- FMA
- The Fabricator
- FABTECH
- Canadian Metalworking
Categories
- Additive Manufacturing
- Aluminum Welding
- Arc Welding
- Assembly and Joining
- Automation and Robotics
- Bending and Forming
- Consumables
- Cutting and Weld Prep
- Electric Vehicles
- En Español
- Finishing
- Hydroforming
- Laser Cutting
- Laser Welding
- Machining
- Manufacturing Software
- Materials Handling
- Metals/Materials
- Oxyfuel Cutting
- Plasma Cutting
- Power Tools
- Punching and Other Holemaking
- Roll Forming
- Safety
- Sawing
- Shearing
- Shop Management
- Testing and Measuring
- Tube and Pipe Fabrication
- Tube and Pipe Production
- Waterjet Cutting
Industry Directory
Webcasts
Podcasts
FAB 40
Advertise
Subscribe
Account Login
Search
Fabricating tube to win races
The Motor & Sport Institute helps racing teams fabricate components, build cars, win competitions
- By Eric Lundin
- November 10, 2018
- Article
- Tube and Pipe Fabrication
In essentially every field of human endeavor, a small amount of execution is preceded by vast amounts of preparation. Whether it’s a matter of working out, training, practice, scrimmage, making a dry run, or some other term, it’s usually the indispensable component in any success.
Veteran driver Bobby Unser summed up the importance of preparation when he said, “Success is where preparation and opportunity meet.” He’d know. A champion who holds six racing titles in open-wheel (Indy car) racing, he won the Indianapolis 500 three times. More remarkable still, he’s one of just two drivers to win the Indy 500 three times in three decades, taking the checkered flag in 1968, 1975, and 1981. He not only got to the top, but remained there much longer than most.
One of the greatest athletes of our time, Michael Jordan, remained at the top of his game for many years also. He summed up the necessity of a regular and strenuous training regimen to maintain the momentum of a dedicated champion: “I'm not out there sweating for three hours every day just to find out what it feels like to sweat.” Elite athletes dedicate enormous energy to preparing to compete throughout their careers.
To that end, the Motor & Sport Institute (MSI), Madrid, was founded to help racing teams prepare for competition, work their way to the top, and remain there. A high-tech center that embraces every aspect of automobile racing—building, testing, and modifying—its goal is to help Spain continue to build a legacy in motorsports.
While the institute’s foundation is strong and its reputation continues to develop, the cornerstone is the remarkable pedigree of its founder.
“MSI was founded by legendary driver Teo Martín, who many regard as one of Spain’s modern national treasures,” said Pedro Ferreira, sales and marketing director for machine builder AMOB S.A.
Spain’s legacy in motorsports goes back to the early days of the automobile. The Spanish Grand Prix, held at the Circuit de Barcelona-Catalunya, is among the oldest racing circuits in the world, dating to 1913. Its modern legacy started in 1990, when Carlos Sainz won the World Rally Championship. He won it again two years later. Formula 1 driver Fernando Alonso has racked up 32 wins since he started racing Formula 1 in 2001, taking the championship in 2005, garnering 133 points. He followed that by winning it again in 2006, earning 134 points. Sainz’s son, Carlos Sainz Jr., is a racing veteran, having participated in karting, Formula BMW, Formula 3, GP3, and two Formula Renault series. He took first place in two competitions, Formula Renault 2.0 in 2011 and Formula Renault 3.5 in 2014, and has been competing in Formula 1 since 2015. He has been working his way up, finishing in 15th place in 2015, 12th place in 2016, and 9th place in 2017.
For all that, Spain does even better in motorcycle racing. Of the 27 motorcycle riders registered to compete in the 2018 MotoGP schedule, nine are from Spain (and, as of press time, 11 races into the 19-race schedule, three of the top five competitors were from Spain).
Is more to come? Sure.
“MSI’s goal is to develop professional racing teams to further Spain’s reputation in international racing,” said Luís Ribeiro, AMOB’s lead engineer.
