Senior Editor
- FMA
- The Fabricator
- FABTECH
- Canadian Metalworking
Categories
- Additive Manufacturing
- Aluminum Welding
- Arc Welding
- Assembly and Joining
- Automation and Robotics
- Bending and Forming
- Consumables
- Cutting and Weld Prep
- Electric Vehicles
- En Español
- Finishing
- Hydroforming
- Laser Cutting
- Laser Welding
- Machining
- Manufacturing Software
- Materials Handling
- Metals/Materials
- Oxyfuel Cutting
- Plasma Cutting
- Power Tools
- Punching and Other Holemaking
- Roll Forming
- Safety
- Sawing
- Shearing
- Shop Management
- Testing and Measuring
- Tube and Pipe Fabrication
- Tube and Pipe Production
- Waterjet Cutting
Industry Directory
Webcasts
Podcasts
FAB 40
Advertise
Subscribe
Account Login
Search
Flexible automation meets structural fabrication
Welding robots spur growth at Lexicon
- By Tim Heston
- Updated May 5, 2023
- December 17, 2022
- Article
- Automation and Robotics
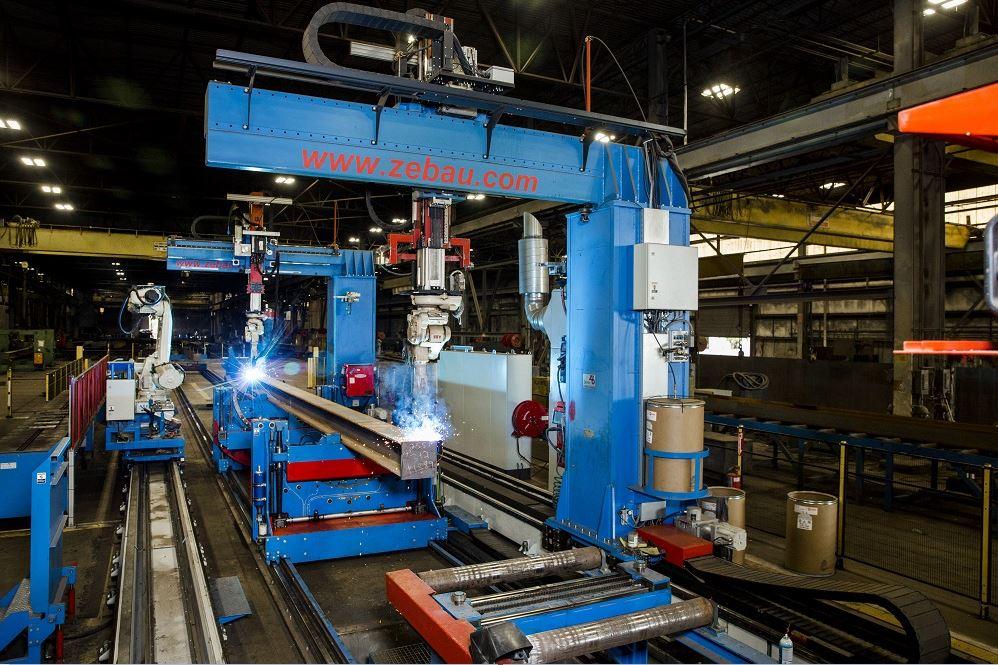
A part-handling and -fitting robot (left) works with the welding robots to tack pieces in place. After that, the welding robots complete the final weld.
In the early 2010s, John Bailey toured numerous structural fabricators in Europe. He was looking to automate welding, and he wanted to see some of the latest and greatest technology in action. Alas, the then president of Little Rock, Ark.-based Prospect Steel, a division of Lexicon, wasn’t impressed. The robotic cells welded just fine, but they had to be programmed. This demanded resources that, as he saw it, would hinder overall throughput.
“The technology wasn’t there yet. But then, just a few years later, we took a trip to Austria and took our 3D structural models with us.”
