Independent welding consumables professional
- FMA
- The Fabricator
- FABTECH
- Canadian Metalworking
Categories
- Additive Manufacturing
- Aluminum Welding
- Arc Welding
- Assembly and Joining
- Automation and Robotics
- Bending and Forming
- Consumables
- Cutting and Weld Prep
- Electric Vehicles
- En Español
- Finishing
- Hydroforming
- Laser Cutting
- Laser Welding
- Machining
- Manufacturing Software
- Materials Handling
- Metals/Materials
- Oxyfuel Cutting
- Plasma Cutting
- Power Tools
- Punching and Other Holemaking
- Roll Forming
- Safety
- Sawing
- Shearing
- Shop Management
- Testing and Measuring
- Tube and Pipe Fabrication
- Tube and Pipe Production
- Waterjet Cutting
Industry Directory
Webcasts
Podcasts
FAB 40
Advertise
Subscribe
Account Login
Search
Consumables Corner: Why you shouldn’t use shielding gas with self-shielded FCAW electrodes
Using this welding method is not only incorrect, it's a total waste of money
- By Nino Mascalco and Rob Koltz
- August 26, 2020
- Article
- Consumables
Q: We use C25 argon/carbon dioxide blend shielding gas throughout our shop. We do some MIG welding but mostly use flux-cored arc welding (FCAW). We use a gas-shielded flux core, but in some areas we use self-shielded flux core. The welders like to use shielding gas with the self-shielded wire because it reduces smoke generation. Is there any problem with doing so?
A: Yes. Using a shielding gas with a self-shielded flux core can cause several problems.
Flux-cored welding electrodes come in two types: gas-shielded and self-shielded. The gas-shielded electrodes use an external gas along with the internal flux to protect the molten weld puddle from the atmosphere. They also generate a slag that cleanses (or deoxidizes) the weld by reacting with impurities in the weld pool to create a clean, mechanically sound weld. Slag reacts with other elements in the weld puddle and forms compounds that float to the surface, which are then trapped in the slag layer that is removed after welding.
In contrast, self-shielded electrodes rely solely on the internal flux to generate both the shielding gas and slag. The deposition efficiency of these two electrodes is different because the self-shielded electrode must generate its own gas shield. The gas-shielded FCAW process has a weld efficiency in the mid to high 80% range, while the self-shielded FCAW efficiency is generally in the 70% range.
Both wires are manufactured similarly by forming the sheath into a trough and filling it with a fine particle flux. The sheath is then formed into a closed tube and drawn down to its final diameter.
The flux and wire chemistry is developed by the wire manufacturer, which is responsible for meeting the American Welding Society’s final weld metal testing requirements to comply with the intended classification. Each wire manufacturer tries to create a flux that produces a flux-core wire with good arc characteristics, welder appeal, easily removable slag, low spatter and fume, and the right amount of deoxidizers for the intended shielding gas. Both wire types are designed to produce a weld deposit that has an ideal chemistry makeup based on the shielding gas used to produce the desired mechanical test results.
Some gas-shielded flux-cored wires are classified to be welded with either 100% carbon dioxide or a C25 gas mix. A few FCAW wires on the market are dual-certified by the manufacturer for use with either type of shielding gas, while self-shielded flux-cored wires are designed to produce their own shielding gas. This is accomplished by using flux ingredients that when put through the intense heat of the welding arc create a chemical reaction, and one of the byproducts is a shielding gas for the weld puddle, generally carbon dioxide.
Carbon dioxide or argon shielding gases at standard temperature pressure are nonreactive and remain so during welding at short distances from the welding plasma or arc cone. They protect the molten weld puddle by displacing the atmospheric air long enough for the weld to solidify and prevent porosity. However, the extreme temperatures within the arc cone cause the carbon dioxide to disassociate into carbon, oxygen, and carbon monoxide. These components are active and react with different parts of the molten weld puddle and slag to scavenge up impurities and clean the weld metal deposit.