The Many Facets of MSI
The institute is dedicated to everything that concerns automobile racing, comprising seven focus areas that overlap and complement each other.
Its technology and innovation division is replete with machining centers for making automotive components, equipment for testing engines or entire powertrains, autoclaves for doing work with composites, a metrology lab for taking precise measurements, and a painting division for the finish. MSI partners with University Francisco de Vitoria, Madrid, to provide real-world projects that are well-suited to mechanical and electronic engineering students, making positions available to students from universities throughout Europe. Other divisions are dedicated to esports, providing the thrills of racing without the hazards, and road safety, helping to reduce everyday driving risks. Its motorsports division supports Teo Martín Motorsport, which fields eight teams in various racing series throughout Europe. MSI’s spaces and experiences division is dedicated to providing racing events for fans—those who aren’t involved in the sport but want to see what a day at the track is like.
Finally, it’s bioengineering department focuses on the physical capabilities of the drivers and other athletes. Whether the athlete is focused on improvement or recovery from an injury, this department helps them with strength and endurance by planning workouts, facilitating training on specialized athletic equipment, and diet planning.
The theme that runs throughout the institute’s various disciplines is preparation. Whether it’s a matter of measuring an engine’s output, verifying how a chassis reacts to dynamic loading, or training the driver to endure grueling hours in a hot cockpit, the institute’s mission is to prepare the teams to compete and to win.
Tube Fabrication at MSI
Of course racing participants at the institute don’t just build racing cars; they fabricate the components that go into racing cars. Applications include brake lines, seat frames, intercoolers, frame components, roll bars and roll cages, radiator components, and exhaust tubes. To that end, the teams buy and form tube in various alloys, diameters, and wall thicknesses. Chrome-moly steel, stainless steel, INCONEL® alloy, aluminum, and titanium are among the most commonly used materials.
In turn, this means that they deal with an extensive variety of characteristics. Chrome-moly steel in the normalized condition has a minimum yield strength (MYS) of 97,000 pounds per square inch (PSI) and its elongation is 25.5 percent; grade 2 titanium has an MYS of 50,000 PSI and an elongation of 20 percent; a mild steel might have an MYS of 72,000 PSI and an elongation of just 10 percent. Meanwhile, the dimensions likewise vary substantially. The diameter-to-thickness (D/t) ratio can be as little as 6.7 to 1 for a brake line and as much as 48 to 1 for an exhaust component.
In short, the racing teams and engineering students at MSI deal with endless combinations of tube dimensions and forming characteristics.
Setting Up Students for Success
This situation isn’t necessarily unusual, but it is extreme. Most fabrication shops bend a couple of alloys in an assortment of sizes and wall thicknesses, but the breadth of alloys, diameters, wall thicknesses, and D/t ratios fabricated at MSI is extraordinary. Also, while every fabrication shop has a little turnover, MSI’s association with a university guarantees some turnover every year as senior students graduate and new students fill the vacated positions.
It sounds like AMOB has set itself up for providing endless courses in bending theory, machine setup, best practices, and troubleshooting. How does the company undertake such a challenge in educating MSI’s customers about bending?
In short, it doesn’t.
For MSI’s applications, the company provided an eMOB 52. A fully electric rotary draw bender, it handles tube in diameters from 0.39 to 2.04 inches. The machine is well-suited to an institute such as MSI because the bend geometries for racing applications are likely to be limitless. The 9-axis machine can perform both fixed- and variable-radius bending in a single bending cycle. The tooling arrangement is such that the machine can make back-to-back bends—two successive bends with no straight length between them—and its carriage boost brings bend radii down to 1D.
As far as preparing to make the bender run, AMOB expects that MSI’s participants will do no programming.
“The machine imports files from any CAD program, and the software generates the bending sequence,” Ribeiro said. “The machine develops a 3-D view of the part, simulates the bending process, and verifies that it will bend without a collision,” he said.
