Senior Editor
- FMA
- The Fabricator
- FABTECH
- Canadian Metalworking
Categories
- Additive Manufacturing
- Aluminum Welding
- Arc Welding
- Assembly and Joining
- Automation and Robotics
- Bending and Forming
- Consumables
- Cutting and Weld Prep
- Electric Vehicles
- En Español
- Finishing
- Hydroforming
- Laser Cutting
- Laser Welding
- Machining
- Manufacturing Software
- Materials Handling
- Metals/Materials
- Oxyfuel Cutting
- Plasma Cutting
- Power Tools
- Punching and Other Holemaking
- Roll Forming
- Safety
- Sawing
- Shearing
- Shop Management
- Testing and Measuring
- Tube and Pipe Fabrication
- Tube and Pipe Production
- Waterjet Cutting
Industry Directory
Webcasts
Podcasts
FAB 40
Advertise
Subscribe
Account Login
Search
What FABTECH 2023 revealed about the future of metal fabrication
Automation, robotic, and AI technology are becoming a workforce multiplier
- By Tim Heston
- October 30, 2023
- Article
- Shop Management
When robotics entrepreneur Carol Reiley presented on the main stage at this year’s FABTECH, she showed a video demonstrating how robots performed tele-surgery, with autonomous robots replicating the expertise of an expert surgeon many miles or even several continents away.
At first glance, the technology seemed far away from metal fabrication. But in the adjacent hall in Chicago’s McCormick Place, in the far front corner, EWI showcased tele-welding technology, allowing expert welders to control and teach robotics from a remote location. EWI’s and Reiley’s work were developed separately, but the presence of both at FABTECH hinted at where technology is heading.
“Can we use autonomous manufacturing as a workforce multiplier?”
That was Arnold Kravitz, chief technology officer of the BlueForge Alliance, during a press conference. The organization advocates for the submarine and defense industrial base that, like everywhere else, has a great need for skilled workers. Kravitz himself walked the show in search of technology that could get more out of the available talent and effectively attract, train, and retain the next generation.
“In addition to winning the war for talent, we’re asking, ‘How do we work with the talent we have, and how do we make the best use of that talent?’ Using new technology, how do we create that hyperenabled worker?”
That’s a difficult question, but FABTECH 2023 had plenty of potential answers, most of which focused on the industry’s digital evolution. As more tasks become tracked and measured, the more technology can streamline and optimize those tasks. The result has become a dynamic industry, with skilled talent freed from the mundane, free to question the status quo, and free to push the envelope and discover what’s possible.
The Importance of Partnership
More than 40,000 people attended the show between Sept. 11 and 14, a 40% increase from the last Chicago FABTECH two years ago. And most didn’t just visit for a few hours to kick some tires. Historically, attendees spend about a day and a half walking the exhibit halls. According to Mark Hoper, senior vice president of expositions and media at the Fabricators and Manufacturers Association, a FABTECH event partner, “This year, more attendees returned to the show for two or three days,” adding that many exhibitors were calling it the best FABTECH in recent memory.
Such attendance trends could point to the ever-tighter partnerships between industry stakeholders. This includes not only machine vendors, material suppliers, and their custom fabricator and OEM customers, but also various service providers, such as ones that promote new ways to invest in technology.
This includes the so-called “automation as a service” model. Fabricators don’t purchase equipment outright but instead are charged an hourly rate to use it. This arrangement might sound like a glorified lease, but as Misa Ilkhechi, co-founder and vice president of sales at Formic, an automation as a service provider, explained, his company’s approach has a few distinctions.The most obvious is that Formic covers all maintenance for the cell and guarantees uptime.
“With a lease, you don’t get guaranteed uptime or throughput, and you don’t get service or ongoing maintenance.” He added that Formic does go through a risk mitigation process, validating the manufacturing process and ensuring the equipment will run a certain amount of time during certain periods. But as long as some basics of the service agreement are met, the fabricator pays only for the time an automated system is running.
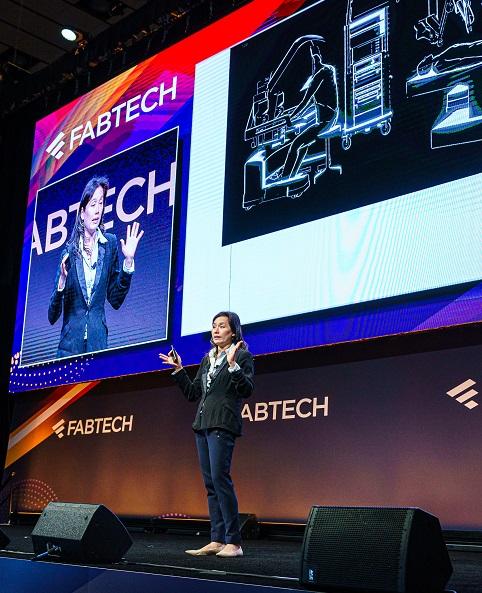
Robotics entrepreneur Carol Reiley presented her work on the FABTECH main stage, including innovations in tele-surgery—work that could be a harbinger in the metal fabrication arena. Butler Photography
Automation and AI
Manufacturing technology providers are working together like never before. Cobot players like Universal Robots build a platform for others to experiment with and optimize—a strategy that’s clearly working, considering the sheer number of cobots at the show.
