Industrial Systems and Manufacturing Instructor
- FMA
- The Fabricator
- FABTECH
- Canadian Metalworking
Categories
- Additive Manufacturing
- Aluminum Welding
- Arc Welding
- Assembly and Joining
- Automation and Robotics
- Bending and Forming
- Consumables
- Cutting and Weld Prep
- Electric Vehicles
- En Español
- Finishing
- Hydroforming
- Laser Cutting
- Laser Welding
- Machining
- Manufacturing Software
- Materials Handling
- Metals/Materials
- Oxyfuel Cutting
- Plasma Cutting
- Power Tools
- Punching and Other Holemaking
- Roll Forming
- Safety
- Sawing
- Shearing
- Shop Management
- Testing and Measuring
- Tube and Pipe Fabrication
- Tube and Pipe Production
- Waterjet Cutting
Industry Directory
Webcasts
Podcasts
FAB 40
Advertise
Subscribe
Account Login
Search
How can community college welding programs update, evolve?
- By Gina Cutts
- November 27, 2023
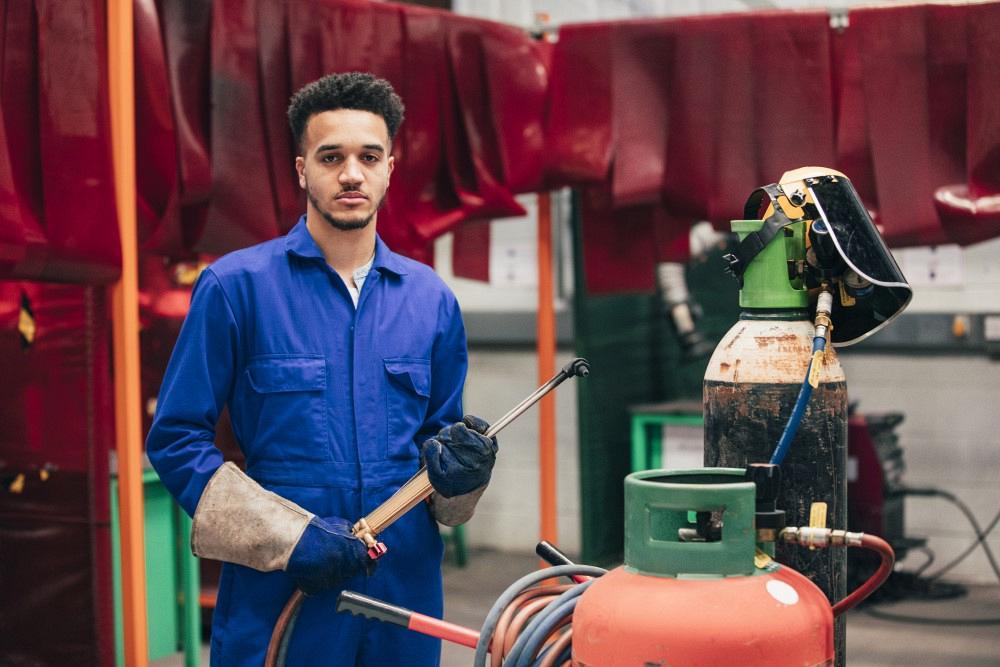
As the welding industry becomes more advanced, sustainable, safe, versatile, and connected, Gina Cutts says community college welding programs must adapt and update to meet employers’ needs. SolStock / E+ / Getty Images
I speak with educators and employers across the country and this subject continuously comes up. Community college welding programs must adapt and update curriculum to ensure students are equipped with the necessary skills to meet the demands of today’s industry.
Once upon a time, community colleges were the backbone of the welding industry, providing students with essential skills and knowledge to help them embark on successful careers. Potential employers from companies and unions regularly offered positions to graduates. Unfortunately, this is not the reality anymore.
As industry evolves and technology advances, welding programs must provide training on these advanced technologies. Today’s welding machines have become more sophisticated, incorporating automation, computerized controls, and robotics. Students should learn how to operate and troubleshoot computer-controlled welding systems, as these are increasingly prevalent in today's industrial settings.
