Editor-in-Chief
- FMA
- The Fabricator
- FABTECH
- Canadian Metalworking
Categories
- Additive Manufacturing
- Aluminum Welding
- Arc Welding
- Assembly and Joining
- Automation and Robotics
- Bending and Forming
- Consumables
- Cutting and Weld Prep
- Electric Vehicles
- En Español
- Finishing
- Hydroforming
- Laser Cutting
- Laser Welding
- Machining
- Manufacturing Software
- Materials Handling
- Metals/Materials
- Oxyfuel Cutting
- Plasma Cutting
- Power Tools
- Punching and Other Holemaking
- Roll Forming
- Safety
- Sawing
- Shearing
- Shop Management
- Testing and Measuring
- Tube and Pipe Fabrication
- Tube and Pipe Production
- Waterjet Cutting
Industry Directory
Webcasts
Podcasts
FAB 40
Advertise
Subscribe
Account Login
Search
How a fabricator helps to keep data flowing for all of us
Hennig feeds big tech’s insatiable hunger for generator enclosures
- By Dan Davis
- February 1, 2024
- Article
- Shop Management
Hennig not only fabricates the enclosures and fuel tanks for the generators, but it also integrates the engines into the final package. Images: Hennig Power Protection
As a reader of this article, you likely are interested in metal fabricating, and chances are you’re using the internet, via a PC, tablet, or smartphone, to access this text. But you might not realize that metal fabricators are helping to make that digital interaction possible.
Founded in 1950, Hennig is a global manufacturer of machinery and components related to chip management, machine protection, and facility safety. Many of its machinery enclosures are found on machine tools throughout the North American metal fabricating community.
More than a decade ago, Hennig officials looked to expand upon its manufacturing expertise and started fabricating generator enclosures. They would not be simple sheet metal boxes around the generator, however. For example, they required insulation to minimize noise when the generators were engaged, and they needed double-walled fuel tanks to provide an added level of safety in case of leaks. Hennig took on this new challenge and began fabricating the enclosures at its Machesney, Ill., facility.
Over the next few years, the business was active, but not growing significantly. Then Hennig got its first call for an enclosure for a data center application.
“All of a sudden, that changed everything,” recalled Dietmar Goellner, Hennig CEO. “Instead of building one or two, it was, ‘Can you make 100 or 200 of these?’”
That began the meteoric rise of Hennig’s generator enclosure business. With the giant tech companies looking for reliable backup power should their data centers lose connection to the grid for any reason, they need generators to prevent stops in data transmission and storage. Videos need to be streamed. Emails need to be sent. Social media feeds need to be updated. For that to happen, the data centers need to keep operating—and cooled—even when powered by backup generators.
Today, Hennig Power Protection, Hennig’s enclosure manufacturing division, is booked through 2025. It has 350,000 sq. ft. of manufacturing space devoted to the fabrication of these enclosures, with plans to more than double that to 850,000 sq. ft. with new expansions by the end of 2024.
“In the last four years, we’ve grown at a rate of 100% a year,” Goellner said. To keep up with business bookings, he added that Hennig will need to do that again in the next couple of years.
The thirst for data storage continues to grow, and the emergence of information tools powered by artificial intelligence, which are particularly computationally intensive, likely will accelerate growth even more. Hennig’s plan to stay on top of these opportunities is bold, but recent successes suggest the company is more than capable of delivering on its commitments.
Building Structures and Capacity
In 2016, Hennig expanded its existing facility on its campus dedicated to enclosure systems. The building was designed to accommodate design, engineering, sales, marketing, and manufacturing capabilities, with additional room for testing the generator systems outdoors before they are shipped to customers.
