Applications Engineer/CWI
- FMA
- The Fabricator
- FABTECH
- Canadian Metalworking
Categories
- Additive Manufacturing
- Aluminum Welding
- Arc Welding
- Assembly and Joining
- Automation and Robotics
- Bending and Forming
- Consumables
- Cutting and Weld Prep
- Electric Vehicles
- En Español
- Finishing
- Hydroforming
- Laser Cutting
- Laser Welding
- Machining
- Manufacturing Software
- Materials Handling
- Metals/Materials
- Oxyfuel Cutting
- Plasma Cutting
- Power Tools
- Punching and Other Holemaking
- Roll Forming
- Safety
- Sawing
- Shearing
- Shop Management
- Testing and Measuring
- Tube and Pipe Fabrication
- Tube and Pipe Production
- Waterjet Cutting
Industry Directory
Webcasts
Podcasts
FAB 40
Advertise
Subscribe
Account Login
Search
Tips for welding wire drum storage, handling, and setup
Proper care can reduce consumables costs, production interruptions, damage, and product waste
- By Lewis Nerone
- August 16, 2023
- Article
- Consumables
Follow best practices for drum storage, handling, and setup to help eliminate issues with wire feeding or performance and improve operations.
For automated welding applications or high-production welding operations, purchasing filler metal in wire drums can deliver significant gains in productivity and throughput. Because the quantity of welding wire in drum packaging is much greater than that of conventional wire spools and coils, operators can spend less downtime on wire changeover.
However, drums contain so much wire. Improper storage, handling, or setup can result in damage or product waste—driving up consumable costs and possibly interrupting production. Following some best practices can help optimize results.
Welding Wire Drum Sizes and Types
Depending on the filler metal manufacturer and the type of wire being used—solid, metal-cored, or flux-cored—conventional welding wire spools for industrial applications generally weigh between 33 lbs. and 60 lbs., but can be as light as 12 lbs.
Compare this to wire drum options, which range from 500 to 1,000 lbs. for robotic and hand-held welding. Solid and metal-cored wires often come in larger drums of up to 1,000 lbs., while flux-cored wires and any type of larger-diameter wires often come in 500- to 600-lb. drums.
Welding wire drums are available in several styles:
- Standard drums are the conventional style in the industry and designed for good wire feedability without using a turntable or any special attachments to aid in wire feeding. Some standard drums on the market include features that reduce the twist of the wire as it feeds out of the drum to help ensure straight wire feeding. This can be especially important in robotic welding applications, where having a lot of cast to the wire can cause it to wander as it exits the contact tip, resulting in overwelding. In robotic welding and other highly repeatable welding applications, it’s important for the wire to come out in the same place every time to gain consistent weld quality and to properly fuse the weld.
- Octagonal drums are typically made from completely recyclable material. They carry the same amount of wire as a standard drum, but they can be flattened and recycled once empty, taking up less space on the plant floor. Standard drums, in comparison, use a metal ring as part of the cylinder and often use glue in the drum itself, making them harder to recycle. And because they cannot be folded down or flattened, empty standard drums take up more space on the manufacturing floor. Another benefit of octagonal drums is their lids can act as the drum cone that wire can feed directly out of, which means one less setup step.
- Aluminum drums contain aluminum welding wire. These 10-sided drums often include plastic components in place of conventional metal or cardboard components for optimal aluminum wire delivery.
Tips for Proper Drum Storage, Handling, and Setup
Optimizing performance when using welding wire drums comes down to following best practices for storage, handling, and setup. Consider these six tips.
1. Don’t Stack the Drums. Stacking wire drums for storage is not recommended, especially when using octagonal drums. Stacking compromises the integrity and durability of the container, which can negatively impact wire feedability. Storing them in a stack can also be a safety hazard, as the very heavy drums could fall or tip over, causing damage to the area or potential injury to someone.
2. Store Drums in a Dry Place. Wire drums should be stored indoors in a dry, climate-controlled environment with low humidity. Storing drums outside can cause condensation to form on the wires, resulting in wire contamination that affects weld quality.
It’s also recommended to keep the drums at ground level and avoid storing them on an elevated surface, since this could cause the containers to fall or tip over and cause a safety hazard.
Because drums contain so much filler metal wire, improper storage that damages the product means the loss of much more wire compared to smaller spools—and at a higher cost. Also, losing an entire wire drum to poor storage can potentially slow down production, lead to additional costs associated with production delays, and require filler metal replacement.
Octagonal drums carry the same amount of wire as a standard drum; they take up less space on the shop floor because they can be flattened and recycled once empty.
3. Move Drums With Care. The movement of drums can affect the integrity of the packaging and the wire inside. To move drums for storage or setup, always lift from the bottom using a forklift, hand truck, or crane. Wire drums have built-in straps to help properly distribute weight when the drums are lifted. Most drum manufacturers also include a lifting mechanism on the drum’s exterior. Make sure to use the straps and the proper lifting mechanism or else the drum can be torn. Lift drums as little as possible, as lifting poses the highest risk of damage to the drum and the wire, in addition to the threat of injury to personnel. If lifting a drum is absolutely necessary, use the drum’s built-in straps or the manufacturer’s recommended lifting mechanism to avoid accidentally tearing the drum walls.
Always move wire drums at a steady pace and make sure there is a clear path for moving. A slow, steady pace can prevent the load from tipping over. When lowering the drum to the ground, be sure the spot where it’s placed is level and not elevated.
Don’t remove the pallet that is built into the bottom of many wire drums, as it helps support the wire inside and provides a sturdy lift point for a forklift or pallet jack. Also, take care to avoid gouging or cutting the drum walls with the forklift during moving. Damage to a drum can also damage the wire inside, which can cause poor wire feeding and premature wear to other consumables like the liner, contact tip, and drive rolls.
