Independent welding consumables professional
- FMA
- The Fabricator
- FABTECH
- Canadian Metalworking
Categories
- Additive Manufacturing
- Aluminum Welding
- Arc Welding
- Assembly and Joining
- Automation and Robotics
- Bending and Forming
- Consumables
- Cutting and Weld Prep
- Electric Vehicles
- En Español
- Finishing
- Hydroforming
- Laser Cutting
- Laser Welding
- Machining
- Manufacturing Software
- Materials Handling
- Metals/Materials
- Oxyfuel Cutting
- Plasma Cutting
- Power Tools
- Punching and Other Holemaking
- Roll Forming
- Safety
- Sawing
- Shearing
- Shop Management
- Testing and Measuring
- Tube and Pipe Fabrication
- Tube and Pipe Production
- Waterjet Cutting
Industry Directory
Webcasts
Podcasts
FAB 40
Advertise
Subscribe
Account Login
Search
Consumables Corner: A guide to understanding heat treating and how it affects the weld
- By Nino Mascalco, Rob Koltz, and Steve Sigler
- September 26, 2018
- Article
- Consumables
Q: I work for a small fab shop and I am beginning the process of earning my CWI. I don’t have any formal technical training, but I am interested in understanding the behaviors of filler metals when subjected to heat treatments. I’m not clear on why there are different yield, tensile strength, and Charpy properties of filler metals depending upon if they were heat treated or in the as-welded condition. Can you shed some light on this?
A: Excellent! Earning your Certified Welding Inspector (CWI) will be great career move and will benefit the company you work for.
Stress relieving, or more commonly referred to as postweld heat treat (PWHT), is a type of heat treating performed on the weld to reduce the residual stress caused by welding. However, PWHT is not the same as tempering or annealing, which change the metallurgical structure of the metals. This is a very complex topic, so we'll try to keep it straightforward and simple.
The primary reason for stress relieving welded components or large structures is to relieve residual thermal weld stresses. During the fabrication and welding of complex structures or simple components, there is a large amount of residual weld stress.
Residual weld stress is caused by the solidification and contraction of the molten weld pool that is constrained by the adjacent material. The greater the degree of constraint, the greater the residual stress.
During welding, the extreme heat in the welding arc melts the filler metal and causes the weld pool to expand. Initially, this creates compressive stress in the neighboring material since it is at a lower temperature and cannot expand as much or at the same rate. When it is deposited in the relatively cool weld joint, however, the weld puddle rapidly cools, solidifies, and contracts. The contraction is restrained by the cooler base material and fixturing/bracing of those pieces welded together. This leads to residual stresses in the weld metal and nearby base material.
The amount of residual stresses within the weld metal are what cause the yield strength (YS) and ultimate tensile strength (UTS) to be greater in the as-welded (AW) condition versus the stress-relieved condition. The reason is the nonuniform localized heating or cooling of the components. With higher temperatures of the weld metal or base metal during welding, the YS will be lower, which will allow plastic deformation to occur. Plastic deformation means the material has been distorted (bent or stretched) from its original shape by exceeding the YS of the material itself.
Basically the same idea as heating steel to “hot form” or “hot work,” it will take less external force. Hot forming or hot working is the process of heating metal to an elevated temperature, which then lowers the YS. This allows it to be bent or formed with a lower amount of external force, such as a hydraulic press or how a blacksmith heats steel and then uses a hammer to shape it.
When the weld and base metals cool down, the YS increases and resists plastic deformation, resulting in residual stress. The residual stresses can be either tensile or compressive in nature. Depending on part geometry and loading conditions, this weld shrinkage can either increase or decrease the amount of loading the joint can withstand before failing.
During destructive testing of filler metals, the weld metal is already under an internal load from the residual stress. Typically, in the AW condition, the welded material will produce higher YS and UTS values. Conversely, Charpy V-notch values will be slightly lower. Stress relieving weldments will produce slightly lower YS and UTS values, and Charpy V-notch values will improve.
In some cases, the residual stress exceeds the yield strength of the base material and leads to distortion and possibly premature part failure. It also can create hot cracking or other cracking issues. If the parts have to be machined after welding, it often is necessary to stress relieve first, which stabilizes the material’s shape by reducing the resulting weld stress. Otherwise, without the PWHT, the machining operation may remove material that is under internal stress, causing the part to change shape and distort beyond the desired tolerances.
During stress relieving applications, the entire component is heated uniformly (minimal temperature gradients throughout) to a value below the critical temperature and held for a minimum amount of time, based on weld thickness, to allow the entire part to relax or the stresses to subside. It is then slowly cooled uniformly to prevent any reintroduction of stresses.
About the Authors
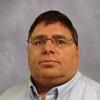
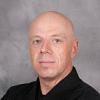
Rob Koltz
Application Engineer
411 S. Ebenezer Rd.
Florence, 29501
636-485-2253
Steve Sigler
Application Engineer
411 S. Ebenezer Rd.
Florence, South Carolina 29501
636-485-2253
About the Publication
Related Companies
subscribe now
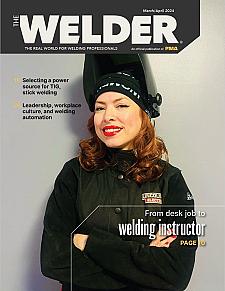
The Welder, formerly known as Practical Welding Today, is a showcase of the real people who make the products we use and work with every day. This magazine has served the welding community in North America well for more than 20 years.
start your free subscription- Stay connected from anywhere
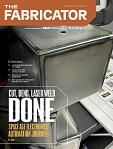
Easily access valuable industry resources now with full access to the digital edition of The Fabricator.
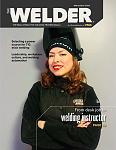
Easily access valuable industry resources now with full access to the digital edition of The Welder.
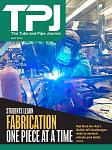
Easily access valuable industry resources now with full access to the digital edition of The Tube and Pipe Journal.
- Podcasting
- Podcast:
- The Fabricator Podcast
- Published:
- 04/16/2024
- Running Time:
- 63:29
In this episode of The Fabricator Podcast, Caleb Chamberlain, co-founder and CEO of OSH Cut, discusses his company’s...
- Trending Articles
Sheffield Forgemasters makes global leap in welding technology
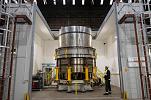
ESAB unveils Texas facility renovation
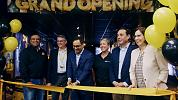
Engine-driven welding machines include integrated air compressors
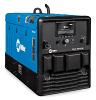
How welders can stay safe during grinding
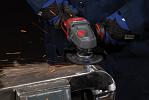
The impact of sine and square waves in aluminum AC welding, Part I
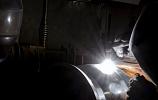
- Industry Events
16th Annual Safety Conference
- April 30 - May 1, 2024
- Elgin,
Pipe and Tube Conference
- May 21 - 22, 2024
- Omaha, NE
World-Class Roll Forming Workshop
- June 5 - 6, 2024
- Louisville, KY
Advanced Laser Application Workshop
- June 25 - 27, 2024
- Novi, MI