Editor-in-Chief
- FMA
- The Fabricator
- FABTECH
- Canadian Metalworking
Categories
- Additive Manufacturing
- Aluminum Welding
- Arc Welding
- Assembly and Joining
- Automation and Robotics
- Bending and Forming
- Consumables
- Cutting and Weld Prep
- Electric Vehicles
- En Español
- Finishing
- Hydroforming
- Laser Cutting
- Laser Welding
- Machining
- Manufacturing Software
- Materials Handling
- Metals/Materials
- Oxyfuel Cutting
- Plasma Cutting
- Power Tools
- Punching and Other Holemaking
- Roll Forming
- Safety
- Sawing
- Shearing
- Shop Management
- Testing and Measuring
- Tube and Pipe Fabrication
- Tube and Pipe Production
- Waterjet Cutting
Industry Directory
Webcasts
Podcasts
FAB 40
Advertise
Subscribe
Account Login
Search
Young fabricators ready to step forward at family shop
A family company in Ohio makes key investments to support the third generation’s plans for growth
- By Dan Davis
- May 3, 2024
- Article
- Laser Cutting
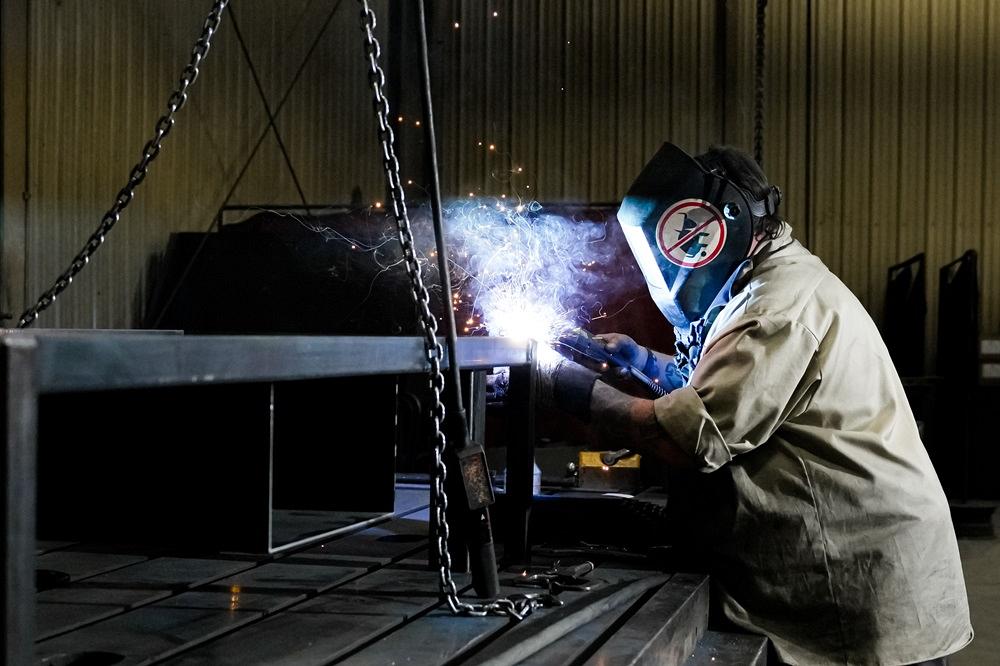
Fabcor Metal Fabricators has grown aggressively over the past few years. Like many other shops, it’s always ready to take on new employees. Images: Fabcor Metal Fabricators
Look around a metal fabricating shop and you probably see more than a few people with gray hair—if they still have their hair. A “silver tsunami,” as one cable outlet coined it, is occurring, and experienced workers in the manufacturing industry have either left to enjoy retirement, or they are making plans to do just that.
Luckily, manufacturing companies have had some time to plan for these transitions, hopefully transferring what industry and institutional knowledge they could from those experienced minds to the young people tasked with replacing them. Fabcor Metal Fabricators, Minster, Ohio, is a good example of a place where planning for a generational shift in leadership is taking place.
