Senior Editor
- FMA
- The Fabricator
- FABTECH
- Canadian Metalworking
Categories
- Additive Manufacturing
- Aluminum Welding
- Arc Welding
- Assembly and Joining
- Automation and Robotics
- Bending and Forming
- Consumables
- Cutting and Weld Prep
- Electric Vehicles
- En Español
- Finishing
- Hydroforming
- Laser Cutting
- Laser Welding
- Machining
- Manufacturing Software
- Materials Handling
- Metals/Materials
- Oxyfuel Cutting
- Plasma Cutting
- Power Tools
- Punching and Other Holemaking
- Roll Forming
- Safety
- Sawing
- Shearing
- Shop Management
- Testing and Measuring
- Tube and Pipe Fabrication
- Tube and Pipe Production
- Waterjet Cutting
Industry Directory
Webcasts
Podcasts
FAB 40
Advertise
Subscribe
Account Login
Search
Siempre imperfecto, siempre mejorando
Perfeccionando el calendario en la fabricación de metal a la medida
- By Tim Heston
- June 13, 2023
- Article
- Shop Management
Los fabricantes han invertido en láseres de fibra cada vez más potentes, prensas dobladoras con cambios automatizados de herramientas, capacidad de soldadura expandida, recubrimiento con polvo – la lista de gastos en capital continúa, y sin embargo el desempeño de la entrega a tiempo sigue siendo obstinadamente mediocre. De acuerdo con la encuesta anual de Financial Ratios & Operational Benchmarking (Coeficientes financieros y comparativa de mercado operacional), publicada por Fabricators & Manufacturers Association, la entrega a tiempo promedio ha rondado entre 77% y 88% durante la década anterior.
Por supuesto, los retos de la cadena de suministro han complicado la situación conforme la entrega de material y componentes adquiridos se vuelve más errática. La escasez aguda de trabajadores y las ausencias inesperadas tampoco han ayudado. Sin embargo, la entrega a tiempo en la fabricación a la medida era mediocre mucho antes de la pandemia, y la mayoría de los fabricantes han lidiado con la escasez de mano de obra calificada por años. Entonces, ¿cuál es el problema?
Un taller establece un calendario y sin embargo no se apega a éste. Ocurre el caos. El tiempo extra crece junto con la frustración. Las causas raíz abundan y pueden ser generalizadas, afectando a cada proceso del negocio. Mejorar las cosas es un rompecabezas complicado, y una pieza importante puede implicar encontrar una mejor manera de calendarizar.
Mejoras en los datos
Cada taller de fabricación a la medida tiene su propia mezcla única de clientes, por lo que las razones detrás de los retos de calendarización son demasiado numerosas para listarse, pero muchas de éstas tienen que ver con un área clave: falta de buena información. Como con todo lo demás, cuando se trata de calendarizar, basura entra, basura sale.
“Hemos visto en el transcurso de los años que las compañías están obteniendo mejor información”, dijo Dan Hahn, vicepresidente de ATS Lean Scheduling International, proveedor de software de planeación y calendarización avanzada (APS, por sus siglas en inglés) en Bradenton, Florida. Sin embargo, los datos siguen siendo uno de nuestros principales problemas. Si trabajamos con un fabricante con datos buenos, limpios, es una bendición.
“Recientemente, hemos visto muchos problemas con las personas y con los materiales, y a los talleres les cuesta trabajo mantener un grupo consistente de personas talentosas”, continuó Hahn. “Ahora están recurriendo a nosotros, los proveedores de software APS, buscando adquirir la capacidad de recalendarizar, reorganizar y reaccionar al cambio”.
La recolección de datos sigue estando en el centro del problema. Algunos de éstos podrían guardarse en software inadecuado que necesita desesperadamente una actualización. Y aun con el mejor software, no cambia el hecho de que si basura entra, basura sale. Es difícil calendarizar con base en la capacidad disponible cuando un fabricante no sabe cuál es realmente la capacidad disponible.
Imagine que un operador de prensa dobladora marca el inicio de un trabajo de doblado específico, luego se da cuenta de que necesita traer herramental del cuarto de herramientas en el otro extremo de la planta. Así que, camina, obtiene el herramental, configura e inicia el trabajo, luego finalmente marca el fin del trabajo. El sistema dice que el trabajo tardó 30 minutos, pero en realidad le llevó al operador menos de la mitad del tiempo configurar la máquina y producir partes. El problema podría ser fácil de detectar si ese trabajo se presenta con frecuencia. (Al final de cuentas, de eso se trata ir a Gemba, el lugar de la acción.) Sin embargo, en una operación de alta mezcla de productos, ésta y muchas otras tareas ineficientes pueden permanecer escondidas y desapercibidas.