FABTECH saw innovations in cobot reach as well as an element that’s been long missing from the platform: a positioner moving in concert with the welding cobot. UR showcased such technology, and it’s highly likely such capability will become more widespread in the coming years. The positioner and cobot “are handshaking and exchanging information in real time to stay in sync,” said Travis Langford, channel development manager at UR.
Most automation at the show was touted to be easily programmable. A few even automate the task of programming entirely, including a platform offered by Abagy. One cell set up by Path Robotics showcased automated programming, welding, and even weld tacking, using a combination of sensors and vision technology.
“These robots have the capability to feel.” So said Andrew Lien, lead hardware engineer at Path, describing a cell featuring three UR cobots working in concert. “We’re calling this ‘autonomous fit-up.’”
Given only the CAD model of the assembly, two cobots retrieved parts from a bin and placed them on a fixture table. Another cobot tacked the assembly, after which it’s brought to a weld fixture for final welding. The whole cell required no manual intervention.
“The software algorithms and our AI neural networks are designed to deal with variability,” Lien said, adding that artificial intelligence has allowed Path to push the limits of bin-picking as well as dealing with variation overall, be it from upstream cutting, forming, or anything else.
Overall, this year’s FABTECH showed the increasing importance of software, not to mention the eyebrow-raising potential of AI. “When ChatGPT really caught fire and everyone started using it last year, ever wonder why?”
Ben Wald, founder of Very, a company focusing on the Industrial Internet of Things (IIoT), asked the question during a presentation on the show’s main stage. Different iterations of ChatGPT have utilized a certain number of parameters, AI’s rough equivalent to neurons in the human brain. The first version of ChatGPT had just about 100 million parameters; the version that caught everyone’s attention happened to have 175 billion. The human brain has about 100 billion neurons.
“ChatGPT 4.0 has 175 trillion synaptic connections, or parameters,” Wald said. “We’re seeing exponential growth. It’s hard to imagine what these systems are going to be capable of so quickly.”
Such rapid innovation can be difficult to fathom, but it’s one reason so many are predicting a very different future. AI has been most visible in large language models, and it has yet to spread widely in the metal fabrication arena. But considering just how quickly AI is evolving, its widespread use in fabrication might be coming sooner than many expect.
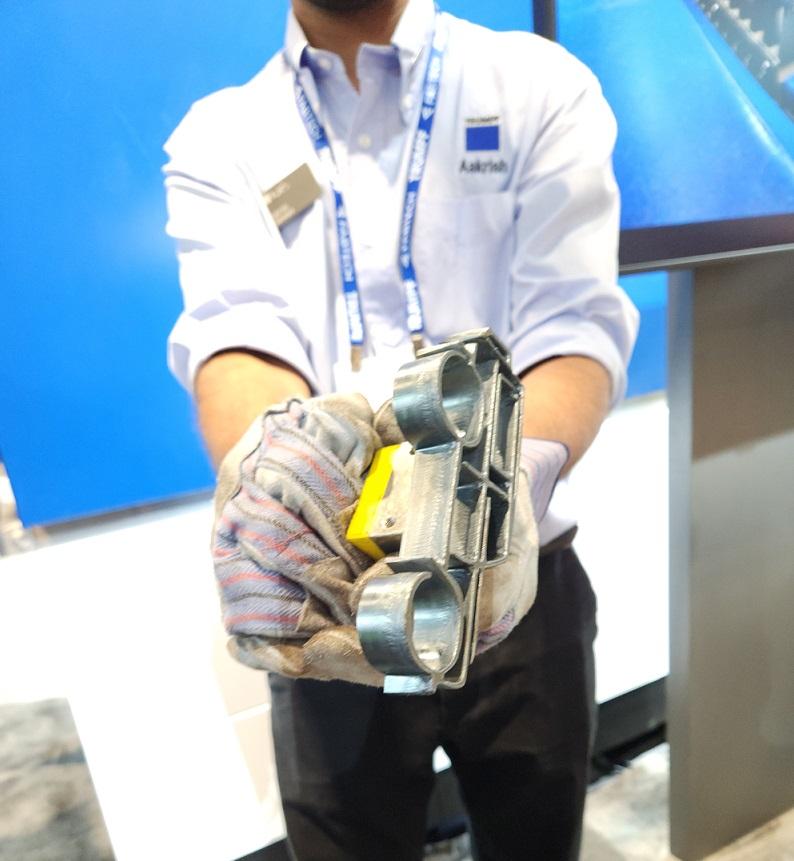
During a TRUMPF press conference, a technician showed a dross-free workpiece—a challenging, thin-walled geometry—cut moments earlier from heavy plate and lifted easily from the bed of a 24-kW laser.