Robert Hoying founded Fabcor in the mid-1980s after working to help get another metal fabricating company up and running in nearby Sidney, Ohio. Hoying’s son Jon, an engineering student at the University of Cincinnati at the time, joined him on this entrepreneurial adventure.
By 2020, Fabcor had grown to become a well-respected job shop in northwest Ohio. It had reached $5.4 million in annual revenues, which included work from its Jails Correctional Products business, which was dedicated to fabricating, designing, and installing equipment and furniture for prisons, courtrooms, and police stations. (Jails Correctional Products was established in the 1990s after a local company went out of business and some of those employees brought their know-how and connections to Fabcor.)
Today, Jon has been joined by his son Jacob Hoying, Fabcor’s plant manager, and son-in-law Kurtis Thobe, the company’s controller. Jon, Fabcor’s president and CEO, is not about to leave the business in the coming months as he nears 40 years with the company, but he also recognizes that he doesn’t want the third generation to leave either. After all, they have only begun their journey in the metal fabricating industry, both joining Fabcor in 2018.
As any demographic researcher will tell you, the current generation of young people are different from the baby boomers and Gen Xers that preceded them. Today’s youth are much more comfortable with advanced technology, and they like to know what’s in it for them. They aren’t afraid of hard work if they understand what the goal is and how they will achieve it.
That’s where the Fabcor leadership team found themselves in 2020.
“When COVID came around, Jon, Jacob, and I decided that we had to do what we could to really push ourselves to be a driving leader in metal fabrications,” Thobe said.
That dedication was not only good for driving business decisions in the near term, but it was part of a long-term plan for everyone’s success. “We had to look out for everyone’s future,” Thobe said.
Some of these business decisions have proved to be very fruitful for Fabcor since the early days of the pandemic.
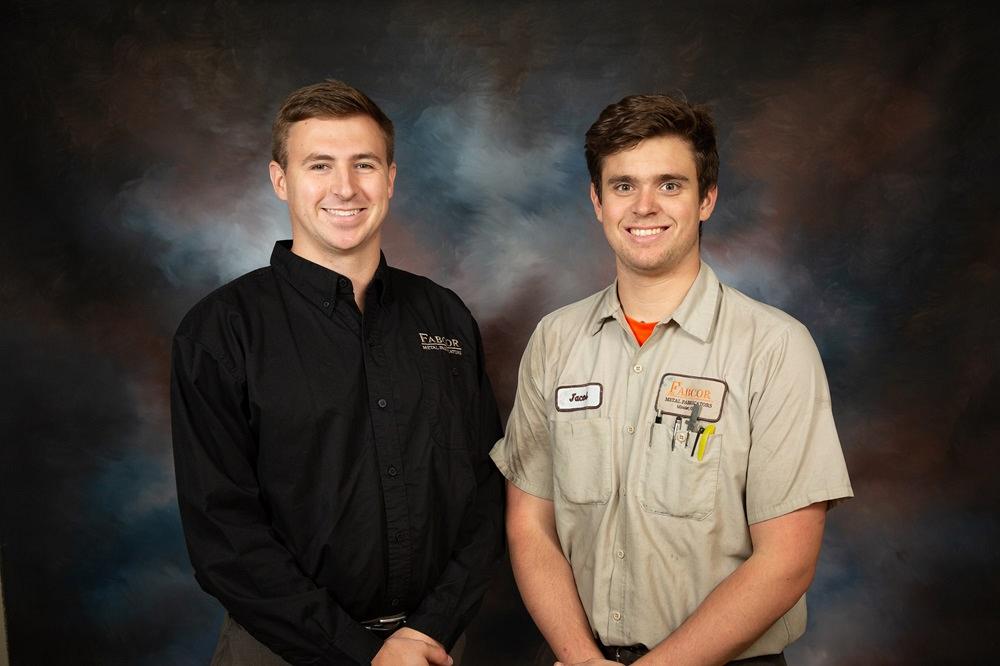
(From left) Kurtis Thobe and Jacob Hoying want to grow Fabcor Metal Fabricators to provide not only for their futures, but also the company’s employees.
