Contributing editor
- FMA
- The Fabricator
- FABTECH
- Canadian Metalworking
Categories
- Additive Manufacturing
- Aluminum Welding
- Arc Welding
- Assembly and Joining
- Automation and Robotics
- Bending and Forming
- Consumables
- Cutting and Weld Prep
- Electric Vehicles
- En Español
- Finishing
- Hydroforming
- Laser Cutting
- Laser Welding
- Machining
- Manufacturing Software
- Materials Handling
- Metals/Materials
- Oxyfuel Cutting
- Plasma Cutting
- Power Tools
- Punching and Other Holemaking
- Roll Forming
- Safety
- Sawing
- Shearing
- Shop Management
- Testing and Measuring
- Tube and Pipe Fabrication
- Tube and Pipe Production
- Waterjet Cutting
Industry Directory
Webcasts
Podcasts
FAB 40
Advertise
Subscribe
Account Login
Search
Die fully sensored and still getting miss-hits?
Toolmaker fine-tunes sensor windows to protect dies, cut miss-hits, reduce downtime
- By Kate Bachman
- December 26, 2018
- Article
- Bending and Forming
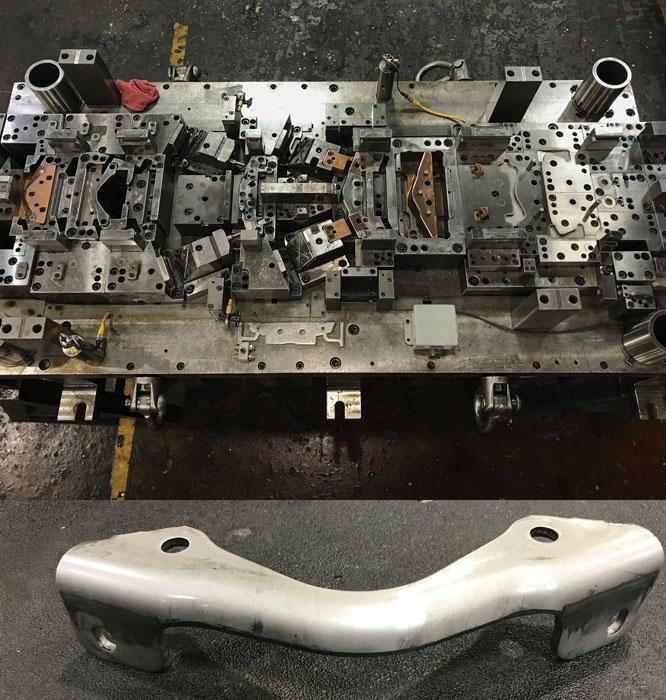
The G.A. Richards Group/Burnside Industries plant was experiencing challenges with miss-hits and misfeeds while stamping an automotive component, even though its die was well-sensored.
The G.A. Richards Group is a mid-sized manufacturer with headquarters and operations in Grand Rapids, Mich. with additional plants in Zeeland and Norton Shores. The company supplies directly to the automotive, aerospace, agriculture, heavy equipment, and medical industry segments.
The G.A. Richards/Burnside Industries plant in Norton Shores was having problems with miss-hits and misfeeds while stamping an automotive component out of ¼-inch-thick stainless steel material, even though its die was well-equipped with sensors (see lead image).
“The die was extremely sensored,” said Brandon Mattson, toolroom lead. “It had two part ejection sensors, a material buckle sensor, an end-of-stock feed sensor, and a short-feed sensor. It was still having miss-hit problems but none of the sensors were firing.
“The material would feed, hit the short-feed sensor at the end of the stock, and push the two parts off, but then it would fall back.”
Mattson said he enlisted the help of “the sensor guy” from the sensor OEM to help the setup crew tweak the program, but was not able to get a satisfactory outcome. When he was able to, Mattson devoted some additional time to investigate the problem.
The company’s setup technician found that the problem started in the feed spring pressure setting. The jobs that usually run in that press are stamped of thin material, so the feeder pressure setting wasn’t right for this thicker material. In the middle of the feed cycle or afterward, the springs would allow the material to bounce back, Mattson relayed.
Brake Test
Mattson said that the toolroom group enrolled in a class offered by Wintriss about its Smart PAC® to understand the sensors and controls settings better.
