- FMA
- The Fabricator
- FABTECH
- Canadian Metalworking
Categories
- Additive Manufacturing
- Aluminum Welding
- Arc Welding
- Assembly and Joining
- Automation and Robotics
- Bending and Forming
- Consumables
- Cutting and Weld Prep
- Electric Vehicles
- En Español
- Finishing
- Hydroforming
- Laser Cutting
- Laser Welding
- Machining
- Manufacturing Software
- Materials Handling
- Metals/Materials
- Oxyfuel Cutting
- Plasma Cutting
- Power Tools
- Punching and Other Holemaking
- Roll Forming
- Safety
- Sawing
- Shearing
- Shop Management
- Testing and Measuring
- Tube and Pipe Fabrication
- Tube and Pipe Production
- Waterjet Cutting
Industry Directory
Webcasts
Podcasts
FAB 40
Advertise
Subscribe
Account Login
Search
Construyendo una vasta estructura tubular, una sección de caja irregular a la vez
El fabricante utiliza tecnología robótica para construir moldes de hormigón para presa hidroeléctrica
- By Eric Lundin
- August 10, 2021
- Article
- Automation and Robotics
Suena su teléfono. Es una llamada sobre una oferta para un trabajo de fabricación y suena sencillo. La persona al otro lado de la línea quiere que usted construya algo como una caja de acero. No es exactamente una caja, sino una caja con extremos abiertos. Debe estar hecho de seis piezas de placa: una parte superior y otra inferior, dos lados y dos soportes que corren paralelos a los lados. Cuando termine, la caja debe tener 24 pulgadas de alto, 30 pulgadas de ancho y 36 pulgadas de largo.
Debe cortar las piezas, fijarlas, soldarlas y limpiar los bordes. Suena fácil.
Bueno, no es tan fácil. El cliente necesita estructuras en forma de caja que tengan otros diseños y tamaños, algunos constan de hasta 14 componentes individuales, y luego, eventualmente, tendrá que unir uno al siguiente, al siguiente y al siguiente.
Un conjunto de cajas de acero. Entendido. No hay problema.
Pero a medida que el cliente comienza a describir el proyecto con más detalle, se vuelve más complicado. Necesita verter un poco de hormigón, un poco más de 1,000 toneladas, y necesita que usted construya un molde para el proceso de fundición. El cliente necesita muchas de estas cajas ensambladas para hacer el molde. Es un molde grande y usted necesita hacer muchas cajas.
Está claro que tendrá que configurar una celda para cortar y ensamblar el acero para hacer estas cajas para hacer este molde. Usted realmente no tiene la mano de obra para emprender un gran proyecto, pero sabe que puede usar un robot para algo repetitivo como esto. Bien, bien.
El cliente -bueno, todavía es un cliente potencial, pero con suerte lo será pronto- habla un poco más y resulta que no va a construir una línea recta de cajas en una fila; el conjunto tendrá una curva, tanto que la última caja instalada en el conjunto se unirá a la primera caja.
¿Cómo va a pasar eso? Bueno, cada caja no es realmente un rectángulo. Los lados están inclinados.
Ajá…
El mundo moderno prospera con ángulos rectos y líneas rectas. Mire cualquier artículo fabricado (un electrodoméstico, una máquina, un gabinete, un estante) y verá muchas rectas y ángulos de 90 grados. Casi todo es ortogonal. En arquitectura, casi todos los edificios, excepto los diseñados por personas como Frank Gehry y Santiago Calatrava, tienen lados perfectamente rectos, como todo lo que está adentro, desde las paredes hasta las tuberías.
Una representación de un encofrado de canal de desfogue muestra los contornos y las dimensiones únicas de cada una de las estructuras de bloques de acero que contiene.
Estas estructuras de caja no serán ortogonales. Su cliente está hablando de una curva. Una curva grande y amplia. Bueno, puede que eso no sea tan malo. ¿Está hablando de un círculo? Hacer un ensamblaje circular requeriría un sistema de fijación más complicado que un rectángulo, pero en realidad no es tan difícil. Un círculo tiene un radio, por lo que un accesorio sería adecuado para cada caja del ensamblaje.
Debe configurar una línea de celda de trabajo para comenzar a cortar piezas para hacer formas rectangulares ligeramente inclinadas y hacer un ...
¿Ahora qué es eso? Después de todo, no es un círculo. Es más parecido a una elipse. Es un círculo que se ha aplanado, por lo que los lados se curvan suavemente y tiene radios estrechos en sus extremos. Una elipse no tiene cambios repentinos en el radio, lo que significa que el radio cambia continua y gradualmente a lo largo de la circunferencia.
Esto es desconcertante. ¿Cómo se supone que se verá este proyecto cuando esté terminado?
