Senior Editor
- FMA
- The Fabricator
- FABTECH
- Canadian Metalworking
Categories
- Additive Manufacturing
- Aluminum Welding
- Arc Welding
- Assembly and Joining
- Automation and Robotics
- Bending and Forming
- Consumables
- Cutting and Weld Prep
- Electric Vehicles
- En Español
- Finishing
- Hydroforming
- Laser Cutting
- Laser Welding
- Machining
- Manufacturing Software
- Materials Handling
- Metals/Materials
- Oxyfuel Cutting
- Plasma Cutting
- Power Tools
- Punching and Other Holemaking
- Roll Forming
- Safety
- Sawing
- Shearing
- Shop Management
- Testing and Measuring
- Tube and Pipe Fabrication
- Tube and Pipe Production
- Waterjet Cutting
Industry Directory
Webcasts
Podcasts
FAB 40
Advertise
Subscribe
Account Login
Search
FABTECH 2015: The direct-diode laser and tuning the beam profile
- By Tim Heston
- November 23, 2015
Perhaps no technology at FABTECH® has changed more during the past decade than the laser cutting machine. In 2005, CO2 laser cutting systems dominated the halls. In 2010, solid-state fiber and disk lasers started to gain a presence. Today the high-powered solid-state cutting laser rules the show.
At this year’s show, another type of solid-state cutting laser stepped into the ring. It’s called the direct-diode laser. One machine maker, Elgin, Ill.-based Mazak Optonics, had on display a direct-diode tube laser, dubbed the Versatile Compact Laser, or VCL. In welding, Panasonic Welding Systems demonstrated its robotic welding system using a direct-diode laser.
As the name suggests, direct-diode lasers use energy emitted from diodes directly, not pumped through another medium. Traditionally, it’s been difficult to attain the required beam quality at the high powers required for conventional sheet metal cutting. Individually, diode lasers are very low power, so they need to be combined somehow. The problem has been that when you combine these diode lasers, the beam quality suffers.
Today the story is different. Wilmington, Mass.-based TeraDiode uses what it calls “wavelength beam combining.” Basically, the company combines takes diode bars that emit light of slightly different wavelengths, then combines them by sending them through a diffraction grating. These diode bars are produced in 1-kW modules, or “blades.” Once combined in such a way, these different wavelengths produce one beam with a particular beam parameter product, or BPP, tailored for the application. At the show the company showed lasers with up to 8 kW of power.
Like CO2 lasers, direct-diode lasers are what’s known as a “free space” laser, meaning that the beam is sent through a cavity, then to the output fiber. This allows the energy profile of the direct diode laser beam to be shaped, similar to how the CO2 laser beam has been shaped for decades.
Bryce Samson, director of business development at TeraDiode, put it this way: “We’re dealing with free-space beams. This is like CO2 gas lasers, in which [beam energy profile manipulation] has been around for decades. It gives you freedom to manipulate the beam. After we generate the mode, we send [the direct-diode laser beam] to the delivery fiber and then to the cutting head.”
This in turn allows the BPP to be “tuned” to a particular workpiece, from a near-pure Gaussian mode (high energy in the middle) for thin stock to a donut mode (high energy around the beam edges) for thick stock, and anything in between.
According to Samson, this, combined with the laser’s absorption characteristics, aids cut quality in a variety of metals.
Today TeraDiode’s laser for sheet metal cutting has a wavelength of 970 nanometers, close to the 1-micron wavelength of today’s fiber and disk lasers. Samson added, though, that the company’s direct-diode laser can be made to any number of different wavelengths. In some applications, the direct diode laser wavelengths have been adapted to meet the absorption characteristics of the material at hand.
Today solid-state cutting lasers in general have been tested on both thin and thick material. Beam-altering technology has been available in fiber and disk laser machines for several years now. Through cutting heads and other technology, solid-state laser cutting advancements in metal fabrication have been truly extraordinary. And a new solid-state laser cutting technology in the market offers another choice for fabricators.
subscribe now
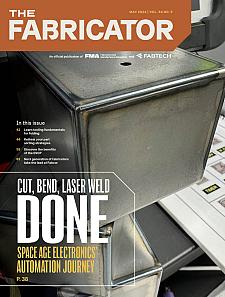
The Fabricator is North America's leading magazine for the metal forming and fabricating industry. The magazine delivers the news, technical articles, and case histories that enable fabricators to do their jobs more efficiently. The Fabricator has served the industry since 1970.
start your free subscriptionAbout the Author
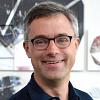
Tim Heston
2135 Point Blvd
Elgin, IL 60123
815-381-1314
Tim Heston, The Fabricator's senior editor, has covered the metal fabrication industry since 1998, starting his career at the American Welding Society's Welding Journal. Since then he has covered the full range of metal fabrication processes, from stamping, bending, and cutting to grinding and polishing. He joined The Fabricator's staff in October 2007.
Related Companies
- Stay connected from anywhere
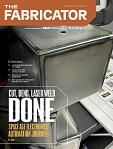
Easily access valuable industry resources now with full access to the digital edition of The Fabricator.
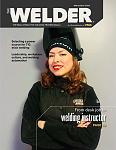
Easily access valuable industry resources now with full access to the digital edition of The Welder.
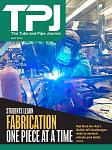
Easily access valuable industry resources now with full access to the digital edition of The Tube and Pipe Journal.
- Podcasting
- Podcast:
- The Fabricator Podcast
- Published:
- 04/16/2024
- Running Time:
- 63:29
In this episode of The Fabricator Podcast, Caleb Chamberlain, co-founder and CEO of OSH Cut, discusses his company’s...
- Trending Articles
Tips for creating sheet metal tubes with perforations
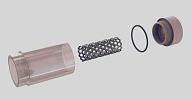
Are two heads better than one in fiber laser cutting?
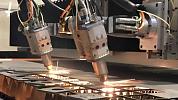
Supporting the metal fabricating industry through FMA
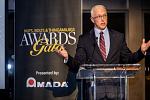
JM Steel triples capacity for solar energy projects at Pennsylvania facility
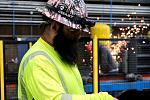
Omco Solar opens second Alabama manufacturing facility
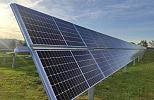
- Industry Events
16th Annual Safety Conference
- April 30 - May 1, 2024
- Elgin,
Pipe and Tube Conference
- May 21 - 22, 2024
- Omaha, NE
World-Class Roll Forming Workshop
- June 5 - 6, 2024
- Louisville, KY
Advanced Laser Application Workshop
- June 25 - 27, 2024
- Novi, MI