- FMA
- The Fabricator
- FABTECH
- Canadian Metalworking
Categories
- Additive Manufacturing
- Aluminum Welding
- Arc Welding
- Assembly and Joining
- Automation and Robotics
- Bending and Forming
- Consumables
- Cutting and Weld Prep
- Electric Vehicles
- En Español
- Finishing
- Hydroforming
- Laser Cutting
- Laser Welding
- Machining
- Manufacturing Software
- Materials Handling
- Metals/Materials
- Oxyfuel Cutting
- Plasma Cutting
- Power Tools
- Punching and Other Holemaking
- Roll Forming
- Safety
- Sawing
- Shearing
- Shop Management
- Testing and Measuring
- Tube and Pipe Fabrication
- Tube and Pipe Production
- Waterjet Cutting
Industry Directory
Webcasts
Podcasts
FAB 40
Advertise
Subscribe
Account Login
Search
Controlling High Speed Machining
Generally speaking, high speed machining is most prevalent in the mold and die market as well as the aerospace and automotive sectors.
This doesn't mean, however, that these are the only areas that can take advantage of the benefits of this type of machining. For example, production job shops, which keep a close eye on cycle times can often be prime examples of high speed machining shops.
"High speed controls become most essential when the part-program is created via a traditional CAM programming technique in which tens of thousands of points are used," explained Fagor Automation marketing manager, Todd Drane. "Thus the CNCs throughput, both from a block processing speed aspect and look-ahead with optimum servo filters to increase performance from speed and finish aspect, is important."
According to Drane, high speed machining with features such as 10,000+ RPM spindles, coolant through the spindle, high speed dual-arm tool changers and rapid traverse speeds in excess of 1,000 IPM, are all typically necessary to maximize your high speed requirements. However, many ignore perhaps the most important element of a high speed machining center... the CNC system.
What will limit the performance of a high speed machine is the slowest link, or for lack of a better term, the bottleneck. In many cases this is the CNC control system. It is a fairly common occurrence to see a machine equipped with many of the features associated with high speed machining centers become sluggish or overshoot when the feedrate is increased if the CNC does not have the processing power needed to accomplish the required high speed tasks.
The Technology
Fagor Automation has answered the market's need for a high speed CNC with their Pentium-based high speed Open CNC 8070 control system.
According to Drane, one of the first requirements for a high speed CNC control is the ability to process commands.
"The most common term for this is 'block processing speed', which is typically expressed in either the time required to execute a single block of program code or blocks executed per second," explained Drane.
In other words, a control that has the ability to execute a block every 5 ms, would then also be rated as 200 blocks per second. Typically, each block of code is equal to a single line of code with three- axes interpolation commands.
You will find the vast majority of CNC controls to be limited to BPS ratings of five to 15 BPS. The Fagor 8070 Control system has the ability to execute in excess of 1,000 blocks per second, thus a BPS rating of less than one BPS. With this high level of CNC speed, you would look elsewhere for your machine bottleneck.
Block processing speed, while extremely important, is not the only consideration for a high speed CNC control. The following CNC features are imperative to insure you have the ability to optimize your total machine capability:
- Block look ahead of 150 blocks.
- High speed servo update speed.
- Automatic jerk control.
- High speed programmable logic controller (PLC).
- Spline interpolation algorithms.
- Post interpolation filters to eliminate resonance.
- Gains and adjustments controllable via parameter management and/or the part program.
- N-blocks horizon to avoid tool collision.
- Ethernet and RS 232 capability for high speed communications with external devices.
- Large on board hard drive for large program storage capability.
- Open control for OEM or user specific application customization.
- Tool life management capability.
- High speed sercos digital communication utilizing fiber optics for high speed drive/motor communication.
Getting an edge in the highly competitive aerospace and automotive markets often relies on staying on top of technology trends. What this means is that once a new control system debuts, manufacturers are looking to add it to existing machine tools.
"In Canada the high speed retrofit market is very healthy," explained Drane. "We are constantly working with customers on new retrofits, in a wide variety of applications."
Moving Quickly
The need for high speed cutting of contours, especially in Canada' aerospace sector is what is driving high speed CNCs. Controls must be able to transfer large amounts of data, make large programs efficient to edit while at the end of the day producing the needed workpiece.
"In high speed machining there are many factors that are important," explained Scott Warner, Canadian regional manager for HEIDENHAIN. "High speed cutting cycles and filters are very important. As are the machine tool itself, the tooling, the control and CAD integration."