That was Steve Grandfield, president of the Lexicon Fabrication Group, recalling the tour company executives took in 2015. They visited Zeman Bauelemente, a robotics firm introduced to Lexicon by Peddinghaus. (Peddinghaus is Zeman’s U.S. partner. Lincoln Electric purchased Zeman in April 2021.) Lexicon wanted to take information directly from its 3D structural model (in Tekla Structures BIM software) directly into the software for Zeman’s robotic fitting and welding line.
Several factors hold many structural fabricators back from welding automation. One is the need for programming. Another is the need for processing flexibility. Lexicon Fabrication Group has achieved both and, in doing so, actually increased the number of manual welders, fitters, and assembly personnel it employs. That might seem ironic, considering that the lack of skilled labor is what drives many fabricators to robotics in the first place.
Grandfield attributed the irony to the opportunities Lexicon has gained over the past seven years. Robotics has allowed the fabricator to win work it wouldn’t have otherwise. The structural fabricator’s experience shows just how well skilled manual labor complements robotics. Automation versus manual operation isn’t a zero-sum game. Instead of one eliminating the other, they become more effective together.
Flexible Automation Flow, From Model to Weld
Someone at an OEM or custom fabricator might spend time programming a robot via a teach pendant. The process might be streamlined with offline programming and simulation, followed by a brief program touch-up with the teach pendant. But even if offline programming minimizes robot downtime, someone still needs to sit in front of a computer to program it. That can be problematic for structural fabrication, in which every beam, channel, or hollow structural section (HSS) might have different weld locations and requirements.
Similarly, robotic systems still need operators to wield components, fixture or tack them, and prep them for the robot. And unless the shop has a beam processing system that scribes layout marks, someone needs to mark up the cut beams before they flow downstream.
A shop relying solely on an overhead crane or fork truck to move material—instead of conveyors—might find flow hindered even more. The robot itself can be incredibly productive when it’s running, but too often it just sits idle, waiting for material to arrive.
Lexicon was an early adopter of automatic layout marking. Until 2016, most beams exited the company’s Peddinghaus cutting and drilling machines with marks made by the PeddiWriter system. Once the company turned to robotic welding, though, fewer components required those marks. That’s because the Steel Beam Assembler robotic system by Zeman automates not only the welding but also the fitting and assembly.
The part flow works like this. Beams emerge from the cutting, coping, and drill machines to a conveyor, which feeds all beams downstream. If those beams are destined for robotic welding, conveyors feed them directly to that system. The welding robot scans the beam to locate it and find the zero point.
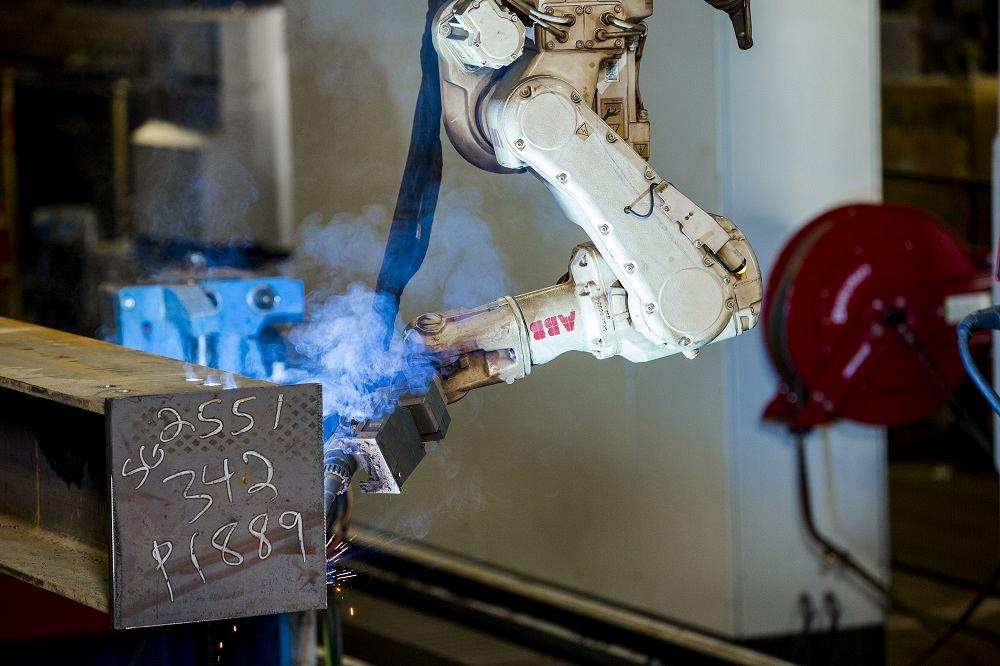
The beam sits on a table that can rotate the work 360 degrees, allowing the robots to access all sides of the workpiece.