As per the instructions from the class, they ran a brake test to see how far the die continued after the brake was activated. “So you apply the brake at the most critical point, at 90 degrees, where the ram, with the whole weight of the die, is on its way down. You measure the distance that the ram travels beyond the 90-degree point until it comes to a complete stop. That is the critical stop angle. During stopping, in a worst-case scenario, that’s the farthest the ram will travel when it misses a sensor,” Mattson said.
Adjusting the Window
Mattson decided to try making some adjustments by optimizing the size of the sensor windows during feeding. He changed where the sensors are positioned in the window (see Figure 1).
“That brake test gave us our spread as to how late in the cycle we can position the short-feed sensor.” By making the short-feed sensor window a lot smaller and setting it later in the window, any material slippage would occur before the sensor even began to look for the material, he said.
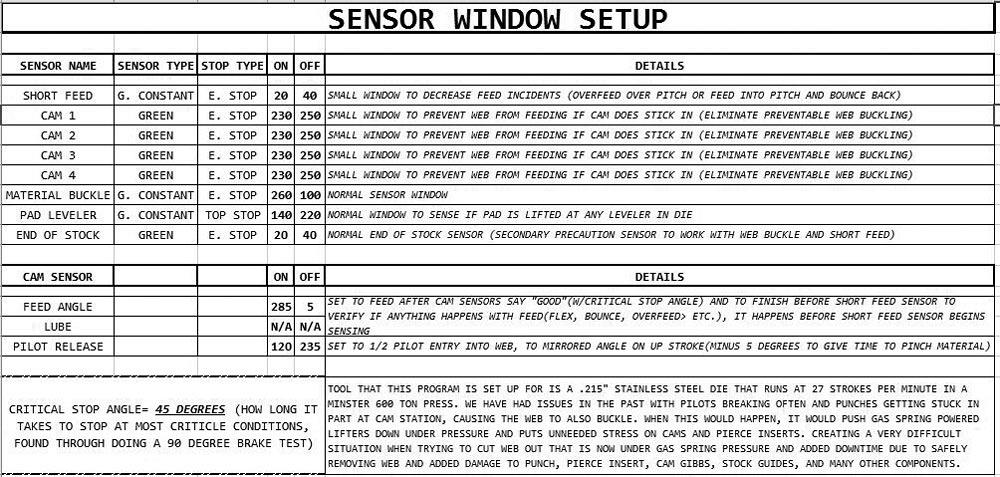
Toolroom Lead Brandon Mattson analyzed where in the sensor window the sensors were positioned and optimized their placement to maximize effectiveness and catch more problems earlier.
“The sensor is positioned so that if the web falls back, it would see that, yeah, the material was here, but it’s not now, so stop.
“So let’s say the part left the pilots completely at 220 degrees. We fed at 235 degrees at a steady rate. But we positioned the sensor so that whatever happened during that feed cycle—whether the material was bouncing off and coming back, skipping over the short feed, or the edge of the last part was out of alignment and nicking the pitch notch—would be done by the time the short-feed sensor started sensing. We set the short-feed sensor to detect the material’s presence as late as possible. Is the steel here? If it’s not, the sensor will stop the ram before it hits the web.”
Mattson and his team were able to resolve the problem as a result.
Die With Cam Punch
Mattson said the team applied the same concept to another, similar problem on a heavy-duty die for a ¼-in. stainless steel part. The die had cam punches with cam return sensors to detect when the punch was out of the part.
“What would happen is we’d have an incident with the lube, or maybe the cam would stick into the material and the web buckled. The guide would be all torqued (down under nitrogen pressure) because it would catch the cam had not returned, but it had already started feeding the web before it stopped the press.
“So it shut it off for the right reason and didn’t damage the die, but it was very hard to cut the web out of the die at that point to get to the punches in the cam to fix the problem,” Mattson said. It was especially difficult because the material was so thick and wound through the die.
Mattson said he thought that he could resolve the problem by being more precise with the sensor windows. “A lot of stampers use a sensor only for its specific function. For example, they use a cam return sensor specifically to make sure the cam is returned before the die hits. That’s it. Well, I want to use the cam sensor to its fullest capabilities, for more than just trying to save that cam. I want to save as much downtime as possible,” he said.
