- FMA
- The Fabricator
- FABTECH
- Canadian Metalworking
Categories
- Additive Manufacturing
- Aluminum Welding
- Arc Welding
- Assembly and Joining
- Automation and Robotics
- Bending and Forming
- Consumables
- Cutting and Weld Prep
- Electric Vehicles
- En Español
- Finishing
- Hydroforming
- Laser Cutting
- Laser Welding
- Machining
- Manufacturing Software
- Materials Handling
- Metals/Materials
- Oxyfuel Cutting
- Plasma Cutting
- Power Tools
- Punching and Other Holemaking
- Roll Forming
- Safety
- Sawing
- Shearing
- Shop Management
- Testing and Measuring
- Tube and Pipe Fabrication
- Tube and Pipe Production
- Waterjet Cutting
Industry Directory
Webcasts
Podcasts
FAB 40
Advertise
Subscribe
Account Login
Search
Surveying suitability of welding processes for roll formed parts
Productivity drives suitability
- By Bill Schubert
- December 12, 2006
- Article
- Roll Forming
Fusion weld processes melt the material so that it flows together and recasts when cool. They allow a lot of freedom in weld joint design; lap, butt, and fillet configurations are possible in many applications.
The fusion weld processes most successfully integrated with roll forming are those that don't require a filler metal. The relatively high line speeds in a roll forming system would require an impracticably large filler metal delivery system to support a reasonable amount of production. In addition, controlling the location of the weld bead precisely for filler metal dispersion requires automated seam-tracking. Although they are available, these devices are sophisticated and expensive and do not lend themselves well to integration into a roll forming line.
Some fusion welding processes create a shielding slag to keep the weld from being contaminated as it cools. These processes also are not good candidates for integration, because automating weld slag removal is not practical at high speeds, and the slag itself is highly abrasive to machine components and creates maintenance issues. For these reasons, fusion weld processes such as submerged arc; flux-core; oxyfuel; electroslag; and gas metal arc welding (GMAW), also referred to as MIG, normally are not good candidates for integration in a roll forming system.
Fusion Welding Processes Used in Roll Forming
Gas Tungsten Arc Welding (GTAW). GTAW, also referred to as TIG, requires filler metal in some applications, such as welding most carbon steels. However, GTAW can be used to weld aluminum, stainless steel, and sometimes carbon steel without filler metal. In these instances, GTAW can be integrated in a roll forming line quite successfully.
In the material thickness ranges suitable for roll forming, a shield gas—usually argon—is used to prevent impurities from entering the molten pool of material in the weld bead. Applications that require prepunched holes or notches are more difficult to weld using GTAW because the shield gas will not seal as well against the material to shroud the weld properly.
When weld parameters are set properly, the GTAW process yields good weld appearance and metallurgical integrity. The major disadvantage of the GTAW process is the weld speed: Depending on the material and thickness, the weld speed is from approximately 5 to 25 feet per minute (FPM) (1.5 to 8 meters / min. [MPM]). This speed range requires that the roll forming line be slowed to integrate GTAW. In addition to the obvious productivity loss, the speed range of the roll former drives must be configured specifically for operation in this range to prevent overheating. The slow process speed also allows time for the material to absorb heat, possibly causing thermal distortion of prepunched features.
Plasma Arc Welding (PAW). PAW is less commonly integrated with roll forming than GTAW, because PAW generally is used to weld material thicker than roll forming can process. However, in applications that require filler metal, or on material thicknesses for which GTAW is impractical, PAW can be a viable alternative.
PAW's setup parameters are slightly more forgiving than GTAW's, allowing more variance in torch standoff distance and the resultant arc length, but the equipment usually is more expensive and sophisticated to maintain and operate. Like GTAW, line speeds are slow by roll forming standards, but the process provides high-quality and attractive welds.
When GTAW or PAW is integrated into a roll forming line, the weld amperage, electrode type, shield gas type, travel speed, and the standoff distance of the torch to the material need to be determined in counsel with the weld equipment supplier. To integrate these processes into a roll forming system, a torch holder needs to be designed specifically for the application. The roll form tooling supplier or machine manufacturer may be able to supply a specially designed torch-holding fixture to position the torch on the roll forming machine.