4. Check the Conduit During Setup. When operations encounter issues with a wire drum, it often stems from improper setup and wire feeding. Proper drum setup can eliminate many wire feeding issues that increase the risk of poor arc starts, porosity, undercut, and poor fusion.
Be aware of how much conduit is used in drum setup. Too much conduit means the wire must travel a longer distance between the drum and the welding power source. This creates more friction and causes poor wire feeding. In addition, a longer distance means the machine must work harder to feed the wire, increasing the risk of wearing out the drive roll motors in the wire feeder. Excessive friction on the wire can cause it to burn back to the contact tip, which can decrease consumable life and cause downtime.
A conduit that is too long often stems from poor weld cell layout. Be sure to set up the weld cell with the appropriate amount of reach for the part. The conduit should not be restrictive—especially in a robotic weld cell—but there should not be an excessive amount of conduit either. It should be just long enough to reach the feeder. Take the shortest, straightest path possible with the conduit and use a maximum of three bends, with each bend using a minimum radius of 24 in. to avoid harsh bends. Make sure the conduit exits vertically from the top of the drum, with 12 to 18 in. of straight conduit before it gradually bends into the welding power source.
It's also important to choose the right conduit for the welding wire being used. For metal-cored and flux-cored wire—which are softer than solid wire—use a plastic conduit so it doesn’t shave off or burr the wire. A stiffer steel conduit works well for solid wire.
5. Don’t Reuse Drum Lids or Float Rings. Most wire drums include a float ring on the inside to keep the wire level and compressed and to help the wire feed out of the drum consistently. Drums of solid welding wire often have a metal float ring because solid wire has more cross-sectional area; a heavier float ring is necessary to ensure that the wire feeds well and doesn’t tangle. Plastic float rings are typically used for softer alloys like aluminum.
Don’t attempt to remove the float ring, as removing it can cause the wire to bind or tangle inside the drum. Also, float rings should not be reused from one drum to another. When using an octagonal drum and feeding directly out of the lid, be sure to use the new lid that comes with that drum rather than reusing an old lid.
The wire should exit the drum through the center of the float ring. Also, be sure to remove the rubber band that is often used to hold wire in place in a new drum. Failure to remove the band can cause the wire to snag on it and prevent proper feeding. When using a drum hood, center it securely on top of the drum. Check that the drum hood is the proper size since drums vary in size, depending on the manufacturer.
Some aluminum alloys require a top hat spinner or turntable to help guide the wire as it spins and exits the drum. This accessory reduces tension on the wire as it is fed. These are common when using larger-diameter wires, such as those for a submerged arc welding process. Be sure the spinner is properly installed, or it could result in feeding problems.
Always follow the wire manufacturer’s setup instructions for the best results.
6. Monitor the Shelf Life. Most wire drums have a warranty of one to two years for unopened drums. It is best practice to use the wire as quickly as possible and avoid moving it once a drum is opened. After the rubber band holding the wire has been removed, some of the compression on the wire itself is lost and the wire tends to move around more inside the drum. Leaving the drum where it’s already positioned can help eliminate this movement and reduce the potential for tangles or wire overlap.
Optimizing Wire Drum Performance
Welding wire drums offer the potential for significant productivity gains and less downtime for wire changeover. Following best practices for drum storage, handling, and setup can eliminate issues with wire feeding or performance—improving operations as a result.
About the Author
About the Publication
Related Companies
subscribe now
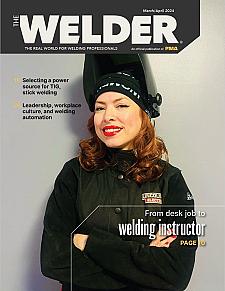
The Welder, formerly known as Practical Welding Today, is a showcase of the real people who make the products we use and work with every day. This magazine has served the welding community in North America well for more than 20 years.
start your free subscription- Stay connected from anywhere
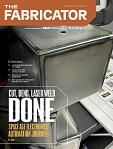
Easily access valuable industry resources now with full access to the digital edition of The Fabricator.
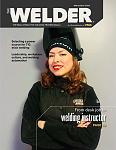
Easily access valuable industry resources now with full access to the digital edition of The Welder.
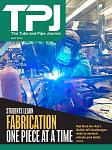
Easily access valuable industry resources now with full access to the digital edition of The Tube and Pipe Journal.
- Podcasting
- Podcast:
- The Fabricator Podcast
- Published:
- 04/16/2024
- Running Time:
- 63:29
In this episode of The Fabricator Podcast, Caleb Chamberlain, co-founder and CEO of OSH Cut, discusses his company’s...
- Trending Articles
Sheffield Forgemasters makes global leap in welding technology
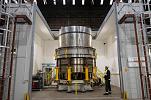
ESAB unveils Texas facility renovation
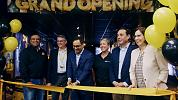
Engine-driven welding machines include integrated air compressors
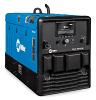
How welders can stay safe during grinding
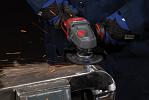
The impact of sine and square waves in aluminum AC welding, Part I
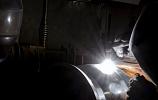
- Industry Events
16th Annual Safety Conference
- April 30 - May 1, 2024
- Elgin,
Pipe and Tube Conference
- May 21 - 22, 2024
- Omaha, NE
World-Class Roll Forming Workshop
- June 5 - 6, 2024
- Louisville, KY
Advanced Laser Application Workshop
- June 25 - 27, 2024
- Novi, MI