So he set the sensor window as close as possible to the end of the pilot release, reasoning that when the pilots are released, the cam should have returned as well. “It should just be a quick check. Cam’s there. OK. Now you can feed. But if the cam gets stuck and the material is fed a little later, it buys you time. If the cam sensor stops the die, the material doesn’t try to feed it while the punch is stuck in the part,” Mattson said.
“Just that alone on that given project saves 20 to 30 minutes of downtime,” he added.
Applied to All Dies
Mattson surmised that applying this approach—optimizing the sensor window—on every press could save substantial downtime, especially on a die that has a thin web carrier on the outside. Web carriers on a small, gas spring-lifted rail are prone to getting bent and torqued, he said. “Misfeeds just really put a lot of pressure everywhere.”
Optimizing the sensor window so that it catches feed or ejection problems sooner is safer, he said. “It puts less wear and tear on the die. You don’t have all that force exerted on the guide rails or other die components. Because the feeder is going to feed. That material has to go somewhere.
“So, A, you can save the web from buckling; B, save wear and tear on the die; and C, you’re going to catch when the cam is sticking. If it returns late, you want to know that before it’s too late because that means that it’s stuck in the part,” Mattson said.
“So now we saved that one problem. We’ve got 20,000 other ones with dies, just like every shop has,” Mattson added. “The good thing about this sensor window approach is that we can apply it across every die.”
He added, “It’s just about trying to prevent any possible problems by using what’s available to us.”
Photos courtesy of G.A. Richards Group, Norton Shores, MI.
G.A. Richards Group/Burnside Industries, 6830 Grand Haven Road, Norton Shores, MI 49456, 231-798-0064, www.garichards.com
In the March/April issue of STAMPING Journal, Ask the Expert columnist Tom Vacca explains how the pilot sensor works: A spring-loaded pilot is designed into the tool so that if the feed does not feed the material precisely or there is no corresponding pilot hole in the raw material strip because of a short feed, the pilot can retract as the tool is closing without breaking. When the pilot retracts, the sensor senses the head of the pilot in the top die shoe and stops the press. If there is 0.001-in. clearance between the pilot and the pilot hole in the strip, any feed error greater than 0.0005 in. (half the diameter of the difference between the pilot and pilot hole) will activate the stop.
About the Author
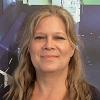
Kate Bachman
815-381-1302
Kate Bachman is a contributing editor for The FABRICATOR editor. Bachman has more than 20 years of experience as a writer and editor in the manufacturing and other industries.
subscribe now
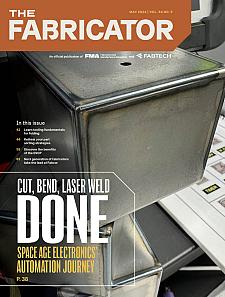
The Fabricator is North America's leading magazine for the metal forming and fabricating industry. The magazine delivers the news, technical articles, and case histories that enable fabricators to do their jobs more efficiently. The Fabricator has served the industry since 1970.
start your free subscription- Stay connected from anywhere
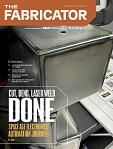
Easily access valuable industry resources now with full access to the digital edition of The Fabricator.
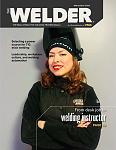
Easily access valuable industry resources now with full access to the digital edition of The Welder.
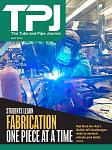
Easily access valuable industry resources now with full access to the digital edition of The Tube and Pipe Journal.
- Podcasting
- Podcast:
- The Fabricator Podcast
- Published:
- 04/30/2024
- Running Time:
- 53:00
Seth Feldman of Iowa-based Wertzbaugher Services joins The Fabricator Podcast to offer his take as a Gen Zer...
- Industry Events
Pipe and Tube Conference
- May 21 - 22, 2024
- Omaha, NE
World-Class Roll Forming Workshop
- June 5 - 6, 2024
- Louisville, KY
Advanced Laser Application Workshop
- June 25 - 27, 2024
- Novi, MI
Precision Press Brake Certificate Course
- July 31 - August 1, 2024
- Elgin,