Contributing editor
- FMA
- The Fabricator
- FABTECH
- Canadian Metalworking
Categories
- Additive Manufacturing
- Aluminum Welding
- Arc Welding
- Assembly and Joining
- Automation and Robotics
- Bending and Forming
- Consumables
- Cutting and Weld Prep
- Electric Vehicles
- En Español
- Finishing
- Hydroforming
- Laser Cutting
- Laser Welding
- Machining
- Manufacturing Software
- Materials Handling
- Metals/Materials
- Oxyfuel Cutting
- Plasma Cutting
- Power Tools
- Punching and Other Holemaking
- Roll Forming
- Safety
- Sawing
- Shearing
- Shop Management
- Testing and Measuring
- Tube and Pipe Fabrication
- Tube and Pipe Production
- Waterjet Cutting
Industry Directory
Webcasts
Podcasts
FAB 40
Advertise
Subscribe
Account Login
Search
Servo press trends
Twins, heat, high-torque, controls, energy converge to contort Olympian-strength metals
- By Kate Bachman
- September 21, 2016
- Article
- Bending and Forming

A hot metal blanked part is being transferred from the oven to a servomechanical press. Photo courtesy of FAGOR Arrasate USA Inc., Willowbrook, Ill.
Automakers have made great strides over the last few years in reducing vehicular weight to meet corporate average fuel economy (CAFE) standards (see Figure 1) while also retaining—and even exceeding—U.S. National Highway Traffic Safety Administration- (NHTSA-) required levels for safety—a skillful balancing act if there ever were one. Aerospace OEMs have been working to achieve lightweighting for fuel efficiency as well.
The weight reductions have largely been attributed to the use of advanced high-strength (AHS) materials—and the stamping manufacturers forming them.
Not only are these materials vulnerable to springback, tearing, and wrinkling, they increase stress on blanking and forming presses and auxiliary equipment; create high-impact shock vibrational waves that produce cracks on dies and press seams; and increase press and tool deflection.
Stampers have muscled the Olympian feat of forming AHS metals via many approaches, including using servo-driven mechanical presses.
Four servo press manufacturers were consulted on how servo press technology has advanced to spot stampers to help them meet the challenges inherent in forming super-strong metals with low formability and high work hardening. According to AIDA-America, Dayton, Ohio; Nidec Minster, Minster, Ohio; Schuler Inc., Canton, Mich.; and FAGOR Arrasate, Willowbrook, Ill., AHS materials require presses with higher tonnage and energy than those with lower tensile strengths. They point to servo presses’ ability to supply high energy at low speeds; slow during forming, then accelerate in the nonproductive portion of the stroke; restrike without an extra die station; and vary stroke heights on-the-fly make them well-suited for the task.
1 How is servo press technology evolving to help meet stamping manufacturers’ challenges? What have you done with the technology that is new?
Barry Lewalski, sales and product manager for servo press systems, Schuler Group: Schuler recently introduced its twin servo technology (see Figure 2). The drive unit is no longer located in the crown but, rather, is under the press. The draw rods apply the press force to the slide’s end faces, pulling the slide down. This allows greater eccentric loads, and the maximum press force can be applied right up to the bed edge. In conjunction with the play-free guides, this not only improves the precision of the manufactured parts, but also significantly enhances process reliability and prolongs die life.
In addition, the externally mounted draw rods ensure that the press can handle greater forces in individual stations, as well as significantly greater off-center loading capability in the press die area.
Twin servo technology offers increased die configuration flexibility as well. It has high resistance to slide tilting, which increases stability and reduces springback. This results in increased output and part quality. The high rigidity and low deflection of the overall system reduce the effects of a snap-through, which in turn makes the press quieter. Because it has no crown, the overall press height of the twin servo press is lower.
In addition, we introduced ourIntraFeed transfer system (see Figure 3). The grippers responsible for transporting the parts are not mounted on rails but on movable carriages with their own drive units. This significantly reduces the length of the transfer rails and, thus, of the entire line.
One positive side effect is that having less mass to move results in higher output performance. Thanks to these movable carriages, the forming stations can be arranged in variable distances from each other. This opens up new possibilities in die design, because more forming stations can be accommodated in the press bed. It is feasible, for example, to serve the individual cutting and subsequent forming stations with separate carriages. This allows the gaps between each station to be arranged optimally.