Aquí puede ayudar la conexión directa con la máquina y el monitoreo. Imagine el mismo escenario, sólo que esta vez la propia máquina reporta automáticamente el tiempo de producción y el tiempo de configuración real para cada trabajo, así como los requerimientos de personal: el operador, chofer del montacargas o manejador de material, quizás una persona dedicada para la configuración. Esos datos revelan rápidamente mejoras, como tener las herramientas en el punto de uso. Más ampliamente, la conexión rebela lo que realmente está pasando durante la producción.
Compitiendo en las diferencias
“Siendo honesto, un software APS es difícil de implementar”, dijo Mike Liddell, fundador de Lean Scheduling International y autor del libro “The Little Blue Book on Scheduling” (El pequeño libro azul sobre calendarización), un tomo que detalla los retos de la calendarización para el taller con alta mezcla de productos. “Cada compañía es diferente, y esa diferencia es su ventaja competitiva. Se trata de poder incorporar esa diferencia en un software APS”.
Hahn agregó, “debido a que cada fabricante es diferente, con procesos diferentes, necesitamos poder moldear la herramienta APS para mejorar esos procesos”.
Dos talleres de chapa metálica de precisión podrían tener máquinas similares, pero sus clientes son diferentes. Algunos podrían pedir que el taller tenga cierto nivel de inventario de bienes terminados. Otros clientes (pasto y jardín, por ejemplo) podrían tener una demanda altamente estacional, lo que significa que el calendario necesita considerar esa variabilidad en la demanda. Otros clientes más podrían tener ciertos trabajos que hacen que un fabricante use muchos servicios externos y componentes comprados – aún más variables que el software APS necesita considerar.
“Un taller de un solo trabajo podría producir 20,000 partes en un lote, lo cual puede ser fácil de calendarizar pues se tienen las mismas máquinas haciendo las mismas partes una y otra vez”, dijo Hahn. “Luego están los que producen lotes muy pequeños, lo que significa que es necesario enfocarse en los cambios y en cómo procesar mejor el material a través de la ruta”.
Dicha demanda variante da lugar a estrategias diferentes en cuanto a piezas en proceso (WIP, por sus siglas en inglés). Algunos talleres producen ciertos componentes con anticipación para mantener un supermercado de partes del cual pueden surtirse las operaciones corriente abajo. Otros simplemente no pueden producir con anticipación debido a que no saben qué partes van a necesitar.
Esto a su vez da lugar a diferentes estrategias de liberación de órdenes y anidado en el punzón y láser. ¿Tiene sentido cortar con anticipación en el calendario para llenar un nido? De manera alternativa, ¿el taller debe manejar sobrantes o simplemente lidiar con desperdicios excesivos? Además, ¿varios trabajos se agrupan dinámicamente en una sola hoja, o ciertos recursos de corte se dedican sólo a ciertos clientes? ¿Qué pasa con los trabajos que requieren chapas de diferentes grados y espesores? ¿Cómo deben dispersarse y secuenciarse los subcomponentes entre los centros de trabajo de corte del taller?
Además, ¿qué pasa con el tiempo para mantenimiento preventivo que es especialmente crítico para el equipo moderno de la actualidad? Por ejemplo, algunos talleres con láseres de potencia ultra-alta dedican algunas horas o incluso todo un turno para limpiar tablillas. Un láser de 20 kW conectado a automatización puede ser extraordinariamente productivo – hasta que las horquillas en un sistema de automatización de descarga de partes chocan cuando intenta levantar una parte cortada con metal fundido soldado a tablillas atascadas. Las tablillas necesitan limpiarse, los enfriadores necesitan mantenimiento, los espacios de trabajo de la máquina también necesitan limpiarse, y los calendarios necesitan considerar el tiempo y las personas que estas tareas requieren.
Acerca de la secuenciación
Cuando una operación tiene datos buenos, limpios, exactos, es un paso adelante para las oportunidades de calendarizar. Por ejemplo, en su libro, Liddell describe la importancia de la secuenciación de trabajos en un ambiente de alta mezcla de productos, especialmente cuando cada trabajo tiene tiempos de configuración y de producción diferentes en recursos compartidos.
Considere la Figura 1, la cual muestra tres órdenes que necesitan producirse en las mismas tres máquinas, cada una con diferentes tiempos de producción. Ahora considere la Figura 2. Cambiar la secuenciación – de la secuencia “trabajos en azul luego verde luego naranja” cambiar a la secuencia “trabajos en naranja luego verde luego azul” – permite al taller concluir las tres órdenes 27% más rápido. Si aplica secuenciación estratégica en varias máquinas y flujos de valor, la capacidad disponible se dispara, todo sin contratar más personal ni comprar más equipo.
