Independent welding consumables professional
- FMA
- The Fabricator
- FABTECH
- Canadian Metalworking
Categories
- Additive Manufacturing
- Aluminum Welding
- Arc Welding
- Assembly and Joining
- Automation and Robotics
- Bending and Forming
- Consumables
- Cutting and Weld Prep
- Electric Vehicles
- En Español
- Finishing
- Hydroforming
- Laser Cutting
- Laser Welding
- Machining
- Manufacturing Software
- Materials Handling
- Metals/Materials
- Oxyfuel Cutting
- Plasma Cutting
- Power Tools
- Punching and Other Holemaking
- Roll Forming
- Safety
- Sawing
- Shearing
- Shop Management
- Testing and Measuring
- Tube and Pipe Fabrication
- Tube and Pipe Production
- Waterjet Cutting
Industry Directory
Webcasts
Podcasts
FAB 40
Advertise
Subscribe
Account Login
Search
Consumables Corner: Addressing penetration at the root of aluminum tack welds
- By Nino Mascalco and Rob Koltz
- September 26, 2019
- Article
- Consumables
Q: We tack weld many of our aluminum parts manually with gas metal arc welding (GMAW) in a fixture before final robotic welding takes place. We are having difficulty getting good fusion from the robot station in the areas where it welds over the tack weld. The aluminum material is 6061-T6, the manual tack weld wire is 5356, and the robot welds with 4043, all done with argon shielding gas. Any ideas how to resolve this?
A: There are several things to consider, but ultimately it could be one small change or several things combined to resolve your issues. As a refresher, cleaning the weld joint, selecting the right GMAW parameter settings, and using the proper weld technique are all necessary to achieve good results.
Two things we noticed right away that might be partially to blame for the lack of fusion (LOF) are the pure argon shielding gas and the two different filler metals. Not that these are uncommon combinations, but they may cause some problems.
Pure argon shielding gas is common for welding specialty alloys including aluminum because it is a nonreactive gas. With regards to aluminum, it provides good cleaning action, stable arc characteristics, good arc initiation, and moderate penetration at an affordable price.
However, argon does produce a narrow arc cone that coincides with a narrower weld bead and fusion zone. To determine if this is part of the problem, put the weld through a simple T-joint fillet weld break test. Since your welders are tacking the joints manually, make sure they are using proper gun angles and travel speeds along with good weld settings. Remember, you should be welding in spray transfer mode to maximize penetration.
If you find that the fusion issues are not related to machine settings or weld technique, you can try using an argon-helium gas blend, with helium comprising 25 to 50 percent of the blend. Helium is a hotter gas due to its greater ionization potential and thermal conductivity, to which it produces a wider bead and resulting fusion zone. This alone may resolve your problem.
For 6061-T6 aluminum, both filler metal types are good choices as long as they meet all the requirements of the weldment. The 4043 filler metal is preferred since it's an aluminum-silicon alloy, which minimizes solidification cracking and has good welder appeal. The silicon promotes improved puddle control, flows better or has improved wetting characteristics, generates less spatter, and provides a smooth bead appearance. It is a soft filler metal, so you might run into feeding issues.
The 5356 filler metal is an aluminum-magnesium alloy that provides higher-strength welds than the 4043. 5356 has lower electrical conductivity, thereby allowing for a lower amperage at similar or higher wire-feed speeds, which deposits weld metal faster. This is beneficial for welding thin materials but may contribute to LOF at the root since the heat input is low. Employing improper welder technique or using incorrect weld settings with 5356 is more than likely to cause fusion issues at the root of the weld compared to 4043.
At this point you need to examine why you’re using two different filler metals in the same weld joints.
For manual GMAW, 5356 has greater columnar stiffness—resistance to bending—so it feeds much better and reduces bird nests at the drive rolls. Most weld shops use a push/pull welding gun, but feeding problems still can occur in guns that are long in length, so we recommend using 5356 instead of 4043.
However, since the robot has a much smaller welding envelope, the welding gun lead tends to be much shorter, thereby reducing feeding issues. Since 4043 overall has better weldability, it is the preferred filler metal.
To sum it up, if you want to resolve LOF, ensure good manual tack welding is happening and that the welders can pass a fillet weld break test. Try adding helium shielding gas to the process and see if that promotes better fusion. Finally, try using 4043 filler metal for the tacking operation and track the success or failure compared to 5356.
About the Authors
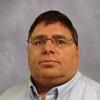
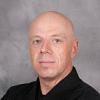
Rob Koltz
Application Engineer
411 S. Ebenezer Rd.
Florence, 29501
636-485-2253
About the Publication
Related Companies
subscribe now
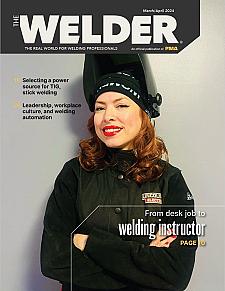
The Welder, formerly known as Practical Welding Today, is a showcase of the real people who make the products we use and work with every day. This magazine has served the welding community in North America well for more than 20 years.
start your free subscription- Stay connected from anywhere
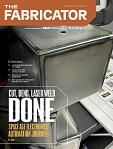
Easily access valuable industry resources now with full access to the digital edition of The Fabricator.
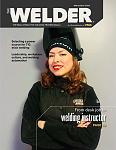
Easily access valuable industry resources now with full access to the digital edition of The Welder.
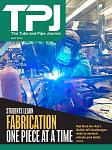
Easily access valuable industry resources now with full access to the digital edition of The Tube and Pipe Journal.
- Podcasting
- Podcast:
- The Fabricator Podcast
- Published:
- 04/16/2024
- Running Time:
- 63:29
In this episode of The Fabricator Podcast, Caleb Chamberlain, co-founder and CEO of OSH Cut, discusses his company’s...
- Trending Articles
Sheffield Forgemasters makes global leap in welding technology
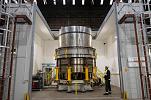
ESAB unveils Texas facility renovation
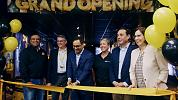
Engine-driven welding machines include integrated air compressors
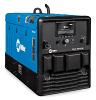
How welders can stay safe during grinding
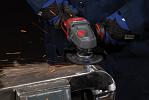
The impact of sine and square waves in aluminum AC welding, Part I
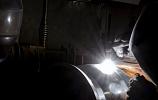
- Industry Events
16th Annual Safety Conference
- April 30 - May 1, 2024
- Elgin,
Pipe and Tube Conference
- May 21 - 22, 2024
- Omaha, NE
World-Class Roll Forming Workshop
- June 5 - 6, 2024
- Louisville, KY
Advanced Laser Application Workshop
- June 25 - 27, 2024
- Novi, MI