Searching for More Capacity
Ohio is home to 12,106 manufacturing firms and approximately 660,000 manufacturing employees, according to a National Association of Manufacturers report from 2019. In Ohio, manufacturing accounts for 16% of the total gross state output, which totals $114.7 billion. By comparison, in California, a place with 34,360 manufacturing companies, manufacturing represents only12.3% of total gross state manufacturing output. Ohio is a manufacturing hotbed.
With that reality, Fabcor knew it needed more modern fabricating technology to be competitive with other nearby shops. A 1990s-era CO2 laser cutting machine just wasn’t going to match the cutting speeds of a modern fiber laser cutting machine, which in turn affects laser cutting quotes and lead times.
“It was just slow as molasses,” Thobe recalled.
Fabcor installed its first fiber laser cutting machine, a 10-kW TRUMPF TruLaser 5030 with automated material load and unload, in late 2020. The laser cuts parts at a speed the shop had never seen before, according to Thobe. It also opened the door to cutting thicker parts, up to 1.5 in. in mild steel and 1.625 in. in stainless steel, something that makes Fabcor unique in its immediate area.
“Before we got that laser, you were talking at least six to eight weeks for fabrications to be done,” Thobe said. It’s about half that time now, and customers with rush jobs can be accommodated much more easily, he added.
That soon was followed by other investments. A TruBend 7050 press brake with just over 50 tons of forming force and a 12-kW TruLaser 5040, which can accommodate 72-in.-wide by 144-in.-long sheet, were added in early 2023. Shortly thereafter, a 6-kW TruLaser tube laser cutting machine, which replaced an older tube laser, and a 350-ton TruBend 5320 press brake were added to the machinery mix in Fabcor’s 75,000-sq.-ft. facility.
Just Starting With the Finishing
While the addition of new fabricating machinery might have been enough change for some shops, Fabcor also decided to add powder coating capabilities to its service offerings during the pandemic. Thobe said that customers kept asking if the company offered that type of finishing service, and it got to the point where the demand was great enough for them to consider bringing the activity in-house.
“If you are considering painting something, you have to consider powder coating. It adheres better than paint. It’s more durable than paint. That’s just the way that things are going now,” he said.
Until recently, Fabcor had a small-batch operation. Powder coating was applied in one area, and a small oven was used to cure the powder coating, creating the durable outer layer desired by Fabcor’s customers. The small size of the oven, however, really limited the type of parts that could be powder coated. Thobe estimated that anything beyond 6 by 6 ft. couldn’t fit into Fabcor’s oven, so some outsourcing still needed to be done for anything larger than that.
To accommodate a wider range of that type of work in-house, Fabcor installed a much larger oven in early March. The structure, approximately 12 by 12 by 24 ft., can accommodate larger racks of parts and larger weldments.
