- FMA
- The Fabricator
- FABTECH
- Canadian Metalworking
Categories
- Additive Manufacturing
- Aluminum Welding
- Arc Welding
- Assembly and Joining
- Automation and Robotics
- Bending and Forming
- Consumables
- Cutting and Weld Prep
- Electric Vehicles
- En Español
- Finishing
- Hydroforming
- Laser Cutting
- Laser Welding
- Machining
- Manufacturing Software
- Materials Handling
- Metals/Materials
- Oxyfuel Cutting
- Plasma Cutting
- Power Tools
- Punching and Other Holemaking
- Roll Forming
- Safety
- Sawing
- Shearing
- Shop Management
- Testing and Measuring
- Tube and Pipe Fabrication
- Tube and Pipe Production
- Waterjet Cutting
Industry Directory
Webcasts
Podcasts
FAB 40
Advertise
Subscribe
Account Login
Search
Creating prestige around skilled trades with YouTube competition series
Ray Dick of Project MFG discusses the National Skilled Trade Challenge, YouTube series, and the state of U.S. manufacturing
- By Amanda Carlson
- June 16, 2021
- Article
- Arc Welding
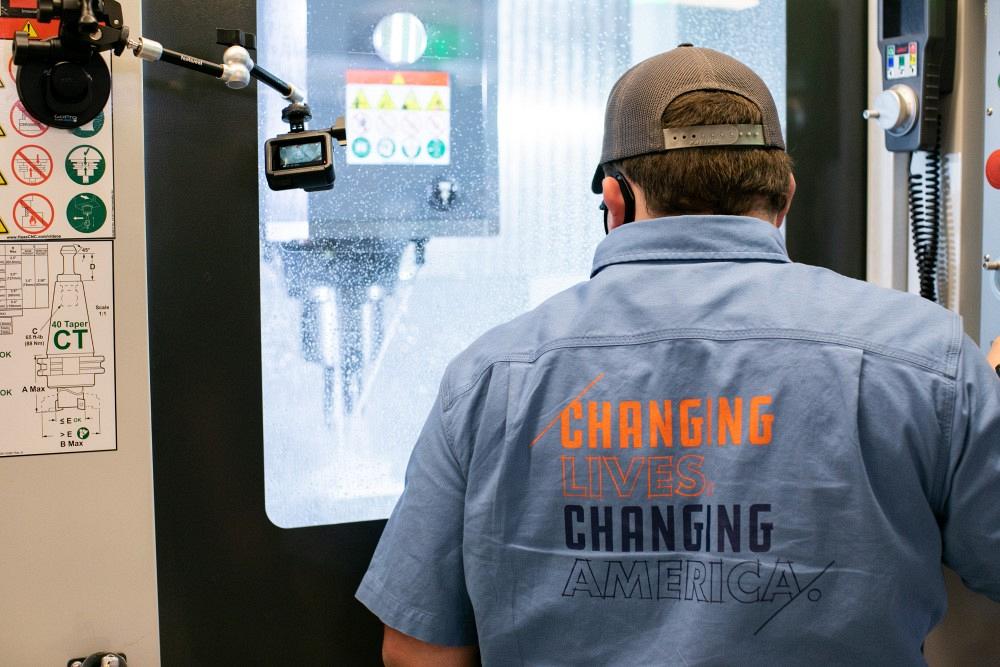
Student Trent Oswald watches through the window of the Haas CNC machine during Project MFG’s National Skilled Trades Challenge. Images: Project MFG
What is Project MFG, and what’s the mission behind it?
Project MFG is an initiative funded by the Department of Defense. It was stood up under the office of the Secretary of Defense's Industrial Base Analysis and Sustainment Program. The director there is Adele Ratcliff, and we've worked together for many years and had a lot of conversations about the state of the trade workforce talent pipeline. Between historical offshoring and the loss of jobs and the aging out of the workforce, the state of trade skills is a critical national security issue. If we can’t get things made where we need them and when we need them, it’s an economic issue for the U.S.; it's a national security issue too.Our mission is to elevate the skill level so that the rising tide lifts all ships. We want to provide pathways for training and education so that young people or trainees who enter the workforce are better prepared. And then we want to tell the story as loud and as proud as we can that the skilled trades today are a very viable career path and a long-term profession.How did the idea of the National Skilled Trade Challenge evolve from concept to reality?
Adele had this idea of a “Top Chef”-style competition that would promote, elevate, and accelerate the workforce pipeline. So, through those conversations, we started to develop this hands-on, integrated, advanced manufacturing competition where teams from community colleges, trade schools, and other training facilities would have the opportunity to really demonstrate a full range of skills by making a product. We were originally supposed to have our 2020 national finals in Chicago at IMTS last fall, but COVID-19 took over and we had to step back and retool things. We did single-site competitions in a round-robin format. That allowed us to finish our state competitions, move into our regional round of competition, and from there narrow it down to four teams that qualified for the national finals. Those four were Danville Community College, Danville, Va.; Calhoun Community College, Decatur, Ala.; Tennessee College of Applied Technology, Clarksville, Tenn.; and Southwestern Illinois College, Granite City, Ill.Between the state, regional, and now the national rounds, we had a total purse of about $300,000. That is a combination of grants to the schools, scholarships for the students, upgrades to the facilities, and trade kit and swag.We had over $1 million in grants, scholarships, and in-kind donations by our wonderful partners. Mastercam, Haas Automation, and HFO Phillips have been incredible partners. Lincoln Electric on the welding side has been a great help as well. They’ve provided welding machines for our competitions, and their training crew and subject matter experts have helped us design elements of the competition.Can you describe the competition?
