- FMA
- The Fabricator
- FABTECH
- Canadian Metalworking
Categories
- Additive Manufacturing
- Aluminum Welding
- Arc Welding
- Assembly and Joining
- Automation and Robotics
- Bending and Forming
- Consumables
- Cutting and Weld Prep
- Electric Vehicles
- En Español
- Finishing
- Hydroforming
- Laser Cutting
- Laser Welding
- Machining
- Manufacturing Software
- Materials Handling
- Metals/Materials
- Oxyfuel Cutting
- Plasma Cutting
- Power Tools
- Punching and Other Holemaking
- Roll Forming
- Safety
- Sawing
- Shearing
- Shop Management
- Testing and Measuring
- Tube and Pipe Fabrication
- Tube and Pipe Production
- Waterjet Cutting
Industry Directory
Webcasts
Podcasts
FAB 40
Advertise
Subscribe
Account Login
Search
TUBE® expo exhibitors demonstrate the latest equipment for monitoring dimensions
Choices abound for tube and pipe producers, fabricators to help achieve, maintain tight tolerances, consistency
- By Eric Lundin
- June 9, 2014
- Article
- Testing and Measuring
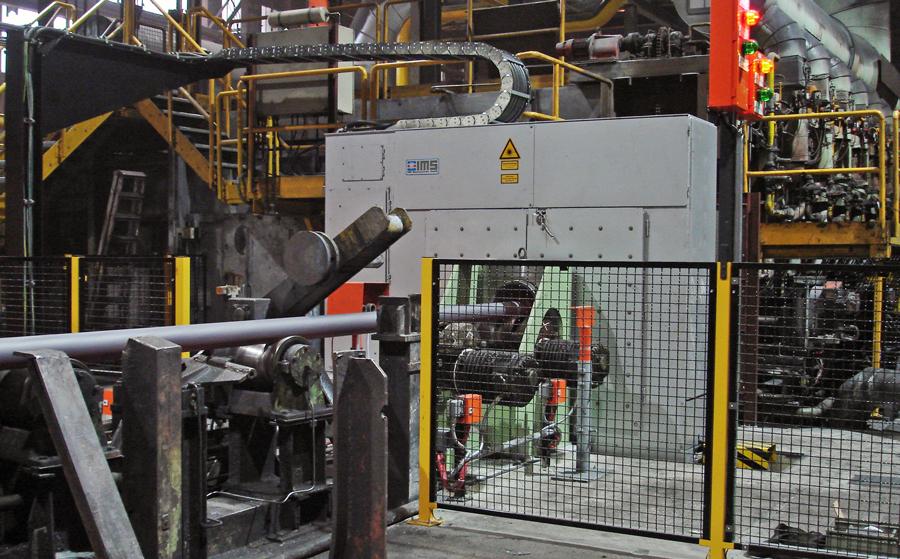
IMS Messsysteme manufactures systems equipped with five, nine, or 13 pairs of transmitters and receivers to measure seamless products.
For tube or pipe manufacturers and fabricators, few issues are more challenging than maintaining consistent dimensional accuracy. The demands for tighter tolerances and rock-solid consistency are relentless for myriad applications. High-volume industries like automotive and highly regulated industries like aerospace and nuclear power demand tight tolerances to meet their goals. Oil and gas applications require minimum ovality for successful threading and square end faces for coupling integrity. Hollow structural sections used in construction projects and oil rigs must meet various strength and bend stiffness specifications.
Proper equipment setup and frequent maintenance are critical steps, but don’t guarantee consistency. Among tube and pipe producers, competitive pressures mean doing more with less at the highest possible line speeds. For fabricators, tooling setup can vary from operator to operator. Even if the equipment is in topnotch condition, the metal’s characteristics vary from heat to heat, so maintaining consistent dimensions—diameter, wall thickness, ovality, and straightness—is an unending challenge.
Keeping up with these demands is a matter of keeping up with the latest monitoring and measuring technologies, several of which were on display at the recent TUBE® expo in Düsseldorf, Germany.
Monitoring Welded and Seamless Hollows
Tube wall thickness consistency carries a lot of weight with tube and pipe producers. Walls that are too thin are prone to rejection by the customer or premature failure if they are put into use. Walls that are too thick cut into profitability. Diameter measurements likewise are critical.