The Potential of Precision Plate Cutting
During a press conference at the show, TRUMPF showcased its 24-kW laser’s capability to oxygen-cut cleanly through thick, surface-blasted plate. “Materials that are bead-blasted are typically difficult to process with a standard oxygen cutting process,” explained James Gamache, laser sales engineer, describing the company’s technology that makes use of a high focus position and new nozzle technology that balances assist gas utilization with the need to create optimal flow through a thick kerf—leaving no deep striations or hard-to-remove dross.
Years ago, the fiber laser was seen mainly as a thin-sheet-cutting technology. This year’s show demonstrates just how much that has changed. Numerous machine vendors showcased their laser’s capability to cut cleanly through thick plate. The idea is to eliminate the need for secondary operations. Combine the fiber laser’s immense power density and ability to cut cleanly so quickly, and the business viability of precision plate cutting begins to make sense.
Driving a lot of this has been innovations in power distribution across the beam diameter, as well as in assist gas mixing and delivery. David Bell, president of Witt Gas Controls, pointed to a system that regulates the delivery of oxygen-nitrogen assist gas mixes. It evenly distributes mixes of oxygen (usually between 1% and 5%) within the column of nitrogen gas flow.
Even distribution occurs thanks to the unique way the system draws gas from the cylinder. To be most effective, oxygen needs to be well dispersed within the nitrogen gas flow—a flow that, with increasing laser powers, has become ever more critical for cutting plate cleanly, with no deburring or other secondary processes required.
“The evolution is happening quickly,” Bell said. “A year ago, a 10-kW fiber laser was considered a lot of laser cutting power. Now, we’re seeing 24-kW lasers and even more.”
Keeping the Flow
How much laser cutting power does a fabricator really need? That of course depends on the range of grades and thicknesses a fabricator processes. The last thing a fabricator needs is an ultrahigh-power fiber laser sitting idle most of the time simply because people can’t remove parts fast enough. Hence the value of part removal automation in blanking—and the show had plenty on display, both Cartesian and articulating-arm robotic systems.
A highly powerful laser might have offloading automation, but what then? Who transports those parts downstream, and how long do parts wait until those material handlers or fork truck drivers are available? Some have delved into automated guided vehicles (AGVs) of one kind or another, but at this year’s FABTECH, the industry got a taste of what the autonomous mobile robot (AMR) could do for part flow on the shop floor.
During a press conference, Jason Hillenbrand, executive general manager at AMADA AMERICA, pointed to part removal automation stacking blanks onto an AMR that the company calls the AMTES, or Autonomous Mobile Transport Engineering System.
“The AMTES will take this material to wherever it needs to go,” Hillenbrand said. “In our setup here, it’s taking parts to a bending robot, but it can go anywhere. It could go to painting, welding, another press brake, or a buffer area near assembly.” He added the AMR system communicates continually with other machines and systems on the floor, to ensure it arrives at the right place at the right time and moves the correct parts to where they need to go.
A New Way to Grow
“In January, we were ready to have our best year ever, and for the first six months, we were pretty close to achieving it. During the past few months, though, we have seen a slowdown. We knew it and we expected it. That said, we’re still on the path toward acquisition. I just had a call about one this morning in fact.”
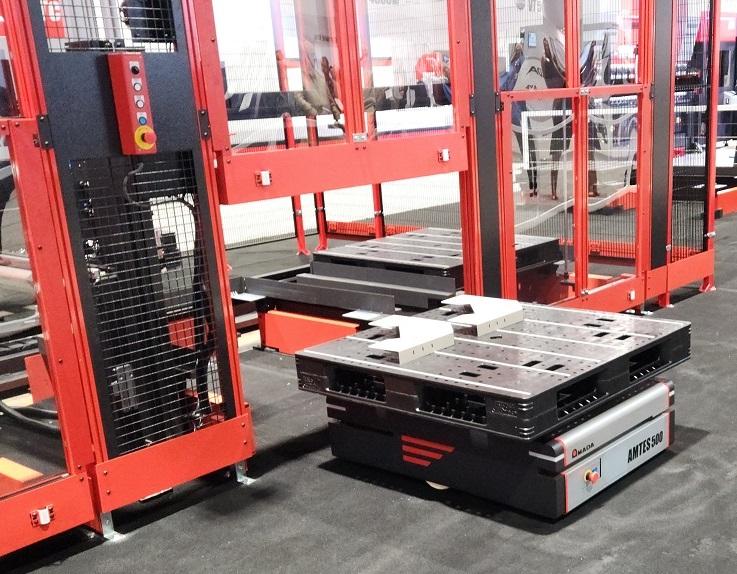
During AMADA’s press conference, company officials showcased an autonomous mobile robot (AMR) concept, dubbed the Autonomous Mobile Transport Engineering System (AMTES). A demonstration cell at the booth showed an AMR transporting parts from cutting to bending and operations downstream.
