Independent welding consumables professional
- FMA
- The Fabricator
- FABTECH
- Canadian Metalworking
Categories
- Additive Manufacturing
- Aluminum Welding
- Arc Welding
- Assembly and Joining
- Automation and Robotics
- Bending and Forming
- Consumables
- Cutting and Weld Prep
- Electric Vehicles
- En Español
- Finishing
- Hydroforming
- Laser Cutting
- Laser Welding
- Machining
- Manufacturing Software
- Materials Handling
- Metals/Materials
- Oxyfuel Cutting
- Plasma Cutting
- Power Tools
- Punching and Other Holemaking
- Roll Forming
- Safety
- Sawing
- Shearing
- Shop Management
- Testing and Measuring
- Tube and Pipe Fabrication
- Tube and Pipe Production
- Waterjet Cutting
Industry Directory
Webcasts
Podcasts
FAB 40
Advertise
Subscribe
Account Login
Search
Consumables Corner: Choosing the correct carbon equivalency formula
- By Nino Mascalco, Rob Koltz, and Steve Sigler
- March 25, 2019
- Article
- Consumables
Q: We're a midsize fabrication shop that builds and welds machines and structural components from varying types of carbon steel. Some of the material is mild carbon steel, while some is high-strength, low-alloy (HSLA) or stronger grades of structural steel. If we're welding on thicker sections of material, we typically determine preheat temperatures based on just the carbon content.
Someone mentioned that we should be using a carbon equivalency formula to determine preheat temperatures. Can we use the one provided by AWS D1.1 or do we need to consider others?
A: This question comes up rather frequently, so let's take a look at some background information on carbon equivalency (CE) formulas.
The first CE formula developed by Dearden and O'Neill dates back several decades and was initially used to give a numerical value that related to the hardenability of carbon steel. In the mid-1960s the International Institute of Welding (IIW) derived a simplified formula for determining this property.
Various other formulas have been released over the years; some are for low-carbon steel, while others take into consideration grades that have small amounts of alloying elements. The reason is small amounts of alloying elements such as chromium (Cr), nickel (Ni), molybdenum (Mo), and manganese (Mn) increase the potential for martensite formation in the heat-affected zone (HAZ), which is the area of base material adjacent to a weld or high-temp cutting process.
From a welding standpoint, a couple of common formulas based on the parent material chemistry serve as a guideline for welding considerations such as hardenability, weldability, and HAZ hydrogen-induced cracking potential.
The equation that follows is the early version from IIW that is commonly found today in various publications, and the elements are calculated by weight percentages. This formula is suitable for carbon and carbon-manganese type steels:
CE(IIW) = %C + (%Mn)/6 + (%Cr+%Mo+%V)/5 + (%Ni+%Cu)/15
The American Welding Society (AWS D1.1 code) adopted this formula with an additional term to include silicon (Si); it is mostly used in applications involving various structural steel grades. The next formula is used mostly for steel with moderate levels of carbon to determine minimum preheat temperatures:
CE(AWS)=%C + (%Mn)/6 + (%Cr+%Mo+%V)/5 + (%Ni+%Cu)/15 + (%Si)/6
Neither of these formulas should be used with HSLA or low-alloy CrMo steels.
The next two formulas are better suited for low-carbon grades of steel and place an emphasis on carbon being the primary element that produces the greatest potential for microstructural changes. The first one is called the critical metal parameter equation or Pcm.
Pcm = %C + (%Si)/30 + (%Mn+%Cu+%Cr)/20 + (%Ni)/60 + (%Mo)/15 + (%V)/10 + 5%B
The last equation was derived by Düren and is similar to Pcm :
CEq = %C + (%Si)/25 + (%Mn+%Cu)/16 + (%Ni)/40 + (%Cr)/10 + (%Mo)/15 + (%V)/10
These two formulas are more applicable to a wide array of modern-day alloyed steels in which carbon content typically is less than 0.11 percent by weight.
Depending on which formula you use and the chemistry of the base material, the calculated result will typically fall between 0.30 and 0.70. The lower value corresponds with material that is readily weldable with a low tendency for increased hardness or potential for hydrogen-induced cracking. The middle to high range corresponds to poor weldability or high potential for increased hardness and cracking.
The best practice is to follow the code you are working to, keep customer requirements (if any) in mind, and consult the steel manufacturer for welding guidelines.
About the Authors
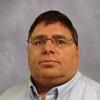
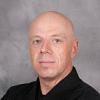
Rob Koltz
Application Engineer
411 S. Ebenezer Rd.
Florence, 29501
636-485-2253
Steve Sigler
Application Engineer
411 S. Ebenezer Rd.
Florence, South Carolina 29501
636-485-2253
About the Publication
Related Companies
subscribe now
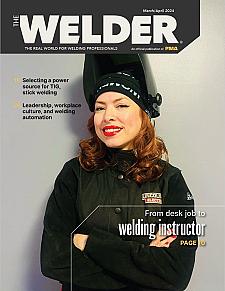
The Welder, formerly known as Practical Welding Today, is a showcase of the real people who make the products we use and work with every day. This magazine has served the welding community in North America well for more than 20 years.
start your free subscription- Stay connected from anywhere
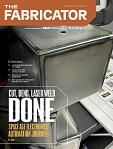
Easily access valuable industry resources now with full access to the digital edition of The Fabricator.
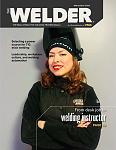
Easily access valuable industry resources now with full access to the digital edition of The Welder.
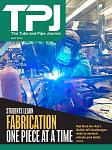
Easily access valuable industry resources now with full access to the digital edition of The Tube and Pipe Journal.
- Podcasting
- Podcast:
- The Fabricator Podcast
- Published:
- 04/16/2024
- Running Time:
- 63:29
In this episode of The Fabricator Podcast, Caleb Chamberlain, co-founder and CEO of OSH Cut, discusses his company’s...
- Trending Articles
Sheffield Forgemasters makes global leap in welding technology
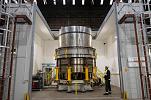
ESAB unveils Texas facility renovation
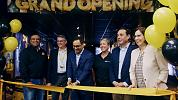
Engine-driven welding machines include integrated air compressors
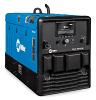
How welders can stay safe during grinding
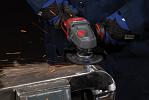
The impact of sine and square waves in aluminum AC welding, Part I
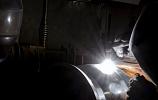
- Industry Events
16th Annual Safety Conference
- April 30 - May 1, 2024
- Elgin,
Pipe and Tube Conference
- May 21 - 22, 2024
- Omaha, NE
World-Class Roll Forming Workshop
- June 5 - 6, 2024
- Louisville, KY
Advanced Laser Application Workshop
- June 25 - 27, 2024
- Novi, MI