- FMA
- The Fabricator
- FABTECH
- Canadian Metalworking
Categories
- Additive Manufacturing
- Aluminum Welding
- Arc Welding
- Assembly and Joining
- Automation and Robotics
- Bending and Forming
- Consumables
- Cutting and Weld Prep
- Electric Vehicles
- En Español
- Finishing
- Hydroforming
- Laser Cutting
- Laser Welding
- Machining
- Manufacturing Software
- Materials Handling
- Metals/Materials
- Oxyfuel Cutting
- Plasma Cutting
- Power Tools
- Punching and Other Holemaking
- Roll Forming
- Safety
- Sawing
- Shearing
- Shop Management
- Testing and Measuring
- Tube and Pipe Fabrication
- Tube and Pipe Production
- Waterjet Cutting
Industry Directory
Webcasts
Podcasts
FAB 40
Advertise
Subscribe
Account Login
Search
La realidad sobre la porosidad de la soldadura
No es tan mala como pudiera creerse
- By Paul Cameron
- July 25, 2022
- Article
- Arc Welding
Paul Cameron, AWS CWI, arguye que la porosidad de la soldadura ha ganado mala reputación de manera injusta. Muchos intentos de arreglar la porosidad terminan empeorando la situación más que si se dejara por la paz. Getty Images
Un joven emprendedor invierte sus ahorros en un nuevo negocio de recolección de basura. Compra un camión nuevo de basura y lo rotula con su nombre, número y un nuevo y sofisticado logo. Lo limpia para una sesión fotográfica vespertina, y mientras revisa las fotos nota un flujo de óxido que baja a un lado del nuevo y sofisticado logo. Al investigar más, descubre que la humedad se está filtrando desde un solo poro de la porosidad encontrada en una soldadura a filete. Eso es algo que nadie quiere ver.
AWS A3.0, Welding Terms and Definitions (términos y definiciones de soldadura) define la porosidad como “discontinuidades tipo cavidad formadas en metal soldado por el atrapamiento de gas durante la solidificación....” Los criterios de aceptación para la porosidad en códigos con los que podemos estar familiarizados pueden verse así:
- AWS D1.1: La porosidad no debe exceder 3/8 de pulgada en cualquier pulgada lineal de soldadura, y no debe exceder ¾ de pulgada en una longitud de 12 pulgadas.
- ASME B31.1: la porosidad no puede tener dimensiones mayores a 3/16 de pulgada.
- API 1104: la porosidad no puede exceder 1/8 de pulgada de diámetro.
Leer esos criterios de aceptación me lleva a creer que los códigos con los que construimos son mucho más permisivos cuando se trata de porosidad que los departamentos de aseguramiento de la calidad que los hacen cumplir.
La porosidad ha desarrollado una mala reputación en la cual su simple mención hace que los soldadores deseen tomar medidas drásticas para removerla o eliminarla. Ciertamente, hay situaciones donde eso es necesario, pero en otras, la presencia de porosidad puede ir desde una molestia estética hasta un beneficio potencial.
¿Qué causa la porosidad?
Entonces, ¿qué causa la porosidad? Dicho de manera sencilla, la porosidad ocurre cuando nitrógeno, oxígeno o hidrógeno queda atrapado dentro del charco de soldadura fundida conforme ésta se solidifica. Esos gases dejan un hueco debajo de la superficie o dejan un poro visible en la superficie:
- Porosidad causada por nitrógeno u oxígeno. Este tipo de porosidad se debe principalmente a una cobertura inadecuada del gas de protección. Hay muchas razones para una cobertura inadecuada del gas de protección.
- La velocidad de flujo del gas de protección es demasiado lenta. La soldadura hecha de acuerdo con una especificación del procedimiento de soldadura (WPS, por sus siglas en inglés) requiere que la velocidad de flujo del gas de protección esté dentro de un rango específico. Asegúrese de que el rango de la velocidad de flujo sea el apropiado, tomando en consideración condiciones ambientales como la velocidad del viento. Si la velocidad de flujo del gas de protección se ajusta correctamente, pero se mide demasiado baja en la boquilla, el sistema de alimentación puede ser el culpable. El sistema de alimentación para gas de protección comprende componentes unidos y sellados con selladores y anillos O en cada una de las diversas conexiones. Una falla de sello da lugar a velocidades de flujo bajas en la boquilla y/o arrastre de nitrógeno y oxígeno hacia el sistema de alimentación, lo que reduce la protección en la soldadura.