En un contexto de fabricación de metal, considere un conjunto de trabajos de doblado que el supervisor del departamento de prensas dobladoras agrupa en una sola configuración con herramientas comunes acomodadas en toda la cama de la prensa. La configuración parece ideal pues los operadores no necesitan cambiar herramientas. Agrupando los trabajos de esta manera, el departamento produce esos tres trabajos en un tiempo récord.
Sin embargo, esos tres trabajos con una configuración común mantienen ocupados dos recursos finitos – la prensa dobladora y su operador. Imagine si esos trabajos representaran el trabajo azul en el diagrama de Gantt en la Figura 1. Producir esos trabajos al mismo tiempo atrasa otros trabajos en la cola. Si esos tres trabajos de prensa dobladora se separaran, podrían “abrir un carril” para que esos otros trabajos avanzaran en su ruta. Por supuesto, la secuencia implicaría algunas configuraciones de prensa dobladora, pero el tiempo extra se compensaría de sobra con el ahorro de tiempo (y capacidad adicional) que brinda la nueva secuencia.
FIGURA 2. Cuando el trabajo en naranja se hace primero, se ocupan sólo ocho días para procesar las tres órdenes.
La secuenciación también importa en las celdas multiprocesos. En una entrevista el año pasado, Robert Hasty, director general de Humanetics Precision Metal Works, con sede en Dallas, describió cómo la compañía maneja el flujo de trabajos a través de una celda de corte y doblado, la cual incluye una nueva prensa dobladora que forma con aire y otra prensa dobladora antigua que hace operación de doblado profundo. La nueva prensa eléctrica puede configurarse muy rápido, y la primera parte formada usualmente es una parte buena; la prensa eléctrica, no tanto – pero sigue teniendo una capacidad productiva que, con la estrategia adecuada de secuenciación, puede hacer una verdadera diferencia. Además, la operación de doblado profundo de la prensa antigua puede producir un doblez agudo de calidad que es crítico para ciertos trabajos.
En este caso, unas cuantas partes destinadas para doblado profundo son anidadas y cortadas en el láser primero, luego fluyen inmediatamente a la prensa dobladora antigua, donde el operador puede iniciar la configuración y empezar a doblar piezas de prueba. El siguiente nido de partes procesadas en el láser está destinado para formado con aire en la nueva prensa eléctrica. Lo siguiente en el láser es un nido de partes destinado para doblado profundo. Gracias a la secuenciación inteligente, estas partes llegan a la prensa dobladora antigua poco después de que el operador termina de configurarla. Al final, los operadores de la prensa nueva y de la prensa antigua acaban sus respectivos trabajos casi al mismo tiempo – todo gracias a la secuenciación.
Como lo dijo Hasty en una entrevista en 2022, “en cuanto al éxito de nuestro arreglo celular híbrido, la secuenciación lo es todo”.
Por supuesto, Humanetics no solucionó esto manualmente, en una hoja de Excel o de alguna otra manera. El fabricante a la medida emplea su propio equipo de software que desarrolla programas a la medida, siendo uno de ellos una especie de “simulador de cuellos de botella” que mejora el sistema de calendarización existente de la compañía.
El taller usa software por una razón con la que Liddell y Hahn estarían de acuerdo. Escalar la secuenciación, conectando los puntos a través de toda la cadena de valor, desde la orden inicial hasta el embarque final, se vuelve extraordinariamente complicado. Un pequeño cambio en el ensamble, por ejemplo, puede tener efectos dominó en la soldadura, el doblado y el corte. Si se suman complicaciones con la cadena de suministro y con la mano de obra, esas olas pequeñas se convierten en olas enormes.
“Es realmente imposible hacer esto sin software”, dijo Liddell. “Es imposible ver cómo se conecta todo. Es como resolver un cubo de Rubik gigantesco. Cuando cambia una variable, necesitamos ver cómo cambian los otros lados”.
Defina el problema
Supongamos que un taller de fabricación quiere cambiar su estrategia de calendarización. Podría estar usando la función de calendarización en su plataforma de planeación de recursos empresariales (ERP, por sus siglas en inglés). Quizá calendarice manualmente o use un sistema propio desarrollado con los años. Cualquier cosa que estén usando, no está funcionando, por lo que deciden llevar la calendarización al siguiente paso – y empezar con las expectativas correctas es un buen inicio – En toda la manufactura, y en los talleres en particular, el calendario, en constante evolución, siempre es imperfecto.