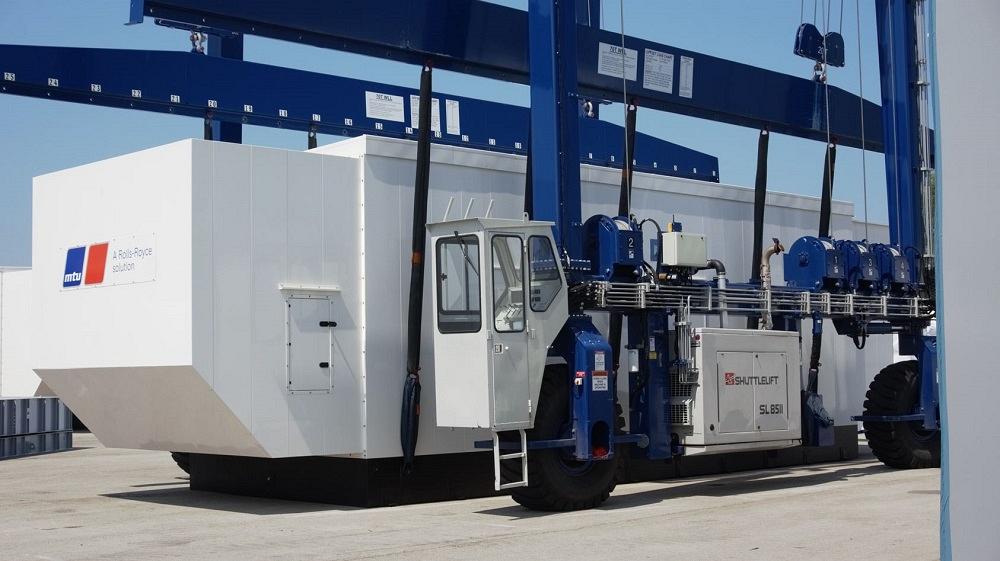
This generator, fabricated by Hennig Power Protection, is destined for a data center, where it will provide backup power to servers should there be an interruption in power delivery from the electrical grid.
That was just the beginning. In 2019, Hennig opened a new 125,000-sq.-ft. facility to accommodate more manufacturing, including room for a state-of-the-art, four-stage powder coating line. It also purchased a nearby empty manufacturing space and made plans to expand that building as well. With plans for completion in 2024, this facility will quadruple the company’s current manufacturing space for enclosures.
Meanwhile, Hennig also set up a storage lot for completed generator systems on a neighboring property. The lot, which can host up to 65 units, catches the eyes of many passing drivers, as the generators are about the size of a mobile home. This complements the lot near the original enclosure manufacturing facility, which can hold 30 completed units.
All of this new manufacturing space doesn’t contribute to productivity unless tools are supplied to assist with the metal fabricating. Goellner said that the new facility will have five new laser cutting machines and six folding machines to produce parts. Additionally, Hennig plans to add 30 more large cranes to the manufacturing mix.
Scaling up to stay on top of the work coming its way has required big planning. Goellner said that Hennig was somewhat new to this manufacturing segment, so it had some catching up to do. Some of the data center customers seeking its metal fabricating services for the enclosures and turnkey delivery of the generators were somewhat doubtful that Hennig could get there. They aren’t sharing those doubts with Goellner anymore.
“We’re going to be in a position where we might be the largest supplier of this type of infrastructure item in the Americas,” he said. “That’s where we are headed right now.”
Cultivating a Workforce
New manufacturing facilities need not only machine tools but also skilled workers. Goellner said the company hopes to add 250 more people to its current roster of 550 employees over the next 12 months.
“We need people to fill out applications. We need people that can run laser machines and folding machines. We need painters and assemblers. We need people that are good with electrical,” Goellner said. “That’s the challenge.”
One of the ways that Hennig hopes to fill the ranks is through its connection with Rock Valley College in nearby Rockford, Ill. Hennig is a sponsor of the welding program at the community college. (Hennig’s sister company, Advanced Machine and Engineering, a manufacturer and distributor of machine tool components and metal cutting systems, sponsors the CNC machine curriculum at the school.)
Goellner said that the company regularly takes in interns, some of whom have turned into long-term employees for the company. With the continual expansion, some of these hires have been able to take on new responsibilities that would not have been available at smaller operations.
When asked if automation could help to offset the glaring need for welders, Goellner said that robotics aren’t much help for Hennig. For something like the double-walled fuel tanks, which are large and bulky, welders can lay their beads in almost the same time that it would take to get something that large placed into a fixture for robots to do their jobs.
In an effort to recruit welders to join the company, Hennig is a sponsor of the welding program at Rock Valley College’s Advanced Technology Center.
But automation has made a major impact on Hennig’s shop floor in the laser cutting area. Material handling systems can keep these machines supplied with new sheets, after removing laser-cut parts and the accompanying skeleton, which means these systems can run unattended, leaving machine operators to tend to other processes.
Taking Ownership of Design and Manufacturing
As the recent pandemic demonstrated, supply chains are not infallible, but Hennig didn’t need a global medical emergency to learn that lesson. Goellner said it’s always been a goal for the company to control everything it can—from design to almost every aspect of manufacturing—so that it can eliminate the delays that often occur when work is outsourced to partners that have multiple commitments to maintain.
