Senior Mechanical Engineer
- FMA
- The Fabricator
- FABTECH
- Canadian Metalworking
Categories
- Additive Manufacturing
- Aluminum Welding
- Arc Welding
- Assembly and Joining
- Automation and Robotics
- Bending and Forming
- Consumables
- Cutting and Weld Prep
- Electric Vehicles
- En Español
- Finishing
- Hydroforming
- Laser Cutting
- Laser Welding
- Machining
- Manufacturing Software
- Materials Handling
- Metals/Materials
- Oxyfuel Cutting
- Plasma Cutting
- Power Tools
- Punching and Other Holemaking
- Roll Forming
- Safety
- Sawing
- Shearing
- Shop Management
- Testing and Measuring
- Tube and Pipe Fabrication
- Tube and Pipe Production
- Waterjet Cutting
Industry Directory
Webcasts
Podcasts
FAB 40
Advertise
Subscribe
Account Login
Search
Advanced variable-polarity plasma arc welding
Using the process for welding aluminum tailor-welded blanks
- By Chris Pilcher and John Micheli
- November 29, 2000
- Article
- Arc Welding
Automotive companies are struggling to produce more fuel-efficient vehicles capable of meeting new stringent corporate average fuel economy (CAFE) requirements. These environmentally friendly modes of transportation range from battery-powered to fuel cell and cleaner petroleum-burning vehicles.
Shedding weight is a major contributor to achieving these goals; therefore, aluminum is being used more in the manufacture of automotive inner and outer body components in addition to its more traditional role in castings and forgings. Many companies are struggling with manufacturing aluminum-alloy (AA) tailored-welded blanks (TWB), and no joining process has evolved as a leading technology in this process.
A method that has received very little attention is variable-polarity plasma arc welding (VP-PAW). This method of welding is a proven form of welding AA under difficult and demanding applications, such as the manufacture of many aluminum components including cryogenic fuel tanks for the space shuttle and other commercially available launch vehicles.
Variable-polarity PAW is also used in the manufacture of automotive air-conditioning components, with thousands of parts produced daily. Using this method with a proper weld schedule and part preparation can produce X-ray-quality welds consistently. In addition, the weld bead profile produced with VP-PAW enhances the material flow characteristics of the aluminum, producing the optimal weld bead profile for forming AA TWBs.
This article discusses the metallurgical considerations that must be addressed before welding AA. This is followed with a description of VP-PAW and its range of applications for other forms of transportation. The article concludes with some results of work performed in the manufacture of production-worthy AA TWBs.
Metallurgical Considerations
The metallurgical characteristics of the aluminum (see Table 1) alloy to be used in a tailor-welded blank must be considered. In short, weldable and nonweldable grades of aluminum can be categorized as heat treatable or strain hardenable. The heat-treatable grades can be welded but require an alloy filler to prevent cracking on solidification.
Another characteristic of aluminum is its susceptibility to oxidation. Aluminum readily forms oxides, which makes it difficult to weld. The oxides are trapped in the weld pool, forming inclusions and producing weak joints prone to failure. Oxides typically are removed by one of the following three methods used in variable-polarity welding: chemical etch, mechanical grindings or cathodic etch.
Aluminum alloys also are susceptible to porosity during welding. Porosity generally is produced when the weld pool absorbs hydrogen. The solubility of hydrogen in aluminum is very high in the molten state and requires good gas coverage to provide a protective environment. Common sources of hydrogen are water in the form of moisture on the metal surface, shield gas leaks, and water stains. Oil and other lubricants also act as hydrogen sources.
Defining Variable-polarity Plasma Arc Welding
Plasma arc welding is a hybrid method of GTAW. Both methods use a tungsten electrode, but their torches are different. The GTAW arc is bell-shaped, unlike the highly focused, strong arc produced with a PAW torch.
The electrode in a PAW torch is surrounded by a copper nozzle with a constricting orifice (see Figure 1, top of page). Initiating an arc requires two power supplies — a pilot supply connected between the electrode and the nozzle and one to provide the current between the electrode and the workpiece.
When the pilot current is activated, an arc is established between the electrode and the orifice. The stream of gas is ionized and forms a plasma plume called the pilot arc. The welding arc, or transferred arc, occurs when the main power supply is activated, and it establishes a current path through the ionized gas from the electrode to the workpiece.
