Contributing editor
- FMA
- The Fabricator
- FABTECH
- Canadian Metalworking
Categories
- Additive Manufacturing
- Aluminum Welding
- Arc Welding
- Assembly and Joining
- Automation and Robotics
- Bending and Forming
- Consumables
- Cutting and Weld Prep
- Electric Vehicles
- En Español
- Finishing
- Hydroforming
- Laser Cutting
- Laser Welding
- Machining
- Manufacturing Software
- Materials Handling
- Metals/Materials
- Oxyfuel Cutting
- Plasma Cutting
- Power Tools
- Punching and Other Holemaking
- Roll Forming
- Safety
- Sawing
- Shearing
- Shop Management
- Testing and Measuring
- Tube and Pipe Fabrication
- Tube and Pipe Production
- Waterjet Cutting
Industry Directory
Webcasts
Podcasts
FAB 40
Advertise
Subscribe
Account Login
Search
Stampers, automakers doing their part to stamp out COVID-19
Manufacturers, large and small, shape-shift to fulfill urgent needs quickly during pandemic
- By Kate Bachman
- April 30, 2020
Alexander Pope wrote, “Fools rush in where angels fear to tread.” Automakers and stamping industry companies have rushed to the rescue of healthcare workers and patients desperate for respirators, beds, transport vehicles, protective masks, and other equipment and supplies to combat the COVID-19 pandemic. They have transformed their plants and operations within just a couple of months, and in some cases in a matter of weeks, even days, to help fulfill shortages and supply medical needs.
Many have been surprised at the neck-breaking speed at which the agile manufacturers have transitioned their production lines from standard operations to specialized ones.
This readiness comes as a surprise to no one in this industry, though. After all, manufacturers have been leaning, hastening, transforming, and MacGyvering since surviving the 2001 recession, the 2008 recession, and many iterations thereof, developing a nimbleness and responsiveness unheard of in decades past.
Here are some of the initiatives that stampers, automakers, and companies with stamping capacity are undertaking that are making a sizable dent in the COVID-19 crisis.
Automakers, OEMs to the Rescue
Automakers, already expert at speedy, high-volume production, have overhauled their plants to mass-produce desperately needed medical support equipment and devices, as blogger Josh Welton wrote about previously.
Ford is producing respirators, masks, gowns, and testing collection kits. The automaker is expanding its efforts to design and produce urgently needed medical equipment and supplies for health care workers, first responders, and patients fighting the coronavirus. To accelerate production, in some cases they’re using off-the-shelf parts like blower motors used in the F150’s ventilated seats and battery packs from power tools to make a new powered air-purifying respirator (PAPR), with design and testing consultation from 3M. They plan to make more than 100,000.
In addition, Ford is manufacturing reusable gowns from airbag materials with supplier Joyson Safety Systems and helping Thermo Fisher Scientific expand production of COVID-19 collection kits for patient testing quickly.
General Motors, in its “vehicles to ventilators” program, is working with partners to source and manufacture ventilators at scale. “We are leveraging the skill and efficiency of 1,000 American workers to scale production of critical care ventilators immediately,” a spokesperson said.
The automaker has repurposed its electronics components plant with the help of the UAW to produce Ventec-brand ventilators. GM was given a $490 million government contract to make the life-saving machines through the Defense Production Act.
Ford is manufacturing medical equipment and supplies, repurposing some components originally designed for vehicles to accelerate production.
The complex ventilators required the sourcing of hundreds of parts, which the company accomplished in just over a week. It is mass producing the Ventec Life Systems V+Pro critical care ventilator at its Kokomo, Ind., facility and delivered the first of its first ventilator machines to Chicago-area hospitals ahead of schedule. It has shipped more than 600 ventilators to date and projects that half of the 30,000-unit order will be filled by the end of June. The full order will be completed by the end of August, with the capacity to build more ventilators after August if needed, the company said.
GM says its ventilator production efforts have been helped along thanks to “strong support from the leadership of the United Auto Workers, including the UAW-GM Department and UAW Local 292.
The automaker also began producing up to 100,000 Level 1 surgical masks a day at its Warren, Mich., plant’s ISO Class 8-equivalent clean room. It geared up in less than seven days. It plans to distribute the PPE through government agencies and local suppliers.
