Independent welding consumables professional
- FMA
- The Fabricator
- FABTECH
- Canadian Metalworking
Categories
- Additive Manufacturing
- Aluminum Welding
- Arc Welding
- Assembly and Joining
- Automation and Robotics
- Bending and Forming
- Consumables
- Cutting and Weld Prep
- Electric Vehicles
- En Español
- Finishing
- Hydroforming
- Laser Cutting
- Laser Welding
- Machining
- Manufacturing Software
- Materials Handling
- Metals/Materials
- Oxyfuel Cutting
- Plasma Cutting
- Power Tools
- Punching and Other Holemaking
- Roll Forming
- Safety
- Sawing
- Shearing
- Shop Management
- Testing and Measuring
- Tube and Pipe Fabrication
- Tube and Pipe Production
- Waterjet Cutting
Industry Directory
Webcasts
Podcasts
FAB 40
Advertise
Subscribe
Account Login
Search
Consumables Corner: What are the requirements for low-hydrogen electrodes?
- By Nino Mascalco, Rob Koltz, and Steve Sigler
- May 17, 2019
- Article
- Consumables
Q: Our company was contracted for a project and the customer specified that we use low-hydrogen electrodes for all welding processes. We would use shielded metal arc welding (SMAW) for the outdoor work and gas metal arc welding (GMAW) or flux-cored arc welding (FCAW) for the indoor work. In the past we’ve conducted tests using plain 7018 electrodes and have had really good results. Is it really necessary for us to follow the customer's request?
A: Good question, and the short answer is yes, it is necessary for you to follow the customer’s request.
You stated that the customer specified low-hydrogen electrodes, but did they specify a hydrogen limit? The "8" designator at the end of an SMAW electrode classifies it as low-hydrogen. However, there are different levels of low-hydrogen electrodes, and within industry the most commonly referenced value is H4.
Since we are not familiar with the specifics of the contract, we can only provide insight as to why you would want to use an H4 low-hydrogen electrode. Let's start with an overview of what a low-hydrogen electrode is and why it's an important variable in weld manufacturing.
According to the American Welding Society, an HX designator, with the X being a numerical value of 2, 4, 8, or 16, represents the maximum allowable milliliter amount of diffusible hydrogen per 100 grams of deposited weld metal. An H4 classification means no more than 4 ml of hydrogen per 100 grams of deposited weld metal.
A filler metal that is classified as H4 is typically manufactured to produce deposited weld metal with less than 4 ml of diffusible hydrogen, but over time it will pick up a small amount of moisture that will increase the amount of hydrogen that ends up in the weld metal. However, if you follow recommendations for proper storage and handling and use correct welding practices, the resulting deposited weld metal should not exceed the H4 limit.
From an electrode classification standpoint, any electrode that is designated H16 or lower is considered to be low-hydrogen. For all practical purposes, you are most likely using all low-hydrogen electrodes. If, however, your customer stated H4 as the upper limit, then you would need to make sure all welding electrodes you use on the project have the H4 designator.
The purpose of controlling the amount of hydrogen in weld metal is to reduce the potential for hydrogen-induced cracking (HIC). Moisture in the electrode coating; in flux of the FCAW wire; or contamination in the weld joint from things like paint, grease, or dirt can contribute to the amount of available hydrogen that ends up in the weld metal.
The extremely hot temperature of the welding arc causes disassociation of moisture (H2O). Since hydrogen is the smallest atom, when present it can migrate freely between the crystalline structures of the weld or base material. It then seeks out areas of low resistance, which happen to be the boundaries of large grains that are typically found in the heat-affected zone of the weld joint. Hydrogen by itself is unstable and will seek out other hydrogen atoms to form molecular hydrogen (H2). This creates high internal stresses that can lead to cracking if there is a susceptible microstructure such as martensite or too much hydrogen.
Depending on your customer's requirements and the types of base materials you are using for the project, an H4-classified filler metal should adequately assist in preventing HIC.
About the Authors
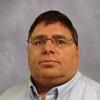
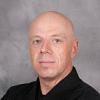
Rob Koltz
Application Engineer
411 S. Ebenezer Rd.
Florence, 29501
636-485-2253
Steve Sigler
Application Engineer
411 S. Ebenezer Rd.
Florence, South Carolina 29501
636-485-2253
About the Publication
Related Companies
subscribe now
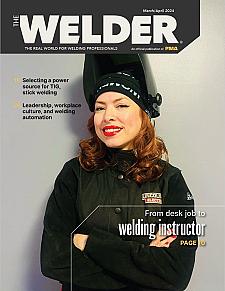
The Welder, formerly known as Practical Welding Today, is a showcase of the real people who make the products we use and work with every day. This magazine has served the welding community in North America well for more than 20 years.
start your free subscription- Stay connected from anywhere
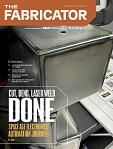
Easily access valuable industry resources now with full access to the digital edition of The Fabricator.
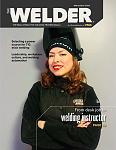
Easily access valuable industry resources now with full access to the digital edition of The Welder.
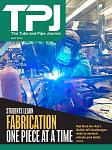
Easily access valuable industry resources now with full access to the digital edition of The Tube and Pipe Journal.
- Podcasting
- Podcast:
- The Fabricator Podcast
- Published:
- 04/16/2024
- Running Time:
- 63:29
In this episode of The Fabricator Podcast, Caleb Chamberlain, co-founder and CEO of OSH Cut, discusses his company’s...
- Trending Articles
Sheffield Forgemasters makes global leap in welding technology
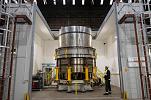
ESAB unveils Texas facility renovation
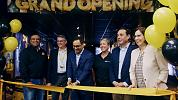
Engine-driven welding machines include integrated air compressors
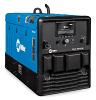
How welders can stay safe during grinding
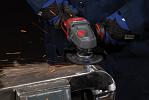
The impact of sine and square waves in aluminum AC welding, Part I
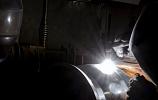
- Industry Events
16th Annual Safety Conference
- April 30 - May 1, 2024
- Elgin,
Pipe and Tube Conference
- May 21 - 22, 2024
- Omaha, NE
World-Class Roll Forming Workshop
- June 5 - 6, 2024
- Louisville, KY
Advanced Laser Application Workshop
- June 25 - 27, 2024
- Novi, MI