- La velocidad de flujo del gas de protección es demasiado alta. Con el gas de protección, más no siempre es mejor. Velocidades de flujo excesivas en la boquilla generarán turbulencia que arrastra nitrógeno y oxígeno al área del charco de soldadura, lo que cambia la mezcla de protección, dando lugar a porosidad.
- Condiciones turbulentas en el charco de soldadura. Algunos códigos limitan la velocidad del viento en el charco de soldadura cuando un proceso usa un sistema de gas de protección externo (GTAW, GMAW y FCAW-G). Estas velocidades altas del viento no se limitan a las tuberías a través de las Grandes Llanuras ni tampoco al piso 45 de una construcción elevada de acero. Pueden encontrarse en su taller y comúnmente son generados por puertas elevadas abiertas, ventiladores de ventilación general o ventiladores individuales de enfriamiento. No se requiere mucho viento para desviar el gas de protección de un charco de soldadura, introduciendo nitrógeno y oxígeno.
- Porosidad causada por hidrógeno. Este tipo de porosidad comúnmente se debe a contaminantes en la unión de soldadura o en el electrodo/relleno.
- Oxidación en superficies de acero. La oxidación ocurre cuando se combinan hierro, agua y oxígeno. Este contaminante se mezclará con la química del metal de soldadura y generará burbujas de hidrógeno que pueden no escapar del metal de soldadura antes de la solidificación. Remover la oxidación de las superficies de acero es crítico para reducir la porosidad.
- Pintura/recubrimientos en superficies de acero. Algunas superficies soldadas están recubiertas. A veces es una pintura ligera, a veces es un compuesto anti-salpicaduras. Independientemente de que las uniones puedan estar recubiertas, es su responsabilidad asegurarse de que el recubrimiento no afecte negativamente la calidad de la soldadura. Puede hacer esto probando y documentando resultados en una WPS. Los recubrimientos excesivos tienen el potencial de mezclarse con el metal de soldadura, evitando que el hidrógeno escape antes de la solidificación.
- Agua, aceite y grasa en superficies de acero. Por supuesto, el agua alrededor del charco de soldadura fundida puede llevar a fractura por hidrógeno, lo cual es una preocupación especial en la industria de la soldadura. A veces el agua en el charco de soldadura es obvia, como lluvia, nieve o hielo. Otras veces no es tan obvia, como cuando se forma en las superficies de contacto, entre placas en una junta a solape, o entre placas de una unión a tope y su barra de respaldo. A veces se forma condensación en el electrodo/relleno debido a una fuerte presencia de humedad. El mantener adecuadamente los electrodos es crítico en esta industria por varias razones, incluida la prevención de la porosidad. Los aceites de corte usados para aserrar tubos o taladrar agujeros en una viga en I son contaminantes comunes usados en el negocio de la fabricación. Esos aceites terminan fácilmente cerca de las uniones de soldadura. Algunos procesos de soldadura pueden manejar la presencia de aceites de corte mejor que otros. Al igual que con los recubrimientos, es su responsabilidad asegurarse de que la WPS considere los fluidos de corte que pudieran llegar a la unión de soldadura. Ciertamente, estos contaminantes tienen el potencial de generar porosidad.
Cómo lidiar con la porosidad
Las discontinuidades de la soldadura se caracterizan por su criticidad. ¿Son lineales o redondas? ¿Hay un filo en la condición del extremo? ¿Llegan a la superficie? Considerando las dimensiones anotadas en los códigos para la porosidad, esta discontinuidad no califica como alta en nuestra lista crítica. La porosidad es una discontinuidad que potencialmente podría detener el crecimiento de una fractura (en un momento se lo explico). Imagine a un soldador reparando una fractura. El primer paso del soldador es determinar lo mejor que pueda dónde se ubican los extremos de la fractura. Esto con frecuencia se hace usando métodos de evaluación no destructivos como ensayos con líquidos penetrantes. Una vez que se localizan los extremos de la fractura, el soldador taladra en los extremos de la fractura, cambiando la condición del extremo filoso a una condición redondeada para ayudar a evitar que la fractura crezca cuando se hace la reparación.
