Contributing Writer
- FMA
- The Fabricator
- FABTECH
- Canadian Metalworking
Categories
- Additive Manufacturing
- Aluminum Welding
- Arc Welding
- Assembly and Joining
- Automation and Robotics
- Bending and Forming
- Consumables
- Cutting and Weld Prep
- Electric Vehicles
- En Español
- Finishing
- Hydroforming
- Laser Cutting
- Laser Welding
- Machining
- Manufacturing Software
- Materials Handling
- Metals/Materials
- Oxyfuel Cutting
- Plasma Cutting
- Power Tools
- Punching and Other Holemaking
- Roll Forming
- Safety
- Sawing
- Shearing
- Shop Management
- Testing and Measuring
- Tube and Pipe Fabrication
- Tube and Pipe Production
- Waterjet Cutting
Industry Directory
Webcasts
Podcasts
FAB 40
Advertise
Subscribe
Account Login
Search
A 3-D CAD modeling case study: The battle between DFM and supply chain
The prototype created a faulty supply chain
- By Gerald Davis
- July 15, 2018
- Article
- Manufacturing Software
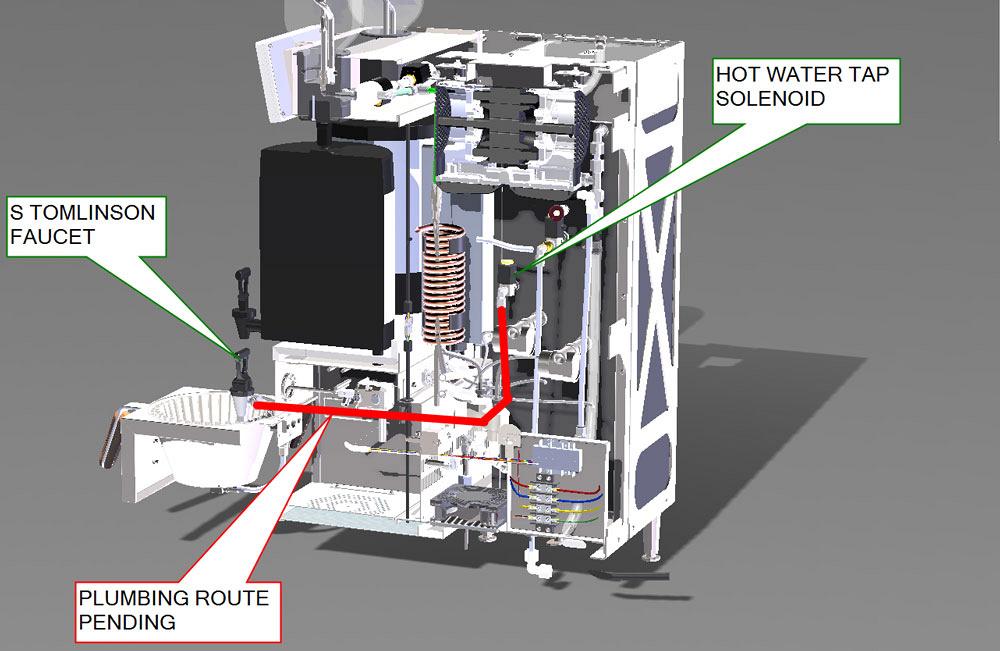
Figure 1
This is a screen shot of the 3-D CAD as the design for manufacturability effort was undertaken for the sheet metal cabinet. A complex machine requires a complex supply chain.
Disclaimer: This case study of a coffee maker’s sheet metal cabinet features a pair of inventors doing their best without the benefit of experience in manufacturing. The result was Voga Coffee Inc.’s commercial coffee maker that can fill a 1-gallon thermal carafe. In fact, the Specialty Coffee Association named the Ground Control® Cyclops™ batch coffee brewer the 2018 Best New Product, Commercial Equipment Award winner.
The previous edition of this column (“A 3-D CAD modeling case study: When DFM imperils industrial design,” Precision Matters, The FABRICATOR®, June 2018, p. 44) suggested that the reconciliation of industrial design (ID) with design for manufacturability (DFM) had a bumpy start. We’ll delve more into how DFM drifted away from ID, but let’s take a sidebar to tell the tale of the impact that the prototype had on inventory and the supply chain.
I am able to publish this story about the predecessor to Cyclops because of the determination, vision, and success of those who invented the machine. When they started their business, they had no experience in manufacturing. They were experts in coffee, but what they really needed was a contract manufacturer. At the time they were afraid of losing control of the cash flow and intellectual property, so they decided to build it themselves. Start small and grow big, but always be in control; that’s good advice.
I am reporting several results of the company’s experience that may seem painful and somewhat embarrassing in hindsight. Be assured, these are men of integrity, wit, and sound character.
DFM Versus Supply Chain
The supply chain theme as it relates to DFM is pretty straightforward, especially when it comes to custom-made parts: Design the parts to suit those who will be fabricating them. When the trade skills required are rather generic—for example, simple machined or sheet metal parts—the supply chain might be selected, or qualified, to match the design.
The end use of the product can have a major impact on qualifying the supply chain as well. The coffee brewer falls into the category of food processing equipment. The materials that come in contact with the coffee—glass, plastic, and various alloys of stainless steel—all must comply with food safety standards.
For those with experience in job shop manufacturing, the need for compliance with standards and a written statement of same is probably routine business. Some shops do it automatically, and for others it is an upcharge to the project. Our heroes, however, didn’t know about material certifications.