With GTAW or PAW, it is imperative that the weld joint be presented to the weld torch flat to the horizon, so that gravity will not cause the molten puddle to run uncontrollably. The complex torch motions required for manual out-of-position GTAW or PAW are not practical for reliable integration into an automated roll forming system. For this reason, the roll tool designer must design the tooling to orient the part as required for the welding process, even if this results in a less-than-optimal part orientation for roll forming. As a result, additional tooling may need to be added to the roll tool set for extra passes, or between-station guides must be added to the roll former to accommodate the required weld position. Positioning the stationary torch in proper relation to the moving material is best done in consultation with both the welding process expert and the roll tooling designer.
Laser Welding. By strict definition, laser welding is a fusion weld process, because it melts and recasts the metal, but it differs from GTAW and PAW in that it is a nonelectrical process. This difference offers unique application opportunities because the part does not need to be positioned to seek an electrical ground; to create, maintain, or control an electromagnetic field; or to achieve the optimal current flow. It also allows the welding of nonconductive materials, such as prepainted metal.
The laser beam's narrow focus produces a very small heat-affected zone (HAZ), a strong and high-quality weld, and good weld appearance. The laser process causes relatively little part distortion because the minimal heat input is focused to a small area, and the high energy concentration facilitates faster weld speeds than many other welding processes.
A laser weld joint needs to be located more accurately than the joint in any other weld process. The roll tooling in an integrated roll forming/laser welding line must position and fit the edge gap to be welded on a horizontal plane, while also maintaining the focus depth of the beam lens in a vertical plane. The accuracy required in the weld joint varies with the application, but common tolerance requirements are ±0.002 in. (±0.050 mm). This tolerance requires that the roll tooling be machined to a high level of accuracy.
Effectively integrating the laser welding process requires that the roll forming machine be of the highest quality. Fine-pitch drive gears sometimes are used to minimize vibrations caused by gear train backlash, minimal bending clearance, and component misalignment.
Even roll forming machines with good drive designs in excellent condition can sometimes transmit resonant frequencies and harmonic vibrations to the material that can make it difficult to keep a laser weld beam in focus. Chain-driven roll forming machines or those with coarse drive gear pitch are not suitable for laser welding integration.
In laser welding, the weld joint must be cleaned to keep contaminants from creating a porous or poor-quality weld. If liquid lubricants or cleaners are used, they must be dried thoroughly before the material enters the weld area. In some applications, such as welding anodized aluminum, the material can be laser-welded without any special preparation.
Two types of laser welders are used for most welding applications in industry—CO2 and Nd:YAG. A CO2 laser requires a fixed beam delivery system, which makes it unsuitable for robotic applications, but ideal for integration into a roll forming line. A CO2 laser can be focused to a smaller area than Nd:YAG, yielding a higher concentration of energy and higher weld speed that maximize the high-speed potential of the roll forming process and allow thick materials to be welded.
Lasers can weld many different materials. Low-carbon and low-alloy steels can be laser-welded well. However, when carbon content is higher than 0.3 percent, or when sulfur, phosphorus, selenium, cadmium, or lead levels are at 0.05 percent cumulatively, the welds can be brittle and suffer from porosity and hot cracking. Laser welds on galvanized materials can exhibit a porosity problem because the zinc coating in the material vaporizes quite easily. This problem is of special concern on lap-type weld joints because the vaporized zinc is trapped and forced into the molten weld bead.
Laser welding is a good process for the 400 series stainless steels, as the weld is usually more ductile than with other weld processes. The 200 and 300 series austenitic stainless steels weld well, except for series 303, 321, and 347, which can be prone to solidification cracking. The 1000, 3000, and 2219 series aluminum can be laser-welded successfully. However, power output often must overcome the aluminum's high reflectivity, and a high weld speed is required because of the high thermal conductivity and relatively low melting point of the material. This requirement can be a significant limitation when laser welding must be integrated with slower processes, such as punching or cutting parts to length. The 5,000, 6,000, and 7,000 series aluminum do not laser-weld well because the magnesium, silicon, and zinc used as an alloying element vaporize quickly, creating a porous weld.