Fiat Chrysler Automobiles (FCA) is bringing one of its plants in China online to produce and donate at least 1 million face masks per month for police, EMTs, firefighters, and workers in hospitals and health care clinics, according to the company. FCA facilities in North America may switch production too. The company’s engineering and logistics teams in Italy are lending support to a ventilator manufacturer there, and it’s using that experience to expand assistance to and partnerships with other PPE and equipment manufacturers.
Honda facilities in North America have donated more than 200,000 items to healthcare providers and first responders, including gloves, face shields, N-95 protective masks, alcohol wipes, half-mask respirators and other types of protective gear.
Honda associates are using 3D printers to manufacture parts for face shields being donated to health care facilities and first responders.
In addition, the automaker is outfitting vans to transport virus patients, according to Reuters. The automaker has remodeled 50 of its minivans to transport COVID-19 patients to hospitals and quarantine facilities in Japan, sealing off the rear section of the vehicles with a one-way ventilation system to keep drivers safe from infection.
At least 18 UAW workers at automaker plants in the U.S. have died of COVID-19.
Steelcase has been making masks, shields, and barriers used for screening patients at local hospitals and is making its patterns and instructions for masks and shields available publicly.
Philips plans to double the production of its hospital ventilators by May and achieve a fourfold increase by the third quarter of 2020. This plan builds on Philips’ initial production increase in the first three months of the year to supply additional ventilators––to hospitals in the most affected regions in the U.S., China, and southern Europe. Philips introduced its new Philips Respironics E30 ventilator, a versatile, noninvasive and invasive ventilator, which has been designed for large-scale production, the company announced.
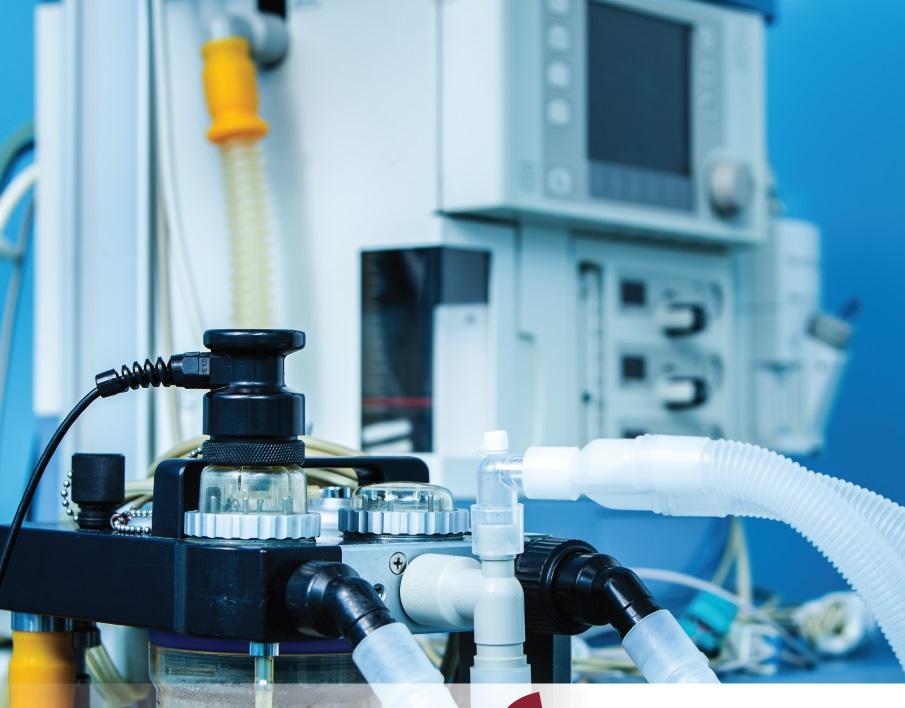
Bunting-DuBois is manufacturing custom magnets and magnetic assemblies that are part of critical medical devices, including ventilators, water filtration systems, and virus testing equipment.
Behind the Curtain: Other COVID-19-fighting Supporters
Stampers and manufacturers with stamping capacity have contributed to the effort in other ways not as apparent as ventilators and masks.
Greenheck Fan Corp. has surged its delivery of fans for hospitals—both permanent buildings and the temporary ones being set up in arenas. The company has pumped up its production of circulating fans for data centers too. The centers have experienced usage spikes as more in the workforce are working from home offices.
