Owner, Brown Dog Welding
- FMA
- The Fabricator
- FABTECH
- Canadian Metalworking
Categories
- Additive Manufacturing
- Aluminum Welding
- Arc Welding
- Assembly and Joining
- Automation and Robotics
- Bending and Forming
- Consumables
- Cutting and Weld Prep
- Electric Vehicles
- En Español
- Finishing
- Hydroforming
- Laser Cutting
- Laser Welding
- Machining
- Manufacturing Software
- Materials Handling
- Metals/Materials
- Oxyfuel Cutting
- Plasma Cutting
- Power Tools
- Punching and Other Holemaking
- Roll Forming
- Safety
- Sawing
- Shearing
- Shop Management
- Testing and Measuring
- Tube and Pipe Fabrication
- Tube and Pipe Production
- Waterjet Cutting
Industry Directory
Webcasts
Podcasts
FAB 40
Advertise
Subscribe
Account Login
Search
How spiral-welded wind turbine towers are changing the energy industry
- By Josh Welton
- October 7, 2023
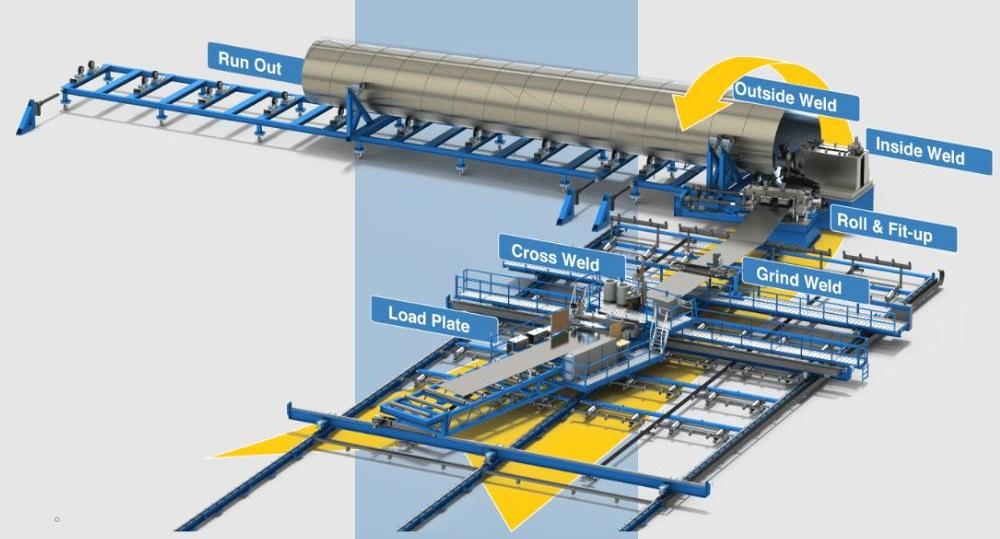
A spiral welding process is making its way into the wind energy industry and changing the way we manufacture large-scale pipe. Keystone Tower Systems
We’ve all seen them. Rolling down the highway, chillin’ at a rest stop, or driving down a small-town road. In the distant fields, they spring up, towering above farmland. At night they blink like a runway, flashing their location to incoming pilots. They are wind turbines.
Any transition towards using fewer fossil fuels will be a joint undertaking, with multiple alternative energy sources— hydrogen, nuclear, solar, hydropower, and wind—filling the void.
I found a few blurbs about how a tried-and-true pipe manufacturing process—spiral-welded pipe—is making its way into the wind energy industry. Due to its versatility and mobility, it might change the game. Here is the mission statement from Keystone Tower Systems:
“To drive down the cost of wind energy by developing the advanced tower design and manufacturing technology needed to reach stronger winds at lower costs.”
There are a couple of things at play here. We’ve likely all seen the towers and turbines, piece by piece, strapped to the back of wide-load trucks, traveling along our highways. To move like that, they can only be so big before bridges and tunnels and other lanes make them too big to pass through. That mission statement’s last notion, “to reach stronger winds at lower costs,” is the kicker. Those “stronger winds” are located higher than current towers can reach. To reach stronger, more powerful winds that increase the output and efficiency of a turbine, you need to build taller towers. Taller towers need to be wider at the base to support their now more highly stressed top portion.
By utilizing spiral-welded pipe built on-site, you not only avoid the cost of shipping giant components, but you can also make those giant components more giant-er. Now you can build that massive, taller tower base to push the modern windmill to never-before-seen altitudes.
This spiral-welded pipe is a long sheet of metal fed into a tubular conveyor system. As the flat metal curves into a spiral, a dual-headed submerged arc welding setup welds from inside and outside of the endless spiral. The process is convenient because so much is automated and relatively easy to set up on location or even right on the water where an offshore tower is going up. All the edge prep and inspection take place right there.
Anyways, here’s the article that caught my eye on the topic—you’ll want to jump down the rabbit hole.
subscribe now
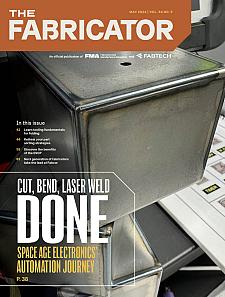
The Fabricator is North America's leading magazine for the metal forming and fabricating industry. The magazine delivers the news, technical articles, and case histories that enable fabricators to do their jobs more efficiently. The Fabricator has served the industry since 1970.
start your free subscriptionAbout the Author
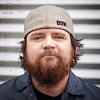
- Stay connected from anywhere
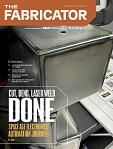
Easily access valuable industry resources now with full access to the digital edition of The Fabricator.
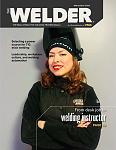
Easily access valuable industry resources now with full access to the digital edition of The Welder.
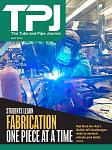
Easily access valuable industry resources now with full access to the digital edition of The Tube and Pipe Journal.
- Podcasting
- Podcast:
- The Fabricator Podcast
- Published:
- 04/16/2024
- Running Time:
- 63:29
In this episode of The Fabricator Podcast, Caleb Chamberlain, co-founder and CEO of OSH Cut, discusses his company’s...
- Trending Articles
Tips for creating sheet metal tubes with perforations
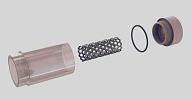
Are two heads better than one in fiber laser cutting?
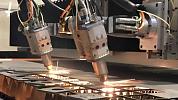
Supporting the metal fabricating industry through FMA
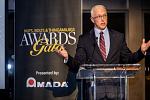
JM Steel triples capacity for solar energy projects at Pennsylvania facility
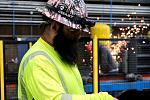
Omco Solar opens second Alabama manufacturing facility
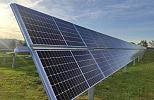
- Industry Events
16th Annual Safety Conference
- April 30 - May 1, 2024
- Elgin,
Pipe and Tube Conference
- May 21 - 22, 2024
- Omaha, NE
World-Class Roll Forming Workshop
- June 5 - 6, 2024
- Louisville, KY
Advanced Laser Application Workshop
- June 25 - 27, 2024
- Novi, MI