The arc produced by the plasma torch is stiff and provides directional stability of the plasma jet. The highly focused arc is less susceptible to magnetic fields and arc wandering. High current densities and energy concentration produce a constricted arc that allows welds with deeper penetration and a small heat-affected zone (HAZ). More important, the arc also is less susceptible to arc gap variations or standoff distance, making it more desirable for the manufacturing production environment.
A PAW power source with variable polarity allows the current waveform to be fine-tuned. The polarity of the arc can be switched and controlled by varying the amounts of direct current electrode negative (DCEN), or straight polarity, and direct current electrode positive (DCEP), or reverse polarity.
These variable-polarity parameters are programmed in the power supply to produce the most effective VP-PAW weld. The example shown in Figure 2 demonstrates a typical waveform and variable-polarity welding parameters required when welding a 6-millimeter-thick aluminum alloy.
Variable-polarity Welding Parameters | |||||||||||
---|---|---|---|---|---|---|---|---|---|---|---|
5456 Aluminum | 2219 Aluminum | 5086 Aluminum | |||||||||
D C E N | ↑ 145 Amps ↓ | 19 ms | |||||||||
D C E N | ↑ 140 Amps ↓ | 19 ms | |||||||||
D C E N | ↑ 130 Amps ↓ | 19 ms | |||||||||
D C E P | 3 ms | ↑ 185 Amps ↓ | D C E P | 3 ms | ↑ 180 Amps ↓ | D C E P | 4 ms | ↑ 180 Amps ↓ |
|||
Figure 2. The light gold and dark gold portions show the current in amps, and its duration, to scale.
|
As mentioned previously, aluminum has a tendency to form oxides, and this barrier must be removed to produce a quality weld. One of these methods is cathodically etching the metal during variable-polarity welding. To understand this effect, it is important to distinguish between and explain the two types of electrode polarity that produce the variable polarity. These differing forms of electrode polarity (see Figure 3) are known as straight polarity (DCEN) and reverse polarity (DCEP).
Straight polarity produces higher arc efficiencies when compared to reverse polarity. In reverse polarity, much of the heat does not transfer to the part. The main advantage of reverse polarity is the ability to clean/ etch the weld surface. The etching effect is necessary to remove the oxide and produce a high-quality aluminum weld. In addition, the cathodic etching produced by DCEP enhances the weld pool flow characteristics significantly, making keyhole welding possible. Visually, a VP-welded aluminum joint is clean in appearance with a clear indication of the etched zone.
Welding Tailor-welded Blanks
A lack of variable control of the AC waveform limits the use of AC DCEP. The welder cannot optimize the arc for heat transfer and cleaning. The process that combines both of these two forms of electrode polarities takes advantage of the high input of DCEN welding and the cleaning effects of DCEP welding.
Test Number |
Dome Height (mm) |
Peak Force (kN) |
Comments |
---|---|---|---|
1 Biaxal | 19.9 | -21.8 |
The test completed its cycle before specimen failure |
2 Biaxal | 20.6 | -24.1 | Failure in thinner parent material 2.5 mm from weld |
3 Biaxal | 19.2 | -21.4 | Failure in thinner parent material 3.0 mm from the weld |
4 Biaxal | 20.2 | -24.3 | Failure in thinner parent material 2.5 mm from the weld |
5 Biaxal | 19.8 | -22.6 | The test completed its cycle before specimen failure |
6 Biaxal | 18.6 | -24.8 | Failure in thinner parent material 2.0 mm from the weld |
7 Biaxal | 17.7 | -22.6 | The test completed its cycle before specimen failure |
Test Number |
Dome Height (mm) |
Peak Force (kN) |
Comments |
---|---|---|---|
1 Plane Strain | 18.8 | -22.0 |
Neck in the parent material 4 mm from the weld |
2 Plane Strain | 18.8 | -18.8 | Failure in thinner parent material 2.0 mm from the weld |
3 Plane Strain | 19.6 | -23.2 | Failure in thinner parent material 8.0 mm from the weld |
4 Plane Strain | 19.1 | -22.9 | Neck in the parent material 4 mm from the weld |
Tables 2 and 3 show the results of the 101.6-millimeter limiting dome height (LDH) tests performed on ASTM 5182 material. The geometry of the welded coupons was 200 millimeters 200 millimeters for the biaxial stretching test and 125 millimeters 200 millimeters for the plane strain test. The material thickness was 0.8 millimeter to 1.6 millimeters.
