Editor-in-Chief
- FMA
- The Fabricator
- FABTECH
- Canadian Metalworking
Categories
- Additive Manufacturing
- Aluminum Welding
- Arc Welding
- Assembly and Joining
- Automation and Robotics
- Bending and Forming
- Consumables
- Cutting and Weld Prep
- Electric Vehicles
- En Español
- Finishing
- Hydroforming
- Laser Cutting
- Laser Welding
- Machining
- Manufacturing Software
- Materials Handling
- Metals/Materials
- Oxyfuel Cutting
- Plasma Cutting
- Power Tools
- Punching and Other Holemaking
- Roll Forming
- Safety
- Sawing
- Shearing
- Shop Management
- Testing and Measuring
- Tube and Pipe Fabrication
- Tube and Pipe Production
- Waterjet Cutting
Industry Directory
Webcasts
Podcasts
FAB 40
Advertise
Subscribe
Account Login
Search
Operating a new heavy-duty press brake
A metal fabricator talks about the transition to working on a modern 1,100-ton brake
- By Dan Davis
- February 5, 2024
- Article
- Bending and Forming
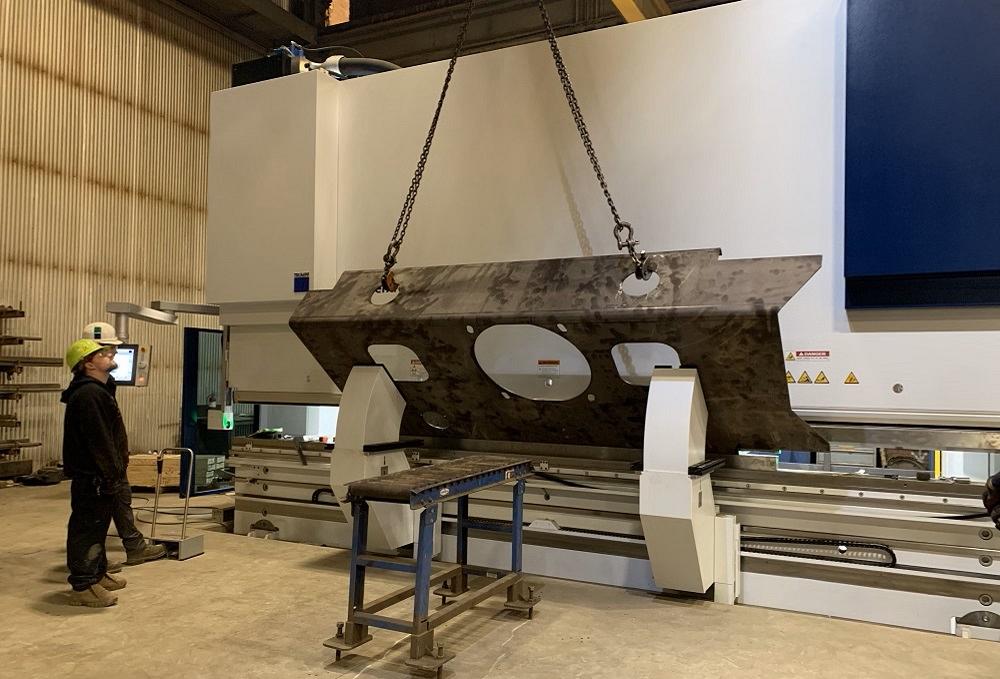
The TRUMPF TruBend 8010 1,100-ton press brake at O’Neal Manufacturing Services’ Pittsburgh facility has been forming parts since the spring of 2023. Images: O’Neal Manufacturing Services
As a large contract manufacturing company, O’Neal Manufacturing Services has nine facilities in the U.S. and Mexico ready to take on almost any metal fabricating activity. Within its manufacturing family, it has capability redundancies, ensuring that if a machine is down, another machine tool can pick up the slack. This manufacturing redundancy even includes the ability to bend very large workpieces in heavy-duty press brakes.
The redundancy for bending very big parts, however, didn’t exist for OMS before 2023. That’s a recent development, and one that’s proved to be a real competitive advantage for the company. Not every facility has a 1,100-ton press brake with all of the productivity and safety enhancements of smaller press brakes.
Bulking Up the Bending Department
In 2019, OMS leadership started a conversation about investing in a heavy-duty press brake, one capable of matching the bending power of its 1,250-ton brake in its Pittsburgh-area facility.
“Obviously when you start forming big contracted parts for big customers, they become a little bit more concerned with process redundancy because they want to ensure that you have the capacity to meet their demands and a contingency plan if needed,” said Gus Cassida, regional general manager for OMS.
Cassida is familiar with big brakes because he was plant manager for the OMS facility in Ambridge, Pa., for almost 10 years. The facility has plenty of experience bending materials from 14-ga. sheet to 0.75-in.-thick plate and as long as 22 ft.
One of the main features that OMS needed in a new heavy-duty press brake was an open height of 34 in., because some of the large parts to be bent on the brake had 33-in. legs. Most of the brake manufacturers, however, offered open heights only up to about 28 in.