La mitad izquierda de la elipse es una imagen especular de la mitad derecha, pero la mitad superior no es una imagen especular de la mitad inferior; además, después de hacer esta elipse, tienes que hacer otra elipse, una que sea un poco diferente a la primera, y unirlas. Y luego tienes que hacer y unir otra y otra, hasta haber hecho 22 en total. ¿Es esto un tubo? Sí, es un tubo. Es un tubo que se irá ensamblando poco a poco. Imagínese cortar un tubo en 22 anillos. Usted revertirá ese proceso construyendo un anillo a la vez y uniéndolos.
Va a necesitar mucho acero, mucho alambre de soldadura y mucho tiempo. Ah, y tendrá que ajustar todos los componentes individuales que tienen formas irregulares y tamaños inconsistentes.
Diseñando un encofrado de canal de desfogue
La humanidad ha construido presas para controlar los ríos durante milenios; agregar un generador hidroeléctrico a una presa es increíble. La inversión de capital es enorme y el costo de mantenimiento algo en qué pensar, pero utiliza energía natural para producir energía artificial. Siempre que la lluvia sea constante y la gravedad no ceda, es una excelente manera de proporcionar un flujo constante de corriente eléctrica.
Diseñado y construido para evacuar el agua debajo de un generador hidroeléctrico, un canal de desfogue funciona como una manga para proteger la presa. La presa está hecha de hormigón común. Es un buen material para construir un depósito que contenga agua, pero no es bueno para canalizar el agua porque se erosiona demasiado rápido. El canal de desfogue está hecho de hormigón especializado que resiste la erosión incluso cuando se expone continuamente al agua corriente.
Una vez que el agua sale del depósito y entra en la entrada de la unidad hidroeléctrica, circula alrededor del rotor, empujando las paletas que hacen girar la turbina, gastando así la mayor parte de su energía. En este punto, el agua cae en el canal de desfogue. Construido con curvas y contornos, el canal de desfogue guía el agua verticalmente lejos de la turbina, luego cambia de dirección y se ensancha para que el agua se ralentice y salga de la presa horizontalmente para reunirse con el flujo del río debajo de la presa.
La firma de ingeniería Wenlock Ltd., Shrewsbury, Reino Unido, fue contratada para desarrollar un proceso para la construcción de una serie de canales de desfogue para la presa Grand Ethiopian Renaissance. Etiopía es una nación grande, hogar de más de 100 millones de ciudadanos. Cuando la presa esté terminada, los generadores hidroeléctricos desarrollarán 16,000 gigavatios-hora de energía anualmente, lo que ayudará a aliviar la aguda escasez de energía del país.
En los componentes del encofrado del canal de desfogue, los planos X, Y y Z variaron sustancialmente.
Es difícil comprender el alcance del proyecto. Como punto de referencia, la presa es tan grande que probablemente el reservorio detrás de ella tarde entre cinco y 15 años en llenarse. La presa es grande, los generadores son grandes y los canales de desfogue son grandes.
Una cosa más: el constructor de la presa no puso todos sus huevos en una sola canasta. Contrató generadores de dos proveedores. Cada uno tiene sus propios diseños para los generadores, las entradas de agua y, por supuesto, los canales de desfogue. El fabricante que presente una oferta para este trabajo tendrá que fabricar canales de desfogue de dos diseños.
Un desafío de ingeniería como pocos
Fijar un proyecto con miles y miles de piezas únicas está fuera de discusión. Si el fabricante construyera accesorios para este proyecto, el tiempo y el esfuerzo para los accesorios competirían contra el tiempo y esfuerzo necesarios para hacer los moldes de los canales de desfogue ellos mismos.
El proyecto llamó la atención de Roberto Garziera, fundador de Wenlock Ltd. Garziera se basa en gran medida en su larga experiencia en fabricación y diseño. Su primer trabajo, uno en el que trabajó todos los veranos hace muchos años, fue hacer trabajos de fabricación para el negocio de su padre. Su exposición a máquinas y herramientas a una edad temprana proporcionó una gran comprensión sobre el uso de procesos de fabricación de metales para fabricar componentes y ensamblajes. Experto en dibujar con lápiz y papel, más tarde adoptó la tecnología avanzada de dibujo en 3D.
Su carrera ha incluido el diseño de maquinaria industrial, el desarrollo de procesos de fabricación de componentes y ensamblajes para proyectos de infraestructura y construcción de acero, y el desarrollo de productos y luego el diseño de la maquinaria y herramientas necesarias para fabricar esos productos.
"Entiendo el diseño", dijo. Como muchas personas en la fabricación, ha visto clientes fabricantes de equipo original que comprenden la facilidad de fabricación y los que no. La realidad del encofrado del canal de desfogue es que no se puede diseñar para facilitar la fabricación.
