Senior Editor
- FMA
- The Fabricator
- FABTECH
- Canadian Metalworking
Categories
- Additive Manufacturing
- Aluminum Welding
- Arc Welding
- Assembly and Joining
- Automation and Robotics
- Bending and Forming
- Consumables
- Cutting and Weld Prep
- Electric Vehicles
- En Español
- Finishing
- Hydroforming
- Laser Cutting
- Laser Welding
- Machining
- Manufacturing Software
- Materials Handling
- Metals/Materials
- Oxyfuel Cutting
- Plasma Cutting
- Power Tools
- Punching and Other Holemaking
- Roll Forming
- Safety
- Sawing
- Shearing
- Shop Management
- Testing and Measuring
- Tube and Pipe Fabrication
- Tube and Pipe Production
- Waterjet Cutting
Industry Directory
Webcasts
Podcasts
FAB 40
Advertise
Subscribe
Account Login
Search
A foundation for 5S
How a clean floor affects perceptions and productivity
- By Tim Heston
- April 7, 2014
- Article
- Shop Management
We repeatedly hear just how sophisticated and clean manufacturing has become. The message: Workers now spend their days in high-tech, sophisticated environments that suit their high-tech, sophisticated technical skills. Thing is, handling plate and sheet metal isn’t the cleanest of jobs. Floors can get dirty and sometimes stay that way for years, particularly in small job shops and contract fabricators without a full-time janitorial staff.
“Cleaning the floors is just very low on the long list of priorities of the typical job shop,” said Charlie Mack, general manager at Macksteel Warehouse in Watertown, S.D. “Cleaning was always a job left until everything else was done. No one wanted to do it.”
Macksteel is part metal service center, part sheet metal and plate job shop. Volumes range from one-offs to about 2,500, and hundreds of customers visit the company’s 100,000-square-foot warehouse every week.
“A dirty floor is not the image you want your customer to have of you,” Mack said.
Last year Macksteel invested in a ride-on sweeper to make a tedious, labor-intensive job easier. To clean the whole floor now takes about an hour (see Figure 1). Visiting customers now see a plant with a clean floor with a polished look, a benefit that may lead to more business, at least indirectly.
Mack added that having a polished floor actually provided a good foundation for the company’s broader 5S and other improvement efforts, literally and metaphorically. Software, automation, organization, clear documentation, and part identification: all such improvements are connected to, at least in some fashion, having a clean floor under foot.
First-line Fabrication
Mack’s parents founded the company in the 1970s as a scrapyard serving the growing demands of mini-mills. They eventually entered into the steel distribution business, splitting off and eventually selling the scrapyard in the late 1990s.
After several years in steel distribution, Macksteel began offering metal fabrication. Today the 40-employee company uses nine band saws, two lasers, and two press brakes to perform first-line fabrication for customers in a variety of sectors. On any given day the shop’s lasers could be cutting parts for farm or construction equipment, then change over to cut sheet metal profiles for the signage business. “We’ve cut out a lot of golden arches,” he said. “We’re lucky. Some of the signage providers to McDonald’s are right here in Watertown.”
Macksteel follows a broader trend among service centers and distributors, many of which offer first-line fabrication to OEMs. “It’s just one less step customers have to deal with,” Mack said.
Nuggets From Europe
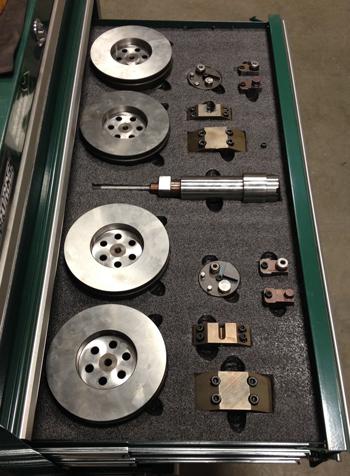
Figure 2
Macksteel employees place tools needed for changeovers in cabinets with foam cutouts. If a tool goes missing, it’s immediately apparent.
A scrapyard is a far cry from a clean-room environment, to be sure, but Mack’s parents still ensured that every type of scrap was placed in its designated place in the yard. They carried this organization over when transitioning to steel distribution. Every grade was (and is) clearly labeled and put in its place.
Mack, who took over the day-to-day operation of the family business several years ago, continued the tradition of organization and cleanliness. But these are relative terms, and his perception changed while visiting several operations in Austria, Switzerland, and Germany four years ago. Mack saw the automation, the 5S, and the gleaming look of some facilities. “I saw their level of organization and automation,” he said. “It was a real eye-opener for me. That’s when we started to look at the way we do things.”
The work environments caught his attention. Efficient lights illuminated the shop floors. Everything was bright. Floors shined, and every tool had its place. These facilities exuded not the stereotypical “dank shop” but instead a professional work environment for the technically skilled.
Less Is Best
Customers of fabrication work essentially are buying capacity. The risk of outsourcing capacity, of course, is delivery unreliability. To mitigate this risk requires an organized, efficient shop that can deliver products on time.
Along with conventional shadow boards, Macksteel purchased cabinets and foam to separate and organize commonly used tools used for job changeovers. The company purchased raw foam and cut holes to the appropriate size (see Figure 2).
Macksteel also places machines side by side so they can share common tools, when practical. For instance, two press brakes that run product families with similar forming requirements share the same tool rack.
When it comes to tools in general, less is best. “Whenever we get a new machine tool, we make sure we strip it down to the bare minimum tools we need,” Mack said. “Otherwise, it can be an uphill battle to maintain the organization.”
He added that although it seems counterintuitive, he has found that having one too few tools at a workstation is far better than having one too many. If on occasion an operator leaves his station to find a tool, so be it. The rare trip to fetch a wrench is far better than overstocking every workstation with an abundance of tools. In Macksteel’s high-product-mix situation, having all the tools necessary for every job at the point of use just isn’t practical.
