- FMA
- The Fabricator
- FABTECH
- Canadian Metalworking
Categories
- Additive Manufacturing
- Aluminum Welding
- Arc Welding
- Assembly and Joining
- Automation and Robotics
- Bending and Forming
- Consumables
- Cutting and Weld Prep
- Electric Vehicles
- En Español
- Finishing
- Hydroforming
- Laser Cutting
- Laser Welding
- Machining
- Manufacturing Software
- Materials Handling
- Metals/Materials
- Oxyfuel Cutting
- Plasma Cutting
- Power Tools
- Punching and Other Holemaking
- Roll Forming
- Safety
- Sawing
- Shearing
- Shop Management
- Testing and Measuring
- Tube and Pipe Fabrication
- Tube and Pipe Production
- Waterjet Cutting
Industry Directory
Webcasts
Podcasts
FAB 40
Advertise
Subscribe
Account Login
Search
Arena project leads to pipe cutting automation at Fought & Co.
Plasma cutting system reduces processing time for Oregon structural steel fabricator
- By Sue Roberts
- November 29, 2019
- Article
- Plasma Cutting
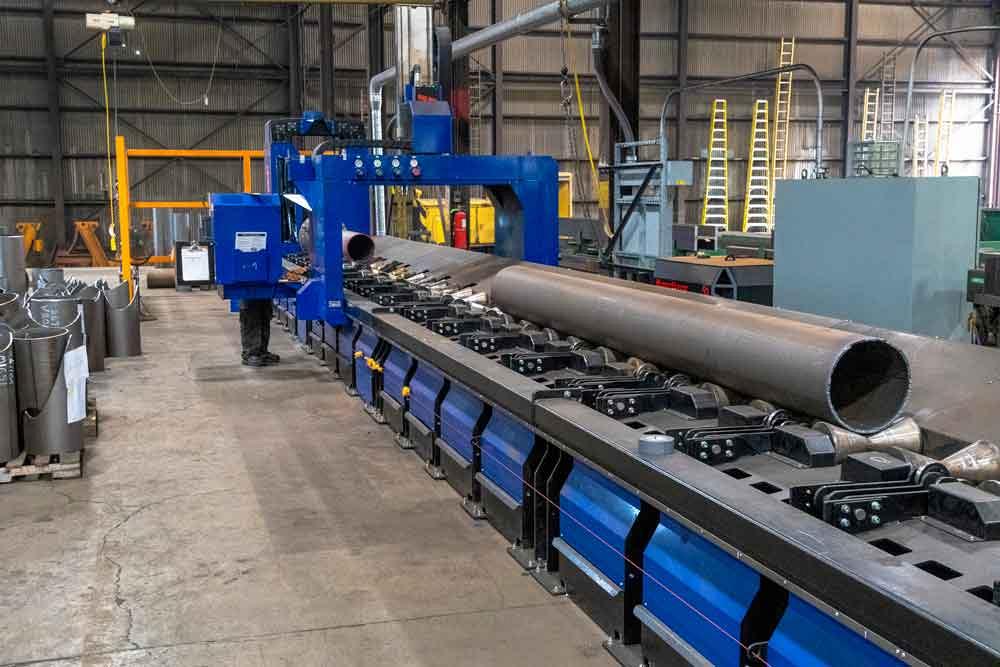
A special 60-ft.-long table was built as part of the Machitech Pipe Cut CNC plasma pipe and tube processing machine. Fought & Co.
Fought & Co., Tigard, Ore., is on track for a very good 2020. A large track and field arena that the company is building in the Pacific Northwest will be one of the world’s largest when it is completed in 2020. Spectators in the 12,650 permanent seats, expandable to 25,000, will have unobstructed views of competitors on a nine-lane track. Its interior will incorporate the typical locker rooms, classrooms, offices, and conference rooms plus a 140-meter, six-lane indoor practice straightaway. Unique exterior features will include an 8-foot-wide concourse that wraps around the upper bowl of the west stands and a multistory tower, shaped to resemble the Olympic torch, that will house exhibits.
Work on the arena began in the summer of 2018 when Fought & Co. and its subsidiary REFA Erection were chosen for the job. Sixty years of experience completing complex structural steel projects—bridges, hospitals, malls, airport terminals, and government buildings, along with stadiums and arenas—made the fabricating and erecting company a good fit with the project.
A full complement of heavy-duty equipment resides under more than 4 acres of roof, making it one of the largest steel fabrication and surface treatment and painting facilities in the region. Its 180,000-sq.-ft. facility resides on 7 acres just outside of Portland.
