Editor-in-Chief
- FMA
- The Fabricator
- FABTECH
- Canadian Metalworking
Categories
- Additive Manufacturing
- Aluminum Welding
- Arc Welding
- Assembly and Joining
- Automation and Robotics
- Bending and Forming
- Consumables
- Cutting and Weld Prep
- Electric Vehicles
- En Español
- Finishing
- Hydroforming
- Laser Cutting
- Laser Welding
- Machining
- Manufacturing Software
- Materials Handling
- Metals/Materials
- Oxyfuel Cutting
- Plasma Cutting
- Power Tools
- Punching and Other Holemaking
- Roll Forming
- Safety
- Sawing
- Shearing
- Shop Management
- Testing and Measuring
- Tube and Pipe Fabrication
- Tube and Pipe Production
- Waterjet Cutting
Industry Directory
Webcasts
Podcasts
FAB 40
Advertise
Subscribe
Account Login
Search
It's the fabricating process, not the fabricated product
Japanese companies realize that monozukuri makes them more valuable suppliers of metal fabricating services
- By Dan Davis
- August 1, 2013
- Article
- Shop Management
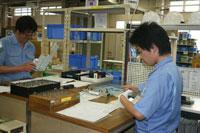
Figure 1: The quality personnel at Fukasawa Inc. use a check list to ensure that every part meets customer specifications before being shipped.
As a concept, manufacturing excellence is not something that can be boiled down into a simple word or phrase. It takes much more than posting a motto on a bulletin board for a fabricator to be a topnotch metal manufacturer.
Japanese manufacturers have known this since the country rebuilt its industrial sector after World War II, and the rest of the world seemingly has been trying to play catch-up for the last several decades. Monozukuri is not something that can be duplicated easily.
If you break down the term in the Japanese language, mono means “thing” and zukuri means “the process of making.” It stands alone as a word, but as a concept, it holds greater meaning for Japanese manufacturers. The term more accurately represents a Japanese company’s commitment to producing high-quality products in a consistent manner and being able to improve the production system over time.
Monozukuri also has emerged as the key to keeping ahead of international competitors. Japanese manufacturers have seen companies in places such as South Korea and China emerge as potent rivals, but they are not ready to accept defeat at the hands of these new manufacturing service providers. Japanese metal fabricators are betting on their manufacturing talents and processes as even more countries look to develop their own manufacturing sectors to boost their domestic economies.
“Some people can make a copy of a product, but they can’t copy the way that the product was made,” Mitsuo Okamoto, president, Amada Co. Ltd., told trade journalists in mid-May.
Amada invited trade press representatives to see not only its headquarters and manufacturing facilities, but also two Japanese job shops, where the spirit of monozukuri is alive and well. For those companies, the commitment to making things is serious, and the result is successful.
Small Company Thinks Big
Fukasawa Inc. is not unlike many North American fabricators: It’s a small, family-owned business trying to adapt in a changing marketplace.
The fabricator, which has been around since 1968, has 50 employees and produces precision parts for customers in the consumer electronics, information technology, and telecommunications industries. The company moved to its current facility in Nakai-machi, Kanagawa, in 2007. It still maintains its headquarters in Setagaya, Tokyo.
Amada officials believe that small to medium-sized companies, such as Fukasawa, comprise about 80 percent of all Japanese manufacturing companies. That’s about 25,000 shops.
Like their counterparts in the U.S., these shops were hit hard by the Great Recession. Fukasawa’s sales volume decreased by half in the days after the collapse of the global financial institutions.
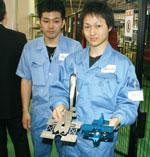
Figure 2a: This metal plane is given to visitors to the Fukasawa facility. It’s formed by an Amada Astro II 100 NT robotic press brake in 28 bends. Despite the automated bending, Fukasawa does not allow inexperienced operators to run this machine.
But even before the downturn, Fukasawa had to deal with OEM customers cutting back their supply bases. Many domestic companies were moving product development and production to overseas locations, and Fukasawa had to bolster its own capabilities and credentials, such as achieving ISO 14001 and RoHS directive compliance.
Around this time, Masao Kurihara, Fukasawa’s president and CEO, said he found “human power” to be a key factor in helping his company to stand out from other firms that may have had the same type of machinery. Employees’ talents would help the fabricator distinguish itself from a technical standpoint with customers.
“Of course, performance of the machine is important, but the human resource development is even more important,” Kurihara said.
