Welding Engineer
- FMA
- The Fabricator
- FABTECH
- Canadian Metalworking
Categories
- Additive Manufacturing
- Aluminum Welding
- Arc Welding
- Assembly and Joining
- Automation and Robotics
- Bending and Forming
- Consumables
- Cutting and Weld Prep
- Electric Vehicles
- En Español
- Finishing
- Hydroforming
- Laser Cutting
- Laser Welding
- Machining
- Manufacturing Software
- Materials Handling
- Metals/Materials
- Oxyfuel Cutting
- Plasma Cutting
- Power Tools
- Punching and Other Holemaking
- Roll Forming
- Safety
- Sawing
- Shearing
- Shop Management
- Testing and Measuring
- Tube and Pipe Fabrication
- Tube and Pipe Production
- Waterjet Cutting
Industry Directory
Webcasts
Podcasts
FAB 40
Advertise
Subscribe
Account Login
Search
5 consejos para aumentar el rendimiento de la soldadura
La mejora requiere un esfuerzo de grupo
- By Robert Fox
- December 10, 2020
- Article
- Arc Welding
El aumentar el rendimiento de la soldadura no es un proceso de un paso. Se requiere un compromiso de tiempo, mano de obra y recursos financieros para ser fructífero. Emprender un proyecto así requiere una mente abierta. Evalúe si una modificación especifica tiene sentido, y si lo tiene, esté preparado para hacer cambios.
Podría requerirse más que girar una perilla en una fuente de poder. Por ejemplo, cambiar metales de aportación puede requerir recalificación. Podría necesitar hacer compras importantes, como sujeciones o posicionadores, que lleva tiempo establecer las pautas del retorno de la inversión.
La meta es crear eficiencias en toda la operación, tanto corriente arriba como corriente abajo de la soldadura, que aumenten el número de partes que se mandan al exterior. Considere los siguientes cinco consejos para ayudar a facilitar el proceso a través de todas sus etapas.
1. Haga un estudio de tiempo
Un primer buen paso, un estudio de tiempo, puede ayudar a identificar la verdadera fuente de los cuellos de botella. Sin embargo, para revelarlos, necesita empezar el estudio de tiempo mucho antes de iniciar el primer arco. Algunos procesos son esenciales para preparar una parte para soldadura, mientras que otros podrían ser alterados o eliminados. Quienes tienen inspector de soldadura certificado o certificaciones de supervisor de soldadura certificado de la American Welding Society típicamente están muy versados en los protocolos de los estudios de tiempo.
El estudio debe identificar y cronometrar cada actividad en toda la operación. Observe todo y regístrelo. Considere fabricación, doblado o estampado de las partes, manejo de material hacia la celda de soldadura, soldadura por puntos y preparación de las partes, tiempo de soldadura, limpieza post-soldadura, cambio de consumibles y cilindro de gas, remoción de las partes de la celda de soldadura, pintura, paros planeados y paros no planeados o tiempo improductivo.
Una vez que termine el estudio de tiempo, establezca un plan que categorice las actividades de pre-soldadura, soldadura y post-soldadura. Localice los pasos que no agregan valor y dificultan a los soldadores concluir las soldaduras lo más rápido posible. Por ejemplo, quitar la escoria dejada por la soldadura por arco con núcleo de fundente (FCAW) es un mal necesario, pero también es un paso sin valor agregado que evita concluir las soldaduras lo más rápido posible.
El plan debe ser exacto y factible. Los beneficios financieros de un mayor rendimiento no pueden lograrse si los procesos corriente arriba no alimentan partes a la celda de soldadura de manera consistente. De manera similar, un mayor rendimiento de la soldadura no tiene efecto si los procesos corriente abajo no pueden manejar el aumento de volumen, y las partes soldadas simplemente se mantienen apiladas como trabajo en proceso. En estas situaciones, evite cambios que dejen a los soldadores desocupados, a menos que puedan moverse y ayudar a lograr metas de producción en otra parte.
2. Cree una especificación de procedimientos de soldadura
Las especificaciones de procedimientos de soldadura (WPS, por sus siglas en inglés) ayudan a los soldadores a completar soldaduras de alta calidad de manera repetida. Cuando se siguen bien, éstas ayudan a estandarizar el proceso de soldadura.
Un elemento de productividad toma en consideración una WPS. La WPS comunica los parámetros de soldadura requeridos que a su vez ayudan a asegurar que la soldadura se lleve a cabo de la manera más eficiente posible. Una mayor eficiencia es igual a una mayor productividad y más partes producidas.
Una WPS bien escrita considera las realidades e incertidumbres de la soldadura, como la destreza del personal y la variación en la preparación, pero es suficientemente restrictiva para garantizar la eficiencia y la calidad. Tener una WPS, buena documentación para cada elemento soldado y capacitación adecuada del soldador ayuda a asegurar que las soldaduras sean concluidas de manera rápida y correcta desde la primera vez. Considere desarrollar una WPS para soldadura tanto plana/horizontal como fuera de posición.