Two 10-hours shifts of 110 shop employees produce the always large components. Add in erection crews and shop personnel and the head count swells to about 350. Still, increased demands, particularly in the summer, can make a few extra hands and increased efficiencies welcome.
“It is definitely a test to find good people right now. We try to treat people good so they stay with us. We do a lot of in-house training, and we try to be creative,” said Wayne Searle, company president. “We have a program called Fought 500. If an employee brings us another hire, after 90 days they both get a $500 bonus.”
Improving the Process
That same creative spirit and willingness to invest are evident on the shop floor, particularly when projects have unusual construction specifications.
“A large number of components going into the current arena project aren’t typically part of that type of a structure. The arena has big plate columns that have to be manufactured in pieces and a lot of pipes that sit on the back side of the arena for support. Some of the pipe configurations are fish mouth—or a V-shape—so they require very sharp cuts,” Searle said.
“Producing them using pattern development and layout with an acetylene torch would have been cumbersome. We had to come up with a way to be better at cutting.”
This is where creativity and investment joined with automation. A Machitech Pipe Cut™ CNC plasma pipe and tube processing machine with a customized 60-ft. table was added to the company’s equipment roster. The system cuts miters, saddles, holes, slots, gussets, and the fish mouths in pipe from 2.5 to 24 inches in diameter and up to just short of the table length. Large components are produced from pipe with 14- and 20-in. diameters and run up to 40 ft. long.
Overhead cranes and pipe grabbers load and unload the pipe, which is stored next to the machine.
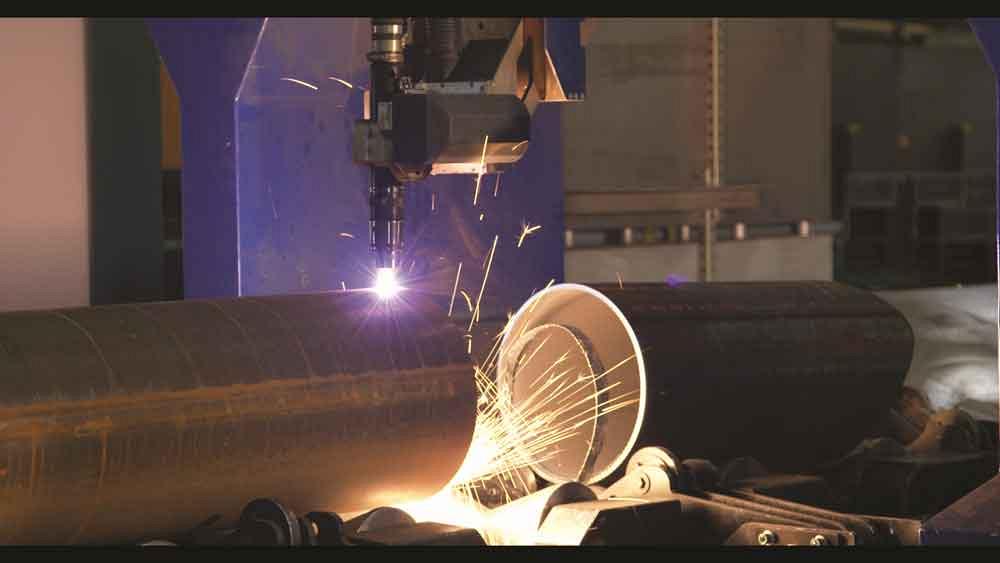
A Hypertherm XPR300 plasma cutting system is combined with a 5-axis cutting head to provide cutting flexibility for structural steel fabricator Fought & Co. Fought & Co.
A floating chuck system prevents slippage and handles out-of-round pipe, a motorized infeed conveyor works with pipe up to 60 ft., and pneumatic support rollers position the material for processing.
“Since each of our jobs is different, the extra-long table gives us processing flexibility. Some of the pipe bays we are working with are 18½ ft. long with three pieces in each bay. I can lay three bays down and cut the equivalent of nine pieces during one run,” Searle said.
A 5-axis cutting head directs the cuts made by the Hypertherm XPR300™ plasma system that cuts mild and stainless steels and aluminum. Plasma gases are automatically mixed to provide what the company terms X-Definition™, the next generation of its HyDefinition® cut.
Rotary Tube Pro™ tube cutting software, also from Hypertherm, allows for programming cut designs and importing and converting CAD/CAM programs.
Making It Easy
Fred Butkovich, operations improvement manager, said that the cut tubes go straight from the plasma cutting system to welding.
