Director of Smart Manufacturing
- FMA
- The Fabricator
- FABTECH
- Canadian Metalworking
Categories
- Additive Manufacturing
- Aluminum Welding
- Arc Welding
- Assembly and Joining
- Automation and Robotics
- Bending and Forming
- Consumables
- Cutting and Weld Prep
- Electric Vehicles
- En Español
- Finishing
- Hydroforming
- Laser Cutting
- Laser Welding
- Machining
- Manufacturing Software
- Materials Handling
- Metals/Materials
- Oxyfuel Cutting
- Plasma Cutting
- Power Tools
- Punching and Other Holemaking
- Roll Forming
- Safety
- Sawing
- Shearing
- Shop Management
- Testing and Measuring
- Tube and Pipe Fabrication
- Tube and Pipe Production
- Waterjet Cutting
Industry Directory
Webcasts
Podcasts
FAB 40
Advertise
Subscribe
Account Login
Search
Staying connected on the shop floor
How connected worker technology benefits factory safety, productivity, and asset management practices
- By Eric Whitley
- January 15, 2023
- Article
- Automation and Robotics
A smart tablet can be the gateway to all that is happening in a modern metal fabricating facility. yoh4nn/E+
The integration of digital technology in manufacturing, with a focus on automating routine tasks, has improved the quality of operations and products. It’s pivotal in addressing the predominant challenges in the manufacturing sector, helping companies build resilience in fast-changing business environments. Having uninterrupted access to several data streams can help manufacturers keep operations sustainable and maintain competitiveness.
Specifically, connected worker technology is enabling manufacturers to adapt to market volatility and manage complex workflows.
What Is Connected Worker Technology?
Connected worker technology uses digital devices, including computers and hand-held units, to distribute step-by-step work instructions to employees and automate all workflow logging within the facility. This helps improve system autonomy and remote operations for everyone in the organization, from shop floor operators and maintenance technicians to supply chain personnel and executives.
Integrating with such shop technologies as cloud computing, IoT sensors and devices, big data analytics, advanced human-machine interfaces, enterprise resource planning, computerized maintenance management systems, and manufacturing execution systems, connected worker technology enhances data management and optimizes the security of the collected and analyzed data.
In addition to simplifying employee engagement and communication and improving data management, this technology also helps enhance safety in the workplace and improve overall shop productivity and asset management.
Enhanced Workplace Safety
Connected worker technology is beneficial for maximizing safety, health, and environmental standards. It provides avenues for employees to report, track, and rectify safety issues across the facility. It also holds equipment-specific safety information that machine operators and maintenance technicians can access whenever required. Access to safety information reduces the work-execution errors that can lower safety compliance.
Employees throughout the facility have hand-held devices they use to log production tasks. These devices have high-resolution cameras for capturing visual defects on equipment or safety hazards on the factory floor. An operator or technician who identifies a safety hazard—such as a defective machine, fluid leak, spillage, or missing safety sign—can report it by capturing a photo or video and uploading it to the safety management module.
When a safety report is uploaded, the safety supervisor receives an alert to analyze the safety risk and assign teams to resolve the issue. In this way, this method of reporting safety risks ensures prompt resolution of the problems, minimizing production shutdowns and potential workplace injuries.
The connected worker technology platform has a comprehensive safety panel that provides updated standard operating procedures, equipment-specific safety checklists, and prerequisites for safe working conditions. These checklists make it easier for operators and field employees to raise a complaint if anything is amiss. Employees also can conduct remote safety assessments to check compliance standards in their specific working areas.
Safety panels also contain the lockout/tagout documentation required for performing maintenance tasks. Everyone in the facility is aware of scheduled machinery shutdowns and potential power interruptions. With lockout/tagout measures in place, technicians can perform maintenance work without worrying about exposure to hazardous energy or unauthorized machinery startup.
Companies can enhance workplace safety by embedding wearable technology into personal protective equipment (PPE) as well. These wearables have several sensors that monitor worker health and environmental conditions. Production supervisors can use the sensor data to optimize production shifts and minimize the fatigue that could lead to errors and enhanced safety risks.
Sensors that monitor environmental conditions can alert operators to spiking room temperatures, smoke, or gas leaks. They enable employees to rectify defects causing these changes or terminate operations without incurring financial or asset losses. Safety supervisors also can use data from IoT-enabled wearables to monitor PPE usage patterns by employees and ensure they are using the right PPE to perform their duties.
Improved Productivity
One important challenge that manufacturers struggle to address is maximizing productivity. The overall productivity of a facility is determined by both the quality and the quantity of products, and it’s affected by equipment effectiveness and employee contribution. Connected worker technology supplements the reliability of automation systems and streamlines maintenance and production schedules.
Operators use the technical information stored in the connected worker platform to initiate equipment startup correctly and keep a log of assigned duties. They can troubleshoot production errors and perform preproduction checks autonomously. The operators use production dashboards to record productivity over fixed timelines. They record the number of defective parts, nonproductive time, and all the challenges experienced during production.
The operators also can request consumables required during production, such as PPE, repair tools, cleaning detergents, or lubricants. Digitizing these requests enables shop floor employees to track approvals and ensure the timely availability of resources needed to support daily production.
Through connected worker technology, companies can track the productivity of each employee, factory section, or branch. The company monitors real-time performance and production volumes of each production asset. These machines are fitted with condition monitoring sensors and autonomous quality inspection utilities.
