President
- FMA
- The Fabricator
- FABTECH
- Canadian Metalworking
Categories
- Additive Manufacturing
- Aluminum Welding
- Arc Welding
- Assembly and Joining
- Automation and Robotics
- Bending and Forming
- Consumables
- Cutting and Weld Prep
- Electric Vehicles
- En Español
- Finishing
- Hydroforming
- Laser Cutting
- Laser Welding
- Machining
- Manufacturing Software
- Materials Handling
- Metals/Materials
- Oxyfuel Cutting
- Plasma Cutting
- Power Tools
- Punching and Other Holemaking
- Roll Forming
- Safety
- Sawing
- Shearing
- Shop Management
- Testing and Measuring
- Tube and Pipe Fabrication
- Tube and Pipe Production
- Waterjet Cutting
Industry Directory
Webcasts
Podcasts
FAB 40
Advertise
Subscribe
Account Login
Search
Aluminum Workshop: Closing the book on porosity
- By Frank Armao
- May 15, 2018
- Article
- Aluminum Welding
In the last two columns we’ve discussed in detail shielding gas problems and porosity. Originally, I had thought we covered the topic thoroughly, but recently I was confronted with a few incidents that convinced me to touch on a few more areas within the topic pertaining to GMAW gun consumables.
Gas Nozzles. First, be sure to use the correct gas nozzle diameter for your application. In general, the inner diameter of the nozzle should be at least as big as the width of the weld you are depositing. If you try to make a ¾-in.-wide weld pass using a 3/8-in.-dia. nozzle, you will have poor gas coverage, and the weld will most probably appear black.
Next, aluminum GMAW produces a lot of fine spatter that can accumulate on the inside of the nozzle, which can really disrupt the shielding gas flow. Surprisingly, one large spatter ball on the inside of the nozzle can have an even worse effect. Take the time to inspect the nozzle inner diameter once in a while, scraping out any spatter buildup.
Gas Diffuser. Make sure you have the right gas diffuser on the gun. Just because it screws onto the end of the gun barrel doesn’t mean it’s the right one. Diffusers for aluminum applications often have different hole diameters, number of holes, or hole orientations than those for steel. Using the wrong diffuser can, at worst, totally block off gas flow or severely restrict it. Additionally, if the diffuser is the wrong length, it will put the end of the contact tip in the wrong place in the torch.
Contact Tip. We have already discussed contact tips, so I won’t repeat myself by going into detail. Just be sure that the end of the contact tip is slightly recessed (1/8 in. to ¼ in.) inside the gas nozzle. It should not stick out beyond the gas nozzle when welding aluminum as it normally does when welding steel. Some manufacturers accomplish this by using a slip fit for the gas nozzle on the torch barrel, so you can slide it to the right position. Other manufacturers put the gas nozzle securely on screw threads and make shorter contact tips for aluminum welding. Both methods work.
Gooseneck. The last item we need to discuss is the gun barrel for either a gooseneck or pistol grip gun. Many manufacturers make these removable so you can use a straight or curved barrel, or a barrel of a different length, angle, or radius. Such barrels usually are attached to the gun by tightening a threaded fitting. Before tightening the barrel, make sure it is well-seated in its mating fitting on the torch.
Check that the threaded fitting is securely tightened. While this may seem obvious, I have seen several cases (and have been the victim once myself) where the welds looked all black and terrible. All it took to fix the problem was to loosen the threaded fitting and push and twist the gooseneck a bit. All of a sudden, the gooseneck popped into the gun barrel about 1/8 in. farther. The fitting was tightened and the welds were fine after that.
It turned out that there were rubber O-rings that had to seat between the gooseneck and the gun barrel. When the gooseneck wasn’t quite all the way on (even though it felt like it was), the O-rings weren’t seated, and little or no shielding gas could flow the rest of the way down the torch; it was all leaking out around the O-rings.
About the Author
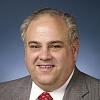
Frank Armao
Aluminum Consulting Inc.
440-479-0239
About the Publication
Related Companies
subscribe now
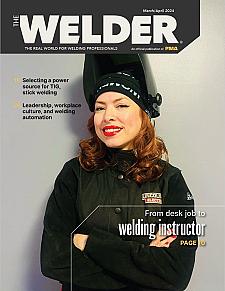
The Welder, formerly known as Practical Welding Today, is a showcase of the real people who make the products we use and work with every day. This magazine has served the welding community in North America well for more than 20 years.
start your free subscription- Stay connected from anywhere
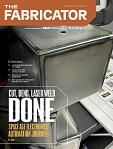
Easily access valuable industry resources now with full access to the digital edition of The Fabricator.
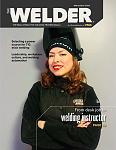
Easily access valuable industry resources now with full access to the digital edition of The Welder.
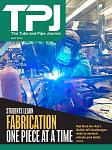
Easily access valuable industry resources now with full access to the digital edition of The Tube and Pipe Journal.
- Podcasting
- Podcast:
- The Fabricator Podcast
- Published:
- 04/16/2024
- Running Time:
- 63:29
In this episode of The Fabricator Podcast, Caleb Chamberlain, co-founder and CEO of OSH Cut, discusses his company’s...
- Trending Articles
Sheffield Forgemasters makes global leap in welding technology
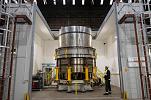
ESAB unveils Texas facility renovation
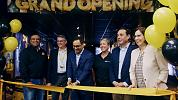
Engine-driven welding machines include integrated air compressors
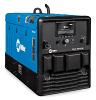
How welders can stay safe during grinding
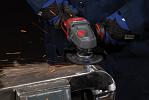
The impact of sine and square waves in aluminum AC welding, Part I
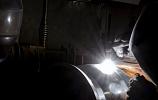
- Industry Events
16th Annual Safety Conference
- April 30 - May 1, 2024
- Elgin,
Pipe and Tube Conference
- May 21 - 22, 2024
- Omaha, NE
World-Class Roll Forming Workshop
- June 5 - 6, 2024
- Louisville, KY
Advanced Laser Application Workshop
- June 25 - 27, 2024
- Novi, MI