Industrial Systems and Manufacturing Instructor
- FMA
- The Fabricator
- FABTECH
- Canadian Metalworking
Categories
- Additive Manufacturing
- Aluminum Welding
- Arc Welding
- Assembly and Joining
- Automation and Robotics
- Bending and Forming
- Consumables
- Cutting and Weld Prep
- Electric Vehicles
- En Español
- Finishing
- Hydroforming
- Laser Cutting
- Laser Welding
- Machining
- Manufacturing Software
- Materials Handling
- Metals/Materials
- Oxyfuel Cutting
- Plasma Cutting
- Power Tools
- Punching and Other Holemaking
- Roll Forming
- Safety
- Sawing
- Shearing
- Shop Management
- Testing and Measuring
- Tube and Pipe Fabrication
- Tube and Pipe Production
- Waterjet Cutting
Industry Directory
Webcasts
Podcasts
FAB 40
Advertise
Subscribe
Account Login
Search
Experimenting with aluminum GMAW pulse settings
- By Gina Cutts
- UPDATED September 29, 2023
- September 26, 2023
Welding aluminum using gas metal arc welding (GMAW) is gaining popularity because it’s versatile, efficient, recyclable, and produces strong, clean welds. Aerospace, automotive, shipbuilding, manufacturing, and energy sectors need skilled aluminum welders—and they need them now.
Knowing when and how to use the pulse setting is a start, given aluminum’s high thermal conductivity and susceptibility to distortion. Pulse involves alternating between high-current pulses and low-current background settings. Pulse welding controls heat input, reduces distortion, and improves the overall weld quality.
Understanding the following settings will help you to dial in your machine properly:
- Peak current (Ipeak) is the highest current level during the pulse cycle. It affects the depth of penetration and the overall weld profile. Higher peak current can lead to deeper penetration, but it also increases the risk of burn-through, especially in thin materials.
- Background current (Ibase) is the lower current level that occurs between pulse peaks. It helps maintain arc stability and controls heat input during the welding process.
- Pulse frequency (Hz) is the number of pulses per second. It influences the overall travel speed and width of the weld bead. Higher frequencies can provide a finer, narrower weld bead, while lower frequencies can produce a wider bead.
- Pulse width (milliseconds) is the duration of the high-current pulse. It affects the amount of heat transferred to the workpiece. Longer pulse widths allow for more heat input, while shorter pulse widths minimize heat input.
- Peak time is the percentage of the pulse cycle during which the high-current pulse is active. It influences the balance between the peak current and the background current. A higher peak time results in more energy being delivered during the high-current pulse.
- Ramp-up and ramp-down time measures the moment when the current rises from the background level to the peak level at the beginning of the pulse and decreases back to the background level at the end of the pulse. Controlling these times can reduce the risk of spatter and improve arc starting stability.
Anyone who welds aluminum regularly knows the following, but these points are worth repeating:
- Watch your welding travel speed. Since travel speed affects overall heat input and penetration, synchronizing your travel speed with pulse settings is crucial to achieving desired weld characteristics. Find your rhythm!
- Use argon as your shielding gas. Protecting the weld area from atmospheric contamination and preventing oxidation is a priority.
- Select an electrode type that is compatible with the base aluminum alloy that you’re welding.
- Pay attention to joint design and preparation, which are crucial for successful pulse welding of aluminum. Ensure that joints are clean and properly fit with minimal gaps. I cannot stress enough how much the cleanliness of your aluminum affects your weld.
Pulse settings can vary depending on material thickness, joint design, and desired bead profiles. Consult welding procedure specifications, manufacturer guidelines, and experienced welders when setting aluminum GMAW pulse parameters
subscribe now
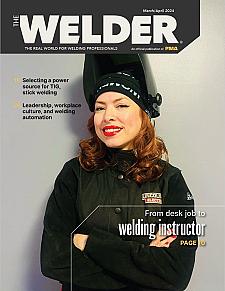
The Welder, formerly known as Practical Welding Today, is a showcase of the real people who make the products we use and work with every day. This magazine has served the welding community in North America well for more than 20 years.
start your free subscriptionAbout the Author
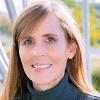
About the Publication
- Stay connected from anywhere
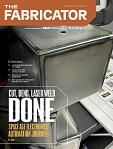
Easily access valuable industry resources now with full access to the digital edition of The Fabricator.
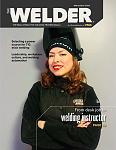
Easily access valuable industry resources now with full access to the digital edition of The Welder.
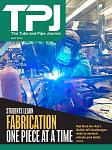
Easily access valuable industry resources now with full access to the digital edition of The Tube and Pipe Journal.
- Podcasting
- Podcast:
- The Fabricator Podcast
- Published:
- 04/16/2024
- Running Time:
- 63:29
In this episode of The Fabricator Podcast, Caleb Chamberlain, co-founder and CEO of OSH Cut, discusses his company’s...
- Trending Articles
Sheffield Forgemasters makes global leap in welding technology
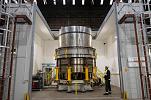
ESAB unveils Texas facility renovation
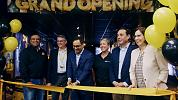
Engine-driven welding machines include integrated air compressors
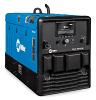
How welders can stay safe during grinding
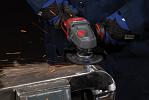
The impact of sine and square waves in aluminum AC welding, Part I
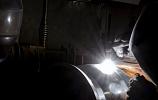
- Industry Events
16th Annual Safety Conference
- April 30 - May 1, 2024
- Elgin,
Pipe and Tube Conference
- May 21 - 22, 2024
- Omaha, NE
World-Class Roll Forming Workshop
- June 5 - 6, 2024
- Louisville, KY
Advanced Laser Application Workshop
- June 25 - 27, 2024
- Novi, MI