On the design side, engineers are guided by design specifications that are written into contracts, but these aren’t run-of-the-mill sheet metal jobs. These generator enclosures are the emergency backups for data centers in the case of grid failure, which might be caused by some sort of natural disaster, such as a hurricane. As a result, these generators have to be fabricated to withstand the worst that Mother Nature can muster.
As an example, Goellner explained how special consideration has to be given to some of the generator enclosures that incorporate extremely tall plenums for emissions and heat release. These plenums, which might stand 100 ft., have to stand up to the power of hurricane winds. That requires designs that get the seal of approval from a professional engineering firm.
“You have to design these things so that you’re not going to have any structural failure,” Goellner said.
The same desire that Hennig demonstrates in wanting to be the design authority also exists on the manufacturing side.
“We like a certain amount of vertical integration,” Goellner said. “There’s an old saying: If you’re going to hang yourself, use your own rope.”
The pandemic really drove that point home for the company, according to Goellner, because supply chains, which up until that point had been pretty reliable, were disrupted. Without timely delivery of components that weren’t made in-house, generator systems are forced to either be held until completion somewhere on the Hennig campus or delivered with assembly finished on-site, neither of which is desired.
Because the company controls all aspects of fabricating and finishing, it only has to worry about obstacles within its own walls. Luckily, those can be discovered quickly and rectified in an organized manner. Goellner said that’s been an important key to Hennig being able to maintain its almost 100% on-time delivery rate, even with all of the expansion taking place.
Practicing Lean Manufacturing
Hennig strives to be a lean manufacturing organization, attempting to root out wasteful efforts and expenditures, with the goal of working to improve all actions—both in the front office and on the shop floor—that are connected to fabricating these generator enclosures and ultimately assembling the final package. That’s why oddities, such as an extra set of panels that was fabricated before it was needed, stick out as Goellner walks through the shop. Parts are only produced as they are needed to ensure that work-in-process (WIP) remains limited and controlled and nothing gets lost on the floor.
Hennig’s commitment to its customers applies to both external and internal parties, the latter of which represents company employees.
If something needs to be addressed, it’s tackled right away. Hennig uses an Andon System (which originates from the Toyota Production System) to bring these issues to light. If someone sees something that is not quite how it should be, say WIP positioned near the generator assembly area that is not scheduled to be there, the appropriate people are flagged down to discuss the situation. From there, they initiate a course of attack, which they call a PDCA (Plan/Do/Check/Act). The group formulates a plan, puts the plan into action, checks the results, and acts on the findings or adjusts the plan slightly to get to the desired outcome.
These PDCA efforts then can be discussed at daily SQID+P (Safety/Quality/Inventory/Delivery + Productivity) meetings that occur each morning. In general, people can learn important lessons from these occurrences and corrections. More specifically, they can see how a root cause analysis can result in corrective actions that resolve an important issue.
“We have to get better during these meetings so there’s not just one person leading it and the other people aren’t saying anything,” Goellner said. “We want to elicit discussion with people and get them engaged.”
Addressing these smaller issues help to make the big picture possible: Processes are completed on-time and parts are delivered where they need to be. This keeps the WIP and inventory to a minimum.
“We don’t like beavers here. They dam up the place,” Goellner said. “It has to flow like a river. It’s all about perpetual motion.”
When a job commences, it’s the beginning of coordinated operations that lead to the on-time delivery of a generator system. Lasers cut blanks from material that’s 14 ga. to 0.75 in. thick. The blanks migrate to press brakes or folding machines where they are shaped into forms needed to complete the housing. They then make their way to the welding department and then to powder coating.
(The newly installed powder coating lines are a good example of how everything revolves around maintaining the right flow of parts through the facility, Goellner explained. The powder coating department has two side-by-side lines with two pretreatment booths, two dry-off ovens, and two powder application booths, but those two lines feed into three curing ovens. Why is that? Because of the curing time of some of the ovens, having only two ovens would create a bottleneck in the manufacturing process. Three ovens help to cure the powder topcoat in a time that keeps parts moving in flow with what the production schedule demands. This synchronization is critical to optimizing the flow of product and to allow for meeting the required takt time, which is the cycle time that aligns customer demand to planned production time.)
