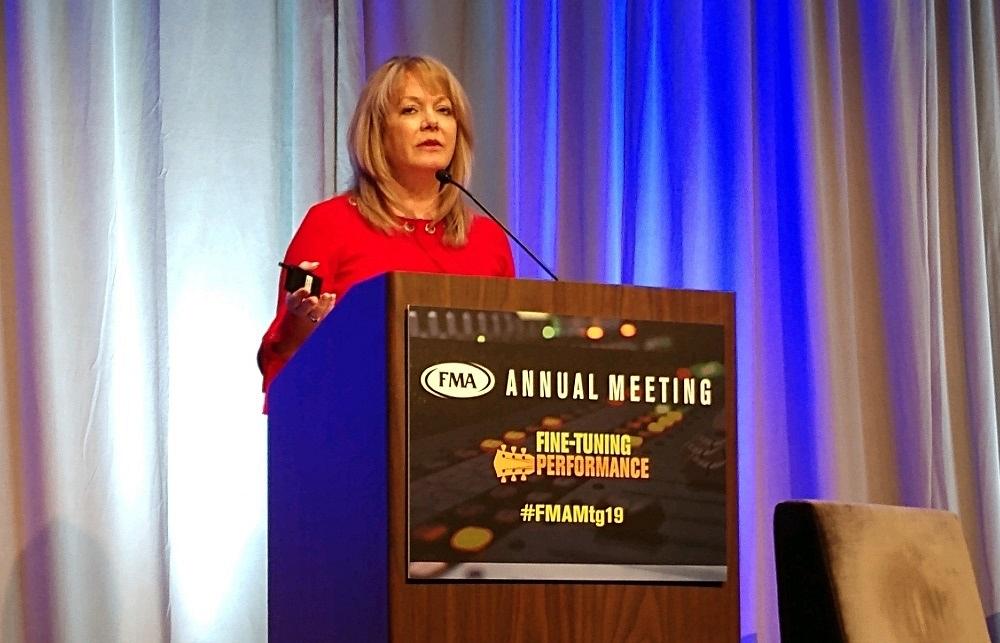
Toyota Motor Manufacturing West Virginia President Leah Curry was a keynote speaker at FMA’s 2019 Annual Meeting in Nashville.
The powertrain transition from the internal combustion engine to electrification and other emissions-free technologies is the auto industry’s race to the moon, said Toyota Motor Manufacturing West Virginia President Leah Curry. Curry was a keynote speaker at FMA’s Annual Meeting in Nashville on March 6. She addressed lightweighting, materials, electrification, tariffs, and her view on where the automotive industry is heading.
The plant employs 1,700 team members.
Forging Ahead to 54.5 MPG
Despite the Trump administration’s plan to freeze corporate average fuel economy (CAFE) standards at 37 MPG, Toyota is still pushing to meet the 54.5-MPG-by-2025 mandate of the original Obama-era standard.
The company plans to accomplish that by both lightweighting and modernizing its powertrain, Curry said.
The Future Is Electric
The automotive industry is in the midst of a powertrain revolution, as it veers away from internal combustion engines to modernized, emissions-free powertrain systems, Curry said.
“I believe EVs [electric vehicles] are going to be the future. The future is not the internal combustion engine.”
Toyota already has mastered and manufactured hybrids and plug-in electrics, she recounted. Toyota is the first automaker to manufacture a commercially available hydrogen-powered vehicle, the Mirai, which emits only water. Toyota Europe is sponsoring the first hydrogen ocean vessel, the Energy Observer. In the spring Toyota’s fuel cell vehicles launch in Spain. “These technologies are happening right now,” she said.
Pressure is on to be ready for the new powertrain system. Curry said that the most important task facing her is planning for the next generation’s vehicles in the years ahead, but doing so is difficult because of the timing uncertainties. “I’m setting up my plant to build electric vehicles, but it’s gray as to when it’s going to be turning over. In the meantime, how many electric powertrain systems will we need to build? How many combustion engines will we need to build and for how long? We have to be ready at all levels.”
Curry expressed concern that without a government mandate for non-ICE propulsion systems, North America’s technology will fall behind China’s and Europe’s, which have incentives and quotas for EVs.
