President
- FMA
- The Fabricator
- FABTECH
- Canadian Metalworking
Categories
- Additive Manufacturing
- Aluminum Welding
- Arc Welding
- Assembly and Joining
- Automation and Robotics
- Bending and Forming
- Consumables
- Cutting and Weld Prep
- Electric Vehicles
- En Español
- Finishing
- Hydroforming
- Laser Cutting
- Laser Welding
- Machining
- Manufacturing Software
- Materials Handling
- Metals/Materials
- Oxyfuel Cutting
- Plasma Cutting
- Power Tools
- Punching and Other Holemaking
- Roll Forming
- Safety
- Sawing
- Shearing
- Shop Management
- Testing and Measuring
- Tube and Pipe Fabrication
- Tube and Pipe Production
- Waterjet Cutting
Industry Directory
Webcasts
Podcasts
FAB 40
Advertise
Subscribe
Account Login
Search
Aluminum Workshop: Two flowmeters don’t make a right
- By Frank Armao
- January 26, 2018
- Article
- Aluminum Welding
I’m sure that we have all seen people engaging in poor practices in many fields from time to time. Today I want to discuss one poor practice that I commonly see and to urge all of you not to do it.
When you are setting up your welding equipment, never lead the shielding gas through more than one flowmeter. Leading the shielding gas through two (or more, which is even worse) flowmeters on its path from the inert gas cylinder or the central source from where large installations supply shielding gas will almost always cause problems.
Typically, a shielding gas source, such as a high-pressure gas cylinder, needs a pressure regulator to reduce the gas pressure in the bottle (usually 3,000 PSI for a full bottle) to a level that can be used for welding (between 20 and 50 PSI). A pressure regulator is screwed onto the gas bottle. It is common to combine the pressure regulator with a flowmeter. You have all seen them. They are the clear plastic tube a few inches long that have an adjustment on them to set the shielding gas flow rate.
The problem arises when you attach the gas hose from the flowmeter to your wire feeder because many feeders already contain a flowmeter. This is intended to be a convenience, allowing you to set the shielding gas flow rate at the feeder without going all the way back to the gas bottle. Because of this, you’ll always set both flowmeters for what you think is a reasonable flow rate—for example, 40 SCFH.
Now you have a problem.
Although both flowmeters read 40 SCFH, your actual gas flow rate is almost always much less because you are using two flowmeters in series.
What should you do? The best thing is to bypass or eliminate one of the flowmeters. Instead of using a regulator/flowmeter on the bottle, use just a regulator and set the flow rate using the flowmeter on your feeder. Or try to bypass the flowmeter on the feeder and use the regulator/flowmeter at the gas bottle to set the flow.
If you can’t do this and you must use the two flowmeters in series, set the flowmeter at the bottle wide open to the highest flow rate possible and use the flowmeter at the feeder to set the actual flow rate. This isn’t the best solution, but it is better than doing nothing.
Last, I recommend that you have one of those simple and inexpensive gauges that you can place over the end of the gas nozzle on your torch that measures gas flow. Most welding distributors have them readily available. They are pretty accurate and can tell you whether you have the gas flow you think you have, whether you have the problem above, whether you have a leak in your gas hose, or whatever else.
About the Author
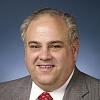
Frank Armao
Aluminum Consulting Inc.
440-479-0239
About the Publication
Related Companies
subscribe now
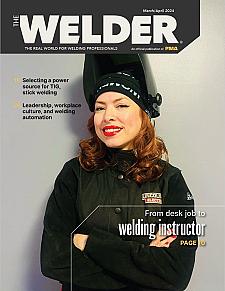
The Welder, formerly known as Practical Welding Today, is a showcase of the real people who make the products we use and work with every day. This magazine has served the welding community in North America well for more than 20 years.
start your free subscription- Stay connected from anywhere
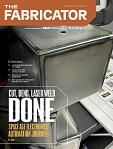
Easily access valuable industry resources now with full access to the digital edition of The Fabricator.
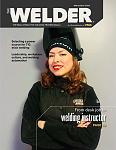
Easily access valuable industry resources now with full access to the digital edition of The Welder.
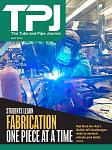
Easily access valuable industry resources now with full access to the digital edition of The Tube and Pipe Journal.
- Podcasting
- Podcast:
- The Fabricator Podcast
- Published:
- 04/16/2024
- Running Time:
- 63:29
In this episode of The Fabricator Podcast, Caleb Chamberlain, co-founder and CEO of OSH Cut, discusses his company’s...
- Trending Articles
Sheffield Forgemasters makes global leap in welding technology
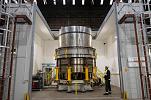
ESAB unveils Texas facility renovation
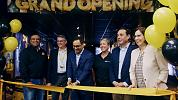
Engine-driven welding machines include integrated air compressors
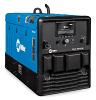
How welders can stay safe during grinding
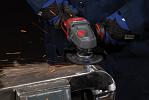
The impact of sine and square waves in aluminum AC welding, Part I
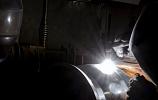
- Industry Events
16th Annual Safety Conference
- April 30 - May 1, 2024
- Elgin,
Pipe and Tube Conference
- May 21 - 22, 2024
- Omaha, NE
World-Class Roll Forming Workshop
- June 5 - 6, 2024
- Louisville, KY
Advanced Laser Application Workshop
- June 25 - 27, 2024
- Novi, MI