"La principal dificultad fue moldear más de 500 bloques únicos con superficies externas que eran irregulares para coincidir con la forma del canal de desfogue, mientras que sus superficies internas eran lo suficientemente regulares para atornillar los bloques", dijo Garziera. “La construcción también tenía que permitir que el constructor de la presa aplicara pilares, instalara escotillas para verter el concreto y realizar inspecciones, aplicar anclajes antiflotantes y permitir el desmantelamiento”.
Así es como se veía en detalle: haga aproximadamente 5400 componentes individuales y utilícelos para ensamblar 528 estructuras de caja, luego ensamble esas estructuras de caja en 22 anillos de 24 estructuras de caja cada uno, completando así un encofrado de canal de desfogue.
“En cada bloque, no había dos componentes que fueran paralelos o perpendiculares entre sí”, dijo Garziera. "Después de colocar un componente -comencemos con la placa inferior- en la mesa de ensamblaje, sería imposible determinar la ubicación y orientación exactas de cualquier otro componente utilizando herramientas de taller comunes como una regla, un cuadrado o un transportador".
Para el aspecto de sujeción de trabajos, Garziera necesitaba algo versátil.
Se forma una elipse. Cada componente tenía que ser preciso para que cada estructura de caja y cada elipse fueran precisos y todas las elipses pudieran unirse para formar un gran conjunto.
Todo el mundo sabe que los equipos de fabricación de metales se vuelven más versátiles con cada año que pasa. Hace tres o cuatro décadas, la mayoría de las máquinas realizaban una función, pero los diseñadores de equipos llevan mucho tiempo combinando las funciones de las máquinas. Una sola máquina corta y perfora, forma y cizalla, corta y enhebra, etc. Al mismo tiempo, los sistemas de control avanzados y la capacidad de programación han hecho que las máquinas sean extremadamente versátiles, especialmente las máquinas sin herramientas como cortadoras láser y chorros de agua.
Para la sujeción de piezas, esta versatilidad también está disponible. Viene en forma de robot. Equipado con juntas totalmente articuladas y aumentado con la versatilidad ilimitada de un sistema de control moderno, un robot puede ser el mejor fabricante o asistente de fabricación.
Para este proyecto, sería posible utilizar un robot para colocar cada componente para la soldadura por puntos y luego poner el ensamble a un lado para la soldadura manual en una etapa posterior. Dicho esto, una implementación exitosa requeriría el uso no convencional de un robot.
Ciertamente, los primeros robots fueron programados, pero esos días ya pasaron. En la era moderna, los robots se enseñan en lugar de programar. Después de colocar una pieza de trabajo de muestra en un soporte de trabajo o plantilla, el operador mueve el brazo del robot manualmente a su ubicación inicial, luego a la siguiente ubicación, luego a la siguiente, hasta que el brazo haya trazado la ruta. Una vez hecho esto, el robot conoce todos los puntos de inicio y parada de cada paso, ya sea soldadura, corte, desbarbado o algún otro proceso. Otra posibilidad es manipular el brazo robótico mediante el uso de un controlador de joystick, pero al final, es casi lo mismo que guiar manualmente el brazo del robot.
En la mayoría de las circunstancias, cualquiera de estos es preferible a escribir línea tras línea de código para programar las ubicaciones inicial y final de cada movimiento, la velocidad de cada movimiento, las instrucciones para prender y apagar el soplete, etc. Sin embargo, fabricar miles y miles de piezas únicas y colocarlas en posición para soldarlas no es un caso de "la mayoría de las circunstancias". Para este proyecto, usar los métodos convencionales para enseñar a un robot a comenzar en el punto A y moverse al punto B requeriría trazar las 260,000 trayectorias de corte del punto A y 260,000 del punto B. No hace falta decir que esto estaba descartado.
¿Podría Garziera encontrar otra forma de usar el robot?
Redescubriendo la CNC
Aunque la palabra manufactura implica un proceso manual, el concepto moderno utiliza automatización, líneas de ensamblaje y constancia para una producción eficiente, especializándose en una mezcla baja (preferiblemente, mezcla cero) y alto volumen. La palabra fabricación es una variación de eso, confiando más en las células de trabajo que en las líneas de ensamblaje y, por supuesto, en el trabajo de mezclas altas y volumen bajo.
Hacer una forma de canal de desfogue es un caso extremo de mezcla alta y volumen bajo. De los 5,400 componentes individuales de este proyecto, solo unos pocos fueron repeticiones. El fabricante tendría que lidiar con cada componente como si fuera único, lo que significa que este proyecto no tenía mezclas.
La precisión fue otro factor. Teniendo en cuenta que cualquier error en la precisión probablemente se agravaría en las 5,400 partes, es difícil concebir que el principio y el final de cada elipse se encontrarían si las dimensiones de la estructura de la caja no fueran precisas.