IMS Messsysteme GmbH’s C-frame and O-frame measuring systems use a radiation source (cesium 137) and up to 13 pairs of transmitters and detectors to provide dimensional measurements on seamless tube and pipe. The tube wall absorbs some of the radiation; the receiver detects and measures the residual amount. The system uses the difference between the transmitted and received signals to calculate the wall thickness.The systems detect typical wall thickness variations associated with each mill type:
- A round but eccentric ID, associated with piercer mills and presses
- An oval-shaped or four-lobed (cloverleaf) ID, associated with conventional multistand pipe mills (two-roll type rolling stands)
- A three- or six-lobed (hexagonal) ID, associated with premium quality finishing (PQF®) mills, fine quality mills (FQM®), push benches, and sizing mills (three-roll type rolling stands)
The system works on diameters from 5⁄8 in. to 30 in. and wall thicknesses up to 2 in.; temperatures up to 2,375 degrees F; and line speeds up to 50 ft. per second. It achieves wall thickness accuracy less than ± 0.3 percent and tube diameter accuracy less than ± 25 µm.
Customized tube measuring gauges, manufactured by IMS, have the ability to combine all dimensional parameters of the pipe, such as wall thickness, eccentricity, diameter, ovality, out-of-roundness, and length. These gauges can also be integrated with diameter measurement systems manufactured by LIMAB.
LIMAB®’s TubeProfiler™ uses laser technology to measure round, square, and rectangular products, hot or cold, welded or seamless. The system uses 36 synchronized lasers and a patented algorithm that prevents workpiece movement from affecting the measurements. The system uses triangulation to determine the minimum, maximum, and average diameter; ovality, length, and straightness; and to find defects such as flat spots.
A pyrometer measures the tube or pipe temperature for hot to cold conversion, and an optional Doppler laser measures the tube length and displays defect locations. The TubeProfiler S model has two additional measurement planes, and uses four to eight sensors in each plane, to measure the dimensions of the tube ends, partial sections, or the entire tube.
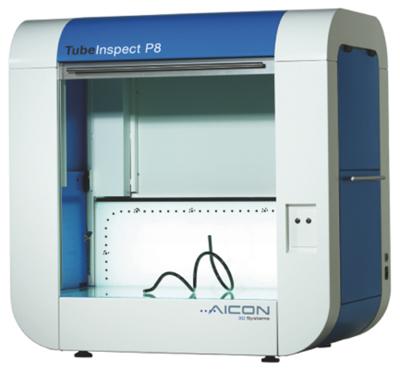
A key development in Aicon’s TubeInspect P8 is the measurement bed, which is a sheet of glass with reference markers. The glass provides a stable measuring surface, and the markers provide permanent reference points for the eight cameras, alleviating the need for an initial calibration.
The systems work on diameters from ¾ in. to 8 ft. and take up to 2,000 measurements per second. The accuracy is ±0.04 in. at 2σ.
Meta Vision Systems’ pipe end measurement system (PEMS) uses two SLS100LR sensors, mounted at 45 degrees to the pipe surface 90 degrees to each other, to scan around the end of the tube or pipe. One sensor measures the OD surface, the other measures the ID surface, and both measure the end face to build a 3-D model of the pipe end. The user sets the scan spacing in fractions of a degree.
The scanned area is about 4 in. of pipe length and assesses diameter (minimum, maximum, and average), ovality, and end face squareness. The system is sensitive enough to display information stenciled onto the pipe by measuring the thickness of the paint used in the stenciling process.
Working With Tailor Rolled Blanks
Nowhere is the pace of manufacturing technology more evident than in the automotive industry, as manufacturers deal with two opposing mandates: reduce weight and maintain (or improve) crashworthiness. Tailored blanks perform a minor miracle in that they provide varying part thickness, allowing OEMs to specify thin material where weight reduction matters most and thick material where part strength matters most. A U-channel with two thicknesses is a typical tailored part, but much more complex parts are possible, such as a B-pillar with eight distinct thicknesses.
Tailor rolled tube also has a small but critical niche in the automotive industry. For fabricators who work with tailor rolled tube, a primary challenge is proper part orientation, for example when loading the part into a bending machine, said Walter Hölsch, sales manager for Roland Electronic GmbH.
“The thickness difference can be small, often less than a millimeter,” Hölsch said. Rather than rely on a machine operator in a hurry to measure the wall thicknesses with a caliper—a time-consuming process at best—he simply inserts the tube into the company’s E20 unit, which uses a magnetic system to measure the wall thickness.
Measuring Bent Tube
AICON 3D Systems GmbH has been developing manufacturing and upgrading camera-based measurement systems since it was founded in 1990. A typical application is an automotive brake line or fuel line, a long length of small-diameter tubing with a handful of bendsand straight sections.
