Contributing Writer
- FMA
- The Fabricator
- FABTECH
- Canadian Metalworking
Categories
- Additive Manufacturing
- Aluminum Welding
- Arc Welding
- Assembly and Joining
- Automation and Robotics
- Bending and Forming
- Consumables
- Cutting and Weld Prep
- Electric Vehicles
- En Español
- Finishing
- Hydroforming
- Laser Cutting
- Laser Welding
- Machining
- Manufacturing Software
- Materials Handling
- Metals/Materials
- Oxyfuel Cutting
- Plasma Cutting
- Power Tools
- Punching and Other Holemaking
- Roll Forming
- Safety
- Sawing
- Shearing
- Shop Management
- Testing and Measuring
- Tube and Pipe Fabrication
- Tube and Pipe Production
- Waterjet Cutting
Industry Directory
Webcasts
Podcasts
FAB 40
Advertise
Subscribe
Account Login
Search
Nature comes to life in hands of Canadian metal artist
Toronto-based Angellos Glaros wins big with “Blue Heron” sculpture
- By Rob Colman
- February 14, 2024
- Article
- Plasma Cutting
Editor’s Note: This feature originally appeared in the January 2024 issue of Canadian Fabricating & Welding.
Last November, Toronto-based Metal Supermarkets announced the winners of its annual Metal My Way contest, which aims to showcase versatility and craftsmanship in metalworking, fabricating, and design. From among 870 international submissions, Angellos Glaros’ sculpture, “Blue Heron,” was chosen as the grand prize winner.
Metal Inspiration
Glaros lives and works in Nanaimo, B.C., running Glaros Studios/WestCoast Arts. He grew up in southern Ontario but pursued his interest in the arts at Nova Scotia College of Art and Design, where he learned to work in marble and clay.
After college, Glaros learned woodworking, further expanding his artistic and commercial skills. In the late ‘90s, an injury led him to switch to finishing work. From there, he developed his woodworking business, eventually opening his own studio in 2000. He built wooden furniture and carved animals, trees, and people.
It wasn’t until visiting a metal artist’s studio in about 2008 that Glaros was inspired to work with mild steel.
“The artist was working on an oak tree motif, including leaves and acorns—a lot of detail,” said Glaros. “I was blown away and ran right out and got myself a welder to start learning.”
He now has two welding power sources (one for the shop and one for on-site work), two plasma cutters, an anvil, a power hammer, and a 6-ton fly press.
Capturing the Natural World
What stands out is Glaros’ ability to bring a lifelike look to metal that is designed to appear organic. For instance, he has made railings that look like tree branches and a shaker-style dining table base that looks like a tree stump.
“I shape the metal with a power hammer first,” explained Glaros. “With the railings, I would heat the pipe to cherry red and use the power hammer to taper the ends, which creates folds and a natural look. Once it was shaped, I basically laid down weld beads along the length of it and filled some of the folds to create the desired shape. Once that is done, I grind it, sand it, and then use a sanding flap wheel to get the textured look and the smoothness just right.”
Although the texture is achieved primarily through grinding, the finishing process is just as important.