Sin una estrategia viable para fabricar cada pieza con la precisión necesaria y posicionar con precisión para ensamblar cada una de las 5,400 piezas irregulares únicas con una plantilla, abrazadera, tornillo de banco o accesorio, el subcontratista correría el riesgo de hacer una gran pila de chatarra.
Garziera entendió que el modo por el cual un robot aprende una ruta es irrelevante. Un operador puede guiar el brazo del robot a lo largo del camino o usar un controlador para manipularlo, o un programador puede ingresar cada comando línea por línea, pero en cualquier caso, las entradas son datos que el controlador del robot convierte en comandos que almacena y usa.
Debido a que Garziera tenía dibujos digitales del encofrado del canal de desfogue, tenía suficiente información sobre las dimensiones, ubicación y orientación de cada componente individual para exportar datos de transformación lineal para crear los comandos necesarios para programar el robot. Era más que una posibilidad; parecía ser la única forma práctica de ejecutar este proyecto.
“Encontramos un fabricante que tenía la capacidad para este proyecto, e incluso encontramos un robot usado para que lo usara el fabricante”, dijo Garziera.
Al final, Garziera ideó una estrategia de tres partes para hacer que cada parte saliera bien.
Primero, el fabricante cortaría con láser cada pieza de acero para cada caja de una sola pieza de materia prima para que el grosor no variara. Algunas partes necesitaban una curvatura, por lo tanto se curvaron.
En segundo lugar, el robot recogería y colocaría cada pieza sobre una superficie de trabajo estable, la mesa de hierro fundido de una gran máquina fresadora. Para obtener la ubicación correcta, el brazo robótico movería cada pieza hacia el destino, luego ejecutaría un movimiento de 3 ejes completamente articulado (balanceo, cabeceo y viraje) para una ubicación adecuada y consistente. Después de la soldadura por puntos (hecha por los trabajadores, no por el robot) en la ubicación del accesorio, el conjunto se reservaría para la soldadura manual tradicional.
Finalmente, el robot se programaría con otro conjunto de coordenadas para el recorte final con un soplete de plasma. Esto se hizo para finalizar las dimensiones de cada pieza, lo que ayudó a garantizar el ajuste más apretado posible entre los bordes de acoplamiento antes de ensamblar las cajas para formar las secciones de elipse.
Una vez que el proceso estuvo en funcionamiento, se desarrolló sin problemas y no requirió retrabajo, según Garziera.
El éxito en un proyecto como este se basa, y muestra, las capacidades de las máquinas CNC y los robots. Después de la programación, la configuración y algunos ajustes, las máquinas funcionan sin problemas. El alcance total de este proyecto comprendió dos pares de encofrados para los dos tipos de canales de desfogue que comprenden más de 20,000 componentes únicos ensamblados para formar más de 2,000 bloques para hacer cuatro encofrados de canales de desfogue.
Este proyecto sin duda marca un hito en técnicas avanzadas para la fabricación de metales de precisión. La única decepción de Garziera es la naturaleza ortogonal de casi todo lo demás en la fabricación y la construcción, lo que significa que no es probable que este tipo de solución sea necesaria nuevamente en el corto plazo.
About the Author
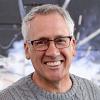
Eric Lundin
2135 Point Blvd
Elgin, IL 60123
815-227-8262
Eric Lundin worked on The Tube & Pipe Journal from 2000 to 2022.
About the Publication
Compañías Relacionadas
subscribe now
FMA Communications ha introducido al mercado la edición en Español de la revista The Fabricator. Esta versión consiste del mismo tipo de artículos técnicos y sección de lanzamientos de nuevos productos que actualmente presentan el personal de primera categoría de Fabricator en Inglés.
start your free subscription- Podcasting
- Podcast:
- The Fabricator Podcast
- Published:
- 04/30/2024
- Running Time:
- 53:00
Seth Feldman of Iowa-based Wertzbaugher Services joins The Fabricator Podcast to offer his take as a Gen Zer...
- Trending Articles
Los operadores de prensa dobladora inexpertos hacen indispensable el repensar la seguridad
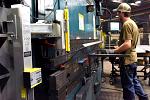
Prescripción para la reducción del desperdicio: arreglo esbelto de las instalaciones
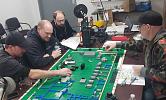
Máquina de corte por láser diseñada para el mercado mexicano
La sierra de doble carro sigue los contornos del tubo perfectamente
La máquina procesadora de placas crea biseles complejos en un solo corte
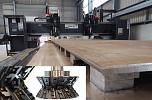
- Industry Events
Pipe and Tube Conference
- May 21 - 22, 2024
- Omaha, NE
World-Class Roll Forming Workshop
- June 5 - 6, 2024
- Louisville, KY
Advanced Laser Application Workshop
- June 25 - 27, 2024
- Novi, MI
Precision Press Brake Certificate Course
- July 31 - August 1, 2024
- Elgin,