The latest version of its flagship machine, TubeInspect, was rolled out this year. The new machine is a complete overhaul of a concept that has been in use more than a decade. In addition to a more modern look, the latest version was designed for improved ergonomics and has a simplified interface. It also is equipped with LED lamps for more uniform illumination and higher-resolution cameras, upgraded from 1.3 megapixels to 2.0 megapixels.
The software uses sophisticated algorithms that compensate for temperature fluctuations and, in the case of measuring long, thin-walled workpieces, compensates for sagging caused by gravity. The system also sends bend correction information to the bender, taking into consideration all of the bends and straights along the entire length of the part.
“The worst thing is sending information to the bender to correct one small area,” said Werner Boesemann, president and CEO. “Changing one bend can throw off the rest of the shape, so this system relies on a full set of bend measurements.”
The company also rolled out its latest system, TubeInspect P8, which has a measurement area of 40 by 23.6 by 15.75 in. and can measure diameters up to 5 in. Boesemann estimates that this measurement envelope encompasses more than 80 percent of all tubing bent for manufactured products. Boesemann added that the machine isn’t limited to tubes that measure 40 in. long. Doors at both ends of the machine fold down so that longer tubes can be fed into it and measured section by section.
The machine is intended to be affordable for manufacturers that don’t have a full production schedule, Boesemann said. At 530 lbs., the system is designed to be portable.
Conclusion
Manufacturers keep finding more uses for tube and pipe, and the finished products continue to become more sophisticated. Premium threads, intricate bends, and complex end forms will continue to challenge producers and fabricators to make products to increasingly tight standards. As OEMs continue to push the envelope, their suppliers will have to do what they can to keep up. A visit to an all-encompassing expo like TUBE is a way to keep current with the latest monitoring and measuring technologies.
About the Author
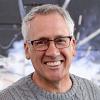
Eric Lundin
2135 Point Blvd
Elgin, IL 60123
815-227-8262
Eric Lundin worked on The Tube & Pipe Journal from 2000 to 2022.
About the Publication
subscribe now
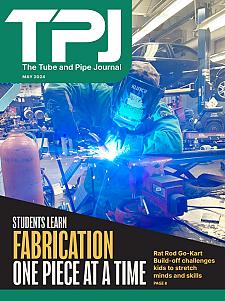
The Tube and Pipe Journal became the first magazine dedicated to serving the metal tube and pipe industry in 1990. Today, it remains the only North American publication devoted to this industry, and it has become the most trusted source of information for tube and pipe professionals.
start your free subscription- Stay connected from anywhere
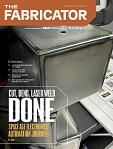
Easily access valuable industry resources now with full access to the digital edition of The Fabricator.
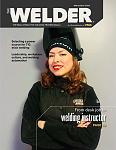
Easily access valuable industry resources now with full access to the digital edition of The Welder.
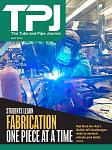
Easily access valuable industry resources now with full access to the digital edition of The Tube and Pipe Journal.
- Podcasting
- Podcast:
- The Fabricator Podcast
- Published:
- 04/16/2024
- Running Time:
- 63:29
In this episode of The Fabricator Podcast, Caleb Chamberlain, co-founder and CEO of OSH Cut, discusses his company’s...
- Trending Articles
Zekelman Industries to invest $120 million in Arkansas expansion
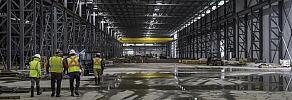
3D laser tube cutting system available in 3, 4, or 5 kW
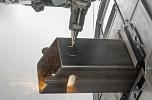
Corrosion-inhibiting coating can be peeled off after use
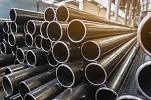
Brushless copper tubing cutter adjusts to ODs up to 2-1/8 in.
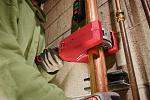
HGG Profiling Equipment names area sales manager
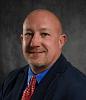
- Industry Events
16th Annual Safety Conference
- April 30 - May 1, 2024
- Elgin,
Pipe and Tube Conference
- May 21 - 22, 2024
- Omaha, NE
World-Class Roll Forming Workshop
- June 5 - 6, 2024
- Louisville, KY
Advanced Laser Application Workshop
- June 25 - 27, 2024
- Novi, MI