From finishing, the parts flow to assembly. Here, everything converges for the generator package to be put together. The generator is moved on to the fuel tank, the housing is moved on to the generator, and the electrical work and final touches are completed before the system moves on to testing and final delivery.
“When you operate a lean environment, you do have to sweat the details,” Goellner said. “You have to get rid of bottlenecks very quickly. You need components delivered when they are needed. All of that puts a lot of pressure on your supply chain and your internal processes.”
It was a little over a year ago when steel spiked in price and there were concerns about availability, so Hennig took on more raw material inventory than it might normally have. With the supply chain stabilizing a bit, Goellner said that the company is working to have its service center partners release inventory on a much more frequent schedule, helping Hennig to minimize the space and racking dedicated to sheet and plate storage. Increasing inventory turns also helps the company to improve cash flow.
Parts are only supposed to be staged when they are needed for assembly. That keeps work in process to a minimum and makes the most of finite shop floor space.
Supporting the Nation’s Digital Infrastructure
As Hennig keeps sprinting toward its goal of making more enclosures and fuel tanks for these generator systems destined for data center farms, it’s doing so in a confident and controlled manner. It knows how much time is needed to manufacture a complete generator package. It knows what it can currently produce. It has a pretty good idea what it will be able to produce when its new facility is up and running.
No one has time to try and tame mayhem, so it’s avoided. The goal is to stay on the known course and minimize the variables that might influence straying from that path.
That sort of manufacturing discipline is reflective of the structure required to maintain the “brains” of the internet, as some might refer to data centers. Internet users don’t have a lot of empathy for the data companies when their servers go down. In a world that values instant gratification, delays in digital communication and e-commerce are bad for business.
You don’t necessarily think of metal fabricating when you think of technology companies, but after learning what Hennig does, it’s hard to minimize its contributions to making the digital future possible.
About the Author
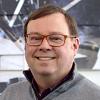
Dan Davis
2135 Point Blvd.
Elgin, IL 60123
815-227-8281
Dan Davis is editor-in-chief of The Fabricator, the industry's most widely circulated metal fabricating magazine, and its sister publications, The Tube & Pipe Journal and The Welder. He has been with the publications since April 2002.
Related Companies
subscribe now
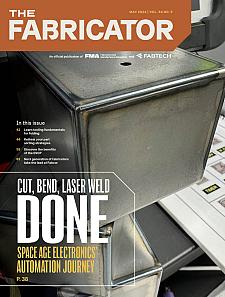
The Fabricator is North America's leading magazine for the metal forming and fabricating industry. The magazine delivers the news, technical articles, and case histories that enable fabricators to do their jobs more efficiently. The Fabricator has served the industry since 1970.
start your free subscription- Stay connected from anywhere
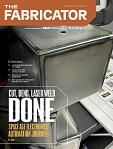
Easily access valuable industry resources now with full access to the digital edition of The Fabricator.
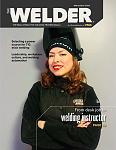
Easily access valuable industry resources now with full access to the digital edition of The Welder.
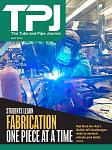
Easily access valuable industry resources now with full access to the digital edition of The Tube and Pipe Journal.
- Podcasting
- Podcast:
- The Fabricator Podcast
- Published:
- 04/16/2024
- Running Time:
- 63:29
In this episode of The Fabricator Podcast, Caleb Chamberlain, co-founder and CEO of OSH Cut, discusses his company’s...
- Trending Articles
Tips for creating sheet metal tubes with perforations
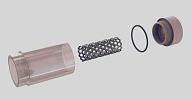
Are two heads better than one in fiber laser cutting?
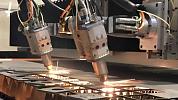
Supporting the metal fabricating industry through FMA
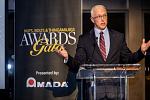
JM Steel triples capacity for solar energy projects at Pennsylvania facility
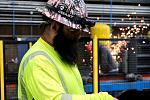
Omco Solar opens second Alabama manufacturing facility
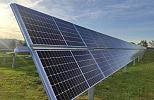
- Industry Events
16th Annual Safety Conference
- April 30 - May 1, 2024
- Elgin,
Pipe and Tube Conference
- May 21 - 22, 2024
- Omaha, NE
World-Class Roll Forming Workshop
- June 5 - 6, 2024
- Louisville, KY
Advanced Laser Application Workshop
- June 25 - 27, 2024
- Novi, MI