While the machine has stacked tooling, there is no guarantee that the right tooling will be installed on the machine at the right time. Beyond loading the machine and pressing Start, swapping out the tooling is the only action that the racing team members or university students will have to do.
“The machine positions the tooling, eliminating the potential for human error,” Ferreira said. “It positions the tooling automatically, and it measures each bend before finishing the bending cycle. It bends, unclamps the tube, and takes a measurement to determine the amount of springback. The machine then clamps the tube and finishes the bend. The goal is to make the first part a good part, which reduces scrap,” he continued. This is critical on pricey alloys. The unit also has a built-in weld seam detector so the weld seam is positioned where it will be subjected to the least tension or compression.
Electric machines, which use servomotors for their motion, contribute to productivity in both speed and accuracy. Each axis of motion is synchronized for optimum positioning speed, and servo technology provides accurate and repeatable positioning. Finally, they run efficiently, drawing power only when needed.
MSI in 2018
The future is bright for MSI. Its affiliate team, Teo Martín Motorsport, has a long history of success in various racing series, and it continues to build on its legacy. In 2015 it competed in the International GT Open for the first time. Despite its rookie status, it was thoroughly prepared for the competition and it won the championship. After a merger with the team led by Emilio de Villota Jr., it won the following year, too.
The current season looks promising. As of press time, drivers Fran Rueda and Andres Saravia were tied for second place with 62 points each.
AMOB S.A., www.amobgroup.com
About the Author
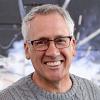
Eric Lundin
2135 Point Blvd
Elgin, IL 60123
815-227-8262
Eric Lundin worked on The Tube & Pipe Journal from 2000 to 2022.
About the Publication
Related Companies
subscribe now
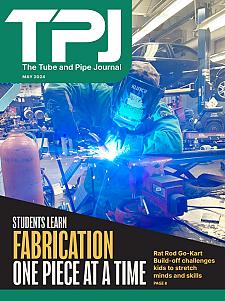
The Tube and Pipe Journal became the first magazine dedicated to serving the metal tube and pipe industry in 1990. Today, it remains the only North American publication devoted to this industry, and it has become the most trusted source of information for tube and pipe professionals.
start your free subscription- Stay connected from anywhere
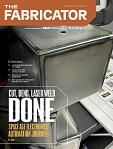
Easily access valuable industry resources now with full access to the digital edition of The Fabricator.
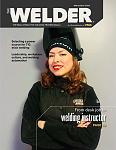
Easily access valuable industry resources now with full access to the digital edition of The Welder.
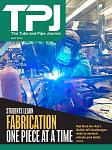
Easily access valuable industry resources now with full access to the digital edition of The Tube and Pipe Journal.
- Podcasting
- Podcast:
- The Fabricator Podcast
- Published:
- 04/30/2024
- Running Time:
- 53:00
Seth Feldman of Iowa-based Wertzbaugher Services joins The Fabricator Podcast to offer his take as a Gen Zer...
- Trending Articles
Zekelman Industries to invest $120 million in Arkansas expansion
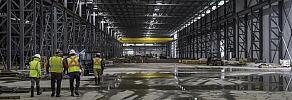
3D laser tube cutting system available in 3, 4, or 5 kW
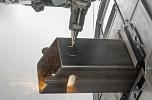
Corrosion-inhibiting coating can be peeled off after use
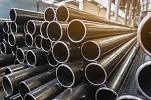
Brushless copper tubing cutter adjusts to ODs up to 2-1/8 in.
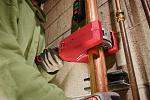
HGG Profiling Equipment names area sales manager
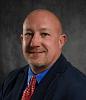
- Industry Events
Pipe and Tube Conference
- May 21 - 22, 2024
- Omaha, NE
World-Class Roll Forming Workshop
- June 5 - 6, 2024
- Louisville, KY
Advanced Laser Application Workshop
- June 25 - 27, 2024
- Novi, MI
Precision Press Brake Certificate Course
- July 31 - August 1, 2024
- Elgin,