Editor-in-Chief
- FMA
- The Fabricator
- FABTECH
- Canadian Metalworking
Categories
- Additive Manufacturing
- Aluminum Welding
- Arc Welding
- Assembly and Joining
- Automation and Robotics
- Bending and Forming
- Consumables
- Cutting and Weld Prep
- Electric Vehicles
- En Español
- Finishing
- Hydroforming
- Laser Cutting
- Laser Welding
- Machining
- Manufacturing Software
- Materials Handling
- Metals/Materials
- Oxyfuel Cutting
- Plasma Cutting
- Power Tools
- Punching and Other Holemaking
- Roll Forming
- Safety
- Sawing
- Shearing
- Shop Management
- Testing and Measuring
- Tube and Pipe Fabrication
- Tube and Pipe Production
- Waterjet Cutting
Industry Directory
Webcasts
Podcasts
FAB 40
Advertise
Subscribe
Account Login
Search
Howe brothers discover precision fabrication
The Discovery Channel reality stars use waterjet cutting to produce their specialty vehicles
- By Dan Davis
- April 1, 2011
- Article
- Waterjet Cutting
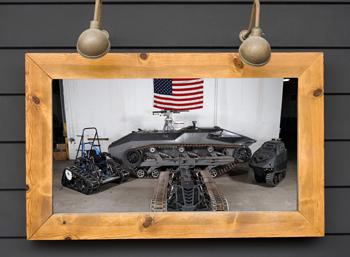
Figure 1: The Ripsaw unmanned tank has inspired many other Howe & Howe Technologies extreme vehicles, such as (clockwise) the Ripchair, an off-road wheelchair; the Riptide, an amphibious version of the Ripsaw; the PAV 1 or Badger, the world’s smallest armored all-terrain vehicle; and the Mini Rip, a miniature Ripsaw for the consumer looking for a unique off-road adventure.
How are fabricators made? The Howes are fabricators made from natural inquisitiveness, tireless enthusiasm, and keen intellect. No formal fabricating training was needed.
More specifically, twin brothers Michael and Geoff Howe are the stars of Discovery Channel's "Black Ops Brothers: Howe & Howe Tech," which documents the activities of the brothers' Waterboro, Maine, shop as it fabricates extreme vehicles for military, law enforcement, and private-sector customers.
They got their big start when their track-based, unmanned tank, dubbed the Ripsaw, was one of three finalists for the 2006 Defense Advanced Research Projects Agency (DARPA) Grand Challenge. When the vehicle made its appearance in the finals at the Washington, D.C., Auto Show, Armament Research, Development, and Engineering Center officials noticed. A few months later, the Howes were making military prototypes for the Department of Defense, and five years later they continue to work on manned and unmanned military models.
In fact, that early work has inspired other vehicles (see Figure 1). The design, fabrication, and testing of these vehicles are covered on the cable series, which is in its second year.
The brothers' work is more than just a cable curiosity, however, because business is expanding. Howe & Howe Technologies now employs 25 and likely will be expanding later in 2011 as more military contracts are awarded.
Perhaps most interesting is how the Howes got to this point. It's less about a structured industrial technology curriculum and more about the simple fact that they were always interested in how things worked.
How's It Done?
"At 5, 6, 7 years old, we were always taking things apart. We were always doing some experimentation," said Mike Howe, who is the company's president. "For some reason—we don't really know why today—we wanted to know why things worked."
To assist in the mechanical mutilation of bikes and toasters, the brothers invested their weekly $1.50 allowance in the basic tools of creative destruction—hammers, screwdrivers, and nails. More formal fabrication tools entered the picture around age 9 when $65 checks showed up from their grandfather for Christmas; instead of toys, the boys purchased a circular saw and a jigsaw. Soon afterward the boys created their first robotic arm out of bicycle parts. At age 16, they started tinkering with vehicles.
Even with their interest in automobiles and fabricating, the Howes didn't shy away from hitting the textbooks. They finished near the top of their class at the prestigious Kents Hill School, taking advanced placement courses while there. Mike eventually graduated from Bowdoin University, where he worked on independent study projects sponsored by NASA and the National Oceanic and Atmospheric Administration. Geoff attended the University of Maine for a couple of years, worked on fishing boats, and wound up working as the chief plant operator at the water treatment plant in Portsmouth, N.H.
In 1996 the twin brothers also were playing in a band called Two Much Trouble. This is when the duo really began their foray into building customized "extreme" vehicles. The Howes converted an old school bus into a movable stage. When it pulled up for a performance, hydraulics lowered one of the bus's walls to create a stage.
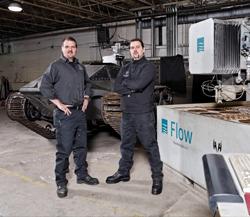
Figure 2: Geoff and Mike Howe stand beside their new waterjet, which has helped the Howe & Howe Technologies team to expedite fabrication of its vehicles.
That led to more vehicle development, particularly "nasty rock-crawling rigs," as Mike described it. All during this time they had to maintain full-time jobs to fund their hell-raisin' hobby.
"It's so hard to make money in the fabrication business. You have to find a niche. You just can't go to a bank and tell them you want to start building extreme vehicles," said Mike. "They'll say, 'Who's your client?'"
The clients eventually found the Howe brothers when military officials noticed the outside-of-the-box thinking in the Ripsaw. Unlike typical tanks, it is quick and nimble, traveling up to 60 MPH and traversing uneven terrain as if it were on an open road. The Ripsaw has a completely new track system, which is patent-pending, that is totally unlike traditional pin-and-bushing systems used to connect treads on modern tanks—and happens to weigh about 90 percent less than similarly scaled tank cleats. To keep the tracks taut as the suspension compresses, the brothers introduced a spring-loaded wheel at the front of the track mechanism that extends to keep the tracks from slipping. They invented a clutching system that is able to handle 14,000 ft.-lbs. of torque in a much smaller package than a typical electric magnetic clutch requires.