To make the most of the employees’ talent, Fukasawa management has taken steps to transform “tacit” knowledge into “explicit” knowledge. In other words, it’s sharing what the more experienced employees know with others in the hopes of creating the most efficient and repeatable manufacturing process possible.
For example, the process sequence for manufacturing is standardized. After product data is extracted from electronic files using either Amada’s SheetWorks 3-D CAD software or AP100 2-D CAD program, a product worksheet, which details the manufacturing steps entailed in production, is created. This worksheet is a 300-item check list that helps the scheduler decide what is the most efficient production process to use.
Because the scheduler is not relying on personal experiences, but rather the input that has helped to create the check list, he or she is unlikely to commit a grievous error by scheduling a part unprofitably on the wrong machines. Consider the production of a blank. Knowing information related to critical tolerances and volume can help the scheduler determine which one of the company’s three Amada laser cutting machines, its Amada EM-255NT turret punch, or its Amada servo press should be used to create the blanks.
This approach also helps to eliminate wasted time in the programming department. If a programmer doesn’t have to wait around for an answer to a question because the check list provides all of the necessary guidance, then he or she can produce more programs. In a department that could be producing as many as 200 programs a day, that type of efficiency is welcomed.
This check list approach is mimicked in the quality department (see Figure 1). Division leaders contribute suggestions to create the quality check list that, once again, is intended to eliminate oversights that might occur during a typical production day.
Check lists, of course, can’t be used at every step in the manufacturing process. At some point employees have to be trusted to jump into a job and see it through to completion with little or no interruption. That’s why Fukasawa management has established a formalized training regimen.
Management has established 23 skill areas, and each of these has seven grades of proficiency. Each employee’s salary depends on the skill and proficiency level attained. Those training details—minus the salary information—are also placed on each employee’s nametag.
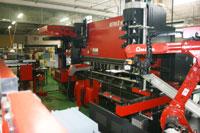
Figure 2b: Fukasawa’s automated press brake has control software that can store a job with as many as 98 bends. The machine’s efficiency is evident in the production of the souvenir plane. The automated press brake needed five minutes to complete all of the bends; an operator duplicating the same bending pattern likely would need eight to 10 minutes to finish the task.
In the front office, the schedulers are aware which employees are available for what tasks because these training details have been digitized. Employees are never assigned to an operation for which they don’t have the training necessary to do the job properly (see Figures 2a and 2b).
The metal fabricator not only takes an interest in the training that fuels the employees’ minds, but also is interested in the food that fuels the employees’ bodies. The company provides the staff with organic and additive-free food because it believes that a healthy body motivates good work.
It’s also a recipe for quality production. Fukasawa has increased its sales volume by more than 20 percent—up to $8 million—when compared to its balance sheets before the downturn. Simultaneously it has been able to diversify its customer base, serving about 45 separate companies, almost double what had been the case.
An Impressive Combination
The folks at OKI Electric Industry Co. Ltd. are not shy about their plant’s manufacturing prowess.
“If you were here a month ago, you could have seen the best cherry blossoms in the world and also the best factory,” Yoshiyuki Nakano, OKI Electric’s executive officer, told visitors to the company’s Mechatronics Systems Plant in Tomioka, Gunma.
OKI Electric has been manufacturing in Japan for 131 years. In fact, it was the first company to produce a phone in Japan.
Today the company, with headquarters in Tokyo and annual sales of $4.5 billion, is involved in the design, production, and maintenance of electronic communications and data processing devices and the development of software to support those products. It has about 23,000 employees worldwide and more than 11,000 in Japan.
At its Mechatronics Systems Plant, 190 employees work in sheet metal processing, turning out thousands of parts per day for as many as 300 different kinds of products per day. These devices include financial data processing equipment, such as ATMs and cash management systems, and transport information terminal products, such as airline check-in stations and automatic ticket vending machines. Each piece of equipment requires hundreds of sheet metal parts; the cash management systems commonly found in banks and supermarkets, for example, require almost 15,000 separate metal parts. Average lot size for a job is about 60 pieces.
At one time, OKI Electric relied mostly on stamping presses to produce the parts. The accuracy was always there, but closer examination of production costs eventually suggested that tool development for small to medium-sized production volumes didn’t make sense.
That led the company to install the first laser/punch combination machine in Japan in 1978. The ability to laser-cut part peripheries and punch holes and shapes with the precision of a stamping press would forever change the way OKI Electric fabricated metal parts.
