Editor-in-Chief
- FMA
- The Fabricator
- FABTECH
- Canadian Metalworking
Categories
- Additive Manufacturing
- Aluminum Welding
- Arc Welding
- Assembly and Joining
- Automation and Robotics
- Bending and Forming
- Consumables
- Cutting and Weld Prep
- Electric Vehicles
- En Español
- Finishing
- Hydroforming
- Laser Cutting
- Laser Welding
- Machining
- Manufacturing Software
- Materials Handling
- Metals/Materials
- Oxyfuel Cutting
- Plasma Cutting
- Power Tools
- Punching and Other Holemaking
- Roll Forming
- Safety
- Sawing
- Shearing
- Shop Management
- Testing and Measuring
- Tube and Pipe Fabrication
- Tube and Pipe Production
- Waterjet Cutting
Industry Directory
Webcasts
Podcasts
FAB 40
Advertise
Subscribe
Account Login
Search
Closing the skills gaps through apprenticeships
A quick overview of the North Carolina Triangle Apprenticeship Program reveals what it takes to build a pipeline of manufacturing talent
- By Dan Davis
- October 13, 2016
- Article
- Shop Management
The need to find skilled manufacturing workers is a constant concern for metal fabricators as they see experienced workers preparing for retirement if they haven’t left already. Many are still trying to figure out just how they are going to replace those valued employees.
The trouble is that the current generations—parents and children alike—generally don’t know what a manufacturing career has to offer. Also, young people aren’t exposed to tasks like working on cars or small engine repair like previous generations were, and as a result, they aren’t as mechanically inclined.
Such trends worry manufacturers. In a PricewaterhouseCoopers/Manufacturing Institute survey released this summer, 29 percent of 120 U.S. manufacturers surveyed said that a skilled-worker shortage exists today and will only increase in the next three years. In the same survey, 31 percent said that they don’t see a skills shortage now, but believe one will emerge in the next three years.
Metal fabricators share similar thoughts. In The FABRICATOR’s 2015 “What Keeps You up at Night?” survey of about 100 fabricators, most (about 38 percent) ranked “availability of skilled workers” as their No. 1 concern, far outranking concerns about the economy. That sentiment was duplicated in the 2013 version of the same survey.
It should come as no surprise that as people wring their hands over what to do about finding new workers, some shops are taking definitive steps to attract young people who not only have general manufacturing skills, but are also familiar with how the shop runs. Those businesses are hiring apprentices. In fact, the U.S. Department of Labor reports that it counted 450,000 registered apprenticeships in 2015, up from 350,000 in 2011.
To learn more about how one fab shop, Accu-Fab Inc., took steps to welcome its first apprentices this summer, The FABRICATOR interviewed Gregg Page, president, Accu-Fab Inc., and Michael Moore, director of apprenticeship training, Wake Technical Community College, both located in Raleigh, N.C.
How Did the Apprenticeship Program Get Started?
Most fabricators probably would like to know that because many simply don’t have the means to launch their own internal program. The North Carolina Triangle Apprenticeship Program got started when other manufacturers in the research triangle area—bounded by Raleigh, Durham, and Chapel Hill—came together.
Moore started at Wake Tech in September 2011. About two months into his job, he met Robbie Earnhardt, owner of Superior Tooling, a mold manufacturer in Wake Forest, N.C., who wanted to start an apprenticeship program modeled after the successful Apprenticeship 2000 program in place in western North Carolina. Moore said that Earnhardt had been working for a couple of years to get something started, but wasn’t gaining a lot of traction on the issue.
Soon after meeting Earnhardt, Moore heard through a co-worker that another company in the area, CaptiveAire, a manufacturer of commercial ventilation systems, was looking for information on Apprenticeship 2000. Moore connected Earnhardt with CaptiveAire President Bob Luddy, and a little later Lukas Schoenwetter of nearby Buhler Aeroglide, a maker of food processing equipment, joined the group.
“They did a lot of hard work, and Wake Tech partnered with them to get the program going,” Moore said. “Our president, Dr. Stephen Scott, committed to them that we would provide the training they needed for the program. That’s the direction we went.”
How Did the Program Launch Go?
Moore said the North Carolina Triangle Apprenticeship Program (NCTAP) had a good foundation from the start. Local companies were interested in hiring the apprentices and offering on-the-job learning and wages. Wake Tech had the classroom training covered. Finding an audience, however, was a little more difficult.
“The first year they wanted to go to the schools to talk about the program, but they had difficulty getting in. The school counselors weren’t quite receptive,” Moore said. They started out with only seven apprentices.
The second year more students were interested because people were talking about the program. Nine students got involved.
This year, the third year of the program, NCTAP took 14 students.
“The parents are starting to hear about it. The students are starting to hear about it,” Moore said. “It’s a great program for the students, and it’s a great benefit for the companies.”