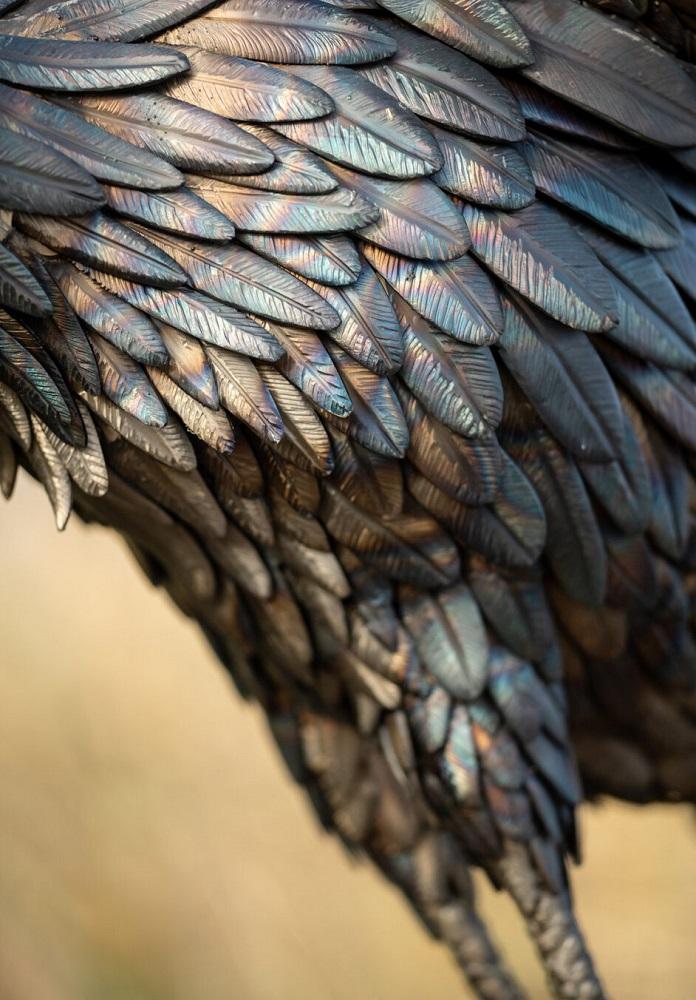
Glaros cut out each feature individually and used a die grinder to create the lines in the feathers. He then blended it all together with a flap-wheel sander.
“At that point, I do a chemical bath, spraying it until I get the color precisely how I want it,” he explained. “I then wash it and apply an automotive finish for outdoor pieces. That helps preserve it better, and it’s the only finish I’ve found that really works effectively for the outdoors.”
Blue Heron
Glaros’ “Blue Heron” required an arduous process to create its look, including the bird’s neck.
“It was a smooth-shaped 12-ga. mild steel pipe when I started, and I just worked it with the die grinder,” he said.
“Similarly with the feathers, I cut them out and used the die grinder to create the lines in the feathers and used a flap-wheel sander to blend it all when I’m done. At that point, I put each one on a fly press to give it a bit of a curve in whatever direction is necessary to dome it.”
With this design, he used an armature for the body, which allowed the finish to flow around the back of all the feathers. For the wings, he used a basic armature at the leading edge to achieve the appearance of lightness.
The layered feathers were the big challenge for Glaros because he had to get the finish on the backside. To achieve this, he pretreated them individually before welding to ensure they would not be affected by the elements.
“I had to hang them all up in the spray booth for six hours and watch to ensure no drips formed on the tips of the feathers,” he said. “When that was dry, I put five coats of automotive finish on it. I use a finish with which you can control the sheen on it, so that I could make it fairly flat. It would look bad if it were too shiny.”
More than 1,200 feathers appear on the finished sculpture, all welded on by Glaros. He created a mortise and tenon joint to insert them and a bolt mechanism to further hold them in place.
The whole bird was torched to some degree to add color.
“For example, the beak was heated to a light red to get the final dark gray color,” said Glaros. “The feathers used much less heat, but heat was used to create the variation in color.”