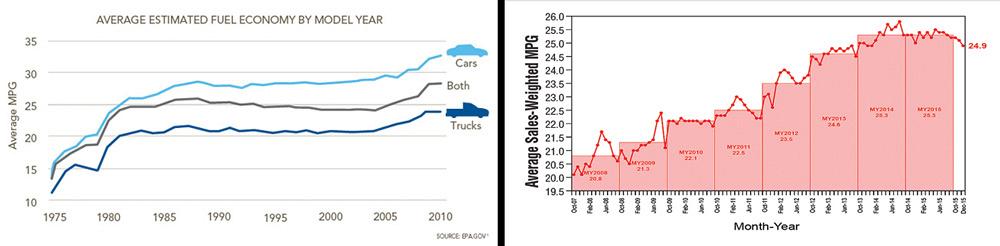
Figure 1
Fuel economy, which was stagnant from 1980 to 2004, made significant fuel efficiency gains from 2005 through 2015 to achieve corporate average fuel economy mandates by 2016. Graph on left courtesy of U.S. EPA and of PEW Trusts; graph on right courtesy of University of Michigan Transportation Research Institute.
Victor Esteban, business development manager, FAGOR Arrasate: Last year FAGOR designed, manufactured, and installed the first servo press for hot stamping. This new technology has been developed to consume less energy and reduce maintenance associated with hydraulic presses, commonly used for hot stamping (see lead image).
This first installation has a capacity up to 1,500 metric tons, a multilevel oven, and an automatic part feed system. The achievable speed is up to 35 strokes per minute (SPM) and the energy available for drawing is 475 kilojoules (kJ). The installation—the first of its kind in the world—is intended for die testing, hot stamping developments, and manufacturing of preseries limited production runs.
Recently we produced the first servo tryout press designed and developed for a Volkswagen facility in Emden, Germany, in collaboration with the BGIA (Institute for Occupational Safety and Health of the German Social Accident Insurance, IFA). Its capacity is 2,100 tons. It achieves production rates up to 18 SPM, with a stroke of 55 inches (1,400 mm). The kinematic is a link-drive type with available energy reaching 900 kJ.
Jim Schulte, general manager, servo and contract products, Nidec Minster: The evolution of servo press technology has been one of the most promising developments to address the need for flexibility in the pressroom. However, one of the trade-offs for that increased flexibility is speed.
Nidec Minster’s servo development team has produced an innovative low-inertia servo drive system. This drive system ensures that stampers with servo presses can obtain near-similar high speeds of mechanical presses while retaining servo presses’ broad flexibility. The compact drive design of our twin-end low-inertia drive system provides faster accelerations and decelerations to boost production rates and energy efficiency.
Shrinivas (Shrini) Patil, product manager, AIDA-America: Servo presses have evolved to provide the programmability of hydraulic presses with the higher productivity of mechanical presses. To help stamping manufacturers realize the improvements, we have developed a robust servo applications training program that includes die trial development at our facility and at the stamper’s facility. Our applications engineers provide on-site support to help users improve their existing processes.
2 How have your controls and drives technologies been upgraded?
Schulte, Nidec Minster: As other industry segments, such as wind power generation, continued to drive the development of high-torque, low-RPM servomotors, these types of motors became more available. That empowered servo press builders to offer a wider range of products and performance levels.
Patil, AIDA: To meet stampers’ requests, AIDA developed the first Allen-Bradley-based servo control for the North American metal forming industry (see Figure 4). Also, we developed our servo-press-to-servo-transfer interface that allows the stamping manufacturer to have a seamless, turnkey human-machine interface (HMI) control that accounts for changes in the servo press motion profile in settings for the automation equipment.
Other features include smart die protection that helps stampers improve throughput and eliminate nuisance die protection faults. It includes remote diagnostic capabilities to help resolve problems in a matter of minutes.
Lewalski, Schuler: The operator interface we developed contains a servo curve generator, called The Optimizer, which ensures a high level of process reliability through optimal coordination of slide kinematics and automation parameters. This simplifies and accelerates setup of the coil feed line, transfer system, and servo press parameters.