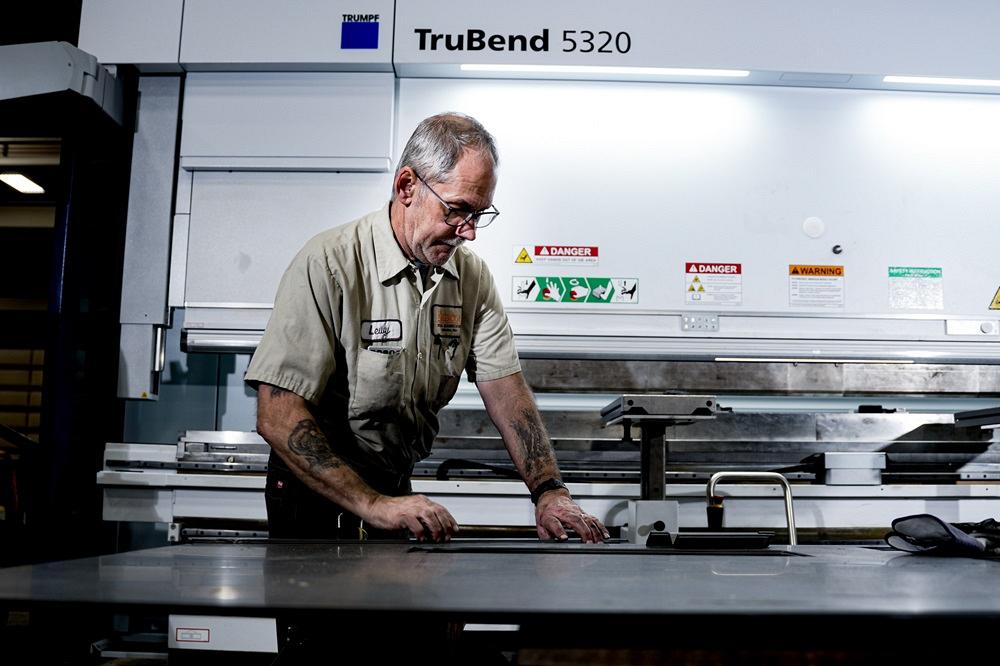
Fabcor’s new press brakes have helped the bending department keep up with the parts coming off the new 10- and 12-kW laser cutting machines.
Thobe added that Fabcor has one operator overseeing powder coating, and she has shown a willingness to take ownership of the whole operation. She has a background in finishing, so she has the experience to ensure that the powder-coated parts consistently meet customer specs, keeping them satisfied and solidifying the business relationship.
Technology Making a Difference
The addition of new fabricating machinery undoubtedly has helped Fabcor grow its business in recent years, but it’s also made the transition a bit easier when it comes to bringing new talent into the organization. Thobe admitted that if the right candidates came to the door, they could easily find positions for them. For the record, the right candidate isn’t necessarily an experienced one.
Thobe said that the modern machine tools on the shop floor help to make the transition much easier for a person new to the metal fabricating world than older equipment could. A person with little idea as to how metal parts are fabricated can become a machine operator in a matter of weeks, not months.
Thobe pointed to the ACB (automatically controlled bending) angle measuring system incorporated into the new TRUMPF press brakes as an example. To ensure that correct measurements are made, the press brake measures the springback in the material and corrects itself on the fly to deliver the desired bending angle. (The brake uses an optical measurement system to help with the angle correction. A laser projects a line on the workpiece surface, and the camera detects the line. That combination is used to determine the exact bending angle, and that information is then transferred to the controller. If the first bending sequence doesn’t deliver the angle specified for the job, the ram prepares for another hit, creating the expected bend angle.)
The pressure to check each piece coming off the press brake is eliminated. That makes the operator much more productive.
Additionally, the inexperienced press brake operator has the benefit of seeing the entire bending process on a touchscreen attached to the brake. The operator doesn’t have to visualize how the bending sequence might flow because he can see it replicated in 3D on the screen.
“These press brakes are really smart,” Thobe said. “They really help out new operators because they show them how to bend the parts correctly.”
The PartMaster material handling automation on the 12-kW laser cutting machine is another example. It feeds the skeleton of laser-cut parts from an elevated perch down to the operator at right around waist level. The person only has to reach directly in front of him to remove the parts to place them on nearby pallets or to break that part of the skeleton, placing the scrap in a conveniently placed bin. The conveyor can be advanced each time the parts sorter removes the parts in front of him, keeping the individual from excessive reaching and strain on the back.
“That’s really huge for us. It saves so much time,” said Thobe, adding that he’d love to see a PartMaster on the 10-kW laser cutting machine, but more space is needed to accommodate it.
