Independent welding consumables professional
- FMA
- The Fabricator
- FABTECH
- Canadian Metalworking
Categories
- Additive Manufacturing
- Aluminum Welding
- Arc Welding
- Assembly and Joining
- Automation and Robotics
- Bending and Forming
- Consumables
- Cutting and Weld Prep
- Electric Vehicles
- En Español
- Finishing
- Hydroforming
- Laser Cutting
- Laser Welding
- Machining
- Manufacturing Software
- Materials Handling
- Metals/Materials
- Oxyfuel Cutting
- Plasma Cutting
- Power Tools
- Punching and Other Holemaking
- Roll Forming
- Safety
- Sawing
- Shearing
- Shop Management
- Testing and Measuring
- Tube and Pipe Fabrication
- Tube and Pipe Production
- Waterjet Cutting
Industry Directory
Webcasts
Podcasts
FAB 40
Advertise
Subscribe
Account Login
Search
Consumables Corner: Heat input and discoloration in stainless steel welding
- By Nino Mascalco and Rob Koltz
- April 15, 2020
- Article
- Consumables
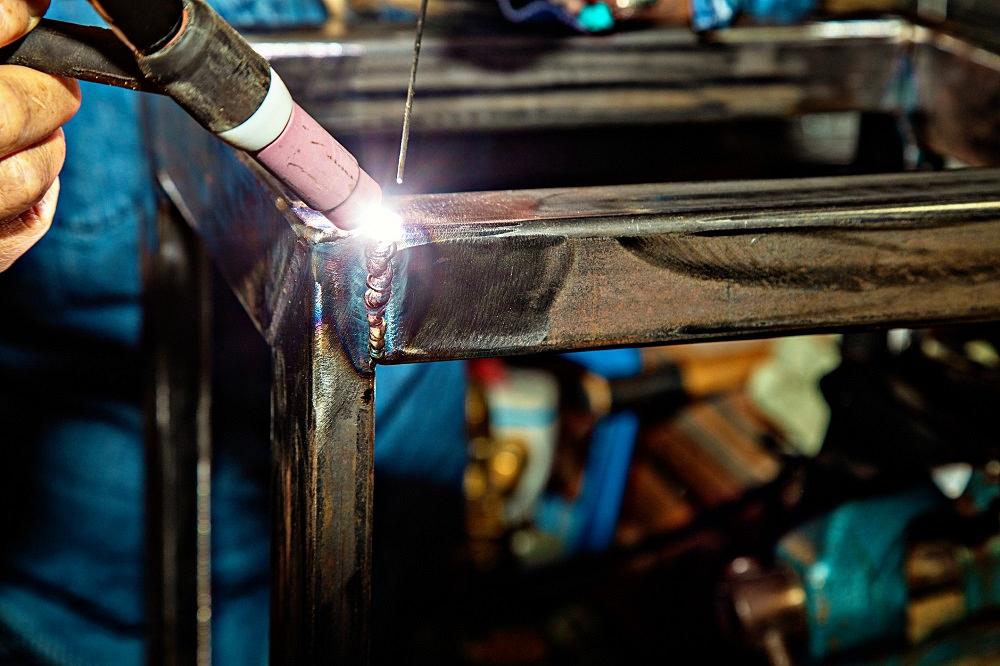
Nino Mascalo and Rob Koltz discuss heat input and weld discoloration in stainless steel welds. Getty Images
Q: What are some ways to identify acceptable levels of heat input other than visually? We typically classify a straw-colored weld as good, a light- to medium-blue weld as borderline, and a dark blue to black weld as poor because it contains carbon precipitation.
On a related note, how can I reduce heat input discoloration if my amperage is in the range it should be for the material thickness? Does stainless steel pulse welding follow the traditional theory that the amperage should be equal to the material thickness (10 ga. = 135 amps)?
A: Based on the information you provided, we're going to assume you are asking only about stainless steel and that you are using gas metal arc welding (GMAW). However, the answer would apply to most stainless steel welding processes.
Technically, the only way to identify the actual heat input (HI) is by measuring the travel speed and then performing the following calculation:
(Volts x Amps x 60)/(Travel speed (IPM)) = [Joules/Inch]
Please note that it is common for HI values to be expressed as [kilojoules/inch (kJ/in.)], which is a simple unit conversion. HI is a measure of energy put into making a weld along with the corresponding cooling rate to deliver a weld of acceptable quality. By performing this calculation, you will obtain a value that allows you to compare your process to known HI values.
However, in most cases, stainless steel HI should not exceed 50 kJ/in., but occasionally it needs to be lower due to the intended service application and the material’s thickness. HI values are intended to deliver the weld’s cooling rate without forming any undesirable metallurgical phases.
The three most important variables that determine stainless steel weld discoloration/oxidation are amperage, travel speed, and quality of shielding gas coverage. If your amperage and travel speeds are within range of the stated upper limit with respect to the overall heat input, then you may want to take a closer look at your shielding gas quality and coverage.
Ignoring all "what if" scenarios, the color descriptions you stated are generally acceptable to gauge HI in stainless steel welds. In fact, the American Welding Society has coloration charts available for welds made with acceptable HI, as well as ones that show color changes that correspond to variations in shielding gas compositions.