Adjacent to this, operators retrieve cut parts from upstream and place them on a table—in no particular order or orientation. They select the job on a nearby computer terminal, after which the assembly robot gets to work. The system scans the workpieces on the table, matching them with the part geometry information gleaned from the 3D model. With its magnetic gripper (one of several magnets the robot uses, depending on the part weight), the part-handling robot grasps the component and carries it to the beam, where it secures the component to the correct location. And because it references the 3D model directly, the robot needs no scribed layout mark.
Just before placing the part, the welding robot scans its intended location and makes any fit-up adjustment required, depending on the beam’s mill tolerances. The welding robot tacks the part in place and, drawing information directly from the 3D model, completes the weld. “The model in Tekla Structures has all the information the robot needs,” Grandfield said, including start and stop location, weld size, and other variables.
The entire beam sits on a rotating table. So, if the robots need to rotate the beam to access a tack or perform the final weld, the table rotates the beam to the required position. From there, the beam exits the system and is conveyed downstream.
In 2018, Lexicon added a dual system in its Blytheville, Ark., plant. That one features one assembly and fitting robot that works with two welding robots on two parallel beam lines (five robots total). The arrangement doubles output and helps balance the cycle times, especially on beams (as well as channels or rectangular or square HSS) with numerous welded components. As the fitting robot and welding robot work together to tack components on one beam, the other welding robot produces the final welds on the other beam.
Flexible Automation in Capacity Planning
Not every job is suitable for welding automation, of course. Some just don’t fit within the systems’ work envelope or are simply too heavy (the systems can’t handle beams more than six tons). Other jobs might not benefit from automated welding, but they would benefit from automated fitting.
“Between 80% and 90% of our jobs could potentially go through the robotic system,” Grandfield said, adding that it can handle a wide variety of work within certain weight and size restrictions, even cambered beams. That said, not all jobs that could go through robotic welding actually do. This, Grandfield explained, has to do with the shop’s capacity planning strategy. Sending everything through robotic welding could create a bottleneck, especially during peak times.
Lexicon might run some beams through automated fitting, then bypass robotic welding and convey them directly to manual welding. Still others are sent only through manual fitting and welding. Which goes where?
As Grandfield explained, that depends on the job and the shop’s current capacity. Beams that fit within the system’s work envelope and require numerous components and a lot of welding are almost always sent through the automation. Meanwhile, jobs that require just a few welded components might be sent directly to manual welding.
It comes down to analyzing the robots’ arc-on time as a percentage of overall cycle time, along with how often the beam needs to be manipulated. The robots will finish a beam with just a few welds very quickly; in fact, the machine might spend more time moving the beam into position than actually welding. On the other hand, a beam that requires multiple welded pieces on different sides—calling for workpiece rotations that, in a manual setting, would need a crane—is a job ripe for automation.
Grandfield added that this all depends on shop capacity at a given moment and, not least, the nature of the work. That said, robotic technology has changed the kind of work Lexicon processes. A lot of this has to do with a different approach to the traditional design compromises made between fabricators and erectors. What’s easy for fabricators can make life difficult for erectors, and vice versa. Robots, however, change the situation.