Problems arise when the shielding gas affects the chemistry of the weld metal deposit. Two common alloys, manganese and silicon, that are part of the chemical makeup of the metal sheath or are added to the flux act as deoxidizers. Deoxidizers bond with the oxygen that is dissolved in the weld pool and end up in the slag layer. For example, if the manganese isn't used properly per design, it will act as an alloying agent in the weld metal, creating a potentially brittle weld situation.
Flux-cored wires are designed to produce weld metal chemistry with optimal amounts of alloy to meet specific strength, impact, and elongation target ranges. If the incorrect shielding gas is used, or a shielding gas is used with a self-shielded wire, the resulting weld chemistry may be out of the expected range, which ultimately could deliver catastrophic results. This may cause weld cracking, porosity, or worm tracks (surface porosity caused by trapped gas between the solidified slag and a still molten puddle).
Something else to consider is cost. Using a shielding gas with a self-shielded wire is not only incorrect, it's a total waste of money. Self-shielded wires are meant for field-service welding applications, so you may want to reconsider why it is being used inside a manufacturing facility. Occasionally this is done because of the presence of strong air currents throughout the shop, which can compromise shielding gas coverage, resulting in weld porosity.
Investing in weld curtains or making some changes to address the strong air currents may be a better option. By doing so you can convert from the self-shielded wire to a dual-shield or even a solid wire if it is a good match for your application. In most cases, the costs are offset by a higher-deposition filler metal, which is realized through reduced weld hours and reduced non-value-added postweld cleanup.
About the Authors
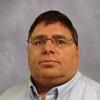
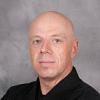
Rob Koltz
Application Engineer
411 S. Ebenezer Rd.
Florence, 29501
636-485-2253
About the Publication
Related Companies
subscribe now
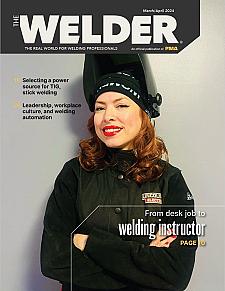
The Welder, formerly known as Practical Welding Today, is a showcase of the real people who make the products we use and work with every day. This magazine has served the welding community in North America well for more than 20 years.
start your free subscription- Stay connected from anywhere
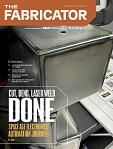
Easily access valuable industry resources now with full access to the digital edition of The Fabricator.
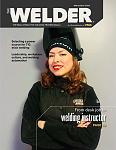
Easily access valuable industry resources now with full access to the digital edition of The Welder.
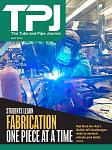
Easily access valuable industry resources now with full access to the digital edition of The Tube and Pipe Journal.
- Podcasting
- Podcast:
- The Fabricator Podcast
- Published:
- 04/16/2024
- Running Time:
- 63:29
In this episode of The Fabricator Podcast, Caleb Chamberlain, co-founder and CEO of OSH Cut, discusses his company’s...
- Trending Articles
Sheffield Forgemasters makes global leap in welding technology
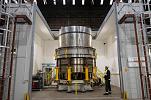
ESAB unveils Texas facility renovation
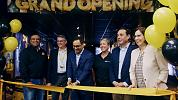
Engine-driven welding machines include integrated air compressors
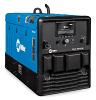
How welders can stay safe during grinding
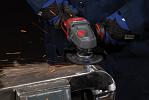
The impact of sine and square waves in aluminum AC welding, Part I
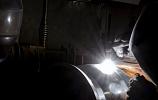
- Industry Events
16th Annual Safety Conference
- April 30 - May 1, 2024
- Elgin,
Pipe and Tube Conference
- May 21 - 22, 2024
- Omaha, NE
World-Class Roll Forming Workshop
- June 5 - 6, 2024
- Louisville, KY
Advanced Laser Application Workshop
- June 25 - 27, 2024
- Novi, MI