“But in the U.S. there are no mandates like in China and Europe,” Curry said. “It worries me. Without mandates and direction in North America, will we fall too far behind? Will we be able to catch up?
“Where there are changes, there are opportunities. There will be winners and losers,” she said. “This is like the race to the moon. North America has to be sure that we’re ready—and then the infrastructure has to be ready.”
Toyota has partnered with Panasonic to develop batteries that will make vehicles go longer distances on a charge, Curry relayed. “Once we do that, watch out.”
Lightweighting Continues
The conversion from ICE-powered vehicles to electrified and hydrogen-powered vehicles will not change the intensity of Toyota’s lightweighting efforts, Curry said. The company will continue to reduce mass to get its vehicles as light as possible.
“We’re committed to making vehicles lighter. That’s our objective. The lighter the vehicle weight, the greater distance it can go on a charge.“We can accomplish that while enhancing safety and without losing quality.”
All Materials
Curry said that Toyota uses all available materials where they make sense to reduce weight and reinforce safety. “We use advanced high-strength steel. We use aluminum. We use carbon fiber. We use all materials.” The automaker is unlikely to manufacture an entire vehicle from one material, as Ford did with aluminum in its F-150, she added.
The RAV 4’s use of aluminum in the hood and back door reduces part weight by 50 percent, she said. The company uses magnesium in some die-cast parts for engines, and plastic in truck liners. Using carbon fiber in the Lexus reduced its weight 50 to 60 percent, Curry said.
Toyota also is conscious about using renewable, recyclable, and reusable materials to generate less waste. It uses postindustrial cotton and synthetic garment clippings for door panel insulation, floor silencer pads, and floor mats. It uses bio-based materials and has developed rare-earth magnetic material that is more abundant than lithium-ion for its EVs.
“We embrace new materials that help to make our environment better. We all want to be part of something bigger, something valuable.”
Trade, Tariffs, U.S. Suppliers
Curry said that cooperative trade is very important to Toyota, because the automaker’s vehicles cross Canada’s and Mexico’s borders several times as they are being built. “Our greatest risk is the tariffs and internal trade friction. It has the capacity to impact us greatly,” she said. “The effects of the tariffs are real and they’re going to get worse.”
Regarding filling in the supply chain where the tariffs have created gaps: “We have to raise the level of our suppliers so we can build more in the U.S.”
The West Virginia plant is the only Toyota factory that manufactures both engines and transmissions at the same site, for several vehicles.
About the Author
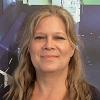
Kate Bachman
815-381-1302
Kate Bachman is a contributing editor for The FABRICATOR editor. Bachman has more than 20 years of experience as a writer and editor in the manufacturing and other industries.
subscribe now
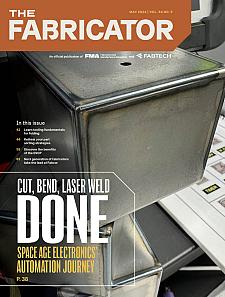
The Fabricator is North America's leading magazine for the metal forming and fabricating industry. The magazine delivers the news, technical articles, and case histories that enable fabricators to do their jobs more efficiently. The Fabricator has served the industry since 1970.
start your free subscription- Stay connected from anywhere
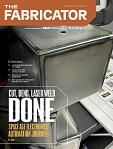
Easily access valuable industry resources now with full access to the digital edition of The Fabricator.
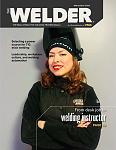
Easily access valuable industry resources now with full access to the digital edition of The Welder.
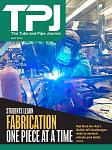
Easily access valuable industry resources now with full access to the digital edition of The Tube and Pipe Journal.
- Podcasting
- Podcast:
- The Fabricator Podcast
- Published:
- 04/30/2024
- Running Time:
- 53:00
Seth Feldman of Iowa-based Wertzbaugher Services joins The Fabricator Podcast to offer his take as a Gen Zer...
- Industry Events
Pipe and Tube Conference
- May 21 - 22, 2024
- Omaha, NE
World-Class Roll Forming Workshop
- June 5 - 6, 2024
- Louisville, KY
Advanced Laser Application Workshop
- June 25 - 27, 2024
- Novi, MI
Precision Press Brake Certificate Course
- July 31 - August 1, 2024
- Elgin,