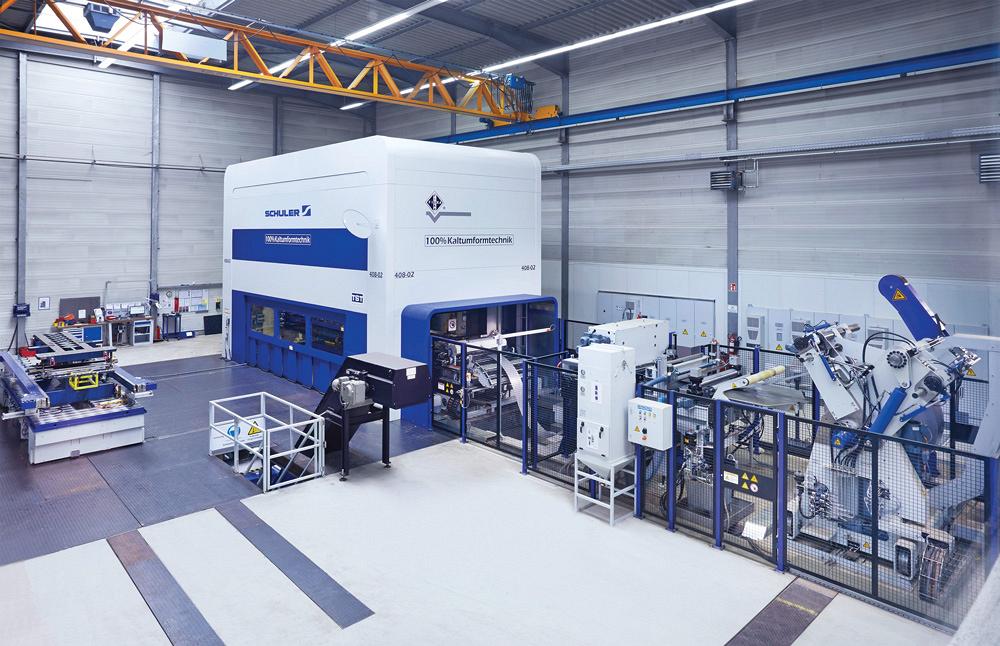
Figure 2
Schuler’s new twin servo technology locates the drive unit under the press, and the slide is pulled down by the draw rods, empowering the press to handle greater forces. Photo courtesy of Schuler North America, Canton, Mich.
Esteban, FAGOR Arrasate. Current servo press installations have evolved from the first generation manufactured back in 2006, mainly because of the improvements in the performance and costs of the servomotors and drives. These modern motors have higher power and are more dynamic than in years prior. This has allowed us to continuously improve and evolve our designs.
3 What are some current developments related to energy management?
Esteban, FAGOR Arrasate: The key to energy management is the advancement of energy efficiency through kinetic buffering. To do this, we create optimal servo press curves by integrating energy efficiency criteria with the theoretical consumption of the curve generation.
The advancement and integration of a unique common kinetic buffer for a tandem line of servo presses is a major improvement. Historically, in the first generation of tandem servo press lines, each press had its own stand-alone energy management system. This made the line less cost effective—not only to manufacture but also to operate—because energy consumption was not optimized. Shared energy management systems have improved both of these.
Lewalski, Schuler: Compared to conventional flywheel presses, servo presses are inherently designed to save energy and resources to a significant degree. We’ve enhanced press performance with energy management systems that store energy during the regenerative braking phase of the press cycle, then make it available for the subsequent motor-driven acceleration phase. This reduces connected loads and smooths current peaks.
Our servo presses come with an energy-efficient drive system that is speed-controlled and has a power/energy feedback system, intelligent standby, and rest circuits.
Our MSC 200 automatic blanking press is the world’s first line with two electrically coupled and freely programmable pressure points, which enhances energy efficiency. Linking the pressure points in the press uprights increases the machine’s rigidity. Furthermore, the play-free and lubrication-free drivetrain comprises a highly dynamic servomotor, brake module, and twin knuckle-joint, connected to the slide. In fact, the automatic blanking press uses two such drivetrains facing each other—synchronized via the drive control—which deliver a press force of 2,000 kilonewton (kN). The drivetrain’s reduced mass increases the slide’s dynamic response. Combined with the absence of gear transmission and roller bearings, this cuts electrical power consumption by up to 50 percent. The innovation received a 2014 EuroBLECH Award.