The weld was performed in the transverse direction to the rolling direction. No lubricants were used to reduce friction. The weld speed for these tests was 2.5 meters/minute. All the welds were produced using a 400-amp VP-PAW power supply integrated with a simple seamer.
Figure 4 shows the weld profile of a blank produced using VP-PAW. The weld bead has a smooth transition between the two different material thicknesses. This profile promotes improved material flow and produces a panel with improved stamping characteristics when compared to profiles produced with a smaller weld bead. It is important to note the equiaxed grains, which are produced by pulsing the current during welding. This grain structure promotes improved formability.
The sample shown in Figure 5 is a macro view of a VP-PAW-produced weld. The white area surrounding the weld is the cathodic-etched zone. Again, in VP-PAW, the polarity of the arc can be switched and controlled by varying the amounts of DCEN (straight polarity) and DCEP (reverse polarity).
Conclusions
VP-PAW is a proven, stable method for welding many types of aluminum alloys for stringent applications. The two forms of electrode polarity produced with VP-PAW cathodically etch the metal, removing the layer of aluminum oxide. Removing this layer is essential for producing quality welds. These characteristics of VP-PAW can help to overcome the metallurgical obstacles of welding AA.
VP-PAW is an operation that is being used in high-production applications. The flexibility in its standoff distance and arc size makes fit-up more forgiving than some other conventional methods of producing TWBs. The constricted arc also produces a weld bead profile conducive to good metal flow.
The reflection characteristic of aluminum does not affect VP-PAW and so operating speed is maximized. Typical seam welding speeds approach 5.5 meters/minute, making it production-capable for the number of AA-TWBs that are forecasted to be produced over the next several years.
For future high-production operations, VP-PAW can be combined with a laser to produce metallurgically sound welds. The cathodic etching produced by VP-PAW drastically reduces the reflection of the aluminum, enabling the laser to weld it.
About the Authors
Chris Pilcher
23814 Michigan Ave., Suite 315
Dearborn, MI 49124
313-278-3507
John Micheli
Metallurgical Engineer
23814 Michigan Ave., Suite 315
Dearborn, MI 48124
313-278-3507
subscribe now
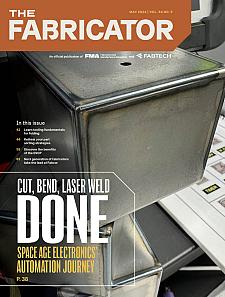
The Fabricator is North America's leading magazine for the metal forming and fabricating industry. The magazine delivers the news, technical articles, and case histories that enable fabricators to do their jobs more efficiently. The Fabricator has served the industry since 1970.
start your free subscription- Stay connected from anywhere
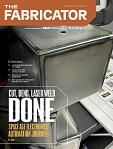
Easily access valuable industry resources now with full access to the digital edition of The Fabricator.
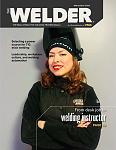
Easily access valuable industry resources now with full access to the digital edition of The Welder.
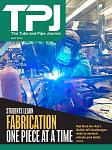
Easily access valuable industry resources now with full access to the digital edition of The Tube and Pipe Journal.
- Podcasting
- Podcast:
- The Fabricator Podcast
- Published:
- 04/16/2024
- Running Time:
- 63:29
In this episode of The Fabricator Podcast, Caleb Chamberlain, co-founder and CEO of OSH Cut, discusses his company’s...
- Trending Articles
Capturing, recording equipment inspection data for FMEA
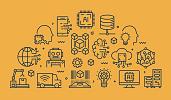
Tips for creating sheet metal tubes with perforations
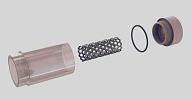
Are two heads better than one in fiber laser cutting?
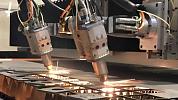
Supporting the metal fabricating industry through FMA
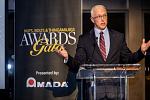
Omco Solar opens second Alabama manufacturing facility
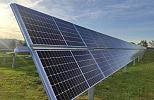
- Industry Events
16th Annual Safety Conference
- April 30 - May 1, 2024
- Elgin,
Pipe and Tube Conference
- May 21 - 22, 2024
- Omaha, NE
World-Class Roll Forming Workshop
- June 5 - 6, 2024
- Louisville, KY
Advanced Laser Application Workshop
- June 25 - 27, 2024
- Novi, MI