The iTNC 530 from HEIDENHAIN was developed with these needs in mind.
Short block processing times remain the best solution for certain machining tasks. One example of this is the machining of contours with a high resolution.
With the iTNC 530 this can be accomplished, in part, due to the system's block processing of less than one millisecond. This control also has a 1,024 block look ahead that enables it to adapt the axis velocities to the contour transitions.
"In high speed machining moving from point A to point B is important, but it's more about creating a part quickly and creating one within tolerances," said Warner. "If you try to move your machine very quickly the machine will overshoot and come back, minimizing this overshoot with varying part descriptions in the most efficient manner, within tolerance is the difficulty. The CNC needs to be able to control this movement. Accelerating and decelerating are important, but so is the rate of change between the two at high speed."
The iTNC 530, for example, controls the axes with special algorithms that ensure path control with the required limits to velocity and acceleration. The integrated filters can also suppress the natural frequencies of the machine tool, while maintaining the desired surface accuracy.
Spline Interpolation
If your CAD/CAM system describes contours as splines you can transfer them to this control as it features a spline interpolator. This is just another example that proves that your control needs to be optimized to the machine.
And, according to Warner, by upgrading your control – even after only a couple of years – you can help maintain your edge over the competition.
How Fast Are You?
There is an easy method to determine the speed of your control system. Ask your CAD/CAM department to create a three-axis program with average increments between the commands of 0.001" starting from absolute zero position and moving a total of 60 inches. Therefore your program would contain approximately 60,000 position command blocks of code. Program a feedrate of 60 IPM, and start your program with an override percentage of 20 percent. Your machine should execute this program in its entirety in five minutes at 20 percent override without any errors or sluggish behavior.
Based upon 60,000 total blocks executed over five minutes, you can quickly see that your control executed 12,000 blocks per minute (60,000 divided by five = 12,000 blocks per minute). Or better expressed as 200 blocks per second. (12,000 divided by 60 seconds = 200 blocks per second) Thus your control system is rated at least five BPS.
Increase your feedrate override percentage to 50 percent and try again. This time the program should be executed within two minutes and if successful, your control system speed would be rated at two BPS. At 100 percent of the programmed feedrate your control would have one BPS capability, and true status as a high speed CNC control.
subscribe now
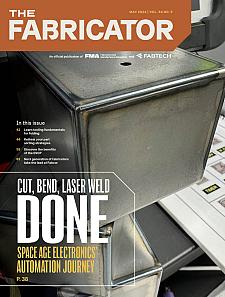
The Fabricator is North America's leading magazine for the metal forming and fabricating industry. The magazine delivers the news, technical articles, and case histories that enable fabricators to do their jobs more efficiently. The Fabricator has served the industry since 1970.
start your free subscription- Stay connected from anywhere
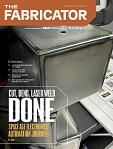
Easily access valuable industry resources now with full access to the digital edition of The Fabricator.
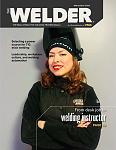
Easily access valuable industry resources now with full access to the digital edition of The Welder.
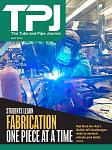
Easily access valuable industry resources now with full access to the digital edition of The Tube and Pipe Journal.
- Podcasting
- Podcast:
- The Fabricator Podcast
- Published:
- 04/16/2024
- Running Time:
- 63:29
In this episode of The Fabricator Podcast, Caleb Chamberlain, co-founder and CEO of OSH Cut, discusses his company’s...
- Trending Articles
Capturing, recording equipment inspection data for FMEA
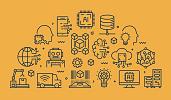
Tips for creating sheet metal tubes with perforations
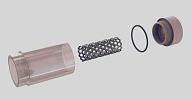
Are two heads better than one in fiber laser cutting?
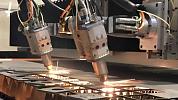
Supporting the metal fabricating industry through FMA
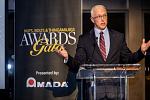
Omco Solar opens second Alabama manufacturing facility
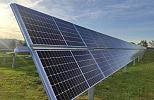
- Industry Events
16th Annual Safety Conference
- April 30 - May 1, 2024
- Elgin,
Pipe and Tube Conference
- May 21 - 22, 2024
- Omaha, NE
World-Class Roll Forming Workshop
- June 5 - 6, 2024
- Louisville, KY
Advanced Laser Application Workshop
- June 25 - 27, 2024
- Novi, MI