Senior Editor
- FMA
- The Fabricator
- FABTECH
- Canadian Metalworking
Categories
- Additive Manufacturing
- Aluminum Welding
- Arc Welding
- Assembly and Joining
- Automation and Robotics
- Bending and Forming
- Consumables
- Cutting and Weld Prep
- Electric Vehicles
- En Español
- Finishing
- Hydroforming
- Laser Cutting
- Laser Welding
- Machining
- Manufacturing Software
- Materials Handling
- Metals/Materials
- Oxyfuel Cutting
- Plasma Cutting
- Power Tools
- Punching and Other Holemaking
- Roll Forming
- Safety
- Sawing
- Shearing
- Shop Management
- Testing and Measuring
- Tube and Pipe Fabrication
- Tube and Pipe Production
- Waterjet Cutting
Industry Directory
Webcasts
Podcasts
FAB 40
Advertise
Subscribe
Account Login
Search
Metal fabrication technology versus the brain drain
The manufacturing sector has an idyllic future, but a messy present
- By Tim Heston
- November 11, 2023
As I walked from the exhibit hall toward the FABTECH Theater, I heard a comment that has stuck with me for weeks. Seeing all the technology at Chicago’s McCormick Place Sept. 11-14, I left FABTECH thinking of what the industry could become. Advances in AI, machine learning, software, robotics, and automation in general seemed to form a bright horizon for a metal fabrication industry benefiting from reshoring trends.
Such technology could attract a new generation who learn differently, who thrive in environments full of software and touchscreens. They’d learn to visualize bending by seeing a simulation on the control in front of them. They’d learn to weld in an environment full of robots and cobots. Surely, I thought, the fab shop of tomorrow will look a world apart from the fab shop today. Then, I heard that comment during one of the show’s panel discussions.
“Let’s face it, outsourcing is a pain. Engineers are just trying to get the right part with a high level of confidence.”
That was Misha Govshteyn, CEO of MacroFab. The Houston-based operation focuses on printed-circuit-board and other electronics-based manufacturing, but his insight made me think of the complex realities of the metal fabrication business.
Considering all the technologies at FABTECH, metal fabrication processes should be more dialed in than ever. From a physical perspective, the only real wildcard left is the quality of sheet metal and plate. Regardless, if material were the only issue, the buyers of fabricated parts and assemblies wouldn’t be thinking that the buying process is so arduous. So, why is outsourcing a pain, particularly in sheet metal fabrication? It might be because shops lack capacity. But again, considering all the technology at FABTECH, why is capacity really an issue?
Potential causes abound: poor procedures, resistance to change, lack of accountability—the usual suspects. Perhaps more worrisome is something anyone in manufacturing has seen coming for years: a severe brain drain. As experts retire, they’re taking their knowledge with them, leaving rookies in the shop without mentors.
Engineers throw designs “over the wall” to an overwhelmed shop floor. With ever-rising demand, operators are forced to just “make it work” and muscle jobs through the shop. Parts get sent to the quality department, and the work they reject gets sent back. Sometimes people know why the part was cut, formed, or welded incorrectly. Other times, people just run the part, and QA personnel reject it again—acting out Einstein’s definition of insanity, doing the same thing repeatedly and expecting different results.
As a reporter, I get to talk with a variety of personalities, from idealistic visionaries to glass-half-empty, don’t-B.S.-me pragmatists. I hear of the potential of AI and machine learning, of building that digital thread through the entire manufacturing process. I imagine a future where no sheet metal, plate, or tubular component is designed without a specific manufacturing process in mind, considering the tooling, material idiosyncrasies, the consumables expended—everything. A designer clicks an online portal, AI and machine learning take over, and the design flows seamlessly to the first manufacturing step, be it in-house or outsourced through a tightly connected network of suppliers.
I also hear about the competition for skilled people, about the struggles of finding employees who actually show up for work and pass a drug test. I hear about the brain drain, about severe disconnects between engineering and the shop floor, about utter lack of organization or controlled manufacturing processes. Recently, someone on The Fabricator staff got a call from a reader desperate for laser cutting advice. He was the welding department supervisor, and now he was also helping out after some unexpected departures. The brain drain is real.
Curiosity also is real, though, and unleashing it can turn a business around. Armed with modern software and machines, polished processes and procedures, along with a progressive culture that holds people accountable, and the messy present can slowly transform into that idyllic future. Put another way, connected machines and software—that digital thread of manufacturing—probably aren’t as effective without people who connect, work well together, and like to learn. Together, they can help make their customers’ outsourcing process less of a pain.
subscribe now
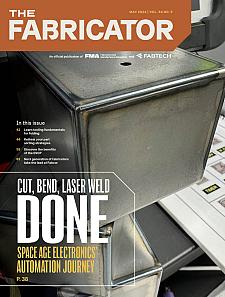
The Fabricator is North America's leading magazine for the metal forming and fabricating industry. The magazine delivers the news, technical articles, and case histories that enable fabricators to do their jobs more efficiently. The Fabricator has served the industry since 1970.
start your free subscriptionAbout the Author
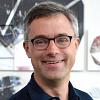
Tim Heston
2135 Point Blvd
Elgin, IL 60123
815-381-1314
Tim Heston, The Fabricator's senior editor, has covered the metal fabrication industry since 1998, starting his career at the American Welding Society's Welding Journal. Since then he has covered the full range of metal fabrication processes, from stamping, bending, and cutting to grinding and polishing. He joined The Fabricator's staff in October 2007.
Related Companies
- Stay connected from anywhere
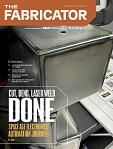
Easily access valuable industry resources now with full access to the digital edition of The Fabricator.
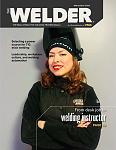
Easily access valuable industry resources now with full access to the digital edition of The Welder.
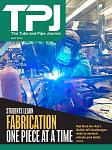
Easily access valuable industry resources now with full access to the digital edition of The Tube and Pipe Journal.
- Podcasting
- Podcast:
- The Fabricator Podcast
- Published:
- 04/16/2024
- Running Time:
- 63:29
In this episode of The Fabricator Podcast, Caleb Chamberlain, co-founder and CEO of OSH Cut, discusses his company’s...
- Trending Articles
Tips for creating sheet metal tubes with perforations
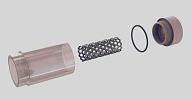
JM Steel triples capacity for solar energy projects at Pennsylvania facility
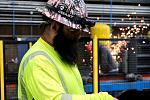
Are two heads better than one in fiber laser cutting?
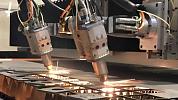
Supporting the metal fabricating industry through FMA
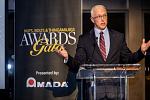
Omco Solar opens second Alabama manufacturing facility
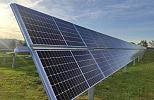
- Industry Events
16th Annual Safety Conference
- April 30 - May 1, 2024
- Elgin,
Pipe and Tube Conference
- May 21 - 22, 2024
- Omaha, NE
World-Class Roll Forming Workshop
- June 5 - 6, 2024
- Louisville, KY
Advanced Laser Application Workshop
- June 25 - 27, 2024
- Novi, MI