Editor-in-Chief
- FMA
- The Fabricator
- FABTECH
- Canadian Metalworking
Categories
- Additive Manufacturing
- Aluminum Welding
- Arc Welding
- Assembly and Joining
- Automation and Robotics
- Bending and Forming
- Consumables
- Cutting and Weld Prep
- Electric Vehicles
- En Español
- Finishing
- Hydroforming
- Laser Cutting
- Laser Welding
- Machining
- Manufacturing Software
- Materials Handling
- Metals/Materials
- Oxyfuel Cutting
- Plasma Cutting
- Power Tools
- Punching and Other Holemaking
- Roll Forming
- Safety
- Sawing
- Shearing
- Shop Management
- Testing and Measuring
- Tube and Pipe Fabrication
- Tube and Pipe Production
- Waterjet Cutting
Industry Directory
Webcasts
Podcasts
FAB 40
Advertise
Subscribe
Account Login
Search
Where is the real value in today’s metal fabricating worker?
Traditional fabricating and welding skills are important, but so are intellectual curiosity and flexibility
- By Dan Davis
- February 22, 2023
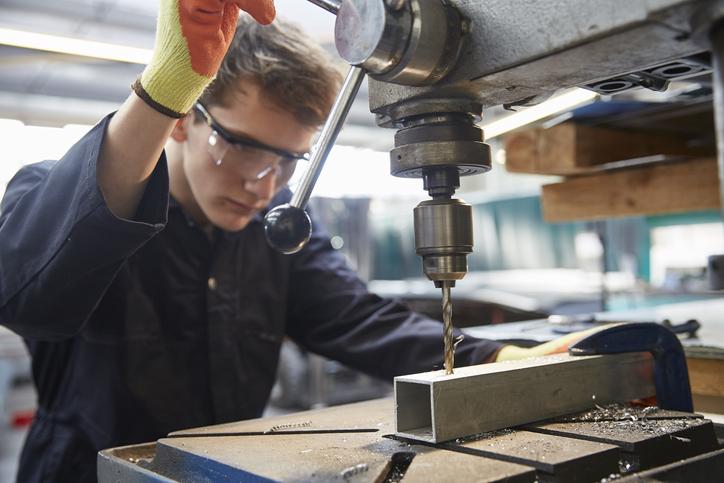
When skilled workers aren’t available, fab shops are going to seek out those with the right soft skills and make the best of it. pablo_rodriguez1/E+
In early February, Josh Welton, a professional welder and a columnist for The FABRICATOR’s sister magazine The WELDER, responded to a Twitter post that claimed working at a fast food restaurant, in this case McDonald’s, was skilled labor. He said, “Tossing around words that have meaning in this context deludes the meaning of those words. You can say they deserve living wages without lumping them in with people who are actual skilled laborers.”
Welton is a very proud, talented welder. He’s also a champion of his trade and defender of what it means to be “skilled” labor. (There’s a reason that he refers to himself as a “weldor” in his own writing outside of our publications and not a “welder.” “A welder is a machine,” he once told our copyeditor, who is skilled in her own right and elected to follow our own internal style.)
As I was reading this social media post, I had just finished wrapping up a story on what metal fabricators need to consider if they are looking to add powder coating capabilities, and I was thinking about a visit I made to an Ohio job shop more than a decade ago. One of the reasons I was there was to chat about the company’s large powder coating operation.
The president of the company was frank when it came to describing those that worked on the finishing line. He basically was looking for warm bodies to hang metal parts and remove finished parts from the racks that moved around on the conveyor. If those folks showed up on time on a regular basis, they could move on to a powder coating application position.
The president didn’t expect much from these new hires. The company also didn’t get much in terms of interested parties. I’m confident that scenario has only grown more dire in recent years.
That memory made me think of what I’ve been hearing other fabricating company owners and managers say to me over the past couple of years. While they are desperate for workers, they aren’t just looking for warm bodies. They are looking for the right fit, not necessarily the right skills. These fab shops need engaged employees who are aware of quality efforts and production schedules and who can adapt to ensure that parts that meet customer specifications are delivered on time. Because in many instances these companies are operating with a barebones crew, they need employees to interact with each other and communicate about potential issues to avoid major rework and possible downtime. Button pushers who kept to themselves for shifts at a time and who enjoyed long-term manufacturing careers 25 years ago need not apply for today’s manufacturing openings.