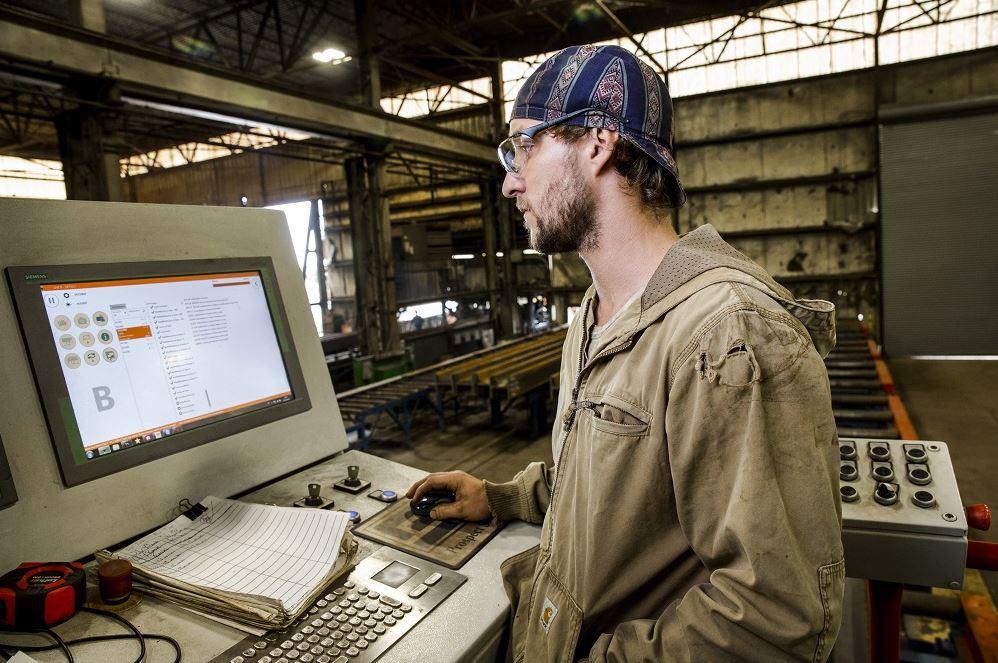
After placing components to be welded on a table, the operator chooses the next job, signaling the system that the work is staged and ready.
“We pride ourselves on our relationships with our erectors,” Grandfield said. “We can plan our engineering and connection design so that it’s not only efficient in the shop but also in the field. There are always some tradeoffs, but the robotic system mitigates many of them.”
For instance, a fabricator might work with detailers and erectors to minimize the number of times the shop needs to flip a beam to access a weld. With automation, though, flipping the beam isn’t an arduous affair.
As Grandfield explained, “Our robotic systems rotate the beam 360 degrees. We can weld on all sides without a crane. When you talk about trying to manually fit, say, a column with 20 pieces versus doing it all with a robot, the savings are quite significant.”
A Competitive Advantage from Flexible Automation
Today, Lexicon has three robotic systems (which incorporate four robotic lines) within its three Arkansas plants. The technology has helped Lexicon gain market share during the e-commerce and warehouse boom, and it has since helped the organization pivot to battery plants, electric vehicle assembly plants, and semiconductor facilities.
The company’s aggressive adoption of technology has spurred a virtuous cycle—and, though it might seem counterintuitive, the cycle really started because Lexicon didn’t throw every job it could at the robotic systems. Instead, the company studied the systems’ strengths (like processing beams with lots of welds and beam rotations) that would help it get the most bang for its automation buck. Then, it developed a dual routing system, one for manually welded projects and another for robotically welded jobs. The routing system balances capacity and helps various elements of a job reach final assembly at roughly the same time.
The company quotes jobs and offers design options that would be far too costly and sometimes outright impractical without robotics. That opens the door for more work, which increases overall volume, including the volume of work that doesn’t fit the robotic system—hence the need for more manual fitters, welders, and assemblers.