Patil, AIDA: Our ECO Energy Conservation and Optimization energy management system has been installed on all of our DSF servo presses for the last 15 years. This is a capacitor bank-based energy management system. It allows additional energy to be supplied instantaneously with minimal energy loss and low maintenance because it does not need additional motors or conversion of mechanical-electrical energy—with the associated energy loss. This type of energy management system saves energy by reducing the peak amperage and kilowatt-hour (kWh) usage by 30 to 40 percent. This is done, in part, by also regenerating excess energy and storing it in the capacitor banks.
Our newest development is a “smart” energy management system that monitors energy consumption to help stampers further reduce their peak loads and regenerate the energy more efficiently.
Schulte, Nidec Minster: Some servo press systems that use no or partial energy management are less costly for press OEMs to manufacture but are also very inefficient for stampers to operate. In today’s manufacturing environment, anything less than full energy management systems will quickly become obsolete. Full energy management encompasses the power required to drive the press and stamp parts while also regenerating, storing, and utilizing all other potential energy sources such as braking, springs, and cushions. Like a hybrid automobile, all available sources should be contained and recirculated in a closed-loop system. This optimal approach delivers an ongoing operational payback in lower net power per part.
4 Servo press technology has grown in terms of sizes offered. Why and how?
Schulte, Nidec Minster: The success that stampers have experienced with servo press technology has driven us to apply it throughout the range of our 45- to 4,500-ton presses. The key is the ability to synchronize multiple servomotors to obtain the torque necessary for either high tonnage or high performance. Before that, the single-motor servo press design limited the size of its applications. Today’s high-performance servo presses can synchronize up to six servomotors easily and produce power and speed results nearly on the same level as a mechanical press, with a high level of flexibility (see Figure 5).
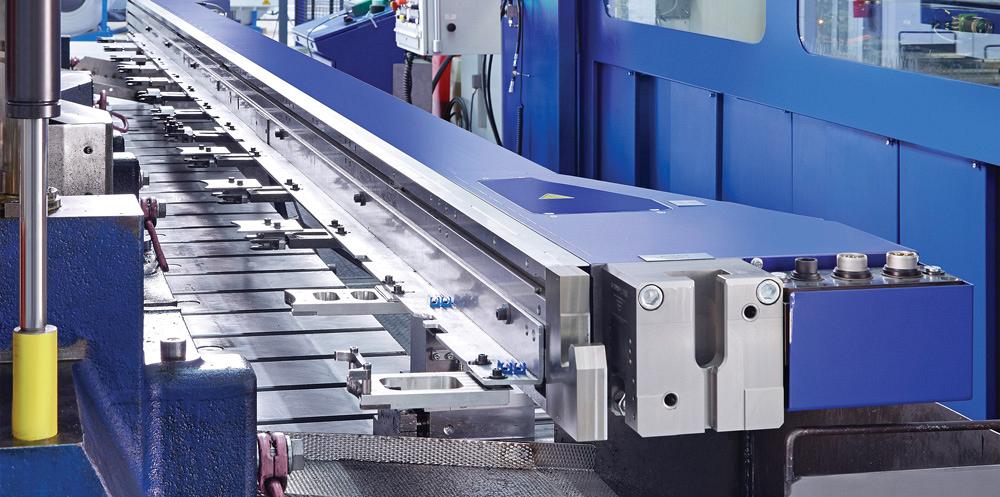
Figure 3
Schuler’s new Intrafeed transfer system’s grippers transport parts on movable carriages with their own drive units, rather than on rails, on the twin servo press. This significantly reduces the transfer rails’ length requirements. Photo courtesy of Schuler.
Lewalski, Schuler: The high forces required to form, pierce, and trim newly developed advanced high-strength steel (AHSS) grades in the automotive industry create significant challenges for the press and the tooling. This drives the need for higher tonnage, larger motors and drive systems, and larger bed and slide dimensions to accommodate larger dies, especially in the automotive industry. Schuler has a product line range of 250 to 3,600 U.S. tons.