Hecha con alambre con núcleo de metal, esta soldadura de filete tiene buenas características de fusión y humedad. Los alambres con núcleo de metal ofrecen un arco ancho en forma de cono que une huecos para combatir el riesgo de perforación y la falta de fusión de pared lateral.
Junto con una WPS, un registro de calificación de procedimientos (PQR, por sus siglas en inglés) podría ser requerido por el código de fabricación. Incluso en casos donde no se requiere un PQR, éste puede ser útil. El PQR soporta a la WPS con base en las pruebas de soldadura. Éste ayuda mostrar que si los soldadores siguen la WPS, producirán una soldadura buena con suficientes propiedades mecánicas, lo que minimizará el riesgo de retrabajo que puede reducir dramáticamente el rendimiento.
3. Atienda los procesos corriente arriba y de pre-soldadura
La preparación de partes es un excelente ejemplo de actividades de mejoramiento corriente arriba. Si un dado de estampado empieza a desgastarse, las tolerancias y la preparación pueden empezar a variar. Una mala preparación obliga a modificar los parámetros de soldadura para evitar defectos de soldadura como por ejemplo soldaduras perforantes, sub-dimensionadas o nulas, particularmente en aplicaciones automatizadas. Para las operaciones de estampado, monitoree el buen estado de los dados y reemplácelos según sea necesario. Para una soldadura robótica repetible, mantenga la fijación de partes para asegurar que las partes y las soldaduras estén bien colocadas.
Los procesos corriente arriba pueden introducir contaminantes como por ejemplo aceites de embutido o maquinado que pueden contribuir a defectos relacionados con la porosidad en el proceso de soldadura. Se pueden minimizar estos contaminantes modificando e implementando procesos como limpieza de pre-soldadura, la cual usualmente requiere mucho menos tiempo que el retrabajo de post-soldadura.
Considere también la condición del material. Los soldadores no necesitan limpiar herrumbre fuerte y otros contaminantes si el material está limpio desde el principio. Siempre que sea posible, almacene los materiales en un área limpia y seca. Si esto no es posible, considere metales de aportación alternativos como por ejemplo alambres con núcleo de metal o núcleo de fundente que pueden soldar a través de contaminantes.
Ciertas actividades de pre-soldadura pueden beneficiar al rendimiento en algunas aplicaciones pero dificultarlo en otras. El arqueo, por ejemplo, ayuda a compensar la distorsión en partes grandes al introducir un doblez o curva en una parte recta. La soldadura posterior distorsiona la parte doblada a su rectitud esperada. Esto ayuda a minimizar el desperdicio y retrabajo causados por la distorsión, por lo que más partes pueden ir a la celda de soldadura. Sin embargo, la operación de arqueo cuesta tiempo. De ser posible, reconsidere el proceso de soldadura o el diseño de partes para reducir o eliminar la fuente de distorsión en sí.
4. Aumente el tiempo de arco encendido
Optimizar los parámetros de soldadura es una de las tareas más importantes en una celda de soldadura, y con frecuencia pasa inadvertida. Los parámetros de soldadura por debajo de lo óptimo pueden evitar que los soldadores o la maquinaria suelden tan rápido como podrían hacerlo de manera cómoda. Los parámetros óptimos aumentan las velocidades de deposición, lo cual puede acelerar las velocidades de viaje y reducir el número de pasadas para concluir una soldadura.
Dicho lo anterior, también considere el proceso de soldadura que elija. Algunos tienen velocidades de deposición más altas que otros, como por ejemplo la soldadura por arco de metal con gas (GMAW) contra la FCAW.
Considere además el metal de aportación que usa. Algunos ofrecen ritmos de deposición más altos y velocidades de viaje más rápidas dentro del mismo proceso de soldadura—como es el caso con alambres con núcleo de metal en comparación con alambres sólidos. Además de mejorar la velocidad de viaje de la soldadura, los alambres con núcleo de metal ofrecen un arco ancho con forma de cono que une huecos para combatir el riesgo de perforación o retrabajo de partes por falta de fusión de pared lateral.
También tome medidas para evitar la sobre-soldadura, la cual no aporta una mejora práctica al rendimiento de la soldadura a costa de tiempo de mano de obra y materiales.
Cualquiera que sea el metal de aportación que use, consulte la hoja de datos del producto preparada por el fabricante del metal de aportación. Éstos ofrecen información valiosa que incluye amperajes, volts, velocidad de alimentación del alambre y distancia recomendada de la punta de contacto a la pieza de trabajo. Confirme que las velocidades de viaje y de alimentación del alambre de la soldadura estén optimizadas y funcionen bien juntas para minimizar la sobre-soldadura y lograr un contorno de cordón óptimo.