Getting the Word Out
Like many metal fabricators, Fabcor is looking for new employees. Thobe said marketing is one of his many responsibilities. (When he finished with the phone call for this interview, he was heading out to the shop floor to lend a hand.) Some Facebook notices about open positions and a story in the local Daily Standard newspaper generated a little bit of interest. He hopes to spend more time with that kind of outreach.
He’s also had some conversations from local trade schools about their welding programs, explaining what Fabcor does and what they might be looking for in terms of welding skills. Thobe said he hopes further discussion leads to possibly influencing how the welding curriculum is shaped so that welders might come to work ready to be immediate contributors.
“We’re doing more, continuing to grow, and looking for more help,” Thobe said.
The steps taken so far seem to be working out as the Fabcor team had hoped. Annual revenues have grown substantially since 2020, and the company expects revenue to increase more than 50% in 2024 when compared to last year. It’s actively looking to add new customers to its portfolio and grow with them as it has with current customers.
To prepare for more growth, Thobe said he wants Fabcor to be a place where people will want to work, and the modern machinery and the type of fabrication work should contribute to that environment. The advanced machinery on the shop floor is being used to fabricate parts related to automation systems being used in other metal manufacturing businesses. Fabcor is helping to fabricate the machines that make modern manufacturing possible.
The business is on the right track. The plan seems sound. It seems like the kids are alright.
About the Author
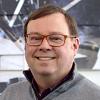
Dan Davis
2135 Point Blvd.
Elgin, IL 60123
815-227-8281
Dan Davis is editor-in-chief of The Fabricator, the industry's most widely circulated metal fabricating magazine, and its sister publications, The Tube & Pipe Journal and The Welder. He has been with the publications since April 2002.
Related Companies
subscribe now
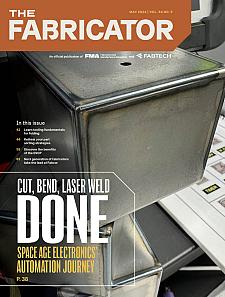
The Fabricator is North America's leading magazine for the metal forming and fabricating industry. The magazine delivers the news, technical articles, and case histories that enable fabricators to do their jobs more efficiently. The Fabricator has served the industry since 1970.
start your free subscription- Stay connected from anywhere
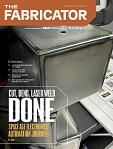
Easily access valuable industry resources now with full access to the digital edition of The Fabricator.
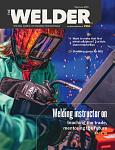
Easily access valuable industry resources now with full access to the digital edition of The Welder.
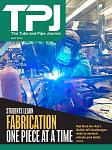
Easily access valuable industry resources now with full access to the digital edition of The Tube and Pipe Journal.
- Podcasting
- Podcast:
- The Fabricator Podcast
- Published:
- 05/14/2024
- Running Time:
- 62:12
Cameron Adams of Laser Precision, a contract metal fabricator in the Chicago area, joins the podcast to talk...
- Trending Articles
Why employee-owned companies make sense in manufacturing
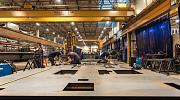
What software automation means for custom fabrication
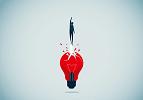
Nucor’s weekly steel price announcement continues to rattle markets
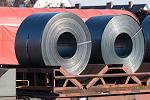
Press brakes, panel benders, and flat blank calculations
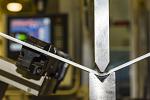
Educating, rather than just training, tomorrow's workforce
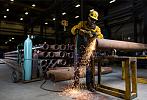
- Industry Events
Laser Welding Certificate Course
- May 7 - August 6, 2024
- Farmington Hills, IL
World-Class Roll Forming Workshop
- June 5 - 6, 2024
- Louisville, KY
Advanced Laser Application Workshop
- June 25 - 27, 2024
- Novi, MI
Precision Press Brake Certificate Course
- July 31 - August 1, 2024
- Elgin,