Patil, AIDA: Because forming AHSS components requires higher tonnage and energy, stampers must use higher-tonnage presses. Stampers also are using servo presses for fineblanking. Press manufacturers are developing large-tonnage, single-point servo presses to meet this demand. AIDA has developed servomotors with peak torque up to 44,000 newton-meter (Nm), and makes servo presses up to 3,500 metric tons, and with beds as long as 288 in. (7.3152 m).
Esteban, FAGOR Arrasate: The size of presses has increased in recent years, and the servomotor technology has been adapted to this new situation. We’ve progressed from our first servo press at 400 tons to servo tandem press lines of 2,500 tons.
This evolution has been the result of motor drive improvements. Today’s motors are more powerful with higher torque (see Figure 6). Consequently, energy management has improved so that we have been able to build higher-tonnage presses with improved energy efficiency to meet market demands.
5 How are servo presses constructed to integrate with auxiliary operations?
Patil, AIDA: Servo press controls have additional features to integrate with auxiliary equipment. Because a servo press can be programmed to run at different speeds in a single cycle and reverse the slide direction, the press communicates with feeders and transfers to move at a constant rate regardless of the slide speed or direction. We optimize the number of motors and sizes to enable maximum line output by matching the press speed with the auxiliary equipment’s maximum speed.
Schulte, Nidec Minster: The key to integrating servo presses with auxiliary operations is having a highly sophisticated but flexible control that is simple to set up and easy to operate. Depending on the type of auxiliary equipment—feeds, transfers, stackers, destackers, robots, and so forth—different parameters are required to time and synchronize all the various motions and positions.
Having a control that is flexible enough to provide a virtual 360-degree axis for some processes while also providing linear slide position for other processes makes it simpler to optimize the process. Our PMC-servo operator interface provides both angular and linear slide positioning with a virtual axis to enable flexible interfacing with press line automation.
Esteban, FAGOR Arrasate: Our servo presses are designed to synchronize well with any number of auxiliary operations such as coil and strip feeding and destacking, as well as to optimize transfer cycles and drawing operations. Our newly developed controls systems allow for all of the peripheral axes to be synchronized with the same virtual axis.
Lewalski, Schuler: Frequently component production involves several steps which take time and slow productivity when performed separately. Our highly dynamic servomotors integrate downstream processes such as in-die welding, tapping, and stud and nut feeding directly into the press cycle to increase output. This is possible by implementing user-programmable time and distance procedures as well as rest times in the press cycle.
6 What innovations can people expect to see next year? In the future?
Patil, AIDA: As the servo press market continues to grow, servo presses will be more seamlessly integrated within the factories in which they operate. Stampers will be able to access data from their smartphones and transfer the programs and developments from one facility to another facility remotely. As controls continue to improve, they will be able to self-diagnose production bottlenecks and generate reports for stampers, who will use this data to optimize the line.
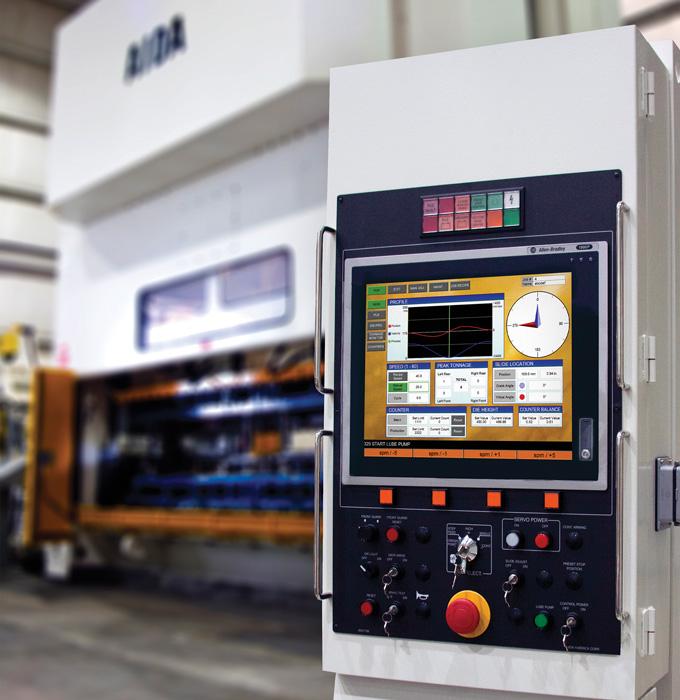
Figure 4
AIDA’s control upgrades include integration of an Allen-Bradley-based servo control, a servo-press-to-servo-transfer interface, and smart die protection. Photo courtesy of AIDA-America, Canton, Ohio.