Industry is placing a growing emphasis on sustainability and environmental responsibility. College programs should incorporate lessons on environmentally friendly welding practices, including the use of eco-friendly welding gases, efficient energy utilization, and waste reduction. Welders with knowledge in these areas are more likely to meet the demands of eco-conscious employers and contribute positively to the industry's environmental impact.
Another critical aspect of modern welding is safety. Protocols and procedures must be updated accordingly as new welding techniques and equipment are introduced. Programs should ensure that students receive comprehensive safety training, covering not only traditional welding hazards like sparks and fumes but also the specific safety measures required when working with advanced equipment and automation systems.
In addition to technology and safety, today's welding industry values versatility. Welders are expected to have a broader skill set that includes expertise in various welding processes (MIG, TIG, and stick welding), materials (steel, aluminum, and stainless steel), and certifications. Community college programs should offer a diverse curriculum that exposes students to a wide range of welding techniques and materials, preparing them to meet the diverse needs of modern industries.
Moreover, soft skills such as problem-solving, teamwork, and communication are increasingly important in the workplace. Welding programs should incorporate opportunities for students to develop these skills through group projects, real-world scenarios, and communication training. Soft skills are essential for welders to collaborate effectively with colleagues and adapt to changing work environments.
Welding educators should prioritize establishing strong connections with local industries and employers. Maintain active advisory boards with diverse industry professionals, ensuring programs stay up to date on the latest trends and skills requirements. These partnerships often lead to internship and job placement opportunities for qualified students, ensuring that graduates are well prepared for the workforce.
Community college programs play a crucial role in preparing individuals for successful welding careers. To remain relevant and effective, these programs must evolve alongside the industry. By doing so, community college welding programs can continue producing skilled and adaptable welders ready to meet present-day demands. After all, students are paying for a quality education and committing their valuable time and effort to achieve their goals. As educators, we must give them a great return on their investment.
subscribe now
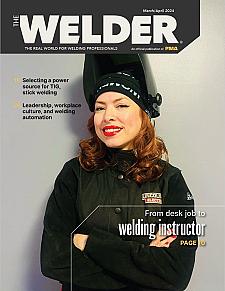
The Welder, formerly known as Practical Welding Today, is a showcase of the real people who make the products we use and work with every day. This magazine has served the welding community in North America well for more than 20 years.
start your free subscriptionAbout the Author
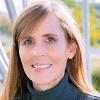
About the Publication
- Stay connected from anywhere
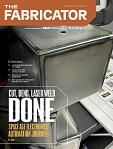
Easily access valuable industry resources now with full access to the digital edition of The Fabricator.
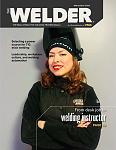
Easily access valuable industry resources now with full access to the digital edition of The Welder.
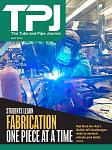
Easily access valuable industry resources now with full access to the digital edition of The Tube and Pipe Journal.
- Podcasting
- Podcast:
- The Fabricator Podcast
- Published:
- 04/16/2024
- Running Time:
- 63:29
In this episode of The Fabricator Podcast, Caleb Chamberlain, co-founder and CEO of OSH Cut, discusses his company’s...
- Trending Articles
Sheffield Forgemasters makes global leap in welding technology
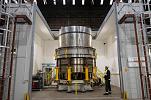
ESAB unveils Texas facility renovation
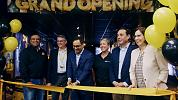
Engine-driven welding machines include integrated air compressors
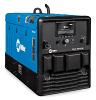
How welders can stay safe during grinding
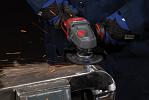
The impact of sine and square waves in aluminum AC welding, Part I
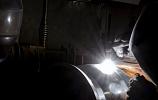
- Industry Events
16th Annual Safety Conference
- April 30 - May 1, 2024
- Elgin,
Pipe and Tube Conference
- May 21 - 22, 2024
- Omaha, NE
World-Class Roll Forming Workshop
- June 5 - 6, 2024
- Louisville, KY
Advanced Laser Application Workshop
- June 25 - 27, 2024
- Novi, MI