Jagemann is making aluminum nose bridges for medical face masks and has outfitted its plastics plant in Murfreesboro, Tenn., to make disposable face shields. “We are pleased to be able to continue employing our staff while assisting in the fight against coronavirus helping keep the country’s health care workers safe and protected,” said Nathan Dudney, director of sales and business development. The company had open orders for more than 350,000 face shields and has committed to produce more than 1 million in the next 60 days.
Industrial Magnetics has invented and manufactured hands-free door openers to eliminate contagion transfer. The manufacturer’s Foot-Pull Door Opener, attached to the bottom of a door, allows users to pull open doors using the sole of their shoe, eliminating the need to touch potentially contaminated door surfaces and helping to stop the further spread of germs and bacteria. The company is donating profits earned from the sale of these items to local food pantries.
Scandic also invested and manufactured hands-free door-opening devices free for its employees, friends, and family and is open-sourcing the designs to others interested. As a bonus, the device doubles as a beer bottle opener, CEO Hale Foote said.
Pioneer is producing a new type of hospital bed system that makes it easier for hospital personnel to move beds when transporting patients from one location to another.
Bunting-DuBois is manufacturing custom magnets and magnetic assemblies that are part of critical medical devices, including ventilators, water filtration systems, and virus testing equipment.
The magnets are used in rotors for blower motors that are a key part of a ventilator’s construction. These blower motors create the air that helps people breathe and are key to the survival of patients battling COVID-19, the company said.
The company notes that its products are completely made in the U.S. and the supply chain does not rely on China.
Monaghan Tooling received a request for custom burnishing tool to produce a microfinish on a flat surface of a ventilator component-and then processed the proposal, engineered the drawings, and manufactured the custom tooling in 5 hours and 15 minutes. “As soon as we heard ‘ventilator,’ we made this our No. 1 priority,” said President Scott Monaghan.
Magna is manufacturing 75,000 face shields to donate for use by first responders.
Flexibility in Wartime, Trade Shortages
There has long been speculation about the U.S.’s manufacturing capacity and ability to quickly defend itself if a war suddenly broke out. The manufacturing industry’s nimble responsiveness to the needs posed by COVID-19 should put those questions to rest.
Another aspect to that speculation has been that some OEMs have claimed that they cannot find U.S. manufacturers that can make certain components for them, pushing them to source offshore. That includes the U.S. military and its contract suppliers.
The apparent ability of stampers and manufacturers to shape-shift and to transform their operations in a matter of a couple of weeks or months to make products so completely different than their usual product lines should upend that line of reasoning.
subscribe now
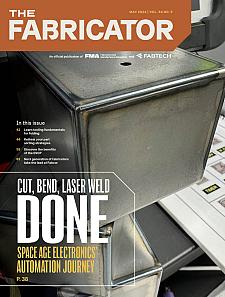
The Fabricator is North America's leading magazine for the metal forming and fabricating industry. The magazine delivers the news, technical articles, and case histories that enable fabricators to do their jobs more efficiently. The Fabricator has served the industry since 1970.
start your free subscriptionAbout the Author
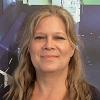
Kate Bachman
815-381-1302
Kate Bachman is a contributing editor for The FABRICATOR editor. Bachman has more than 20 years of experience as a writer and editor in the manufacturing and other industries.
- Stay connected from anywhere
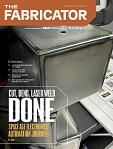
Easily access valuable industry resources now with full access to the digital edition of The Fabricator.
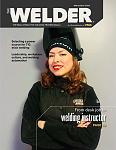
Easily access valuable industry resources now with full access to the digital edition of The Welder.
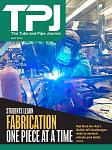
Easily access valuable industry resources now with full access to the digital edition of The Tube and Pipe Journal.
- Podcasting
- Podcast:
- The Fabricator Podcast
- Published:
- 04/30/2024
- Running Time:
- 53:00
Seth Feldman of Iowa-based Wertzbaugher Services joins The Fabricator Podcast to offer his take as a Gen Zer...
- Industry Events
Pipe and Tube Conference
- May 21 - 22, 2024
- Omaha, NE
World-Class Roll Forming Workshop
- June 5 - 6, 2024
- Louisville, KY
Advanced Laser Application Workshop
- June 25 - 27, 2024
- Novi, MI
Precision Press Brake Certificate Course
- July 31 - August 1, 2024
- Elgin,