We are hearing from our customers that they have limited internal resources; therefore, one key need is for continuing application support to help them fully realize the potential improvements and optimization. This support will grow, including a lot of online, long-distance support.
Schulte, Nidec Minster: We see that technology will continue to drive servo press performance to higher levels of both speed and efficiency. For example, our FX2-600 servo press is designed to run either progressive dies or transfer dies using the integrated servo transfer so that stampers can choose the optimal process without sacrificing production speed. Its ability to provide a high degree of flexibility while still achieving high production rates will be the competitive edge that stampers will need in the future.
Esteban, FAGOR Arrasate: The immediate future of servo technology is very promising. This technology has much potential for us to go on improving energy efficiency, developing larger and more dynamic servomotors, and expanding its applications in hot stamping, forging, and beyond.
Lewalski, Schuler: Continued servo press line and automation development will generate greater returns on investment.
Jim Schulte, Nidec Minster, 419-628-1852, jim.schulte@minster.com, www.minster.com
Barry Lewalski, Schuler North America, barry.lewalski@schulergroup.com, www.schulergroup.com
Victor Esteban, FAGOR Arrasate, v.esteban@fagorarrasate.com, www.fagorarrasate.com
Shrinivas (Shrini) Patil, AIDA-America, 937-235-3549, spatil@aida-america.com, www.aida-global.com
About the Author
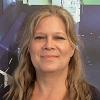
Kate Bachman
815-381-1302
Kate Bachman is a contributing editor for The FABRICATOR editor. Bachman has more than 20 years of experience as a writer and editor in the manufacturing and other industries.
subscribe now
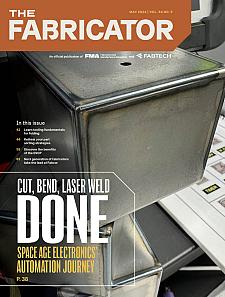
The Fabricator is North America's leading magazine for the metal forming and fabricating industry. The magazine delivers the news, technical articles, and case histories that enable fabricators to do their jobs more efficiently. The Fabricator has served the industry since 1970.
start your free subscription- Stay connected from anywhere
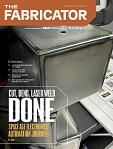
Easily access valuable industry resources now with full access to the digital edition of The Fabricator.
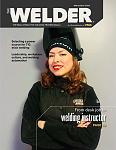
Easily access valuable industry resources now with full access to the digital edition of The Welder.
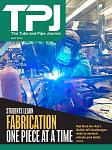
Easily access valuable industry resources now with full access to the digital edition of The Tube and Pipe Journal.
- Podcasting
- Podcast:
- The Fabricator Podcast
- Published:
- 04/16/2024
- Running Time:
- 63:29
In this episode of The Fabricator Podcast, Caleb Chamberlain, co-founder and CEO of OSH Cut, discusses his company’s...
- Trending Articles
Capturing, recording equipment inspection data for FMEA
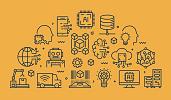
Tips for creating sheet metal tubes with perforations
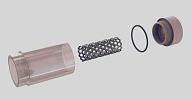
Are two heads better than one in fiber laser cutting?
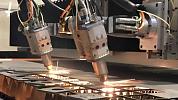
Supporting the metal fabricating industry through FMA
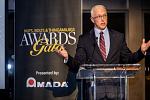
Omco Solar opens second Alabama manufacturing facility
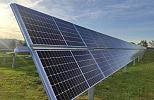
- Industry Events
16th Annual Safety Conference
- April 30 - May 1, 2024
- Elgin,
Pipe and Tube Conference
- May 21 - 22, 2024
- Omaha, NE
World-Class Roll Forming Workshop
- June 5 - 6, 2024
- Louisville, KY
Advanced Laser Application Workshop
- June 25 - 27, 2024
- Novi, MI