This wasn't a backyard fabricator's attempt at creating a new monster truck. This was a monster effort that trucked competing vehicle designs and led to some high-profile work.
"Once you start turning heads, it's a matter of people not caring what our background is or where we come from. The proof is in the pudding," Mike said.
How Can It Be Done Better?
When Howe & Howe Technologies first started fabricating these types of vehicles, it had only a welding table. The real advancement came in 2006, when the brothers purchased their first CNC plasma cutting machine.
Not satisfied with simply using the plasma table to cut 2-D metal, Mike and Geoff set forth trying to streamline the "art-to-part" process. They spent time trying to develop a plug-in for the CNC to accept G code from SolidWorks®, which would allow the plasma table to cut tube. When they finally finished, they had developed a method of converting CAD data to G code and used it to "convince" the plasma table that it was cutting flat even as it was cutting a tube attached to a spinning chuck.
"Take out a pipe that has a five-way intersection, a massively complicated fish mount, and it would take a week to get the cuts right the old-school way," Mike said. "I now can have that cut out in the right length, very accurate when it's cutting round."
But the parts weren't accurate enough. The Howe & Howe team had to grind down the slag by hand on the plasma-cut parts. The removal of extra material during grinding and the warpage of material during the cutting process led to parts that didn't meet the exact tolerances of the original design.
"The amount of hours spent reworking things or jigging the material up to counteract warpage wasted a lot of time and made the work more difficult," said engineer Josh Spaulding.
An episode of "American Chopper" changed the staff's thinking. They saw a waterjet in action and knew it could do a better job.
"As soon as I saw it in action, I knew I wanted to work with one," said Tyler Hentz, the shop's fabrication manager.
They selected Flow's Mach 3 2513b with an 8- by 4-ft. cutting table (see Figure 2). The waterjet came with a Dynamic Waterjet® cutting head, which is designed to counter waterjet stream lag and taper. The head tilts to the side during cutting to eliminate the taper and forward to control the stream. The result is parts that meet tolerances as tight as 0.001 to 0.003 in.
"You don't need complicated jigs and complicated measuring tools," Mike said. "You can just snap it together."
Such precisely cut tubes can make a great difference in assembling something like the brothers' SR-1 mining vehicle, which has about 350 tubes. Now that chassis can be designed so that just one person can assemble it with minimal holding jigs, instead of the three to four previously required.
Mike added that they still are trying to push the envelope in streamlining the art-to-part process, even with the new waterjet. They aren't through tinkering.
How's It Going to Work in the Future?
That goes for the vehicle design as well. In fact, that's what they want to do—be full-time researchers and developers. The Howes aren't interested in becoming full-blown manufacturers of metal products.
Having the waterjet table helps Howe & Howe Technologies accomplish that goal. In addition to cutting hardened and stainless steel, the company now can cut bulletproof glass, Lexan®, high-density polyurethane, wood, and even soft materials such as gaskets.
"The ultimate plan for us is simple: It's R&D for the rest of our lives," Mike said.
The Howes entered metal fabrication on their own terms. It makes sense that they should make a living doing it their own way as well.
Howe & Howe Technologies Inc., 661 Main St., Waterboro, ME 04087, 207-247-2777, www.howeandhowetechnologies.com
Flow International Corp., 23500 64th Ave. S., Kent, WA 98032, 253-850-3500, www.flowwaterjet.com
About the Author
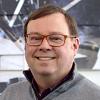
Dan Davis
2135 Point Blvd.
Elgin, IL 60123
815-227-8281
Dan Davis is editor-in-chief of The Fabricator, the industry's most widely circulated metal fabricating magazine, and its sister publications, The Tube & Pipe Journal and The Welder. He has been with the publications since April 2002.
Related Companies
subscribe now
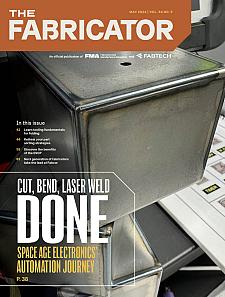
The Fabricator is North America's leading magazine for the metal forming and fabricating industry. The magazine delivers the news, technical articles, and case histories that enable fabricators to do their jobs more efficiently. The Fabricator has served the industry since 1970.
start your free subscription- Stay connected from anywhere
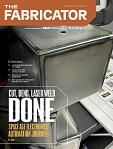
Easily access valuable industry resources now with full access to the digital edition of The Fabricator.
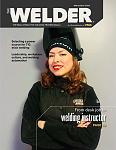
Easily access valuable industry resources now with full access to the digital edition of The Welder.
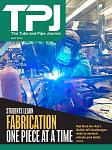
Easily access valuable industry resources now with full access to the digital edition of The Tube and Pipe Journal.
- Podcasting
- Podcast:
- The Fabricator Podcast
- Published:
- 04/16/2024
- Running Time:
- 63:29
In this episode of The Fabricator Podcast, Caleb Chamberlain, co-founder and CEO of OSH Cut, discusses his company’s...
- Industry Events
16th Annual Safety Conference
- April 30 - May 1, 2024
- Elgin,
Pipe and Tube Conference
- May 21 - 22, 2024
- Omaha, NE
World-Class Roll Forming Workshop
- June 5 - 6, 2024
- Louisville, KY
Advanced Laser Application Workshop
- June 25 - 27, 2024
- Novi, MI