La porosidad puede tener el mismo efecto.
Dependiendo de la técnica, las reparaciones hechas a elementos soldados con porosidad pueden ser devastadoras. Durante mi carrera como soldador e ingeniero de soldadura en manufactura, vi gente que trataba de reparar la porosidad llenando el poro con un golpe rápido de una pistola de GMAW. Tomando la porosidad, la cual con frecuencia es aceptable y queda bastante baja en nuestra lista crítica, y convirtiéndola en un golpe de arco, eso ahora la lleva hasta lo más alto de la lista crítica.
Cuando la porosidad no cumple los criterios de aceptación (lo que significa que es rechazable), la única opción es removerla. Puede remover toda porosidad encontrada en la soldadura y reemplazar la soldadura en esa ubicación, o simplemente puede remover y reemplazar toda la soldadura, lo cual en realidad puede que no sea sencillo. Puede remover la soldadura o la porosidad por cualquier medio permisible por código o por el estándar de su compañía. Esos medios comúnmente incluyen rectificado, raspadura o maquinado.
En situaciones donde la porosidad se encuentra que es aceptable, debe pensarlo dos veces antes de hacer una reparación. Sin embargo, a veces la porosidad aceptable interfiere con los recubrimientos o podría hacer que un producto se viera menos atractivo, haciendo necesario repararlo. Cuando repara una porosidad aceptable, el ingeniero de registro puede permitirle deformar mecánicamente la superficie (un proceso que se denomina calafateado) para ocultarla u oscurecerla. Aparte de eso, el único método de reparación aceptable es remover y reemplazar la soldadura.
Pienso que la porosidad ganó mala fama. Está abajo en mi lista crítica debido a que representa poco más que falta de volumen en una soldadura. Diablos, podría incluso detener una fractura en caso de que se desarrollara. Sin embargo, repito, si estuviera causando un rastro de oxidación que atraviesa la defensa trasera en mi reluciente e impoluto Ford F-150, me gustaría repararla. Y cuando digo “repararla”, quiero decir que me gustaría quitarla.
Aunque usted no lo crea, la porosidad de la soldadura queda bastante abajo en la lista crítica. Varios códigos, incluidos AWS D1.1, ASME B31.1 y API 1104 tienden a ser mucho más permisivos de porosidad que los departamentos de aseguramiento de la calidad que los hacen cumplir. De hecho, la porosidad vista en los tres cordones de soldadura es aceptable en los tres casos de acuerdo con estos códigos.
About the Author
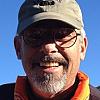
Paul Cameron
Braun Intertec
4210 Highway 14 East
Rochester, MN 55904
About the Publication
subscribe now
FMA Communications ha introducido al mercado la edición en Español de la revista The Fabricator. Esta versión consiste del mismo tipo de artículos técnicos y sección de lanzamientos de nuevos productos que actualmente presentan el personal de primera categoría de Fabricator en Inglés.
start your free subscription- Podcasting
- Podcast:
- The Fabricator Podcast
- Published:
- 04/30/2024
- Running Time:
- 53:00
Seth Feldman of Iowa-based Wertzbaugher Services joins The Fabricator Podcast to offer his take as a Gen Zer...
- Trending Articles
Los operadores de prensa dobladora inexpertos hacen indispensable el repensar la seguridad
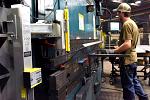
Prescripción para la reducción del desperdicio: arreglo esbelto de las instalaciones
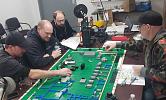
Máquina de corte por láser diseñada para el mercado mexicano
La sierra de doble carro sigue los contornos del tubo perfectamente
La máquina procesadora de placas crea biseles complejos en un solo corte
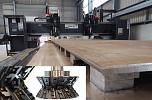
- Industry Events
16th Annual Safety Conference
- April 30 - May 1, 2024
- Elgin,
Pipe and Tube Conference
- May 21 - 22, 2024
- Omaha, NE
World-Class Roll Forming Workshop
- June 5 - 6, 2024
- Louisville, KY
Advanced Laser Application Workshop
- June 25 - 27, 2024
- Novi, MI