We tasked the teams with building their own trophy, which had three components – a stand, midsection, and the feature element on top. The feature element was a surprise-- they didn't know what it was until they showed up at the competition. It was up to each team to design and source materials, and in the first round it was 6061 aluminum. Each team had to show up to the competition with their design package and raw materials and then execute the fabrication of that stand during the two days of competition. In the second round, which was our regional round, we elevated the complexity of the 5-axis machining process and the known commodity in the center section, and for the stand itself. We also added design features to make the welding tougher. This included directional welds and being more specific in what the weld process definition was, and then we judged them to the WPS. And then we also added a functional feature of the stand. It had to incorporate a 2- by 2- by 6-in. welded aluminum pressure vessel made out of 11-ga. 6061 aluminum.For the national competition, we took things a step further. Again, the CNC machining got more complex. They actually had the machine around a globe and then engraved the continents on the globe, which had a bearing fit and had to spin. They had a twisted neck in the center section that held the globe. And then for the stand, we went back and were prescriptive, saying they had to make a part to print, but the part was an octagon-shaped pressure vessel made out of 11-ga. 304 stainless steel. They had to weld the eight pieces of the octagon together and then weld a base, the top, a pressure vessel, and a Schrader valve on it.It went from a fairly open-ended creative exercise where they really got to play to their strengths to what we believe turned out to be a much more prescriptive product for which they had to meet some pretty tight, industry-oriented tolerances on the fabrication and welding.What impressed or surprised you the most about the process of narrowing down to a final four?
I would be very remiss if I didn’t say I was impressed by the pure doggedness of these teams and their ability to work with us collaboratively during the COVID-19 pandemic. What continued to amaze and impress me was the competitors’ willingness to tackle hard projects. The skill these young people demonstrated during the technical portions of the competition, including machining, welding, fabrication, and metrology, was just way beyond any reasonable expectation of what a person emerging out of school should be able to do.Our fear initially was making the requirements too difficult and scaring young people away, but that didn’t end up happening at all. Every time we threw a really dang hard problem at teams, they rose to the occasion and took it as a challenge. I would even argue that part of what we learned throughout the process is that schools can push students way harder than they ever thought they could.Why is a competition like this important?
COVID-19 revealed our inability to produce domestically on demand or pivot our manufacturing base quickly and efficiently to produce what’s needed. The pandemic reflected the general health of the industrial base as a whole. If we don’t start yelling louder about the importance of attracting the next generation of manufacturers to the trades, we’ll never solve this problem. There are a lot of great competitions out there. SkillsUSA has a huge footprint, and I think all 50 states do a lot of great work at the younger ages, introducing people to and challenging them to get into the trades. But somewhere along the line, we need to elevate it to where young people are being recruited into manufacturing jobs just like the college football teams recruit players.That’s a future vision of ours as we continue to offer this national championship-type competition. We want industry leaders showing up, seeing in person what these young people can do, and talking to them about immediate job opportunities. If we can create that kind of prestige around the trades, then and only then can we take a breath and truly say that the future looks bright for manufacturing in the U.S.How can people tune in to watch the final four compete?
The first episode aired April 20 on the Project MFG YouTube channel. All of the details about future shows are available on our website, projectmfg.com.How can schools sign up to compete in the 2021 competition?
Anyone interested in participating can go to our website and access an application form under the Get Involved tab. We are always looking for schools and students that want to challenge themselves to the highest level.About the Author
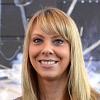
Amanda Carlson
2135 Point Blvd
Elgin, IL 60123
815-227-8260
Amanda Carlson was named as the editor for The WELDER in January 2017. She is responsible for coordinating and writing or editing all of the magazine’s editorial content. Before joining The WELDER, Amanda was a news editor for two years, coordinating and editing all product and industry news items for several publications and thefabricator.com.
About the Publication
subscribe now
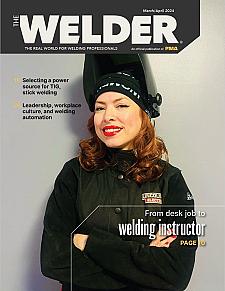
The Welder, formerly known as Practical Welding Today, is a showcase of the real people who make the products we use and work with every day. This magazine has served the welding community in North America well for more than 20 years.
start your free subscription- Stay connected from anywhere
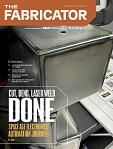
Easily access valuable industry resources now with full access to the digital edition of The Fabricator.
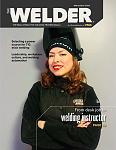
Easily access valuable industry resources now with full access to the digital edition of The Welder.
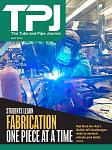
Easily access valuable industry resources now with full access to the digital edition of The Tube and Pipe Journal.
- Podcasting
- Podcast:
- The Fabricator Podcast
- Published:
- 04/30/2024
- Running Time:
- 53:00
Seth Feldman of Iowa-based Wertzbaugher Services joins The Fabricator Podcast to offer his take as a Gen Zer...
- Industry Events
Pipe and Tube Conference
- May 21 - 22, 2024
- Omaha, NE
World-Class Roll Forming Workshop
- June 5 - 6, 2024
- Louisville, KY
Advanced Laser Application Workshop
- June 25 - 27, 2024
- Novi, MI
Precision Press Brake Certificate Course
- July 31 - August 1, 2024
- Elgin,