The technology ensures the company can track even the slightest deviations in cycle times. The supervisory team then looks into small production stops and finds a long-term solution for continuous improvement.
Companies use connected worker technology to quantify product rejects. They establish a quality verification standard and communicate it to all employees on the production line. They also train the employees to use digital inspection tools and automated production technologies, making it easier and faster for operators to track quality deviations.
Better Asset Management
It is difficult to discuss factory productivity without thinking about asset management. All production assets must be operated within the recommended limits and maintained regularly. Implementing connected worker technology improves asset visibility, extends the useful life of machinery, reduces operational costs, and fosters proactive asset management strategies.
Connected worker technology has a comprehensive equipment manual detailing mandatory maintenance tasks and schedules. It also has up-to-date information regarding different automation technology used on the factory floor. Integrating the technology with a computerized maintenance management system simplifies data collection and the generation of timely maintenance alerts. It also provides standard inspection and repair checklists to ensure precise asset maintenance.
The connected worker platform contains information on spare part requirements for each production asset. Maintenance managers can optimize maintenance inventories to ensure adequate and timely availability of tools and spare parts. This minimizes the deferment of critical maintenance tasks, which can cause unscheduled breakdowns and lower production cycle times. Maximizing asset maintenance optimizes overall equipment effectiveness by ensuring production assets are available, efficient, and reliable.
Companies can enhance asset management by installing IoT sensors on production assets. These smart sensors monitor the real-time performance of production equipment. The sensor collects and sends the data to a centralized data management system for analysis and storage. Maintenance and production managers can pinpoint erratic production cycles.
They can also analyze how specific work procedures impact productivity. The availability of real-time machinery performance data makes it easier for maintenance teams to identify the causes and effects of common asset breakdowns. They use the data to conduct root cause analysis and find a permanent solution to asset failures.
Connected worker technology simplifies communication among different teams on the production line. Maintenance teams can guide operators remotely to perform minor repairs on diverse machinery. Technicians also can review production schedules, filled by operators, to verify that routine preventive measures have been performed.
Senior management can use the data on asset utilization patterns to identify skill needs among employees. They then can develop appropriate training programs and schedules to foster continuous improvement and encourage adherence to standard operating procedures.
Connected worker technology provides adequate resources and technical documentation, required by line operators and maintenance technicians, to keep operations foolproof and standardized. It also ensures maintenance schedules are optimized and adequate stock is available to address both scheduled and emergency asset maintenance.
Summing Up
Implementing connected worker technology in manufacturing ensures a seamless collaboration among employees, production systems, and machinery. It ensures adequate availability of resources and data to drive excellence and maximize productivity.
Companies can easily communicate changes in standard operating procedures, asset bases, safety standards, and automation software by sending regular updates via digital devices. Everyone in the company has access to the data required to make informed production choices. Employees track progress and report issues threatening the quality of routine workflows.
About the Author
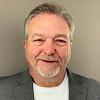
Eric Whitley
299 S. Main St. Suite 1300
Salt Lake City, UT 84111
(877)-225-5201
subscribe now
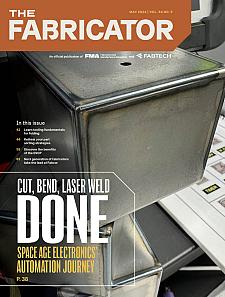
The Fabricator is North America's leading magazine for the metal forming and fabricating industry. The magazine delivers the news, technical articles, and case histories that enable fabricators to do their jobs more efficiently. The Fabricator has served the industry since 1970.
start your free subscription- Stay connected from anywhere
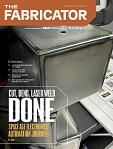
Easily access valuable industry resources now with full access to the digital edition of The Fabricator.
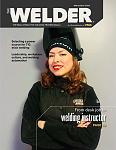
Easily access valuable industry resources now with full access to the digital edition of The Welder.
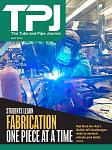
Easily access valuable industry resources now with full access to the digital edition of The Tube and Pipe Journal.
- Podcasting
- Podcast:
- The Fabricator Podcast
- Published:
- 04/16/2024
- Running Time:
- 63:29
In this episode of The Fabricator Podcast, Caleb Chamberlain, co-founder and CEO of OSH Cut, discusses his company’s...
- Trending Articles
Tips for creating sheet metal tubes with perforations
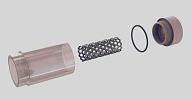
Are two heads better than one in fiber laser cutting?
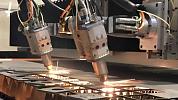
Supporting the metal fabricating industry through FMA
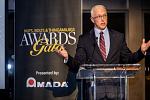
JM Steel triples capacity for solar energy projects at Pennsylvania facility
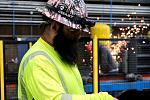
Omco Solar opens second Alabama manufacturing facility
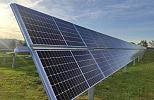
- Industry Events
16th Annual Safety Conference
- April 30 - May 1, 2024
- Elgin,
Pipe and Tube Conference
- May 21 - 22, 2024
- Omaha, NE
World-Class Roll Forming Workshop
- June 5 - 6, 2024
- Louisville, KY
Advanced Laser Application Workshop
- June 25 - 27, 2024
- Novi, MI