Cleaning Up
Employees are responsible for cleaning their work areas, but what about sweeping and cleaning the entire shop? Being a distributorship, with tons of steel entering and leaving the plant every day, the company has plenty of debris: tags and banding from bundles of steel, miscellaneous nails and hardware, you name it (see Figure 3). Until last year employees swept the floor only when time allowed, and that wasn’t often enough. Sweeping the entire floor manually often took four hours or longer.
The cleanup initiative started by organizing the large debris, including the used 4-by-4 blocks that come with delivered metal. The receiving area now has block carriers by all the docking entrances, so blocks aren’t strewn about the place. Those carriers then get moved to the shipping area, where the blocks are used to hold packaged finished goods.
“These little things make a difference in the time,” Mack said. “You can’t compete and grow until you tackle all these little demons.”
One demon just wasn’t going away, though: the time-consuming, much-maligned job of sweeping the floor. So Mack decided to automate the job nobody wanted.
The company bought a Tennant ride-on sweeper. It doesn’t scrub deeply, as some sweepers do—that would be overkill. Instead, it is designed for inside use on concrete; brushes differ depending on the surface type and whether they’re for indoor or outdoor use. The sweeper turns tight corners, and its rotary brush configuration, slowly spinning on its front leading corners, allows it to reach about 6 inches under machines, tables, and material pallets. The job now takes less than an hour (see Figure 4).
Mack added that a clean floor may not be as flashy as new software or advanced fabricating equipment, but it has had numerous hidden benefits. It makes out-of-place debris, material, fastening hardware, and tools easy to spot. Also, leaks from fork trucks or other equipment become immediately apparent.
“We were able to detect a few leaks on fork trucks that may have been there for a while,” Mack said, “because before, the leak marks just blended right in on the dirty floor.”
The look exudes professionalism and efficiency, and it affects perceptions, which builds a shop’s reputation. “When you have a clean shop floor, it brings the whole organization up a notch,” Mack said. “It’s literally the foundation which everything is built on.
“It has come down to the little things,” he added. “I think that’s how modern fabricators really survive. And we’re still not at the end of this journey. It’s one little thing after another, and the sum of all those is what makes up a significant change.”
Software and Supply Chain Transparency
While touring several European fabricators four years ago, Charlie Mack, general manager at Watertown, S.D.-based Macksteel Warehouse Inc., picked up various nuggets, and one that especially inspired him was the shops’ use of software to automate job tracking. “We are really looking to automate further via software,” Mack said. “As far as it has come in the past 10 years, there’s still a lot to be gained.”
Macksteel uses a traditional order-entry approach. A customer calls in an order, the salesperson enters it, and then the work flows to engineering and CNC programming. It’s then manually scheduled based on the due date and equipment load levels. When the job is complete, the traveler paperwork is brought back to the office, where someone calls and notifies the customer that the order is complete.
The company hopes bar coding will change this manually intensive process. At this writing, Mack is planning to upgrade the enterprise resource planning (ERP) platform, Bayern Software’s Steel Plus Capstone, to give customers access to bar-coded jobs on the floor. As soon as an operator scans a bar code on a job traveler, a notification will immediately appear in the customer’s e-mail. Customers then can see how a job travels through various processes on the floor.
When the job reaches the shipping department and is packed and ready to go, the shipping employee will scan the bar code, and a notification and packing list will be e-mailed to the trucking company or the customer’s logistics department, depending on which entity is shipping the job to the customer location.
In effect, Mack hopes to automate information flow throughout the shop, so that everything is quick, documented, and traceable. “To be able to automate this cuts out a lot of the human error,” he said.
About the Author
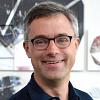
Tim Heston
2135 Point Blvd
Elgin, IL 60123
815-381-1314
Tim Heston, The Fabricator's senior editor, has covered the metal fabrication industry since 1998, starting his career at the American Welding Society's Welding Journal. Since then he has covered the full range of metal fabrication processes, from stamping, bending, and cutting to grinding and polishing. He joined The Fabricator's staff in October 2007.
subscribe now
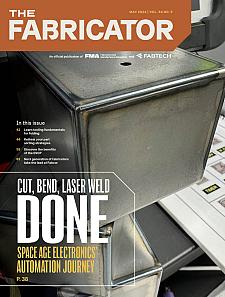
The Fabricator is North America's leading magazine for the metal forming and fabricating industry. The magazine delivers the news, technical articles, and case histories that enable fabricators to do their jobs more efficiently. The Fabricator has served the industry since 1970.
start your free subscription- Stay connected from anywhere
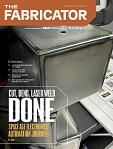
Easily access valuable industry resources now with full access to the digital edition of The Fabricator.
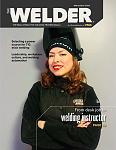
Easily access valuable industry resources now with full access to the digital edition of The Welder.
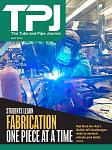
Easily access valuable industry resources now with full access to the digital edition of The Tube and Pipe Journal.
- Podcasting
- Podcast:
- The Fabricator Podcast
- Published:
- 04/16/2024
- Running Time:
- 63:29
In this episode of The Fabricator Podcast, Caleb Chamberlain, co-founder and CEO of OSH Cut, discusses his company’s...
- Industry Events
16th Annual Safety Conference
- April 30 - May 1, 2024
- Elgin,
Pipe and Tube Conference
- May 21 - 22, 2024
- Omaha, NE
World-Class Roll Forming Workshop
- June 5 - 6, 2024
- Louisville, KY
Advanced Laser Application Workshop
- June 25 - 27, 2024
- Novi, MI