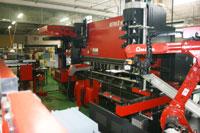
Figure 3: The Amada ACIES 2512 laser/punch combination machine not only delivers faster processing than earlier-generation machines, but also produces mar-free parts. A die-lift system keeps the die lower than the top of the brush table as the material is moved into position; when punching is about to commence, the die is lifted up for engagement and retracted after the hole is made. This prevents scratching of the metal surface.
Today the company operates eight laser/punch combination machines. The oldest machine was purchased in 1997, and the most recent addition—an Amada ACIES 2512 (see Figure 3), took place in 2011.
According to OKI, the newer machine offers a level of production efficiency unmatched by the company’s older combination machines. Manufacturing management suggested that the laser is seven times faster and the punching four times faster compared to its original laser/punch equipment (see Figure 4). The ACIES 2512 also has a 12-shelf material storage and retrieval system and an automatic tool changer (see Figure 5) that help minimize downtime. Only three operators are needed to supervise the work being done on the eight laser/punch combination machines.
Technology also has changed the manufacturing mix in the bending department. OKI Electric jumped into robotic bending in the mid-1980s, and today it has six Amada Astro 100 NT bending robot systems with automatic tool changers. All of the units are placed back-to-back near the manual press brakes.
Manufacturing management has the goal of getting 80 percent of all parts to be bent on the robotic press brakes. It’s been a gradual evolution to reach that stage, as only 50 percent of the parts that required bending were processed in the automatic bending stations in 2008.
One of the reasons for that slow shift has been the efficiency with which press brake operators currently operate. Downtime associated with figuring out which tooling to use and the proper way to set up and run the bending job is eliminated because CAM software produces drawings and photos that guide the operator in tool selection, setup, job run, and part inspection.
The goal—whether the manufacturing process involves a press brake operator or automated equipment—is for parts to have identical quality regardless of the fabricating operation. OKI Electric is confident that it is doing just that, otherwise Nakano would not have challenged the visitors to his factory to name another facility that demonstrates the same type of production prowess.
Setting the Table for Success
All Japanese companies take monozukuri very seriously, not just metal fabricators. That goes for machine tool builders as well.
Even in the production of sophisticated equipment used to bend, cut, and form metal, the steps taken to ensure consistent and quality production are in place. One example at Amada’s Fujinomiya Works, which is located near Mount Fuji, about 60 miles southwest of Tokyo, is the company’s approach to final equipment assembly (see Figure 6).
This tabletop approach takes the guesswork out of assembly operations. Much like a diner knows to start with the utensils on the outside of a dinner place setting, a technician knows where the parts and tools are for the day’s tasks in that assembly bay (see Figure 7). Because software constantly keeps tabs on who is working on a piece of equipment and what job is being done, parts are delivered to the assembly bays and placed in the order that they are needed.
The theory is that if people have the proper tools and parts placed in front of them in a clear and logical manner, they—or anyone else that may be faced with that job—should be able to proceed with little worry of making mistakes. Now, building an advanced machine tool is much more difficult than knowing when to slurp a bowl of miso soup during dinner, but steps are taken to eliminate the possibility of mistakes. Only one day’s worth of parts are delivered for that day’s tasks, which eliminates some distraction and keeps the focus on the jobs. Also, digital instructions are provided, which give the technicians visual guidelines for their work.
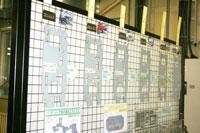
Figure 4: As part of its campaign to remind employees about product quality in a visible manner, OKI Electric has a display of how laser/punch part manufacturing has evolved over the years. In 1986 the newest combination machine could produce only 7.5 of the parts pictured per hour; today the ACIES can process 23 of the same part per hour.
Workers don’t waste time looking for parts and tools. The manufacturing team doesn’t waste time moving equipment from one station to another for separate stages of assembly. Amada management doesn’t waste time worrying about rework because procedures are in place to ensure first-build quality. North American manufacturers know about the Japanese expertise with rooting out waste, so it should come as no surprise that it’s a key part of monozukuri.
The concept of monozukuri is difficult to define succinctly, but the examples of it do a great job of illustrating this manufacturing concept. In the end, a manufacturer needs to focus on the process to ensure cost-effectiveness, on-time delivery, and high overall product quality. When those occur, success usually follows.