“Nos enfocamos en la regla 80-20”, dijo Liddell. “Un fabricante puede obtener una solución del 80% para un problema de calendarización con 20% de esfuerzo. Esto aleja a las personas de una de las grandes trampas de implementar un sistema APS, que es la búsqueda de la perfección”.
Sin embargo, antes de implementar la regla 80-20, Lindell recomendó que los talleres tomen distancia de la calendarización y piensen más ampliamente. Como lo escribe en su libro, “este proceso nos fuerza a pensar y documentar claramente el problema del negocio que estamos tratando de solucionar, y listar todos los beneficios que se lograrán si se tiene éxito ... El problema podría ser que están entregando trabajos tarde, están perdiendo clientes, y no pueden reaccionar suficientemente rápido ante las demandas cambiantes de los clientes”.
Definir el problema ayuda a identificar el alcance. Por ejemplo, un fabricante podría estar sumamente atrasado en cierto trabajo que requiere compras especiales y arreglos con proveedores. El trabajo causa dolores de cabeza, pero no es lo que se hace habitualmente del taller. Definir el problema real – desempeño inaceptable de la entrega para las cuentas principales del taller que generan los ingresos – cambia el enfoque. La solución de calendarización resultante no será perfecta, y es muy probable que no resuelva todos los problemas relacionados con ese trabajo inusual. Sin embargo, podría minimizar los efectos que tenga ese trabajo especial en el flujo de trabajo principal del taller.
FIGURA 3. El cambio empieza con los procesos del negocio (centro). Un sistema de calendarización (APS) se hace, se personaliza y se integra en torno a esos procesos. El sistema completo interactúa con tres puntos de contacto: la planta, compras y recepción de la orden.
Evalúe, diseñe y dibuje un mapa
Una vez que un taller define el problema, empieza la evaluación. Como lo escribe Liddell, “recomendar una solución sin saber cómo funciona un negocio – por qué una compañía hace las cosas de cierta manera y cuáles son los problemas particulares de un negocio – sería algo absurdo ... Las soluciones deben diseñarse de adentro hacia afuera. El problema del negocio lleva a una visión de cómo deben ser los nuevos procesos del negocio”.
Esta fase incluye cómo se procesan las órdenes en la oficina, desde la recepción de la orden pasando por preproducción, asegurando que las hojas de ruta y otra documentación del trabajo tengan todo lo que los empleados necesitan para avanzar un trabajo.
Después de la evaluación viene la etapa de diseño. El documento de diseño muestra gráficamente cómo fluye la información, dónde se almacenan los datos (idealmente en un solo lugar – una sola fuente de información verídica), e incluye una explicación de cómo se calculan los datos. Como lo escribió Liddell, “el diagrama de flujo mostrará claramente la manera en que fluyen los datos entre los diversos sistemas y el trabajo que se necesita para hacer eso. Esto incluirá datos que necesitan ser enviados por su sistema APS a otros sistemas, como por ejemplo su ERP o el sistema de recolección de datos de su taller”.
Agregó que la mayoría de las plataformas de calendarización se hacen con base a tres puntos de contacto (vea la Figura 3). Primero está recepción de la orden, que desarrolla las rutas de la orden y las listas de material y calendariza la fecha de entrega con base en la información sobre la capacidad. Luego está compras, que comunica cuando se requieren materiales; el personal de recepción (o alguien más, dependiendo de la operación) registra cuando los materiales están realmente disponibles. El tercer punto de contacto es la planta en sí, que recibe los calendarios de la planta de producción (con base en tiempos estimados) y registra las transacciones de la planta de producción (registrando los tiempos reales).
De aquí se deriva el mapa de ruta de la calendarización, un documento que, como lo escribió Liddell, “explica cómo el nuevo sistema impactará cada área funcional ... El proceso de crear el mapa de ruta de calendarización les da a todos la oportunidad de hacer sugerencias y volverse parte de la solución”.
El mapa les describe a todos – choferes de montacargas, operadores de máquina, soldadores – cómo fluirán la información y el trabajo, cómo los cambios en un área afectan a otras y, lo más importante, por qué las cosas necesitan cambiar. Como lo escribe Liddell en su libro, “la verdad es que una de las principales razones por la que fallan los sistemas de calendarización es porque quienes podrían beneficiarse más no entienden por qué necesitan cambiar”.
Desarrolle, pruebe, implemente, mejore
La fase de desarrollo crea un modelo de trabajo de la plataforma de software de calendarización, de nuevo diseñada en torno a la regla 80-20, donde 20% de esfuerzo resuelve 80% de los problemas. Una prueba posterior implica aplicar prescripciones documentadas para ciertos escenarios del negocio, como recepción, cambio y borrado de una orden.