Other nonferrous metals are not good candidates for the process. Brass contains zinc and can suffer the same porous weld conditions of other zinc-containing metals. Copper has a high reflectivity and thermal conductivity, so it is better welded by other processes.
Gas Tungsten Arc Welding (GTAW). The weld current is transferred to the workpiece through a tungsten electrode. Argon or helium gas is used to shield the weld from contaminants. These gases are inert and will not combine chemically with other materials, effectively forming a chemical barrier against contaminants coalescing into the weld puddle and bead. Being heavier than air, argon shield gas works best in a relatively open, well-ventilated area. Noninert carbon dioxide is used as a shield gas in certain non-roll forming applications, making the term "GTAW" inappropriate in these instances.
Plasma Arc Welding (PAW). PAW is similar in process to GTAW. Technically, the processes differ because in the PAW process, the argon shield gas is excited to a plasma energy state by the electrical current coming from the power supply through the nonconsumable tungsten electrode. This process is called ionization. In this state, the outer electron shell of the plasma gas atom readily accepts free electrons, which are supplied by the current flow from the power supply. In this way, in addition to providing contaminant shielding, the plasma gas carries the current to the workpiece, similar to the way a conductive metal wire transfers electrons from atom to atom to ground.
Laser Welding. When electrical or light (photonic) energy is introduced into certain materials, called lasing materials, the atoms of the material are raised to a higher energy state. Photons, or particles of light, are spontaneously emitted. The light emitted in this process is called laser light. Instead of spreading out, as does light emitted from most sources in the visible spectrum, laser light stays collimated, even over great distances. This characteristic allows the light to be controlled and focused to a fine point, concentrating the energy in the laser light beam to a very small area.
To raise the energy level to a point that metals can be welded, the laser light beam must be amplified. This is accomplished by reflecting the light back and forth between mirrors, with more photonic energy gained on each successive pass from mirror to mirror. The final mirror assembly is only partially reflective, allowing the unreflected portion of the energy-carrying light beam to pass through a focusing lens that concentrates the energy of the beam delivered to the workpiece. The cavity that amplifies, or resonates, the energy level in the laser beam is called the resonator.
About the Author
subscribe now
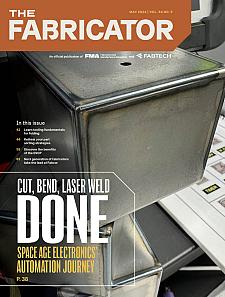
The Fabricator is North America's leading magazine for the metal forming and fabricating industry. The magazine delivers the news, technical articles, and case histories that enable fabricators to do their jobs more efficiently. The Fabricator has served the industry since 1970.
start your free subscription- Stay connected from anywhere
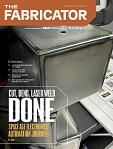
Easily access valuable industry resources now with full access to the digital edition of The Fabricator.
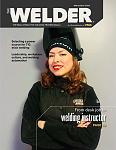
Easily access valuable industry resources now with full access to the digital edition of The Welder.
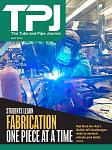
Easily access valuable industry resources now with full access to the digital edition of The Tube and Pipe Journal.
- Podcasting
- Podcast:
- The Fabricator Podcast
- Published:
- 04/16/2024
- Running Time:
- 63:29
In this episode of The Fabricator Podcast, Caleb Chamberlain, co-founder and CEO of OSH Cut, discusses his company’s...
- Industry Events
16th Annual Safety Conference
- April 30 - May 1, 2024
- Elgin,
Pipe and Tube Conference
- May 21 - 22, 2024
- Omaha, NE
World-Class Roll Forming Workshop
- June 5 - 6, 2024
- Louisville, KY
Advanced Laser Application Workshop
- June 25 - 27, 2024
- Novi, MI