Since gas tungsten arc welding (GTAW) typically calls for 100% argon for shielding the back side of the weld, discoloration varies because of the amounts of contamination present. If the shielding gas is impure or highly contaminated by the atmosphere, then the resulting weld will have more discoloration. In these cases, welds will generally exhibit accelerated degradation in service and are undesirable.
For GMAW, though, you must consider several other variables that may affect the discoloration that can occur. Shielding gas and the metal transfer mode you use play roles in your end result.
Stainless steel GMAW doesn’t usually call for pure argon shielding gas. Instead, you’ll usually see numerous blends of two, three, and even four gas combinations for various applications. The goals for each blend are to reduce distortion on thin materials, reduce discoloration or oxidation, maintain material integrity, reduce postweld cleaning, and increase productivity.
One of the most desired blends is helium/argon/carbon dioxide. Helium has a high ionization potential, which increases the effective energy produced in the welding arc. This in turn produces better wetting action of the weld puddle and therefore is beneficial in achieving higher travel speeds. The problem with helium is that it is extremely expensive. A cost-effective alternative is argon mixed with 2% to 5% nitrogen, hydrogen, or carbon dioxide.
Keep in mind, weld parameters or a specific HI that produces good results on one base material thickness may produce better or worse discoloration results on another material thickness. Stainless steel has a lower rate of heat transfer than carbon steel so the weld joint tends to stay at an elevated temperature longer than in a similar carbon steel application.
However, in larger pieces of base material or ones with the greater chance of heat sink (overall mass that can absorb heat from the weld zone) there should be a corresponding lower amount of discoloration. For example, if you weld with 35 kJ/in. of HI on 3/4-in. stainless steel, you might achieve a weld with a light straw color. A similar HI value on stainless steel that is 1/8 in. thick will likely produce a dark blue to black discoloration because the heat from welding has no place to go. The easiest way to reduce HI is to increase travel speed, assuming you have a voltage and amperage value that is producing the desired welder-friendly arc characteristics.
Determining the proper weld settings for GMAW, including pulsed GMAW, will ultimately come down to all the variables we discussed as well as the actual results. The amperage-versus-material-thickness guideline you mentioned, which is 1 amp per every 0.001 in., is typically applicable only for GTAW of thin-gauge materials. With GMAW you will have problems producing a stable arc for any material thinner than 14 to 16 ga. Conversely, there is no reason to weld materials that are ¼ in. thick or more at equivalent amperages unless it's in a robotic application where very high travel speeds are attainable.
In conclusion, HI is a measure that is used to deliver a weld where the total volume is free of any adverse metallurgical phase. Gas shielding is a condition that delivers the weld’s surface in a condition to meet the desired service conditions. Whenever a stainless steel is selected as a base material for a service condition, heat input and shielding of the molten pool are instrumental to delivering welds also capable of meeting said service conditions.
About the Authors
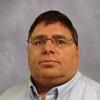
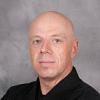
Rob Koltz
Application Engineer
411 S. Ebenezer Rd.
Florence, 29501
636-485-2253
About the Publication
Related Companies
subscribe now
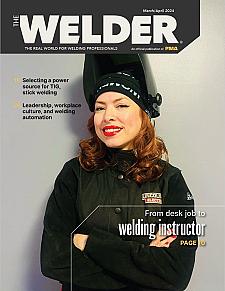
The Welder, formerly known as Practical Welding Today, is a showcase of the real people who make the products we use and work with every day. This magazine has served the welding community in North America well for more than 20 years.
start your free subscription- Stay connected from anywhere
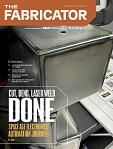
Easily access valuable industry resources now with full access to the digital edition of The Fabricator.
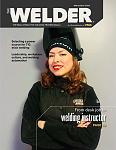
Easily access valuable industry resources now with full access to the digital edition of The Welder.
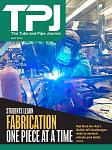
Easily access valuable industry resources now with full access to the digital edition of The Tube and Pipe Journal.
- Podcasting
- Podcast:
- The Fabricator Podcast
- Published:
- 04/16/2024
- Running Time:
- 63:29
In this episode of The Fabricator Podcast, Caleb Chamberlain, co-founder and CEO of OSH Cut, discusses his company’s...
- Trending Articles
Sheffield Forgemasters makes global leap in welding technology
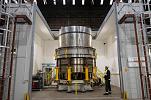
ESAB unveils Texas facility renovation
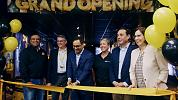
Engine-driven welding machines include integrated air compressors
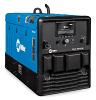
How welders can stay safe during grinding
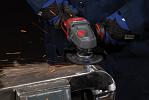
The impact of sine and square waves in aluminum AC welding, Part I
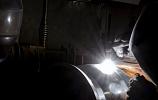
- Industry Events
16th Annual Safety Conference
- April 30 - May 1, 2024
- Elgin,
Pipe and Tube Conference
- May 21 - 22, 2024
- Omaha, NE
World-Class Roll Forming Workshop
- June 5 - 6, 2024
- Louisville, KY
Advanced Laser Application Workshop
- June 25 - 27, 2024
- Novi, MI