President
- FMA
- The Fabricator
- FABTECH
- Canadian Metalworking
Categories
- Additive Manufacturing
- Aluminum Welding
- Arc Welding
- Assembly and Joining
- Automation and Robotics
- Bending and Forming
- Consumables
- Cutting and Weld Prep
- Electric Vehicles
- En Español
- Finishing
- Hydroforming
- Laser Cutting
- Laser Welding
- Machining
- Manufacturing Software
- Materials Handling
- Metals/Materials
- Oxyfuel Cutting
- Plasma Cutting
- Power Tools
- Punching and Other Holemaking
- Roll Forming
- Safety
- Sawing
- Shearing
- Shop Management
- Testing and Measuring
- Tube and Pipe Fabrication
- Tube and Pipe Production
- Waterjet Cutting
Industry Directory
Webcasts
Podcasts
FAB 40
Advertise
Subscribe
Account Login
Search
Aluminum Workshop: Got porosity? Do your homework before assessing blame
- By Frank Armao
- September 25, 2018
- Article
- Aluminum Welding
Q: I’m having a lot of problems with porosity in aluminum welds. My friend told me that it is probably caused by contaminated filler wire. What do you think?
A: Porosity in aluminum welds can have many causes. The two things that usually get blamed right away are contaminated wire or contaminated shielding gas. While either or both can cause porosity, they are rarely the problem. We will talk about shielding gases in an upcoming column, but right now we’re going to discuss contaminated wire (or gas tungsten arc welding [GTAW] rod).
The fact is that all aluminum wire must be lubricated during the drawing process, from the starting rod (typically about 3/8-inch diameter) down to the finished size. If it’s not lubricated, it will snap in the drawing line. All of the lubricants are hydrocarbon based and would cause porosity if left on the wire. So, if you are seeing porosity, it is probably a prudent precaution to change wire spools (or GTAW rod lots), maybe even to a different supplier, and see what happens.
If that was the end of wire manufacturing, the story would be over. But it isn’t. All wire manufacturers perform a cleaning operation near the end of the manufacturing process to remove the drawing lubricant. It is usually an inline solvent bath, which is almost always effective at removing the lube. Could something go wrong? Yes, but the major manufacturers are very good about making sure lube is removed. Such problems do happen, but they are very rare. While you shouldn’t dismiss the wire as being a cause of porosity, you also shouldn’t automatically assume it’s the problem.
One of my pet peeves is when someone takes a gas metal arc welding (GMAW) wire or GTAW rod and rubs it vigorously with a clean white rag and says something like “Look at all the grease on this wire. It’s terrible.” Guess what? You will always get some black residue on the rag because it is the naturally occurring aluminum oxide on the surface of the wire. All aluminum has such a coating on its surface. Don’t be misled.
Here’s an experiment to prove this to yourself. The next time you are at the top of a staircase that has an aluminum handrail, rub your hand fairly hard on the handrail on the way down. At the bottom, look at your hand. It has the same black residue on it.
However, there is a way to make the white rag test much more informative. Place the white rag containing the residue under an ultraviolet lamp (black light). While aluminum oxide does not fluoresce under ultraviolet light, almost all oils and greases do.
The last point I should mention is that some GMAW wire manufacturers today intentionally put a feeding lubricant on their wire after cleaning. However, these lubricants usually do not contain hydrocarbons and should not cause porosity.
So, the next time you have weld porosity problems, do your homework and don’t just automatically blame the wire.
About the Author
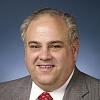
Frank Armao
Aluminum Consulting Inc.
440-479-0239
About the Publication
subscribe now
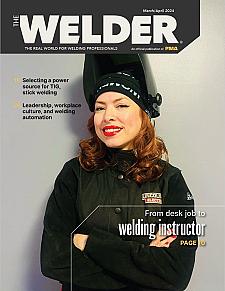
The Welder, formerly known as Practical Welding Today, is a showcase of the real people who make the products we use and work with every day. This magazine has served the welding community in North America well for more than 20 years.
start your free subscription- Stay connected from anywhere
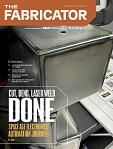
Easily access valuable industry resources now with full access to the digital edition of The Fabricator.
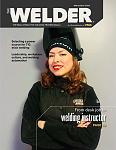
Easily access valuable industry resources now with full access to the digital edition of The Welder.
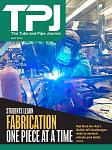
Easily access valuable industry resources now with full access to the digital edition of The Tube and Pipe Journal.
- Podcasting
- Podcast:
- The Fabricator Podcast
- Published:
- 04/16/2024
- Running Time:
- 63:29
In this episode of The Fabricator Podcast, Caleb Chamberlain, co-founder and CEO of OSH Cut, discusses his company’s...
- Trending Articles
Sheffield Forgemasters makes global leap in welding technology
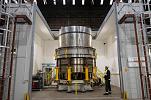
ESAB unveils Texas facility renovation
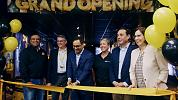
Engine-driven welding machines include integrated air compressors
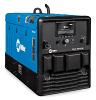
How welders can stay safe during grinding
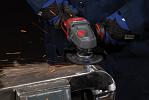
The impact of sine and square waves in aluminum AC welding, Part I
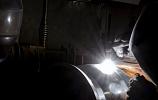
- Industry Events
16th Annual Safety Conference
- April 30 - May 1, 2024
- Elgin,
Pipe and Tube Conference
- May 21 - 22, 2024
- Omaha, NE
World-Class Roll Forming Workshop
- June 5 - 6, 2024
- Louisville, KY
Advanced Laser Application Workshop
- June 25 - 27, 2024
- Novi, MI