How Exactly Does the Program Work?
Accu-Fab Inc. took its first apprentices this summer. They were identified as good candidates after they completed a project their junior years and participated in an internship this summer.
According to Accu-Fab’s Page, the two students are now completing their senior year classes in the morning and working at the shop in the afternoon. Once they graduate, they enter the Wake Tech program where they go to school on Monday and work Tuesday through Friday at Accu-Fab. At the end of four years, the apprentices get an associate’s degree in mechanical engineering technology and a journeyman’s certificate, which demonstrates the individual’s competency in a variety of fabricating technology areas.
What Are the Motivations for Manufacturers to Participate in the Program?
“We were attracted to the apprenticeship program because it seemed like a good way to groom some primarily mechanical engineers,” Page said. Area schools like North Carolina State produce competent mechanical engineers, but they really don’t know anything about practical work in a fabricating operation, he added.
Page also said he has to look at the bigger picture.
“I think a lot of these kids don’t have a concept of manufacturing and what that means,” he said. “They all want to be nurses and app designers.
“In reality, some of these kids are not bound for college. They need to know that there is a way to make a decent living with on-the-job training at this company and at other companies. It’s a whole lot better than working at McDonald’s.”
How Do the Manufacturers Get the Most out of the Apprenticeship?
Moore said it starts with the mentor.
“The mentor’s job is to determine where that person or student is working in the shop,” he said. “They monitor how they are doing in their classes. If that student is struggling in one particular area, they can get the student the help he or she needs to get through that class.”
It should be noted that when young interns or apprentices first hit a shop floor, more experienced workers may be a little cold to them. Moore said that type of reaction is to be expected as these “old-timers” can feel threatened by the arrival of students being groomed to perhaps take someone’s job. That attitude changes quickly, however.
“Once the other people saw what the apprentices were doing and the quality of the work they were doing, the old-timers started asking when they could get them into their areas,” Moore said.
With more people involved in the mentoring experience, the manufacturer can offer a more enriching apprenticeship.
Why Is NCTAP Successful?
It’s good to have educational institutions in line to design a curriculum to support an apprenticeship program. It helps to have students, parents, and guidance counselors aware that a career in manufacturing might be a fruitful one. But without the buy-in from manufacturing companies, NCTAP wouldn’t be having the success it is currently enjoying.
“You can set up all the educational programs that you want, but if there is not a job at the end of it, then it’s not worthwhile,” Moore said. “In this case, the manufacturers talked to us and told us what they needed. Wake Tech is providing what they needed. The manufacturers are stepping up and providing the opportunities. It’s a great collaboration.”
Accu-Fab Inc., 919-212-6400, www.accufabnc.com
North Carolina Triangle Apprenticeship Program, www.nctap.org
Wake Technical Community College, 919-866-5000, www.waketech.edu
About the Author
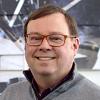
Dan Davis
2135 Point Blvd.
Elgin, IL 60123
815-227-8281
Dan Davis is editor-in-chief of The Fabricator, the industry's most widely circulated metal fabricating magazine, and its sister publications, The Tube & Pipe Journal and The Welder. He has been with the publications since April 2002.
subscribe now
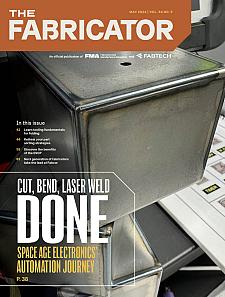
The Fabricator is North America's leading magazine for the metal forming and fabricating industry. The magazine delivers the news, technical articles, and case histories that enable fabricators to do their jobs more efficiently. The Fabricator has served the industry since 1970.
start your free subscription- Stay connected from anywhere
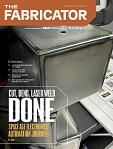
Easily access valuable industry resources now with full access to the digital edition of The Fabricator.
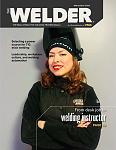
Easily access valuable industry resources now with full access to the digital edition of The Welder.
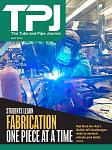
Easily access valuable industry resources now with full access to the digital edition of The Tube and Pipe Journal.
- Podcasting
- Podcast:
- The Fabricator Podcast
- Published:
- 04/30/2024
- Running Time:
- 53:00
Seth Feldman of Iowa-based Wertzbaugher Services joins The Fabricator Podcast to offer his take as a Gen Zer...
- Industry Events
16th Annual Safety Conference
- April 30 - May 1, 2024
- Elgin,
Pipe and Tube Conference
- May 21 - 22, 2024
- Omaha, NE
World-Class Roll Forming Workshop
- June 5 - 6, 2024
- Louisville, KY
Advanced Laser Application Workshop
- June 25 - 27, 2024
- Novi, MI