During the rush to get the first prototype completed, regulatory considerations were given low priority. The prototype was not for general resale. The materials selected seemed safe to the people tasting and testing the coffee. Speed was the primary consideration, so any off-the-shelf item was OK. If the demo went well, the little details could be figured out later.
Occasionally prototype items like solenoid valves and terminal blocks were purchased from famous online auction websites. Price, delivery, and function of the inventory received were all just fine. In retrospect, those “uncontrolled” purchases created havoc in the inventory.
Eventually certified-food-safe inventory was obtained for everything going into the brewer’s production line. At this stage in our brewer’s factory inventory, only a few items had certification.
Over many months, many dollars, and occasionally unexpected travel, our brewer builders learned an important lesson: Those items without certifications should be disposed of by sale at online auction. They probably should never have been purchased to start with, but who knew?
As an example of such a tragedy, one bolt may look like another, but a good bolt has a documented history and can come in contact with coffee, while a very affordable bolt might be a toxic imposter that can never touch coffee. Keep them isolated and clearly marked, and there is hope. Let them mix in the bin or become anonymous, and the whole lot becomes uncertified.
Some of the early, randomly obtained inventory items could not be repurchased at the same low price or in the same schedule. Even worse, a few items seemed to no longer exist on the planet.
Should you be in the job shop trade and would like to attract entrepreneurs as customers, we recommend that your marketing material emphasize your skills with all aspects of inventory control—cost, storage, and certifications. This ties in nicely with DFM services (see Figure 1). If the end use of the product requires certified materials, be prepared to create the documentation for the design. That includes notes on the print to specify the requirement.
Would Have, Should Have
When the brewer was just a vivid dream, thoughts of revision control, inventory control, and regulatory compliance were like peas under the mattress, never to be noticed. At this time it would have been splendid if our boys had found job shops with an understanding of inventory certification.
It would have been good because the prototype builders had worked out the flat layouts, made shop drawings, completed good weld plans, finished work orders, and built jigs. Their labor gained training and their shop made special tooling to complete the prototype. Because of a failure to keep a certification trail of inventoried parts, the brewer builders had a prototype fabricated, but it was a dead end. They had to start from scratch in terms of finding the right supply chain.
The brewer’s design benefited greatly from ID. Time and treasure were expended to make sure the ID was right. If they would have placed the same emphasis on DFM to resolve compliance and supply chain issues at the forefront, the subsequent transition from tradeshow demo to mass production would have been more graceful. Time and opportunity seemed to prevent that in this case.
Help Them to Help Themselves
Our brewer builders had no idea what DFM entailed. They did not need that. All they needed was to make it to the tradeshow with a working brewer. Following the success at the tradeshow, and with my help in DFM, our heroes found job shops and online distributors that could handle their needs in food safety compliance.
This article is dedicated to my peers who work for hire in DFM and 3-D CAD. That peer group generally knows or works closely with a network of job shops that they can optimize a given design for.
These CAD jockeys also tend to bundle services in the arena of ID and DFM. These activities include:
- Definition of function and selection of the required components to create the product.
- Structural design of the enclosure housing the required components.
- Selection of pleasing color, material, and finish.
- Invention of ideal function, which translates into a satisfying end-user experience.
- Optimum use of raw material, which leads to efficient manufacturing.
- Assembly, service, and preventive maintenance.
- Documentation of the design, which covers fabrication, assembly, and end-user instructions.
- Compliance, which entails document control, supply chain management, inventory control, and assembly history.
Gerald would love for you to send him your comments and questions. You are not alone, and the problems you face often are shared by others. Share the grief, and perhaps we will all share in the joy of finding answers. Please send your questions and comments to dand@thefabricator.com.
About the Author
subscribe now
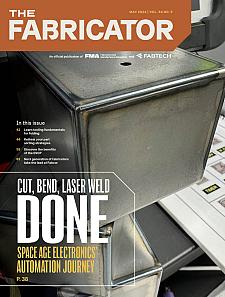
The Fabricator is North America's leading magazine for the metal forming and fabricating industry. The magazine delivers the news, technical articles, and case histories that enable fabricators to do their jobs more efficiently. The Fabricator has served the industry since 1970.
start your free subscription- Stay connected from anywhere
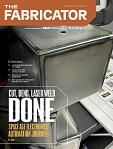
Easily access valuable industry resources now with full access to the digital edition of The Fabricator.
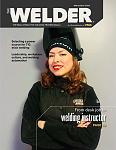
Easily access valuable industry resources now with full access to the digital edition of The Welder.
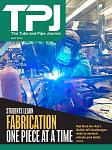
Easily access valuable industry resources now with full access to the digital edition of The Tube and Pipe Journal.
- Podcasting
- Podcast:
- The Fabricator Podcast
- Published:
- 05/07/2024
- Running Time:
- 67:38
Patrick Brunken, VP of Addison Machine Engineering, joins The Fabricator Podcast to talk about the tube and pipe...
- Trending Articles
How laser and TIG welding coexist in the modern job shop
Young fabricators ready to step forward at family shop
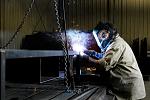
Material handling automation moves forward at MODEX
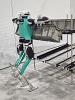
A deep dive into a bleeding-edge automation strategy in metal fabrication
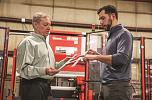
Precision Press Brake Certificate Course
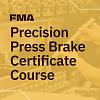
- Industry Events
World-Class Roll Forming Workshop
- June 5 - 6, 2024
- Louisville, KY
Advanced Laser Application Workshop
- June 25 - 27, 2024
- Novi, MI
Precision Press Brake Certificate Course
- July 31 - August 1, 2024
- Elgin,