“Think of a big hat section or a big channel. That’s what we are doing,” Cassida said. “We didn’t want to have to dip the part up in the air to pull it out of the machine. That was very important for us.”
Cassida said that TRUMPF was one of the only press brake manufacturers willing to tweak its machine design to deliver a greater open height than normally might have been available. That, and OMS’ being a long-time customer, helped seal the purchase deal with TRUMPF.
New Bending Efficiencies
OMS installed the TRUMPF TruBend 8010 in late spring of 2023. It’s the largest TRUMPF press brake in the U.S.
“This new press brake gives us great repeatability and accuracy. It’s been massive,” Cassida said.
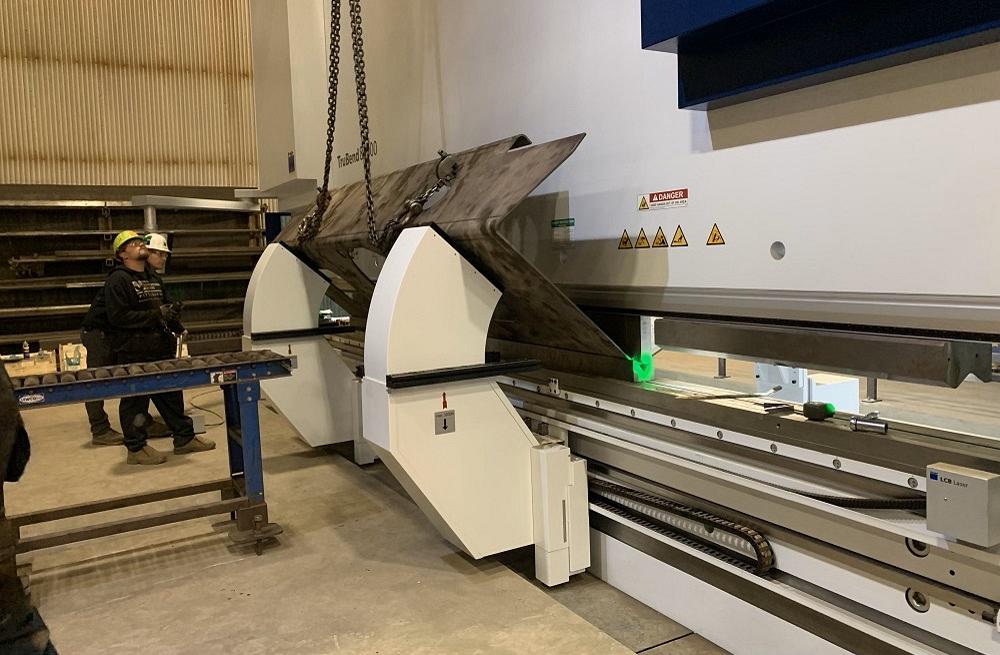
The sheet followers on the new heavy-duty press brake help to make plate handling much more efficient.
One of the biggest areas of technological advancement when compared to OMS’ other heavy-duty press brake has been the new brake’s automatic crowning capabilities. With two large hydraulic cylinders on each end of the press brake driving the ram into the material, the press brake experiences an unequal distribution of force along the die bed. This is especially pronounced in very long parts, such as those bent on the new OMS press brake. Crowning helps to address this disparity.
The brake’s CNC crowning adjustment powers wedge-shaped plates underneath the die bed to create a crowning curve, which applies pressure in the middle to account for the deflection that occurs in the middle of the press beam. There’s no need to apply shims to the tooling to compensate for the crowning and then test those shims on a part. An operator now can place a long part in the brake, bend it, check the part to see what sort of compensation is needed, input the angle changes into the control system, bend the part again, and watch the CNC crowning system make the necessary adjustments.
Cassida said this function is incredibly helpful because a lot of plate processed in the facility is inconsistent from one batch to the next. The material rarely acts the same way when pressure is applied to it.
Assisting this is the brake’s laser angle measurement system. Cassida said that the vast majority of heavy-duty bending activity is air bending. In this type of metal forming, a gap exists between the bottom of the die and the bottom of the material as the ram breaks the plane. The physical properties of plate differ slightly from one batch to another, which makes springback unpredictable from one job to the next. The angle measurement system checks the bend angle after the first hit to see how far off the bend is from the specified angle. The operator then can make the suggested changes to the bending parameters so that the next hit takes into account the springback and gets the bend closer to what’s expected.
The press brake also has a 6-axis backgauge that allows OMS to use the press brake in a much more flexible way than its older heavy-duty brake.
“On our older press bake, we run both the backgauges in parallel. With the new system, we run up and one down with multiple unique setups,” Cassida said.
Now it’s not so unusual to see multiple tooling setups in the big brake. An operator can create a form on one set of tooling, take the part, flip it around, and make a form in another set of tooling. The backgauge, because it’s independent, can provide a different reference point than the other backgauge.
“It’s our most accurate press brake in our portfolio right now,” Cassida said.
