Independent welding consumables professional
- FMA
- The Fabricator
- FABTECH
- Canadian Metalworking
Categories
- Additive Manufacturing
- Aluminum Welding
- Arc Welding
- Assembly and Joining
- Automation and Robotics
- Bending and Forming
- Consumables
- Cutting and Weld Prep
- Electric Vehicles
- En Español
- Finishing
- Hydroforming
- Laser Cutting
- Laser Welding
- Machining
- Manufacturing Software
- Materials Handling
- Metals/Materials
- Oxyfuel Cutting
- Plasma Cutting
- Power Tools
- Punching and Other Holemaking
- Roll Forming
- Safety
- Sawing
- Shearing
- Shop Management
- Testing and Measuring
- Tube and Pipe Fabrication
- Tube and Pipe Production
- Waterjet Cutting
Industry Directory
Webcasts
Podcasts
FAB 40
Advertise
Subscribe
Account Login
Search
Consumables Corner: Aluminum welding for the non-aluminum welder
- By Nino Mascalco, Rob Koltz, and Steve Sigler
- July 26, 2018
- Article
- Consumables
Q: We're a small fabrication shop that is expanding and experiencing some growing pains. We normally work with carbon and some stainless steel for the majority of our work, but we're attempting to branch out and become more diversified to better serve our customers. We recently took on some 6061-T6 aluminum jobs and we're struggling with weld quality using 4043 MIG wire and 100 percent argon. Some of the issues are lack of fusion (LOF) at the root of the weld joint and weld bead profile. What should we do?
A: It’s great to hear that your business is growing! To provide some insight, we'll make some assumptions, but the end results will be minimally affected.
The type of aluminum you are using is referred to as structural-grade aluminum. As with most metals, there are several different types and grades that take advantage of alloying elements and specific processing techniques to optimize their performance for their intended applications. The T6 is a solution heat-treated, artificially aged grade of aluminum that is readily weldable and provides good strength and corrosion resistance.
The most common filler metal is the 4043 you are currently using, but you could also choose from several others depending on the desired results. If your weld bead profile problems are cosmetic, such as weld-toe angle transitions or general bead appearance, you could substitute 4047, which has a greater amount of silicon that will produce a more fluid weld puddle.
In many cases, straight argon as a shielding gas is commonly used, and many shops will have this on hand if they perform any GTAW. The problem with pure argon is it produces a narrow arc cone, limiting the penetration profile width, which could explain your problems with fusion. A better option for welding aluminum is a helium/argon blend between 25 and 75 percent helium with the balance of argon. Helium produces a much wider arc cone throughout the length of the welding arc and more heat. This is beneficial for achieving adequate penetration at the root, better bead appearance, and higher travel speeds. It is best-suited for thick sections of base material. Keep in mind that more helium means you’ll need to set the flow rate higher to provide adequate shielding coverage. This is necessary because helium is lighter than atmospheric air and will float away before it is effective.
Many variables can affect the weld performance and results in aluminum, but the most important variables are the ones that occur before welding. Properly preparing the joint is essential to producing a quality welded joint. Be sure to remove any dross or contamination from thermally cut edges from the base-material joints. Clean the joint before fit-up and welding is the most important.
Aluminum has a protective oxide layer that you need to remove before you weld. Although this oxide forms readily in the atmosphere, removing it in turn eliminates the additional contamination and moisture that goes with it. Use a solvent to remove oil, grease, or moisture before you file, grind, or wire brush the surface and edges of the joint you are about to weld. Be sure to use a stainless steel wire brush dedicated to cleaning aluminum only. This will keep it clean and prevent cross-contamination. Do the same with grinding or sanding wheels.
For aluminum GMAW, set parameters to weld hot and fast in direct-current electrode positive (DCEP). Sometimes LOF occurs at the root because the travel speed is too slow and arc energy is too low. Since you have little control over the rate of filler metal being added to the joint (unlike with GTAW where you have complete control), the welding arc will be focused on top of the molten weld puddle instead of in front of it. This produces an insulating effect at the root of the joint and leads to LOF. Using higher weld parameters in a spray-transfer mode with a pushing or forehand technique while keeping the arc focused at the leading edge of the weld puddle will produce the best penetration results. A simple T-joint break test will verify that your settings and technique are correct and identify if you’ve achieved sufficient penetration.
Changing your shielding gas and following the guidelines outlined here should have you producing quality welds in no time.
About the Authors
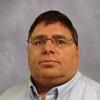
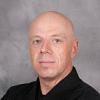
Rob Koltz
Application Engineer
411 S. Ebenezer Rd.
Florence, 29501
636-485-2253
Steve Sigler
Application Engineer
411 S. Ebenezer Rd.
Florence, South Carolina 29501
636-485-2253
About the Publication
Related Companies
subscribe now
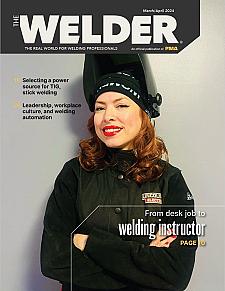
The Welder, formerly known as Practical Welding Today, is a showcase of the real people who make the products we use and work with every day. This magazine has served the welding community in North America well for more than 20 years.
start your free subscription- Stay connected from anywhere
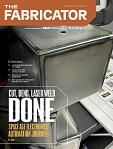
Easily access valuable industry resources now with full access to the digital edition of The Fabricator.
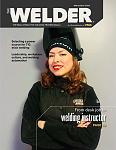
Easily access valuable industry resources now with full access to the digital edition of The Welder.
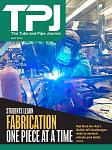
Easily access valuable industry resources now with full access to the digital edition of The Tube and Pipe Journal.
- Podcasting
- Podcast:
- The Fabricator Podcast
- Published:
- 04/16/2024
- Running Time:
- 63:29
In this episode of The Fabricator Podcast, Caleb Chamberlain, co-founder and CEO of OSH Cut, discusses his company’s...
- Trending Articles
Sheffield Forgemasters makes global leap in welding technology
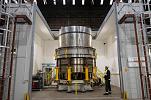
ESAB unveils Texas facility renovation
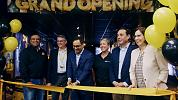
Engine-driven welding machines include integrated air compressors
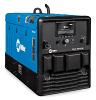
How welders can stay safe during grinding
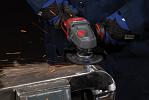
The impact of sine and square waves in aluminum AC welding, Part I
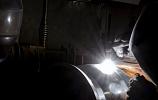
- Industry Events
16th Annual Safety Conference
- April 30 - May 1, 2024
- Elgin,
Pipe and Tube Conference
- May 21 - 22, 2024
- Omaha, NE
World-Class Roll Forming Workshop
- June 5 - 6, 2024
- Louisville, KY
Advanced Laser Application Workshop
- June 25 - 27, 2024
- Novi, MI