Luego viene la fase de implementación, cuando el taller podría aplicar su sistema de calendarización nuevo y el heredado en paralelo para validar resultados. Los problemas se resuelven, todo mientras se mantiene el enfoque en la regla 80-20. Los primeros días de la implementación, escribe Liddell, no es momento de agregar más detalles para manejar todos los problemas de calendarización que traigan las personas, sin importar qué tan pequeños o raros sean esos problemas. “La prioridad debe ser concentrarse en lograr estabilidad, debido a que nada destruye más rápido la confianza en un nuevo sistema que la aparición incesante de errores y problemas”.
Una vez que el calendario se vuelve estable, todo el proceso empieza de nuevo en un ciclo virtuoso. Con los problemas principales de calendarización resueltos, los problemas fuera del alcance ahora se meten a ese 80% de problemas solucionables mediante 20% de esfuerzo.
Por qué la calendarización es tan difícil
En el centro del problema se encuentra la variabilidad – en el tiempo de ciclo, procesamiento de cotizaciones y órdenes, disponibilidad de material, asistencia de los empleados, retrabajo causado por información incorrecta, mala comunicación en la cadena de suministro, falta de capacitación, y variación en el desempeño entre empleados y entre turnos. Mientras más variabilidad tenga una operación, más piezas en proceso (WIP) que absorban la variabilidad necesitará entre pasos de procesamiento, y más largos tendrán que ser los plazos de entrega del taller.
Como lo describió Liddell, “el problema fundamental que tienen todas las plantas es que todo está conectado. Cuando algo ocurre, las personas no saben cómo impacta esto a otras cosas”.
Lo que hace a la fabricación de metal (y a la manufactura en general) tan absorbente y tan difícil es la red de interacción entre la fabricación y la entrega de un producto. Cada acción tiene una reacción; cada chapoteo tiene olas. Los avances en la recolección de datos, el mantenimiento predictivo, el monitoreo de máquina, el control de la producción y (por supuesto) el software de calendarización siguen dibujando una imagen cada vez más exacta de las plantas de producción. Sin embargo, las plantas de producción siguen siendo sumamente complejas y, al igual que las personas que las operan, nunca son perfectas.
Las figuras son de Mike Liddell, “The Little Book on Scheduling” (Palmetto, Fla.: Joshua1ine Publishing, 2008), p. 51-53, 81. Reimpresas con permiso.
About the Author
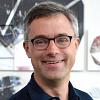
Tim Heston
2135 Point Blvd
Elgin, IL 60123
815-381-1314
Tim Heston, The Fabricator's senior editor, has covered the metal fabrication industry since 1998, starting his career at the American Welding Society's Welding Journal. Since then he has covered the full range of metal fabrication processes, from stamping, bending, and cutting to grinding and polishing. He joined The Fabricator's staff in October 2007.
About the Publication
subscribe now
FMA Communications ha introducido al mercado la edición en Español de la revista The Fabricator. Esta versión consiste del mismo tipo de artículos técnicos y sección de lanzamientos de nuevos productos que actualmente presentan el personal de primera categoría de Fabricator en Inglés.
start your free subscription- Podcasting
- Podcast:
- The Fabricator Podcast
- Published:
- 04/30/2024
- Running Time:
- 53:00
Seth Feldman of Iowa-based Wertzbaugher Services joins The Fabricator Podcast to offer his take as a Gen Zer...
- Trending Articles
Los operadores de prensa dobladora inexpertos hacen indispensable el repensar la seguridad
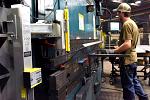
Prescripción para la reducción del desperdicio: arreglo esbelto de las instalaciones
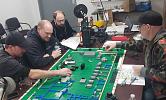
Anidado para la estabilidad del corte láser
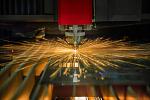
La máquina procesadora de placas crea biseles complejos en un solo corte
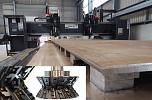
El software guía a los soldadores a través de instrucciones de trabajo
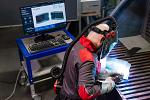
- Industry Events
Pipe and Tube Conference
- May 21 - 22, 2024
- Omaha, NE
World-Class Roll Forming Workshop
- June 5 - 6, 2024
- Louisville, KY
Advanced Laser Application Workshop
- June 25 - 27, 2024
- Novi, MI
Precision Press Brake Certificate Course
- July 31 - August 1, 2024
- Elgin,