So said Adam Schmitt, vice president of business development and administration at NIX Companies, a fabricator based in Poseyville, Ind. The shop exhibited at the show under its ProFab Alliance brand, a consulting division that promotes shared best practices among like-minded fabricators.
At the show, Schmitt was on the hunt for a new ERP system and was networking to lay the groundwork for potential expansion opportunities. The fabricator is exploring both traditional acquisitions as well as a franchise model. NIX’s aim is to follow a model like the one used in the fast-food business, where some locations are corporate owned and others are franchises that have certain branding and operate in a standard way.
As Schmitt explained, “Once the transaction takes place, the company would be either a NIX company [in the case of an acquisition] or ‘powered by NIX’ [in the case of a franchise agreement]. The company would still maintain their brand identity.”
Schmitt made those comments near the end of one of the busiest FABTECHs in years. His words exemplify just one of many new perspectives the industry’s progressive leaders have. People are questioning the status quo and taking their own paths toward business success. The industry is undergoing a shift as the next generation takes the helm, full of new ideas and a deep-seated belief about the real difference a fresh approach to the business can make.
The pace of change seems to be accelerating. Add in advancements in AI—with jumps in capability from millions of connections to billions and literally trillions—one can only imagine what the future will bring.
About the Author
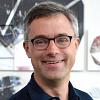
Tim Heston
2135 Point Blvd
Elgin, IL 60123
815-381-1314
Tim Heston, The Fabricator's senior editor, has covered the metal fabrication industry since 1998, starting his career at the American Welding Society's Welding Journal. Since then he has covered the full range of metal fabrication processes, from stamping, bending, and cutting to grinding and polishing. He joined The Fabricator's staff in October 2007.
subscribe now
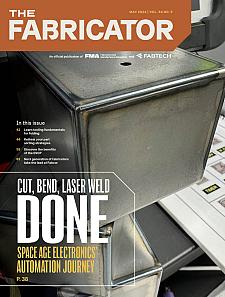
The Fabricator is North America's leading magazine for the metal forming and fabricating industry. The magazine delivers the news, technical articles, and case histories that enable fabricators to do their jobs more efficiently. The Fabricator has served the industry since 1970.
start your free subscription- Stay connected from anywhere
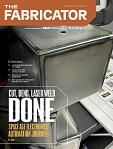
Easily access valuable industry resources now with full access to the digital edition of The Fabricator.
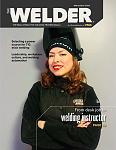
Easily access valuable industry resources now with full access to the digital edition of The Welder.
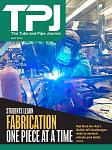
Easily access valuable industry resources now with full access to the digital edition of The Tube and Pipe Journal.
- Podcasting
- Podcast:
- The Fabricator Podcast
- Published:
- 04/16/2024
- Running Time:
- 63:29
In this episode of The Fabricator Podcast, Caleb Chamberlain, co-founder and CEO of OSH Cut, discusses his company’s...
- Trending Articles
Tips for creating sheet metal tubes with perforations
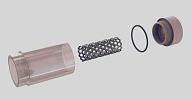
Are two heads better than one in fiber laser cutting?
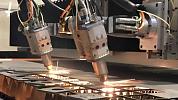
Supporting the metal fabricating industry through FMA
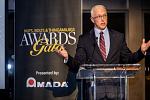
JM Steel triples capacity for solar energy projects at Pennsylvania facility
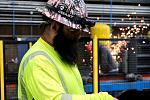
Omco Solar opens second Alabama manufacturing facility
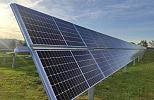
- Industry Events
16th Annual Safety Conference
- April 30 - May 1, 2024
- Elgin,
Pipe and Tube Conference
- May 21 - 22, 2024
- Omaha, NE
World-Class Roll Forming Workshop
- June 5 - 6, 2024
- Louisville, KY
Advanced Laser Application Workshop
- June 25 - 27, 2024
- Novi, MI