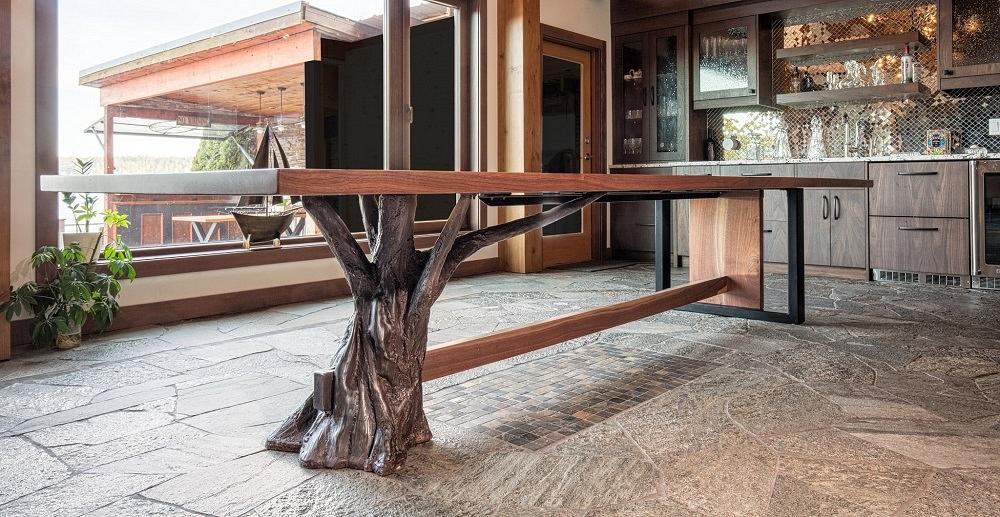
The base of this table is an example of the organic forms Glaros can add to furniture with his metalwork and finishing skills.
The sculpture took approximately 450 hours to complete. “Blue Heron” is, to Glaros’ estimation, the best and most complicated piece he has achieved thus far, but he feels there is still much to learn.
“I have only done one metal sculpture depicting a person, so I think the human face is where I want to explore more now,” he said.
What’s key is that Glaros remains undaunted in the face of new opportunities to explore.
“I’d say to anyone interested in this sort of artistic pursuit, no matter what your medium, take some life-drawing classes. Start sketching. It’s all about training your eyes to see what is there as opposed to seeing what your brain thinks is there,” he said.
About the Author
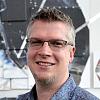
Rob Colman
subscribe now
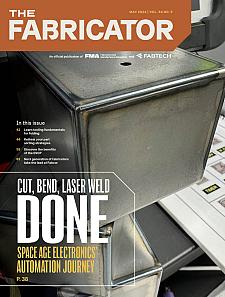
The Fabricator is North America's leading magazine for the metal forming and fabricating industry. The magazine delivers the news, technical articles, and case histories that enable fabricators to do their jobs more efficiently. The Fabricator has served the industry since 1970.
start your free subscription- Stay connected from anywhere
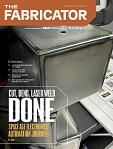
Easily access valuable industry resources now with full access to the digital edition of The Fabricator.
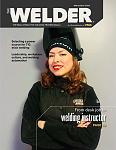
Easily access valuable industry resources now with full access to the digital edition of The Welder.
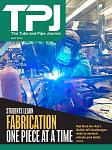
Easily access valuable industry resources now with full access to the digital edition of The Tube and Pipe Journal.
- Podcasting
- Podcast:
- The Fabricator Podcast
- Published:
- 04/16/2024
- Running Time:
- 63:29
In this episode of The Fabricator Podcast, Caleb Chamberlain, co-founder and CEO of OSH Cut, discusses his company’s...
- Trending Articles
Tips for creating sheet metal tubes with perforations
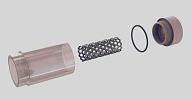
Are two heads better than one in fiber laser cutting?
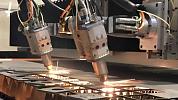
Supporting the metal fabricating industry through FMA
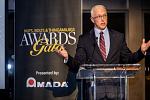
JM Steel triples capacity for solar energy projects at Pennsylvania facility
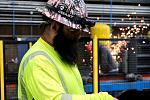
Omco Solar opens second Alabama manufacturing facility
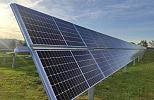
- Industry Events
16th Annual Safety Conference
- April 30 - May 1, 2024
- Elgin,
Pipe and Tube Conference
- May 21 - 22, 2024
- Omaha, NE
World-Class Roll Forming Workshop
- June 5 - 6, 2024
- Louisville, KY
Advanced Laser Application Workshop
- June 25 - 27, 2024
- Novi, MI