Let’s go back to powder coating as an example. Rich Saddler of Industrial Finishing Solutions, the subject matter expert quoted in the powder coating article mentioned earlier, described the need for metal fabricators to have finishing experts on staff if powder coating is to be brought in-house. These types of experts are hard to find, so developing one is the next logical choice of action. The only way this can occur is if an individual is curious enough to learn all the aspects of process. That’s part cleaning chemicals, the tanks or spray booths in which those chemicals are applied, powder application equipment and booths, curing ovens, conveyors, and any automation that might be a part of the system. There’s a lot going on, and a lot to learn. That’s why it’s important to have someone with an idea of what might be happening should a problem arise, because if the powder coating line is shut down, the shop has a major bottleneck on its hands.
That powder coating expert then has to be able to inform and educate others involved in the process. A company’s future is put at risk if others aren’t in a position to step forward and replace current leaders if something were to happen. A company can’t move forward if there is no one to lead.
Intellectual curiosity, a capacity to learn, leadership, adaptability, and the ability to communicate—all are necessary for modern metal fabricating operations. More metal fabricating companies are looking for people with these soft skills. It’s a bonus if they can find someone with hard skills as well.
Being a skilled worker still means a great deal, and welders should take pride in their ability to do what others simply can’t, especially if years have been spent at school, on the job, and on weekends perfecting that skill. But the reality is that a different set of skills can get you on a manufacturing career path, where the chance to develop some welding and fabricating skills possibly awaits.
Job descriptions and occupational modifiers can be debated. The opportunities in the manufacturing sector cannot. They are real and waiting for interested parties.
subscribe now
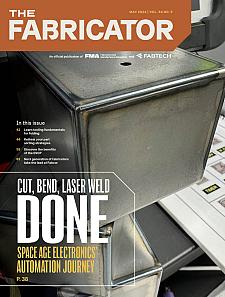
The Fabricator is North America's leading magazine for the metal forming and fabricating industry. The magazine delivers the news, technical articles, and case histories that enable fabricators to do their jobs more efficiently. The Fabricator has served the industry since 1970.
start your free subscriptionAbout the Author
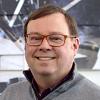
Dan Davis
2135 Point Blvd.
Elgin, IL 60123
815-227-8281
Dan Davis is editor-in-chief of The Fabricator, the industry's most widely circulated metal fabricating magazine, and its sister publications, The Tube & Pipe Journal and The Welder. He has been with the publications since April 2002.
- Stay connected from anywhere
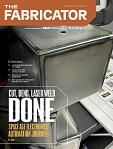
Easily access valuable industry resources now with full access to the digital edition of The Fabricator.
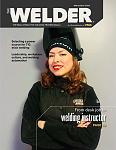
Easily access valuable industry resources now with full access to the digital edition of The Welder.
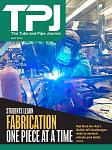
Easily access valuable industry resources now with full access to the digital edition of The Tube and Pipe Journal.
- Podcasting
- Podcast:
- The Fabricator Podcast
- Published:
- 04/16/2024
- Running Time:
- 63:29
In this episode of The Fabricator Podcast, Caleb Chamberlain, co-founder and CEO of OSH Cut, discusses his company’s...
- Trending Articles
Tips for creating sheet metal tubes with perforations
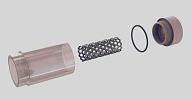
Are two heads better than one in fiber laser cutting?
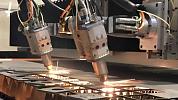
Supporting the metal fabricating industry through FMA
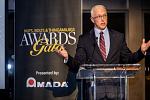
JM Steel triples capacity for solar energy projects at Pennsylvania facility
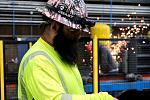
Omco Solar opens second Alabama manufacturing facility
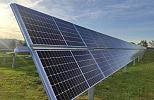
- Industry Events
16th Annual Safety Conference
- April 30 - May 1, 2024
- Elgin,
Pipe and Tube Conference
- May 21 - 22, 2024
- Omaha, NE
World-Class Roll Forming Workshop
- June 5 - 6, 2024
- Louisville, KY
Advanced Laser Application Workshop
- June 25 - 27, 2024
- Novi, MI