“It would have been very difficult for us to do this project without this automation,” he said. “We take stock pieces of pipe and cut the parts we need in a fraction of the time it would have taken using wraparounds and hand burning. The plasma cuts a lot faster than oxyfuel and provides a pretty clean cut. We just specify the amperage based on the thickness and material of the pipe. We haven’t needed to do any secondary cutting unless features require a steeper angle than what the machine can actually do.
“We import files from the detailer in a STEP program,” he continued. “They can go right to the machine; it strikes an arc and cuts at the angle we need. We don’t even need drawings. We specify the length of pipe and the features we want, and we are ready to go. Once the machine is done, the tube is done.
“And the program automatically nests the cuts so we save material on jobs like fish-mouth cuts.”
Prepping for Automation
Preparations for adding the new equipment were minimal. The shop floor had enough space for the lengthy system, so adding a little more electrical service and a dust extraction system were the only things that needed to be done.
Equipment training also didn’t pose a problem.
“Machitech trained four or five of our operators and their managers to make sure that we always have someone to run the system. They helped with training for the software, programming, actual cutting, and safety,” Searle said.
“If we do have any challenges, the machine is actively online with Machitech. They can remotely look at the system’s control at the same time we do and recommend any fixes.”
Shifting the Focus
Since adding the automated system, Searle said any tube cutting issues, which would have been the critical aspect of a job, have been cut away. Stubs, pieces of plasma-cut pipe, are completed quickly and accurately, so production focus has shifted to providing the best possible downstream processes.
“We keep track of the stubs cut each day. For example, in two 10-hour shifts the automated system can cut 49 pieces of large fish-mouth pipe. If we were cutting by hand, that count would probably be two or three in that time frame,” Searle said.
“We’re still in the middle of an arena project, and that will keep the system busy for a while longer, but we’ve already been approached by other people who want us to cut pipe. Beyond that, the additional cutting speed and accuracy of the automation allow us to bid on projects that we would have struggled to be competitive on before.”
Looking ahead, Searle also believes that there is an uptick in the use of pipe as aesthetic, as well as supporting construction elements. He expects that trend will help fill the pipeline that will keep the automated plasma pipe cutting system busy. Is more automation on the way for the company?
“Definitely,” Searle said. “We got this machine to shave hours off a particular project and to give us versatility going forward. We plan on investing in other automation to help us do the same thing in other areas.”
About the Author
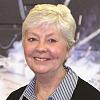
subscribe now
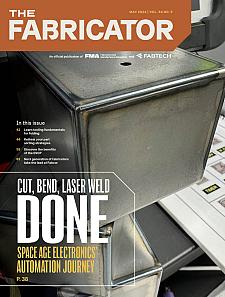
The Fabricator is North America's leading magazine for the metal forming and fabricating industry. The magazine delivers the news, technical articles, and case histories that enable fabricators to do their jobs more efficiently. The Fabricator has served the industry since 1970.
start your free subscription- Stay connected from anywhere
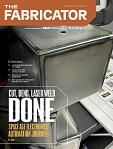
Easily access valuable industry resources now with full access to the digital edition of The Fabricator.
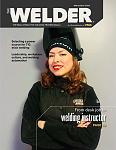
Easily access valuable industry resources now with full access to the digital edition of The Welder.
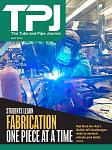
Easily access valuable industry resources now with full access to the digital edition of The Tube and Pipe Journal.
- Podcasting
- Podcast:
- The Fabricator Podcast
- Published:
- 04/16/2024
- Running Time:
- 63:29
In this episode of The Fabricator Podcast, Caleb Chamberlain, co-founder and CEO of OSH Cut, discusses his company’s...
- Trending Articles
Tips for creating sheet metal tubes with perforations
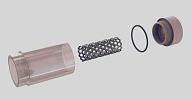
JM Steel triples capacity for solar energy projects at Pennsylvania facility
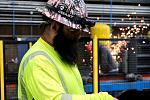
Are two heads better than one in fiber laser cutting?
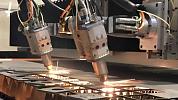
Supporting the metal fabricating industry through FMA
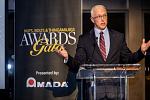
Omco Solar opens second Alabama manufacturing facility
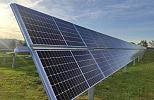
- Industry Events
16th Annual Safety Conference
- April 30 - May 1, 2024
- Elgin,
Pipe and Tube Conference
- May 21 - 22, 2024
- Omaha, NE
World-Class Roll Forming Workshop
- June 5 - 6, 2024
- Louisville, KY
Advanced Laser Application Workshop
- June 25 - 27, 2024
- Novi, MI