Amada unveils new products at fair
Amada Co. Ltd. welcomed customers from all over the world to its global headquarters in Isehara, Kanagawa Prefecture, Japan, for its Amada Innovation Fair 2013 Global, where they got to see 13 new metal fabricating machines.
One that drew a lot of attention was the LASBEND-AJ, a machine that combines laser cutting, tapping, forming, and bending into one device (see Figure A). Blanks are placed onto a bed, which then raises up, like a Murphy bed, to seal off all fabricating activity from outside interference. A laser then cuts the parts out as the blank is held vertically in front of the cutting head. From there a manipulator grabs the part and moves it down the line for further processing—bending, forming, or tapping. Again, all of these operations take place in a vertical orientation. For example, a swinging press is used for bending, which keeps the part stationary as the tool and die are moved simultaneously to achieve certain bends.
Amada corporate officer Katsuhide Ito said that this device is representative of the industrial-wide push toward automation of all fabricating processes. A machine programmer need only create one sequence in which a complete fabrication can be made by simply placing a blank on the machine and retrieving the finished product on the other end of the machine.
“The operator also doesn’t require any metal skills. No bending or forming experience is necessary,” Ito told visiting trade journalists in mid-May.
The all-in-one fabricating machine uses a 2-kW fiber laser, so it doesn’t require a much larger CO2 resonator and an accompanying large chiller. As a result, the entire unit occupies a footprint about the same size as a small CO2 laser.
The machine made its world debut at EuroBLECH 2012 in Hanover, Germany, last October. During the show, Maschinen Markt, a German manufacturing technology journal, awarded the machine its MM Award, which is given to innovative equipment on display on the show floor. The machine likely will be available in North America in a year or so, according to Amada officials.
Also on display at the Innovation Fair was a new robotic press brake tailored for small parts. The EG 6013 AR (see Figure B) is a servo electric press brake that is designed to work with parts that Amada’s Astro series of automated press brakes aren’t specifically designed to handle.
The 60-ton press brake, which has a 6-axis robot, can handle parts as small as 1.57 in. by 3.15 in. and as large as 11.8 in. by 11.8 in. The press brake is designed to deliver repeatability of ± 0.00315 in.
In total, visitors to the Innovation Fair got to see 12 bending, three punching, six laser cutting, and four laser/punch combination machines. Additionally, the event provided an opportunity for visitors to see Amada’s offerings for other areas of metal manufacturing, such as structural steel fabrication, machining, and stamping.
About the Author
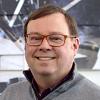
Dan Davis
2135 Point Blvd.
Elgin, IL 60123
815-227-8281
Dan Davis is editor-in-chief of The Fabricator, the industry's most widely circulated metal fabricating magazine, and its sister publications, The Tube & Pipe Journal and The Welder. He has been with the publications since April 2002.
subscribe now
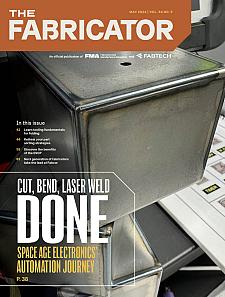
The Fabricator is North America's leading magazine for the metal forming and fabricating industry. The magazine delivers the news, technical articles, and case histories that enable fabricators to do their jobs more efficiently. The Fabricator has served the industry since 1970.
start your free subscription- Stay connected from anywhere
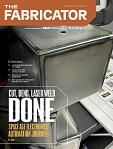
Easily access valuable industry resources now with full access to the digital edition of The Fabricator.
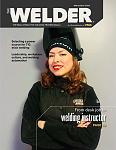
Easily access valuable industry resources now with full access to the digital edition of The Welder.
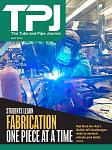
Easily access valuable industry resources now with full access to the digital edition of The Tube and Pipe Journal.
- Podcasting
- Podcast:
- The Fabricator Podcast
- Published:
- 04/16/2024
- Running Time:
- 63:29
In this episode of The Fabricator Podcast, Caleb Chamberlain, co-founder and CEO of OSH Cut, discusses his company’s...
- Industry Events
16th Annual Safety Conference
- April 30 - May 1, 2024
- Elgin,
Pipe and Tube Conference
- May 21 - 22, 2024
- Omaha, NE
World-Class Roll Forming Workshop
- June 5 - 6, 2024
- Louisville, KY
Advanced Laser Application Workshop
- June 25 - 27, 2024
- Novi, MI