“The increased volume has also led us to invest in additional equipment to support our growth, like new plate processing machines and drill lines,” Grandfield said.
Those machines, in turn, need operators to run them and technicians to maintain them. Today, Lexicon Fabrication Group employs about 600 people, and the company continues to hire. Since 2015, its overall capacity has essentially tripled.
Lexicon’s story reveals a misunderstood truth about automation. Yes, it eliminates manual tasks. For instance, fewer people today will spend careers as fitters who apply layout marks by hand. But because automation helps make a fabricator more competitive, it also opens the door to a wide variety of work requiring various skills. That includes manual welding. New opportunity leads to new technology investment—and so the virtuous cycle continues unabated.
About Lexicon
The company’s origins go back to 1968, when Tom Schueck established Scheuck Steel Products in his converted home garage in Little Rock, Ark. Today, Lexicon is a 2,500-plus-employee organization organized under two divisions: Lexicon Fabrication Group and Lexicon Construction Group. The latter provides on-site construction, maintenance, and energy services. The Lexicon Fabrication Group has three fabrication divisions: Prospect Steel Co., Custom Metals, and Steel Fabricators of Monroe.About the Author
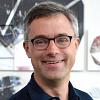
Tim Heston
2135 Point Blvd
Elgin, IL 60123
815-381-1314
Tim Heston, The Fabricator's senior editor, has covered the metal fabrication industry since 1998, starting his career at the American Welding Society's Welding Journal. Since then he has covered the full range of metal fabrication processes, from stamping, bending, and cutting to grinding and polishing. He joined The Fabricator's staff in October 2007.
Related Companies
subscribe now
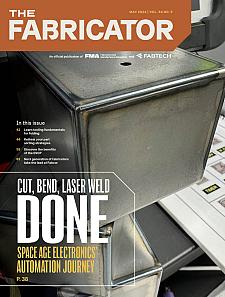
The Fabricator is North America's leading magazine for the metal forming and fabricating industry. The magazine delivers the news, technical articles, and case histories that enable fabricators to do their jobs more efficiently. The Fabricator has served the industry since 1970.
start your free subscription- Stay connected from anywhere
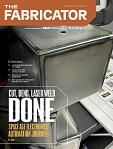
Easily access valuable industry resources now with full access to the digital edition of The Fabricator.
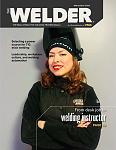
Easily access valuable industry resources now with full access to the digital edition of The Welder.
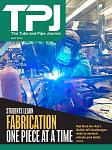
Easily access valuable industry resources now with full access to the digital edition of The Tube and Pipe Journal.
- Podcasting
- Podcast:
- The Fabricator Podcast
- Published:
- 04/16/2024
- Running Time:
- 63:29
In this episode of The Fabricator Podcast, Caleb Chamberlain, co-founder and CEO of OSH Cut, discusses his company’s...
- Trending Articles
Tips for creating sheet metal tubes with perforations
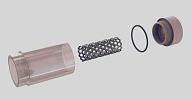
Are two heads better than one in fiber laser cutting?
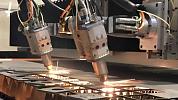
Supporting the metal fabricating industry through FMA
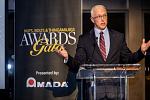
JM Steel triples capacity for solar energy projects at Pennsylvania facility
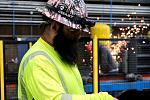
Omco Solar opens second Alabama manufacturing facility
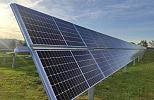
- Industry Events
16th Annual Safety Conference
- April 30 - May 1, 2024
- Elgin,
Pipe and Tube Conference
- May 21 - 22, 2024
- Omaha, NE
World-Class Roll Forming Workshop
- June 5 - 6, 2024
- Louisville, KY
Advanced Laser Application Workshop
- June 25 - 27, 2024
- Novi, MI