Pruebe seleccionando un alambre qPruebe seleccionando un alambre que genere menos islas de silicio (mostradas aquí) para que tarde menos tiempo removiéndolas después de la soldadura.ue genere menos islas de silicio (mostradas aquí) para que tarde menos tiempo removiéndolas después de la soldadura.Pruebe seleccionando un alambre que genere menos islas de silicio (mostradas aquí) para que tarde menos tiempo removiéndolas después de la soldadura.
5. Minimice las actividades de post-soldadura y corriente abajo
Un análisis de causa raíz puede ayudar a identificar maneras de minimizar las actividades de post-soldadura y mantener las partes moviéndose. A diferencia de un estudio de tiempo que observa cada tarea en la operación de soldadura y calcula cuánto tiempo se requiere para concluirlas, un análisis de causa raíz evalúa por qué ocurre un problema.
Por ejemplo, si llegan partes con porosidad al área de post-soldadura, ¿qué causa esa porosidad? Podrán ser los ajustes de soldadura, boquillas con mal mantenimiento o un mantenimiento poco frecuente, o fugas del gas de protección. Identificar tempranamente estas causas raíz reduce la necesidad de reparaciones más adelante en la operación.
Asegúrese de que los soldadores estén capacitados para identificar y rectificar discontinuidades de soldadura antes de que una parte salga de la celda de soldadura. El tiempo y el costo del retrabajo crecen exponencialmente conforme la parte avanza en la operación. Para el momento en que una parte defectuosa llega al área de post-soldadura, requerirá mano de obra adicional que la repare. La mano de obra cuesta dinero. Además, podría incurrir en gastos por partes de reemplazo u operaciones adicionales.
Siempre que sea posible, evite producir soldaduras antiestéticas que requieran contorneado de cordón (rectificado/maquinado) para reducir protuberancias elevadoras de esfuerzo y hacerlas estéticas. En lugar de esto, implemente parámetros en la celda de soldadura que mejoren la apariencia de la soldadura desde el principio.
Considere además el usar un compuesto anti-salpicadura o un proceso de soldadura y alambre de poca salpicadura para eliminar la necesidad de lijar salpicaduras. Seleccione un alambre que genere escoria fácil de remover, y/o menos islas de silicio (o ninguna); de esa manera, perderá menos tiempo en removerlas después de la soldadura.
Reuniendo Todo
Aumentar el rendimiento de la soldadura es un esfuerzo de grupo. Todo mundo, desde los gerentes generales hasta los operadores de primera línea, incluyendo soldadores, deben dedicarse a hacer mejoras. Algunos casos pueden requerir capacitación adicional de los soldadores para aprender nuevos procesos o para ajustarse a las particularidades de un nuevo metal de aportación. En cualquier caso, mantenga abiertas las líneas de comunicación. Un intercambio abierto de ideas puede ayudar mucho para asegurar el éxito.
Robert Fox es ingeniero de soldadura y especialista en mercadotecnia de Hobart, 400 Trade Square East, Troy, OH 45373, 800-424-1543, www.hobartbrothers.com.
About the Author
Robert Fox
101 Trade Square East
Troy, OH 45373
937-332-4000
About the Publication
Compañías Relacionadas
subscribe now
FMA Communications ha introducido al mercado la edición en Español de la revista The Fabricator. Esta versión consiste del mismo tipo de artículos técnicos y sección de lanzamientos de nuevos productos que actualmente presentan el personal de primera categoría de Fabricator en Inglés.
start your free subscription- Podcasting
- Podcast:
- The Fabricator Podcast
- Published:
- 04/30/2024
- Running Time:
- 53:00
Seth Feldman of Iowa-based Wertzbaugher Services joins The Fabricator Podcast to offer his take as a Gen Zer...
- Trending Articles
Los operadores de prensa dobladora inexpertos hacen indispensable el repensar la seguridad
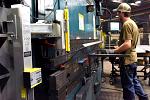
Prescripción para la reducción del desperdicio: arreglo esbelto de las instalaciones
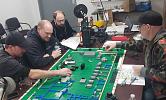
Anidado para la estabilidad del corte láser
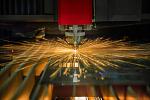
La máquina procesadora de placas crea biseles complejos en un solo corte
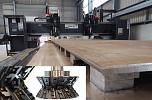
El software guía a los soldadores a través de instrucciones de trabajo
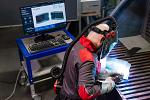
- Industry Events
Pipe and Tube Conference
- May 21 - 22, 2024
- Omaha, NE
World-Class Roll Forming Workshop
- June 5 - 6, 2024
- Louisville, KY
Advanced Laser Application Workshop
- June 25 - 27, 2024
- Novi, MI
Precision Press Brake Certificate Course
- July 31 - August 1, 2024
- Elgin,