With the ability to do multiple setups on the new brake, Cassida added, the operators are working with more segmented tooling. It’s much easier to load and unload than 12-ft. sections of tooling, the latter of which requires a forklift. The segmented tooling also can be changed out more quickly for that very same reason.
“[The segmented tooling] also allows us to replace sections,” Cassida said. “If you buy a 12-ft.-long section and you’re only using 50% of that surface, it’s almost guaranteed that an operator’s going to set that tooling up the same way every time, and he or she will wear out that section of the tool eventually. It’s just human nature.
“With segmented tooling on the new press brake, we can replace certain sections that might wear out.”
Operators Still Matter
Even with all the new brake’s technological advancements, operators remain key to delivering quality bends on a consistent basis. The large, awkward parts particularly need that level of advanced expertise.
These types of jobs are usually done with two operators, according to Cassida. Both are likely to have experience with the older heavy-duty press brake and have certifications to operate cranes and forklifts. That experience plays an important role in keeping them and their colleagues in the immediate area safe.
Maneuvering material of this size is no easy task. The new brake is equipped with sheet followers, which not only support the material in its resting position on top of the die, but also as it rises during the forming process. This greatly improves the ergonomics for the operators.
“The sheet followers have made an unbelievable difference,” Cassida said. “They provide a working surface of about 5 ft., and they give you the ability to put a longer, lighter-gauge sheet up there and handle it easily without the rigidity of form profile that comes after a couple of bends. They’re a game changer.”
The presence of a modern press brake and skilled operators to run it has paid off for OMS. Cassida said the most obvious evidence has been the dramatic reduction in scrap.
For instance, OMS processes a 16-ft.-long, 0.375-in.-thick part several times a week for a customer. Before the part gets to the bending department, it’s plasma-cut and machined. The total processing time is significant, so it’s a very valuable piece of metal by the time it enters the heavy-duty brake.
The new press brake, however, provides the checks and repeatability that keeps those valuable parts out of the scrap bin. Operators don’t have to make educated guesses about crowning or overbending to compensate for springback. The brake addresses those aspects of the process.
“Sometimes it’s hard to change the mindset of people when it comes to processes like press brake bending because people get very comfortable with the equipment they run. That’s why the learning curve was longer than we originally thought with the new machine,” Cassida said. “It wasn’t because the machine’s harder to run. It’s just different.
“But once we started seeing the benefits of it from a repeatability perspective, we saw that it was a game-changer,” he continued. “It’s been a major improvement for us.”
About the Author
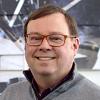
Dan Davis
2135 Point Blvd.
Elgin, IL 60123
815-227-8281
Dan Davis is editor-in-chief of The Fabricator, the industry's most widely circulated metal fabricating magazine, and its sister publications, The Tube & Pipe Journal and The Welder. He has been with the publications since April 2002.
Related Companies
subscribe now
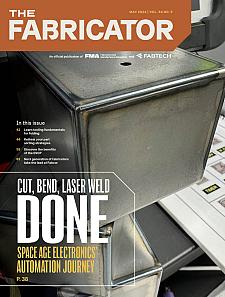
The Fabricator is North America's leading magazine for the metal forming and fabricating industry. The magazine delivers the news, technical articles, and case histories that enable fabricators to do their jobs more efficiently. The Fabricator has served the industry since 1970.
start your free subscription- Stay connected from anywhere
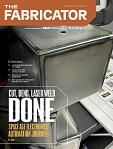
Easily access valuable industry resources now with full access to the digital edition of The Fabricator.
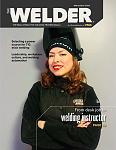
Easily access valuable industry resources now with full access to the digital edition of The Welder.
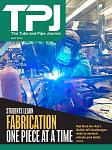
Easily access valuable industry resources now with full access to the digital edition of The Tube and Pipe Journal.
- Podcasting
- Podcast:
- The Fabricator Podcast
- Published:
- 04/16/2024
- Running Time:
- 63:29
In this episode of The Fabricator Podcast, Caleb Chamberlain, co-founder and CEO of OSH Cut, discusses his company’s...
- Trending Articles
Tips for creating sheet metal tubes with perforations
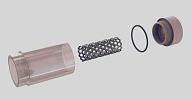
Are two heads better than one in fiber laser cutting?
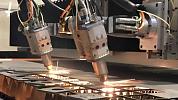
Supporting the metal fabricating industry through FMA
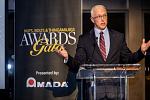
JM Steel triples capacity for solar energy projects at Pennsylvania facility
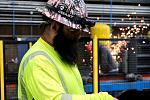
Omco Solar opens second Alabama manufacturing facility
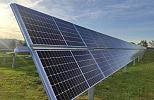
- Industry Events
16th Annual Safety Conference
- April 30 - May 1, 2024
- Elgin,
Pipe and Tube Conference
- May 21 - 22, 2024
- Omaha, NE
World-Class Roll Forming Workshop
- June 5 - 6, 2024
- Louisville, KY
Advanced Laser Application Workshop
- June 25 - 27, 2024
- Novi, MI