Senior Editor
- FMA
- The Fabricator
- FABTECH
- Canadian Metalworking
Categories
- Additive Manufacturing
- Aluminum Welding
- Arc Welding
- Assembly and Joining
- Automation and Robotics
- Bending and Forming
- Consumables
- Cutting and Weld Prep
- Electric Vehicles
- En Español
- Finishing
- Hydroforming
- Laser Cutting
- Laser Welding
- Machining
- Manufacturing Software
- Materials Handling
- Metals/Materials
- Oxyfuel Cutting
- Plasma Cutting
- Power Tools
- Punching and Other Holemaking
- Roll Forming
- Safety
- Sawing
- Shearing
- Shop Management
- Testing and Measuring
- Tube and Pipe Fabrication
- Tube and Pipe Production
- Waterjet Cutting
Industry Directory
Webcasts
Podcasts
FAB 40
Advertise
Subscribe
Account Login
Search
A new kind of skilled workforce
- By Tim Heston
- July 28, 2014
The fear has origins at the very beginnings of the Industrial Revolution, when the first mechanical contraptions allowed fewer people to do more—more harvesting, more manufacturing, more everything. If businesses don’t need as many people, what will happened to those displaced workers?
Although there have been plenty of painful stories about worker displacement, many have found work elsewhere in new industries created by new technologies. So the macroeconomic view has been rosy. The positives of new technologies have far outweighed the negatives.
But according to some, this may be changing. Could high corporate earnings and high employment be the new normal? Many have assumed that displaced workers will find new jobs in newly created industries, but will new technologies always create these industries? Even if they do, will these new industries create enough jobs for all those displaced workers?
When I read about this conundrum, I often think of my mother. For years she was a typesetter for a local print shop. She introduced me to the world of publishing, really. She worked on the cutting edge of 1960s and 1970s technology: a massive typesetting system with a tape drive, and a printer the size of a small bathroom. It was the printing industry’s great leap forward from the linotype.
I still remember the tape drive grinding away, saving the typesetting code. She had mastered a skill after spending years in the typing pools of the1960s office world. And then in came digital publishing and graphic design. From there Mom had two choices: She could learn the new publishing software or return to typing.
She chose typing, mainly because typing was her craft, something she did better than most. I write for a living, and my typing still doesn’t come close. To typeset, you needed to know typing. But graphic design didn’t require high-level typing skills. Mouse clicks replaced keyboard strokes. Graphic design may have been an interesting path, but not one Mom wanted to take.
I see parallels to many other jobs that hinge on technology. A programmer or press brake operator growing up in the industry in the 1970s needed to know G code and a lot of math, and some relished in the detail of it all. They were happy spending their days coding machines, a desirable skill in the early days of numerical control.
Today much of the math is automated. You have graphical user interfaces on press brakes and automated nesting for lasers and punch presses. Where did those early NC programmers go? What path did they choose, and was that new path rewarding?
People say manufacturing needs craftspeople, those detailed-oriented technical wizards. But outside a few jobs, like manual welding or a technician operating an old press brake, technology has taken over much of the detail.
If you’re happiest working with a machine, you may become a supervisor, set up machines, and become the go-to person for all things surrounding that machine, be it a press brake or anything else. As an entry-level operator, your job description depends on your employer and its practices, but at times it may involve a lot of loading, unloading, and pushing buttons. It’s easier and more efficient for part flow, but for the person who grows up loving the mechanical things in life, is it more enjoyable?
Perhaps not. So they go to work, push buttons, and then go home. Do they eventually rise through the ranks to become a supervisor, broaden your skills? Maybe, but maybe not. So how does industry tap the minds of those engaged, the people with positive attitudes and with a willingness to learn and grow?
Lean manufacturing does this, which I suppose is why I like writing about and visiting companies that have gone down the lean path. The company may use machines that make the task of actually making things easier, but everyone remains engaged and excited, because they’re managing how those parts flow, and they realize how important they are in that whole process.
They’re not just pushing buttons. In manufacturing, at least, lean has a place for the worker who is curious and engaged—two attributes that won’t be displaced by technology anytime soon.
subscribe now
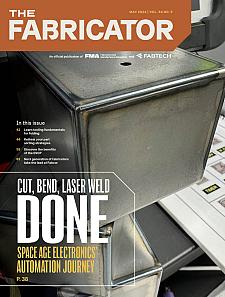
The Fabricator is North America's leading magazine for the metal forming and fabricating industry. The magazine delivers the news, technical articles, and case histories that enable fabricators to do their jobs more efficiently. The Fabricator has served the industry since 1970.
start your free subscriptionAbout the Author
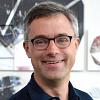
Tim Heston
2135 Point Blvd
Elgin, IL 60123
815-381-1314
Tim Heston, The Fabricator's senior editor, has covered the metal fabrication industry since 1998, starting his career at the American Welding Society's Welding Journal. Since then he has covered the full range of metal fabrication processes, from stamping, bending, and cutting to grinding and polishing. He joined The Fabricator's staff in October 2007.
- Stay connected from anywhere
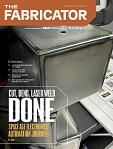
Easily access valuable industry resources now with full access to the digital edition of The Fabricator.
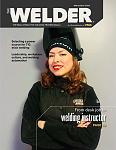
Easily access valuable industry resources now with full access to the digital edition of The Welder.
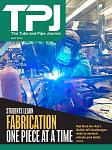
Easily access valuable industry resources now with full access to the digital edition of The Tube and Pipe Journal.
- Podcasting
- Podcast:
- The Fabricator Podcast
- Published:
- 04/16/2024
- Running Time:
- 63:29
In this episode of The Fabricator Podcast, Caleb Chamberlain, co-founder and CEO of OSH Cut, discusses his company’s...
- Industry Events
16th Annual Safety Conference
- April 30 - May 1, 2024
- Elgin,
Pipe and Tube Conference
- May 21 - 22, 2024
- Omaha, NE
World-Class Roll Forming Workshop
- June 5 - 6, 2024
- Louisville, KY
Advanced Laser Application Workshop
- June 25 - 27, 2024
- Novi, MI